Just a few years ago, the maintenance of trains was conducted in the conventional ways. The common methods are preventive maintenance conducted at set intervals and corrective maintenance conducted when failure occurs. However, these two methods require a substantial amount of time and cost and entail suspension of service, increasing the operating and maintenance cost. Accordingly, operating and maintenance efficiency has grown in importance and digital transformation of train data is being rapidly introduced to improve the availability and maintenance of trains.
In the Europe, the 4th industrial revolution technologies such as IoT and ICT have been applied to maintenance, as well as operation of trains since 2018. Hyundai Rotem is also developing a smart maintenance system by combining IoT and ICT with the condition based maintenance (CBM), aiming to collect and analyze the condition data of main devices of trains as part of digital transformation.
Overview of digital transformation
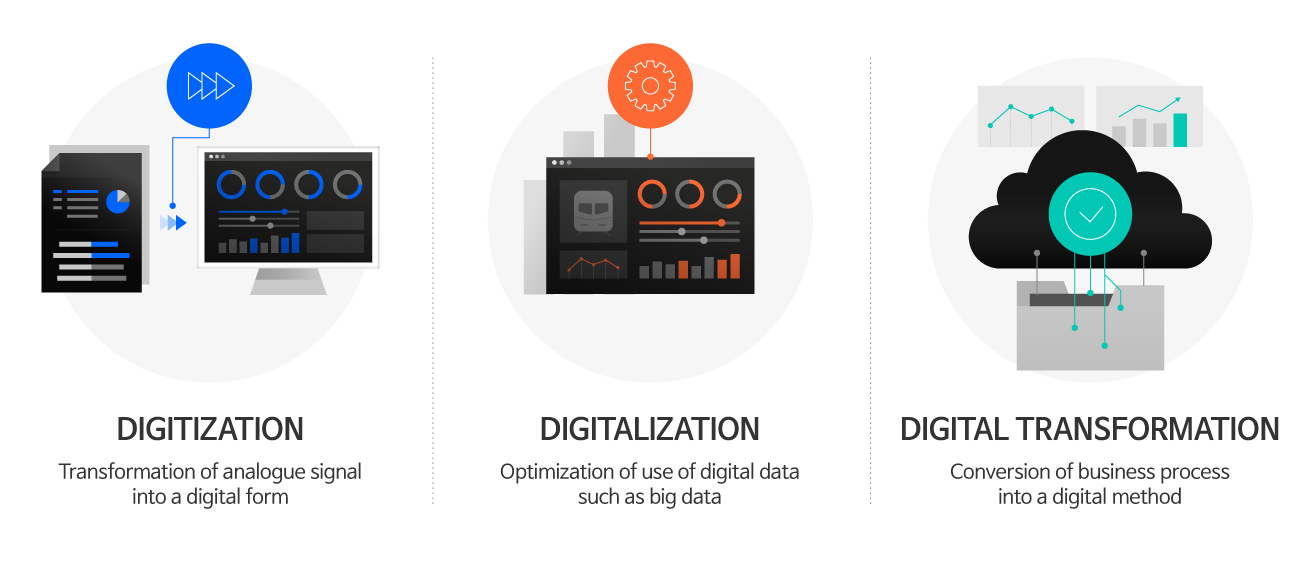
The digital transformation of train maintenance is as follows
• Digitization: Transforms all analogue signals on the condition of trains into digital data and collects them through a dedicated network inside trains
• Digitalization: Optimizes the data collected by digitization through cloud or user-friendly data collection servers
• Digital transformation: Creates a smart maintenance system by monitoring and analyzing the condition of trains real time based on the collected data
• Big data collection through digitization of trains
The key to digital transformation is to collect significant data as much as possible. In addition, data selection and analysis and result deduction are needed. For this, data collection systems and components are being diversified. In the past, a radio frequency identification device (RFID) was used to collect data from trains and main devices and the data were sent to the data collection server through the TCP/IP network of RFID receiver installed around railways. However, as more types and amounts of data are needed to be collected, the previous technology reached the limit.
To address the problem, a radio transmission device (RTD) that collects data at a certain position in real time has been introduced recently. The data collected through the RTD system are used for users’ fault monitoring and big data analysis platform. For example, it notifies possible faults in advance to enable prior actions. Accordingly, it can reduce faults that affect the safety and performance of trains and devices. In this manner, the CBM technology for efficient maintenance of trains improves the reliability, availability, maintainability and safety (RAMS) effectively. Also, it reduces the life cycle cost (LCC) of a device by optimizing maintenance resources.
Digitalization of trains and preprocessing and analysis of big data
Data collection types of trains
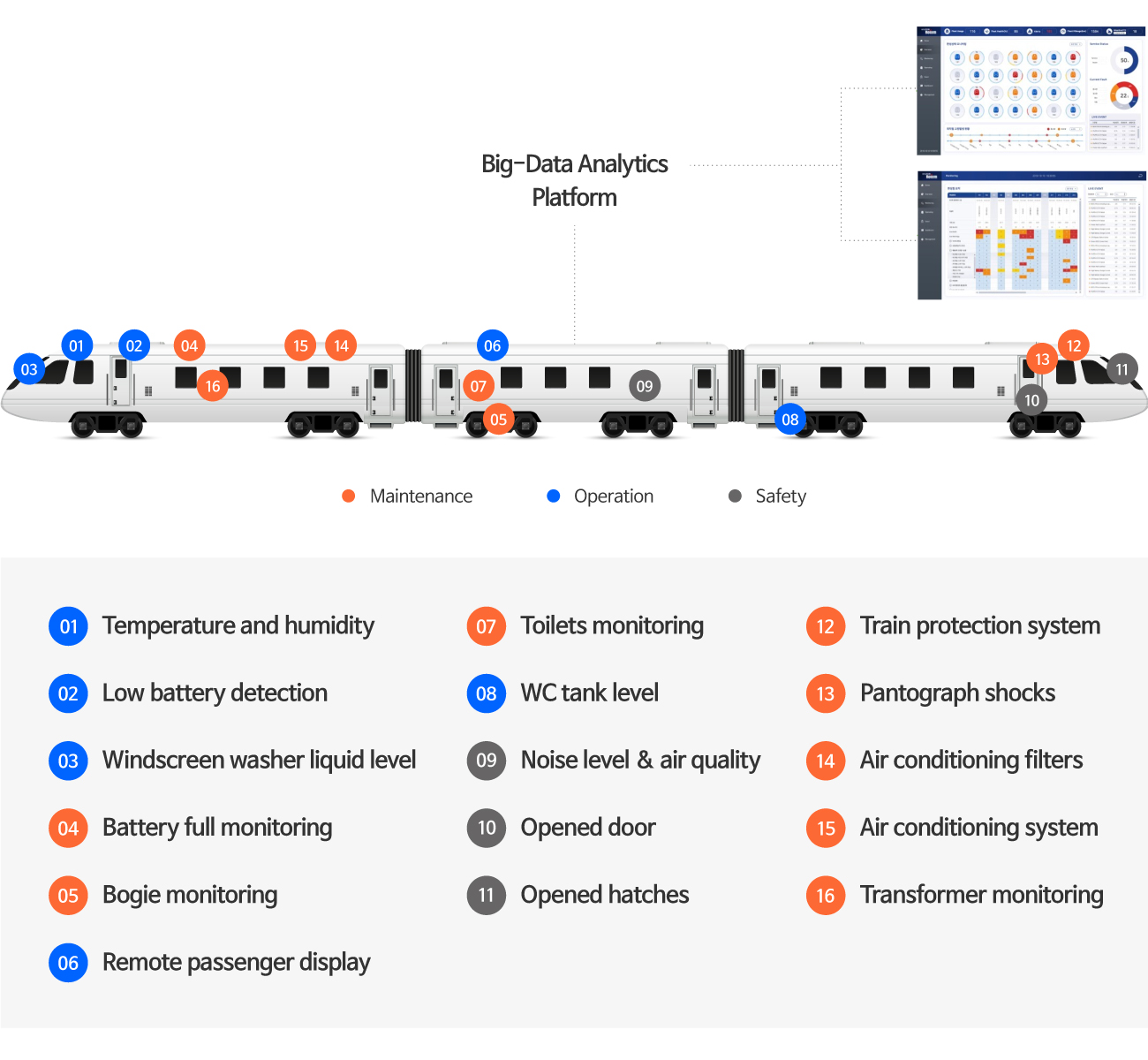
In the past, the purpose of railway operations was to transport many people and cargos and thus, data collection was for control and monitoring of trains. Recently, as the IoT and ICT technology are developed, more efforts are being made to collect condition data for use in operations and maintenance of trains. There are two types of train data collection methods largely: on-board monitoring system that is directly installed on trains and wayside monitoring system that is installed on the trackside.
The on-board monitoring system collects data through the sensors of each device and sends the data to the main server of trains after preprocessing them. Subsequently, it sends the data to cloud through the radio communication of trains or on-premises big data analysis server and provides useful information to operators and maintenance mechanics by keeping and analyzing the data. On the other hands, the on-premises monitoring system obtains data from infrared cameras installed on trackside or by measuring noise or vibration generated from the motor of trains.
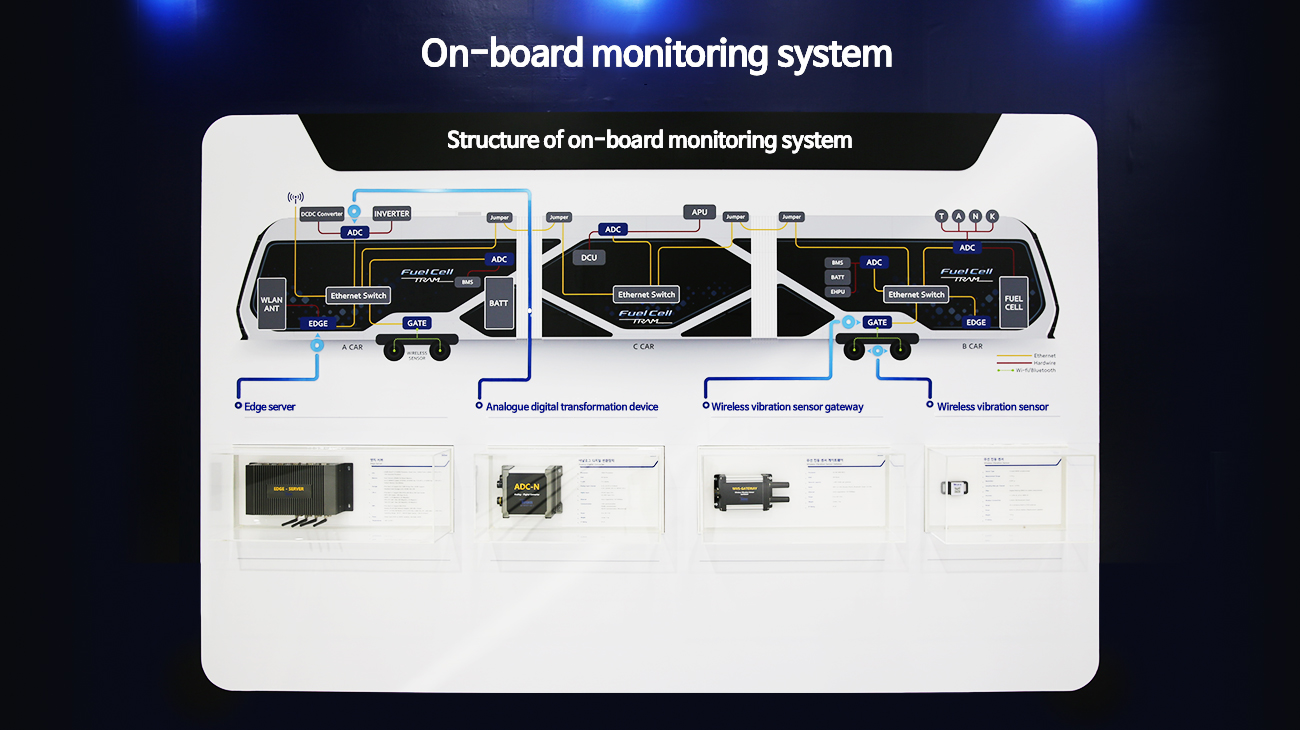
The data collection methods of on-board monitoring system can be divided into two types. The first method is to collect data through Train Control Management System (TCMS) that controls and manages trains. It is limited to devices connected to the main network of trains, but as the data are for control of trains, they show a very high consistency and stability. The second method is to collect data through the on-board monitoring system by creating a separate network from the main network of trains, which means it is not engaged in the control of train operations and thus system failure does not affect the operations of the trains.
The on-board monitoring system consists of sensors that collect condition data from main devices, analogue digital converter (ADC) connected to the sensors to transform analogue data into a digital form and send, ethernet switch and gateway that collect various data at one point and deliver and edge server that collects and manages all data of trains.
Structure of the train on-board network (example for KORAIL electric cars)
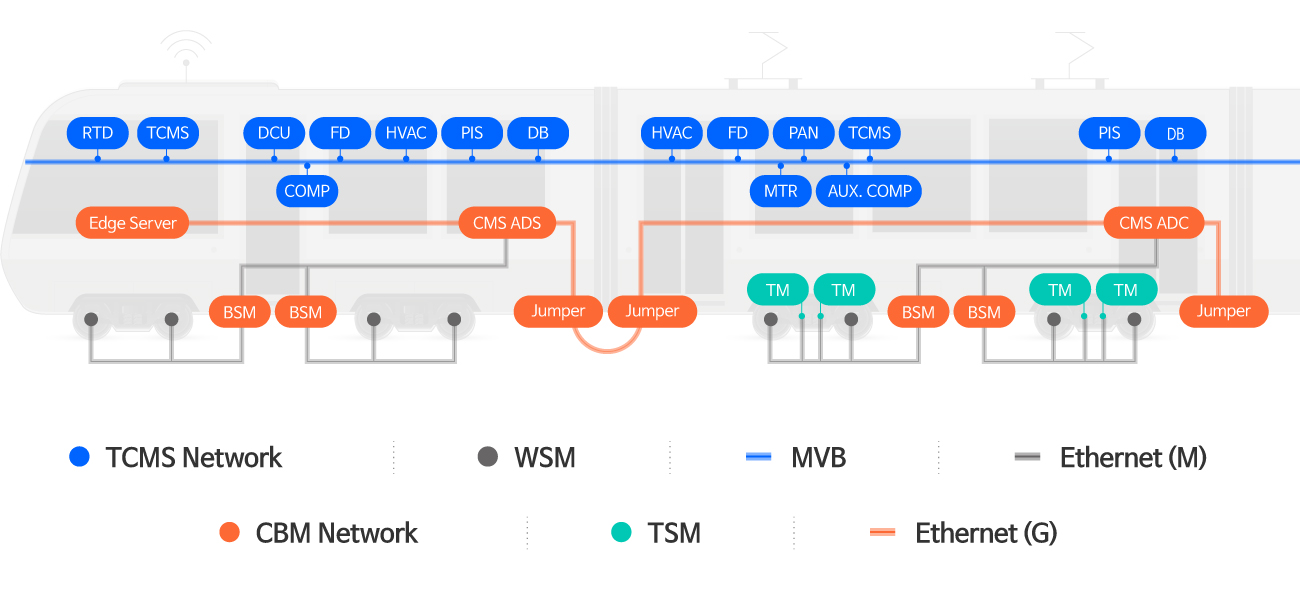
Data collected by each sensor require pre-processing depending on the type and quantity of sensors. Pre-processing is to organize and transform the data to deduce condition indicators as follows
• Abnormal value, omission value, offset, trend removal
• Noise removal such as filtering and smoothing
• Conversion between time domain and frequency domain
• Advanced signal treatment such as short-time Fourier Transform
Data pre-processing is particularly required for efficient analysis of time series data that are significantly affected by operations and operating hours like trains. Also, the wayside CBM platform is essentially required to develop a smart maintenance system that can monitor the condition real time and analyze and predict failures through cloud and big data analysis system inside the on-premises server.
Digital transformation and smart maintenance process of trains
Smart maintenance process
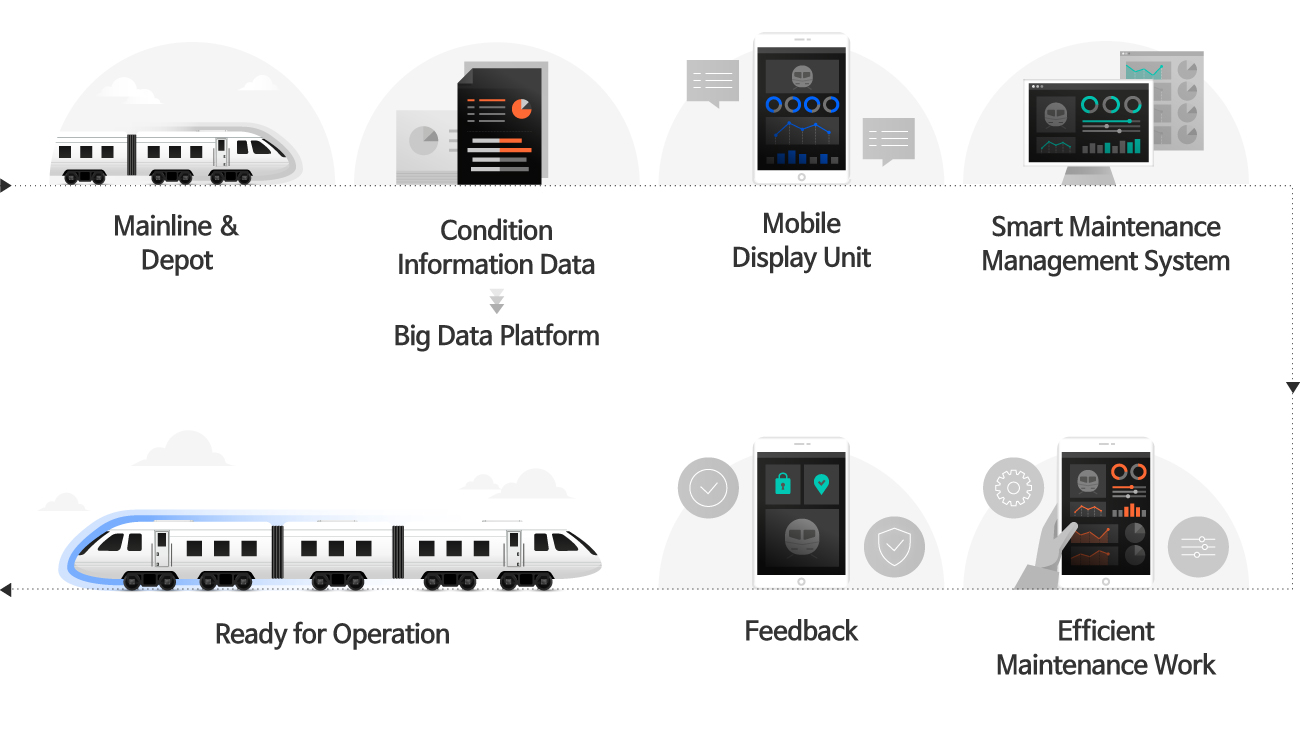
To develop a smart maintenance system, numerous train data need to be collected in various ways and systematically managed. It is easier to collect and manage train data than other mobility industries and unforeseen failures can be minimized through systematic analysis of data base (DB). Ultimately, it means an improved availability of trains, and it can also bring changes in the principle and method of data operation. While the past data collection and management of trains were passively conducted in the maintenance base where inspection and repair were performed, a smart maintenance system using the on-board and wayside CBM platforms enables various users such as operators, maintenance mechanics and administers to more actively respond to unexpected situations through cloud-based real time data collection and management by providing the condition data of trains any time.
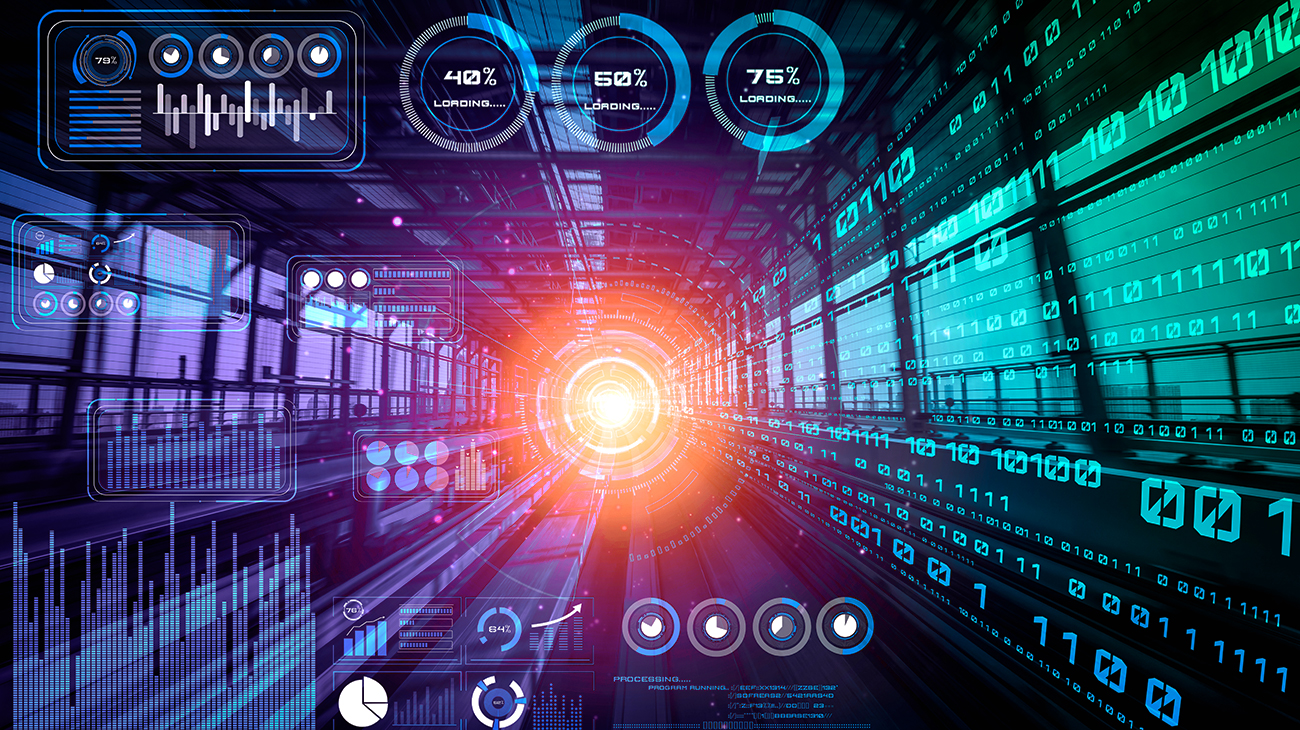
Hyundai Rotem is manufacturing trains up to the requirements of clients and applying the 4th industrial revolution technologies stepwise for more smart operations and management. In addition, it is developing a process that digitizes and converts train data into useful user-centric data. Digital transformation is the kick-off of such changes. In future, it plans to complete its digital service portfolio by developing an asset management solution that manages all train data as an asset, further from developing a real time diagnosis and monitoring solution for trains through data collection and analysis.