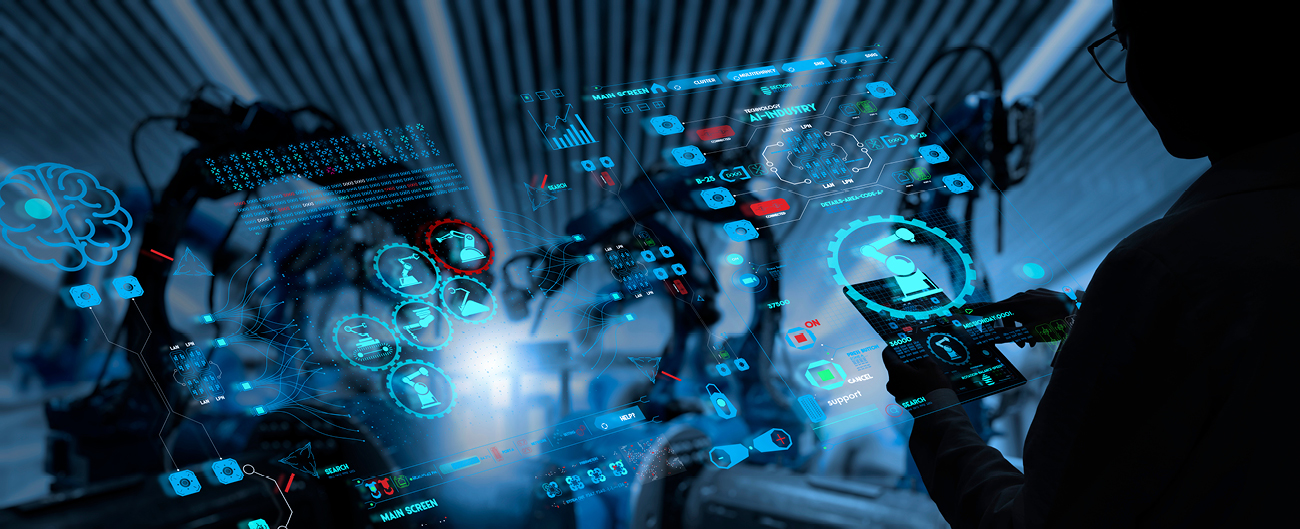
The digitization of manufacturing processes began in the early 1980s with the emergence of 3D CAD. 3D CAD implemented nearly identical 3D shapes in virtual space, resulting in reduced manufacturing time, cost savings and improved quality. It became a driving force in enhancing the competitiveness of automotive manufacturing companies such as BMW, Mercedes-Benz, and Honda.
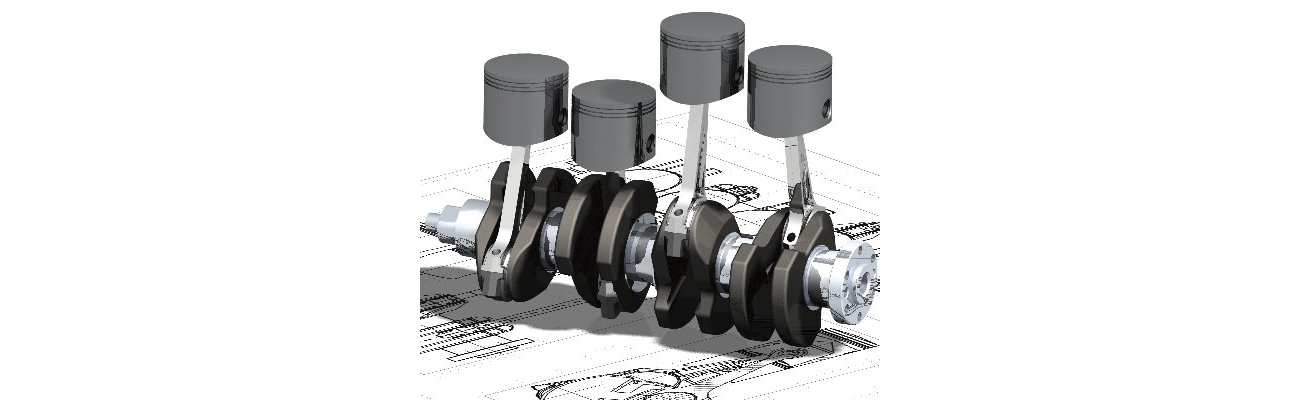
In 1989, 3D CAD advanced further with Boeing’s adoption of the 3D Digital Mock-up (DMU) technology. 3D DMU involved modeling all components in 3D from the early stages of product development and simulating assembly and review with a computer, enabling significant optimization of design and a revolutionary reduction in product development time. Boeing succeeded in mass-producing the Boeing 777 after a virtual prototype in a 3D environment without the need for physical prototypes. Digital production processes expanded with the concept of 3D Product Lifecycle Management (PLM) covering the entire product life cycle, maximizing efficiency in the product development process.
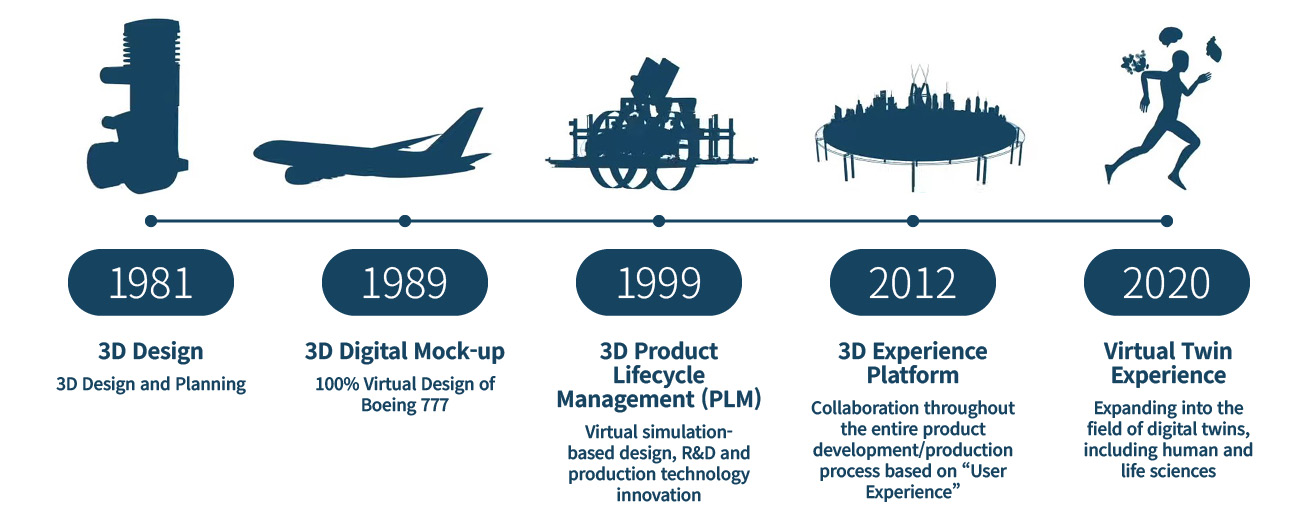
Manufacturing Innovation Driven by Digital Factory
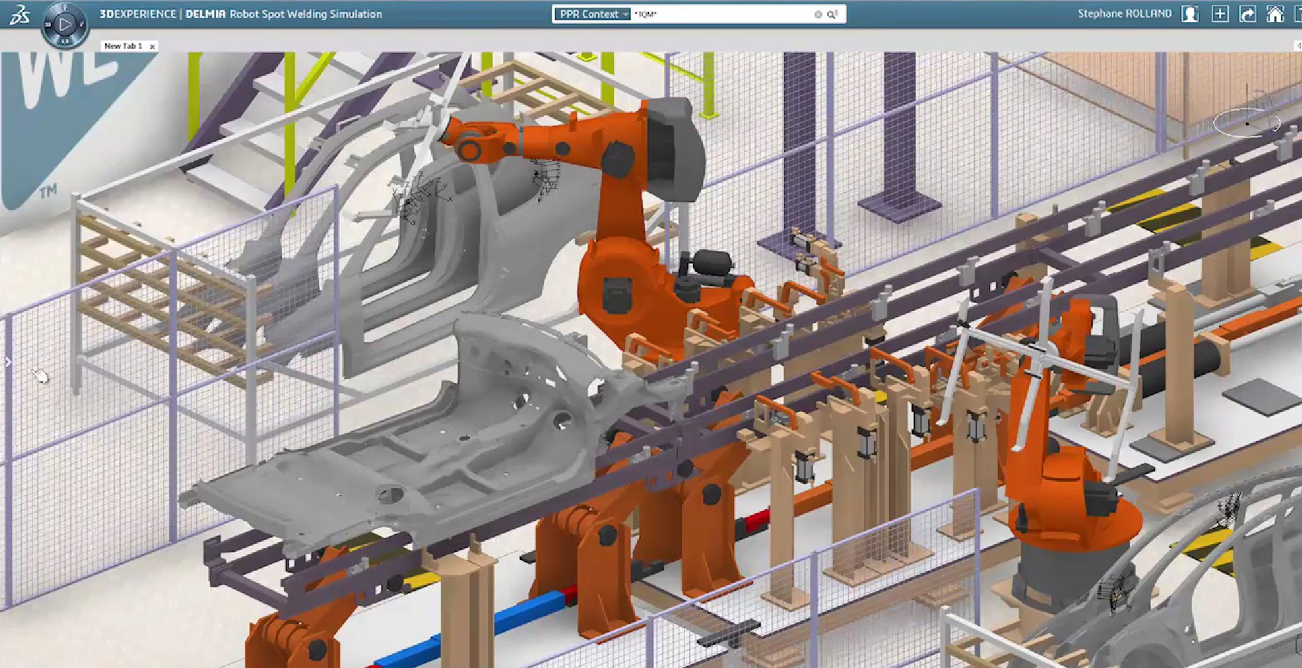
The Digital Factory represents an advanced concept in digital production processes, incorporating concepts like DMU and 3D PLM, reproducing the real factory environment in a virtual space with 3D models. This allows for pre-simulation of potential situations, enabling optimal control and offering innovative manufacturing solutions. Starting with detailed control of production status through 3D design and digital simulation, it further utilizes Digital Twin technology to seamlessly connect the real manufacturing environment and virtual space in real time, continuously optimizing the production system.
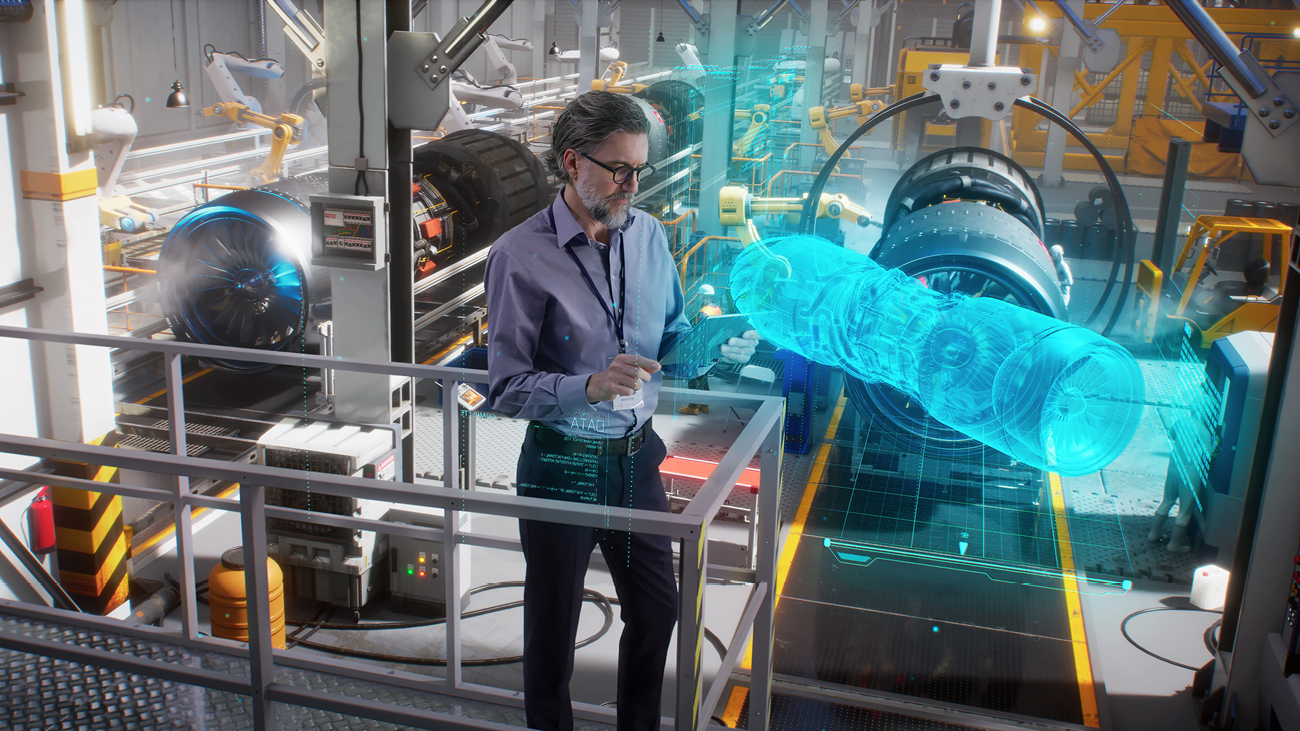
The Digital Factory has already been applied to various companies, leading manufacturing innovations. Boeing explained that it introduced digital twin technology to multiple factories in the United States, achieving a maximum productivity increase of up to 50%. Siemens in Germany applied 100% of digital twin technology to all stages, from PLC product design to the production process, at its Amberg factory, accomplishing a product defect rate of 0.0001%.* China’s Foxconn, the iPhone manufacturer, has reportedly increased production efficiency by over 30% and reduced inventory cycles by 15%** through the introduction of digital twin manufacturing processes incorporating artificial intelligence, machine learning, the Internet of Things and robotics.
* Korea Economic Daily, Sept. 12, 2022, “Siemens completes ‘Digital Twin’ after 20 years… Output increased 15 times, number of items 20 times.”
** Industry News, Jan. 11, 2019, “World Economic Forum selects 7 global future manufacturing plants from steel to smartphone manufacturing in 2019.”
Rail Solution’s Move Toward the New Rotem 4.0 Era: Digital Factory
In its 2023 Sustainable Management Report, Hyundai Rotem declared the transition to the “New Rotem 4.0 era,” intensifying its move toward sustainable mobility. Emphasizing the integration of AI and eco-friendly global industry trends in the railroad, defense, and plant industries, Hyundai Rotem’s Rail Solution division is actively leading sustainable management, accelerating steps toward the New Rotem 4.0 era.
Hyundai Rotem, particularly through the Rail Solution Research Institute, collaborates with the production headquarters to carry out various activities spanning design and production across the entire life cycle of railcars, aiming to realize the Digital Factory.
Hyundai Rotem is implementing advanced-level 3D modeling using an integrated solution of digital design and production tools that encompass computer-aided design (CAD), computer-aided engineering (CAE) and computer-aided manufacturing (CAM). Furthermore, our company employs the fundamental concept of “Digital Pre-assembly” (DPA) in the digital factory, which not only reviews interfaces such as interference, collisions, and gaps in the product but also identifies design errors and improves designs based on interference reviews related to the static/dynamic behavior of the train. In addition, Hyundai Rotem utilizes virtual reality (VR) technology to collaborate with the production technology sector, simulating and optimizing train manufacturing processes and methods, reducing design errors through internally developed design verification content.
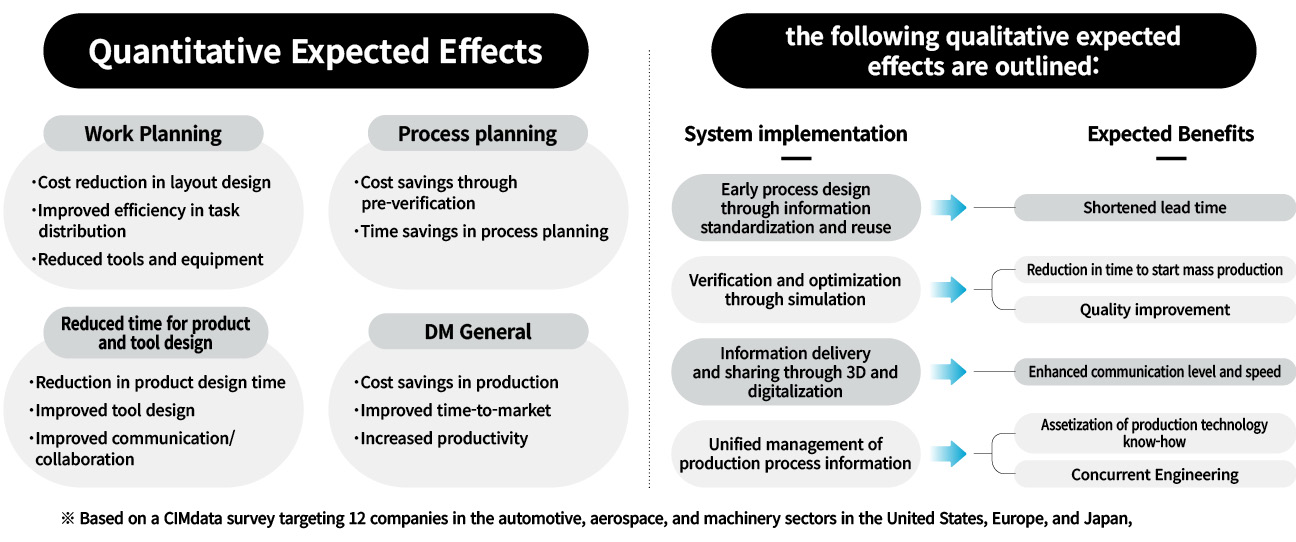
Due to changes in the industrial and business environment, many manufacturing companies consider strengthening the pre-production verification system as an essential task, aiming to maintain market competitiveness by producing products quickly and with high quality using minimal resources. Especially with the continuous increase in overseas market entry in the railcar industry, reflecting not only domestic but also considerable production processes overseas, the establishment of a digital factory that pursues both quality improvement and production process optimization has become a crucial issue.
The First Step in Production Process Optimization: Digital Twin-based Pre-Production Verification
Hyundai Rotem has established and operated a Digital Factory team since 2023 with the goal of implementing an advanced design verification system (DPA) and building a business system. In the future, for the construction of a digital factory related to railcar production, the company plans to model the products and production facility infrastructure in 3D and create a system that verifies the coherence of assembly and production through “digital pre-production simulation,” which reflects the actual process sequence in the production site and the production process (process, method, production facility, working conditions, etc.). To achieve this, the company will use a digital verification-specific commercial solution based on production data to simultaneously verify essential elements for railcar production such as components (product), processes (process) and materials (logistics).
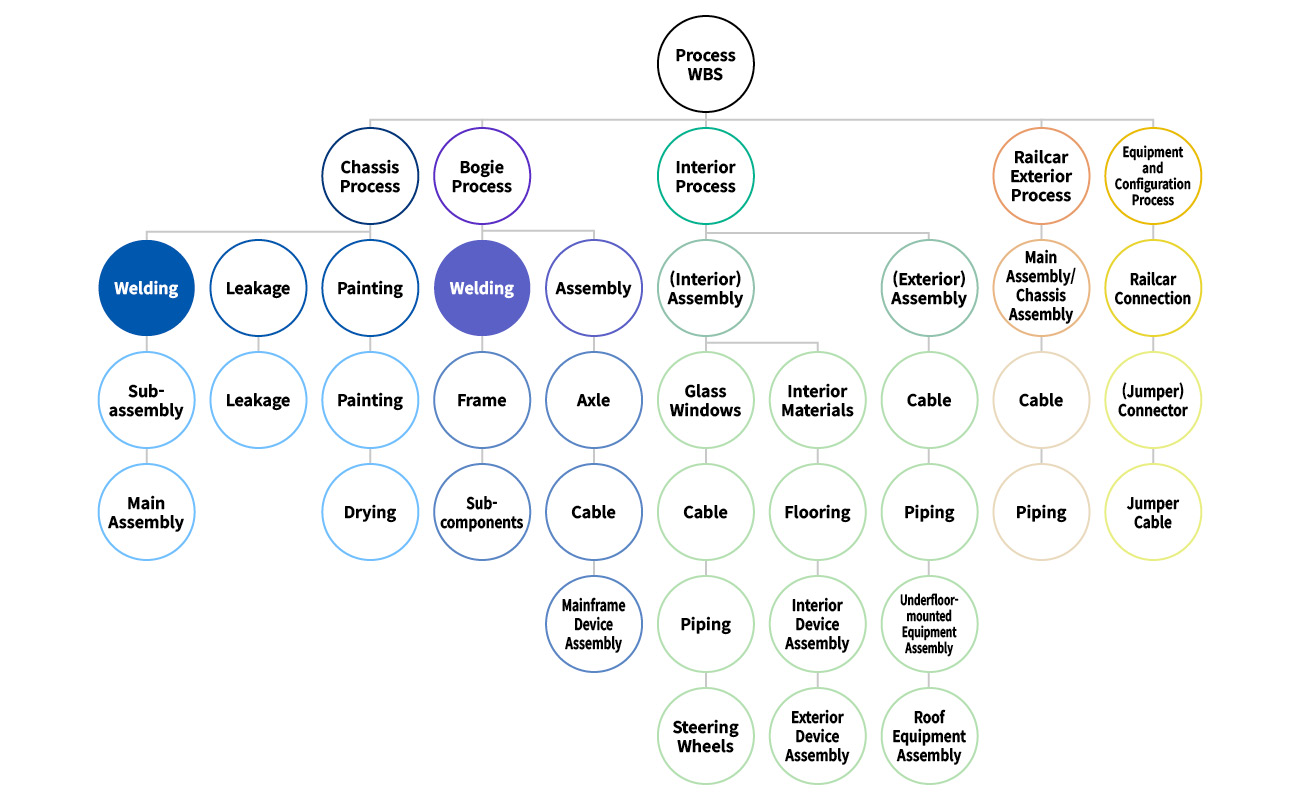
Hyundai Rotem is pushing for the digitization of pre-production verification, particularly in the welding and assembly processes, as part of its efforts to establish a digital factory for railcar production. The first goal is to establish a system for the “Welding Process DPA” covering the welding items that encompass the bogie and car body, and the “Assembly Process DPA” including bogie and car body assembly, as welding processes have the most significant impact on the strength and stiffness of the railcar.To achieve this, the process involves separating and distributing process-specific information (WBS) and utilizing the latest 3D modeling to digitize each process in the actual production order. The 3D modeling process for each stage is an advanced DPA step that precedes actual welding and assembly, verifying the manufacturability and workability of the process.
Applying this system to Hyundai Rotem’s main railcar series in sequence
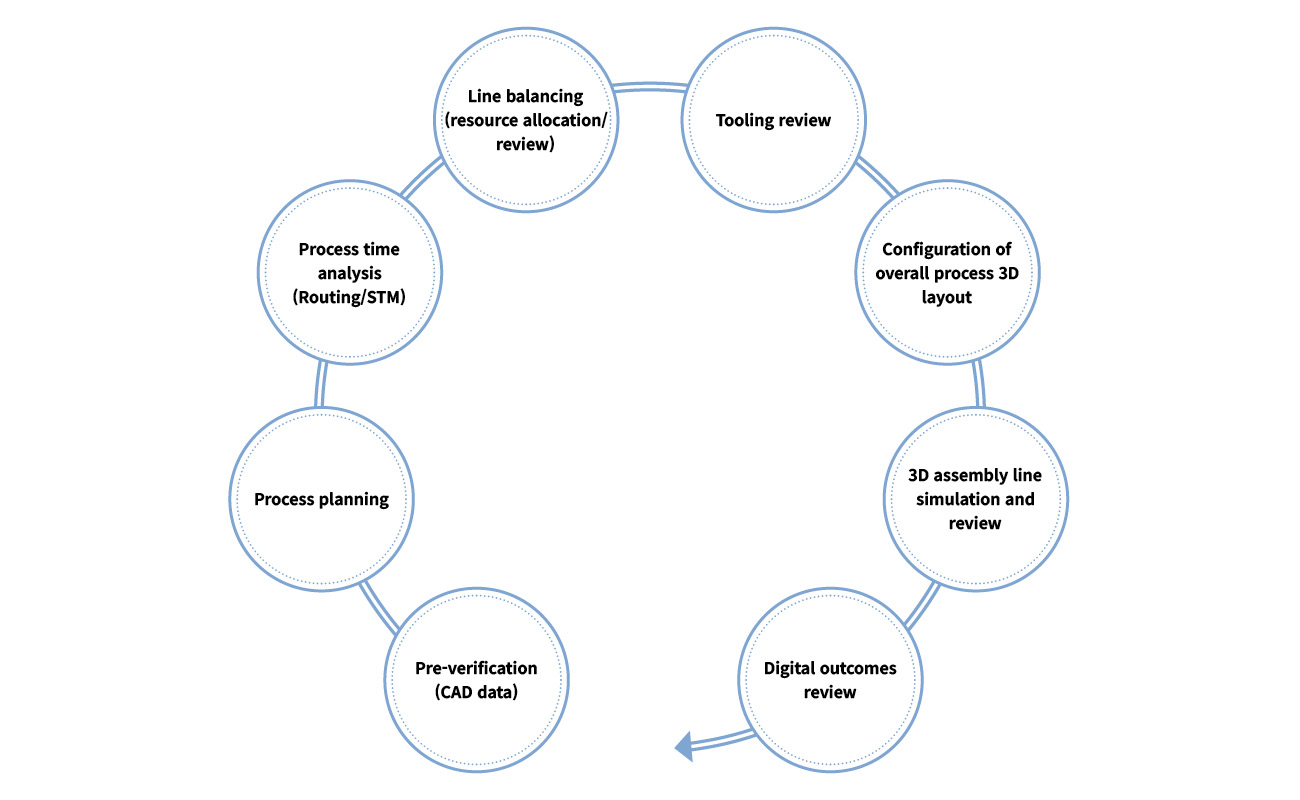
Hyundai Rotem’s digital factory building project, started in 2023, is progressing with the application of a pilot program for the digitalization of major welding processes such as the body welding area in vehicle production processes, starting with the DPA of the body welding field. Currently, there is an ongoing process of collecting various information for digital factory operation in key processes related to welding processes such as body sub-assembly, main assembly, and bogie frame. The application process targets and their scope will gradually expand.
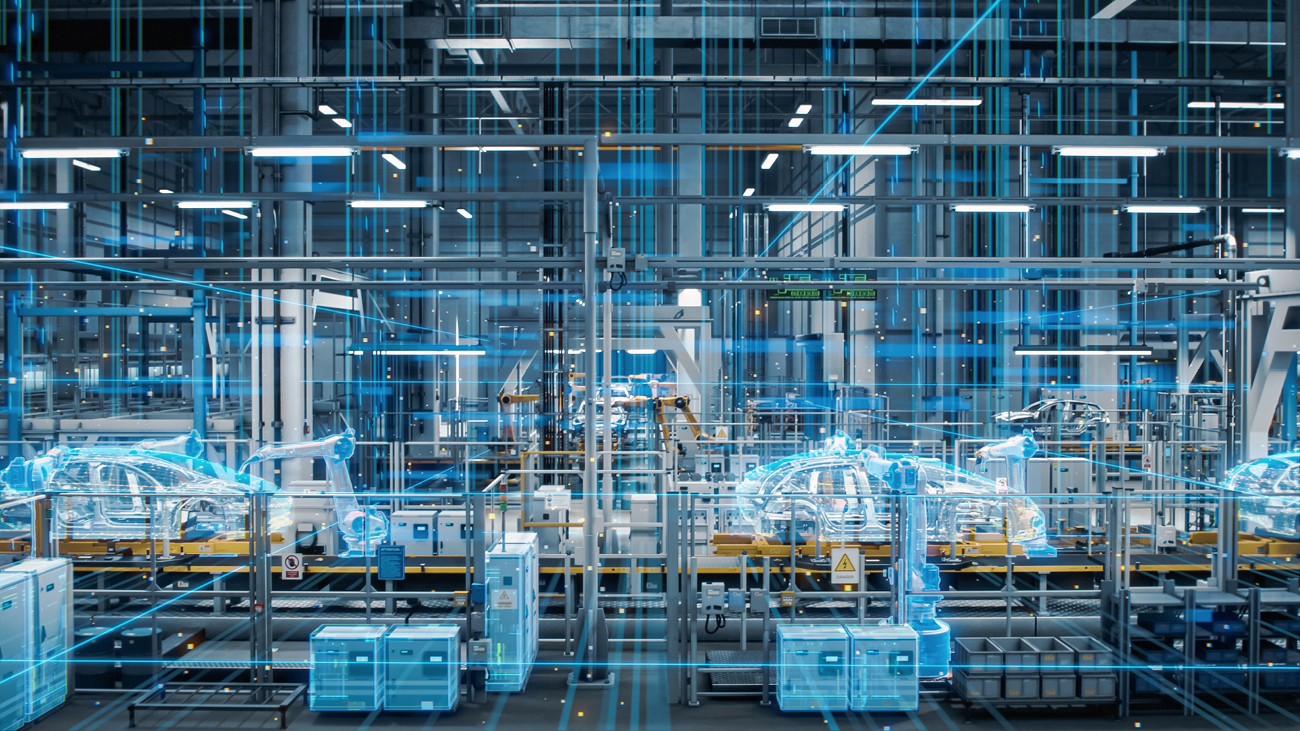
Subsequently, the digital factory will be sequentially applied to Hyundai Rotem’s main railcar series, including electric trains, trams, double-decker electric trains, and electric locomotives, aiming for continuous productivity improvement and production optimization through a reduction in design change rates. In the long term, the plan is to continuously undertake research and development to connect production processes based on big data for various railcar series, monitor them in real time using digital twins, and realize a true digital factory that can analyze and improve the situation and issues in actual production processes.