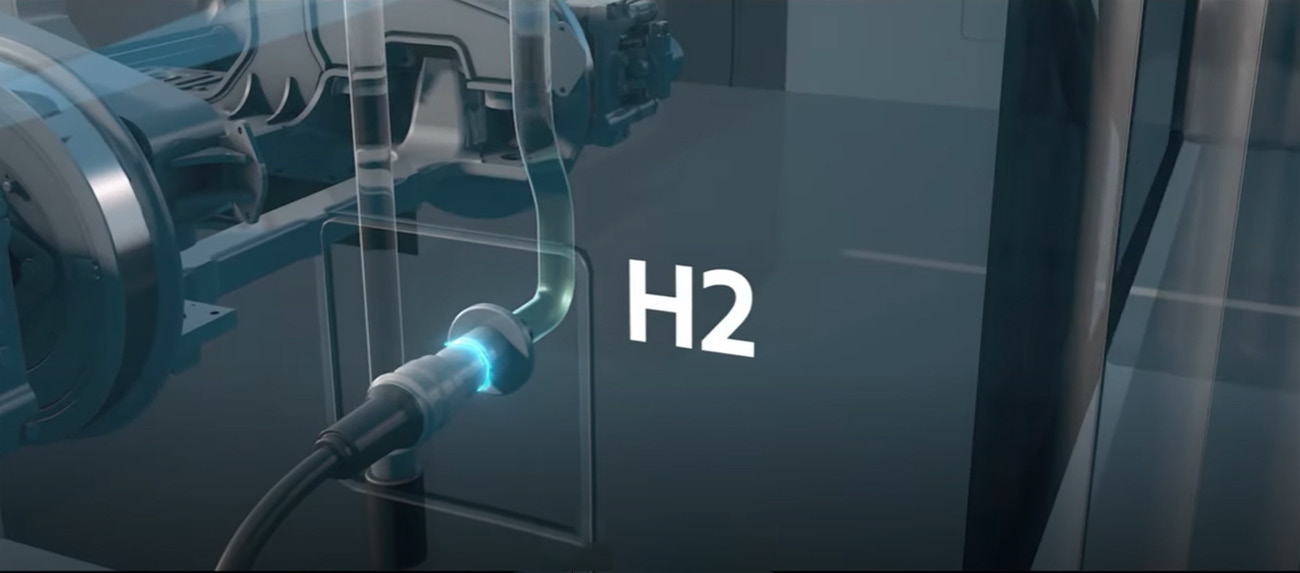
‘Liquid hydrogen’ which is currently gaining attention within the eco-friendly energy industry, refers to the liquid form of hydrogen created by cooling hydrogen in gas form at extremely low temperatures (below -253 degrees). The volume of liquid hydrogen is a mere 1/800 in comparison to gas hydrogen, which allows even more energy to be stored in the fuel tank, and the fueling speed is also significantly faster in comparison. Furthermore, liquid hydrogen-based engine locomotives are being developed to be capable of driving over 1,000km on a single charge, which makes the development of technology for the stable utilization of liquid hydrogen an essential process in the evolution of railway vehicles to achieve eco-friendly mobility.
And in the midst of such a development process, Korea Railroad Research Institute (hereinafter referred to as “KRRI”) has announced that it has successfully completed the experiment on generating and controlling electric power by feeding liquid hydrogen into a fuel cell in October. KRRI has been developing a liquid hydrogen-based hybrid propulsion system and liquid hydrogen fueling and high-speed fueling system based on the success of this experiment. This combination test was a result of success in the ‘Development of Core Technology for Liquid Hydrogen-based Engine Locomotive’ project, a joint project with Hyundai Rotem since 2021, and completion of this technology will result in the world’s first liquid hydrogen-based engine locomotive.
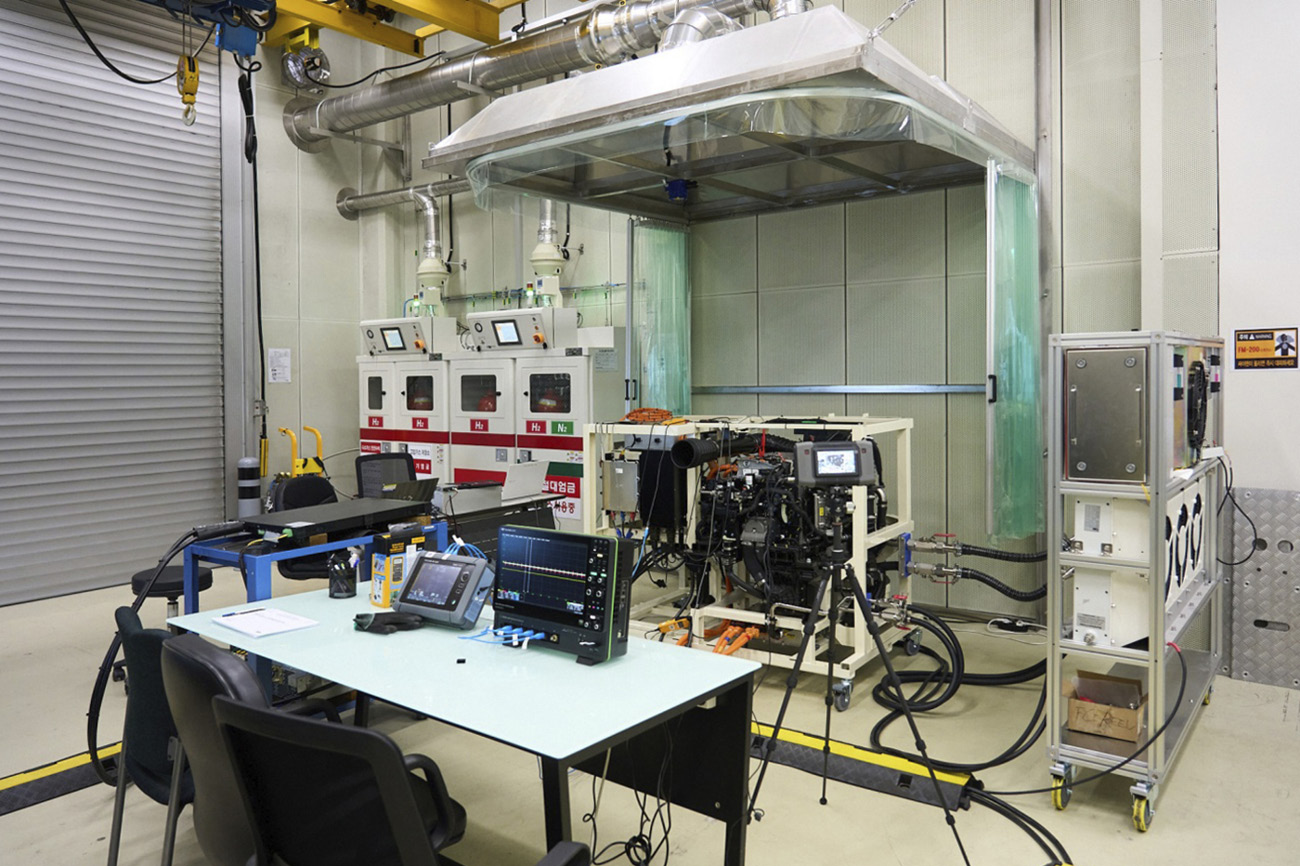
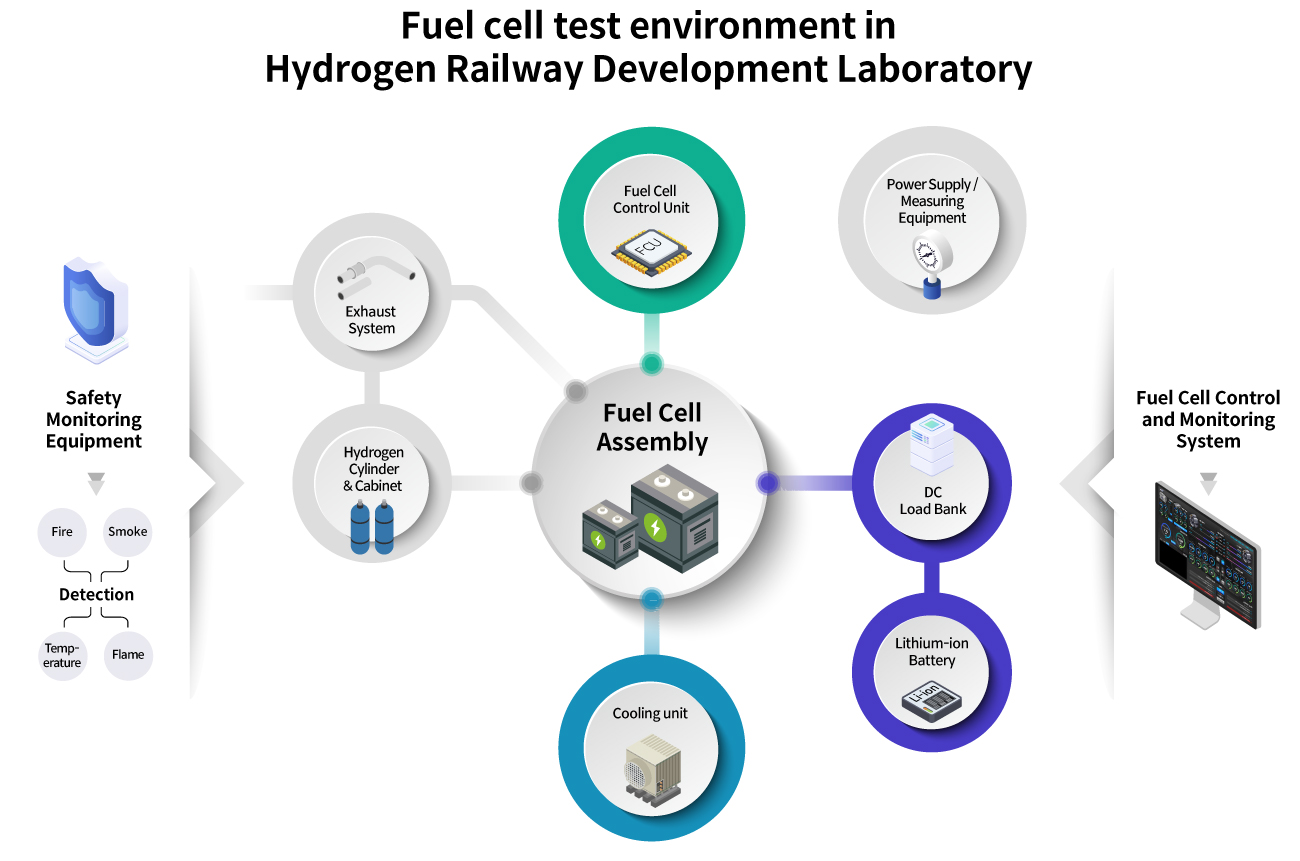
Hyundai Rotem is conducting studies across various fields above for the development and commercialization of hydrogen mobility. Recently, the company has newly established the Hydrogen Railway Development Laboratory within its Uiwang Research Institute. The purpose of this lab is to develop railway vehicles and mobility based on hydrogen fuel cells, and it is capable of testing combinations and performance of hydrogen fuel cell systems consisting of hydrogen fueling equipment, power supply, high-voltage battery, electronic load, cooling equipment, etc. Also, tests are being conducted on fuel cell output, hydrogen consumption level, efficiency, and power distribution and control of fuel cell control unit along with design verification and evaluation of functions and performance of communication interface.
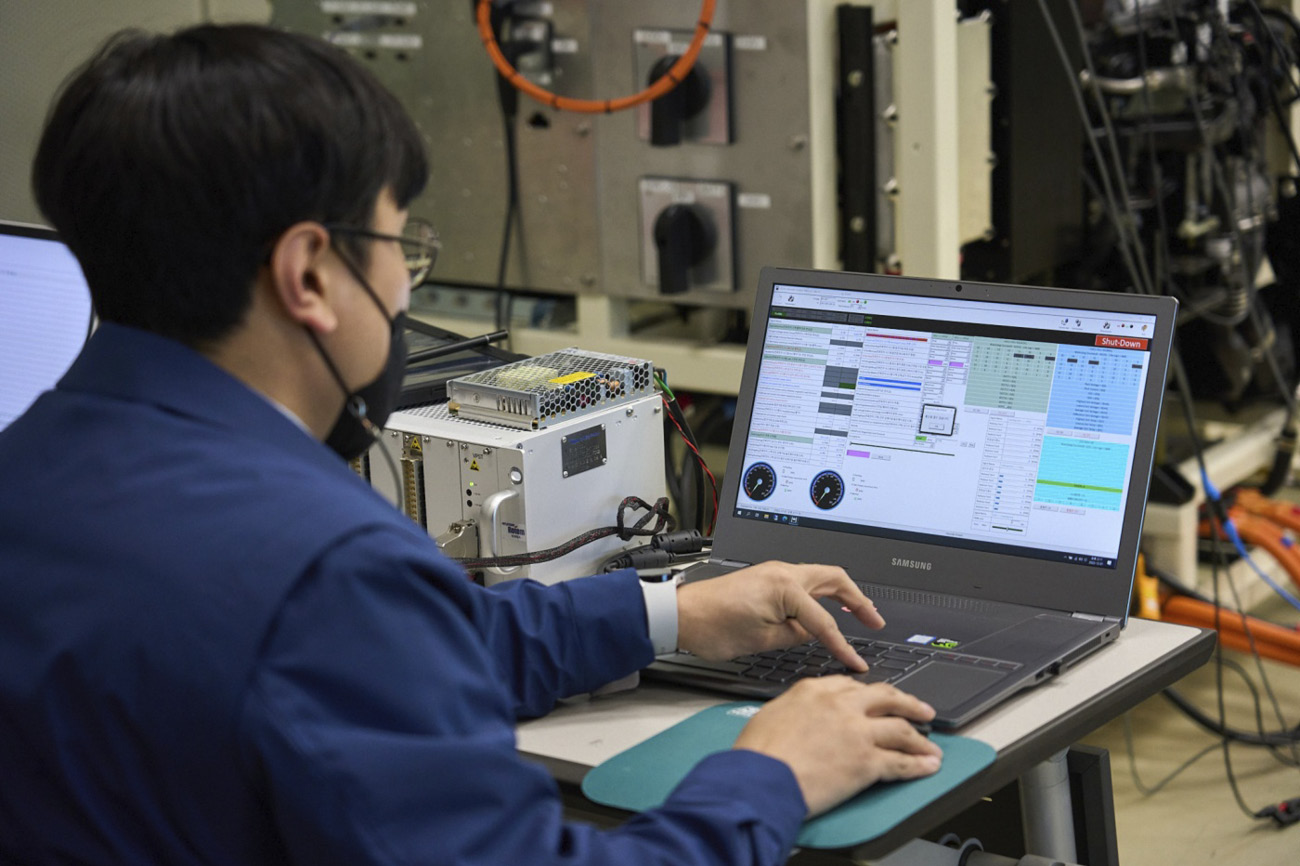
Hydrogen is a relatively difficult substance to handle due to its lightweight and rapid diffusion among gas-form substances. Therefore, the Hydrogen Railway Development Laboratory has constructed the appropriate equipment pursuant to the criteria established by Korea Gas Safety Corporation, a domestic hydrogen safety management institution, and has been conducting tests with low fueling pressure.
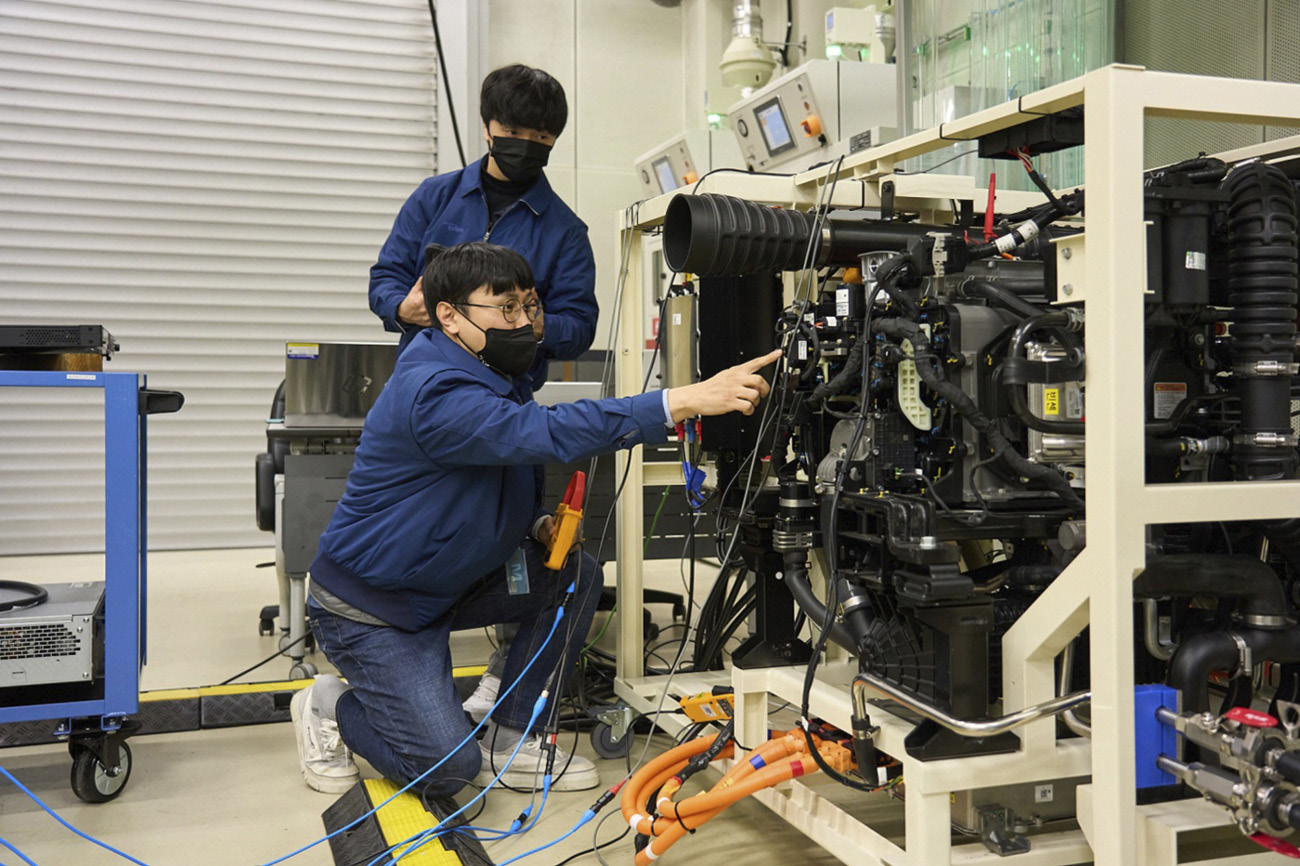
While Hyundai Rotem has been working on the development of hydrogen engine locomotives using liquid hydrogen as fuel, the company has also been working on the hydrogen-electric tram demonstration project and developing the fuel cell ranged extended electric vehicle (FC-REEV) to extend the driving distance of electric buses. Currently, a power module complete (PMC) necessary for the development of said mobility has been assigned to the laboratory. This unit cannot be operated independently and requires a separate device to supply hydrogen and oxygen. Also, it is required to undergo the process of increasing the voltage level to generate an output based on the electric power generated through a chemical reaction. During such process, the fuel cell generates thermal energy and the internal temperature of the assembly is controlled by a separate cooling unit.
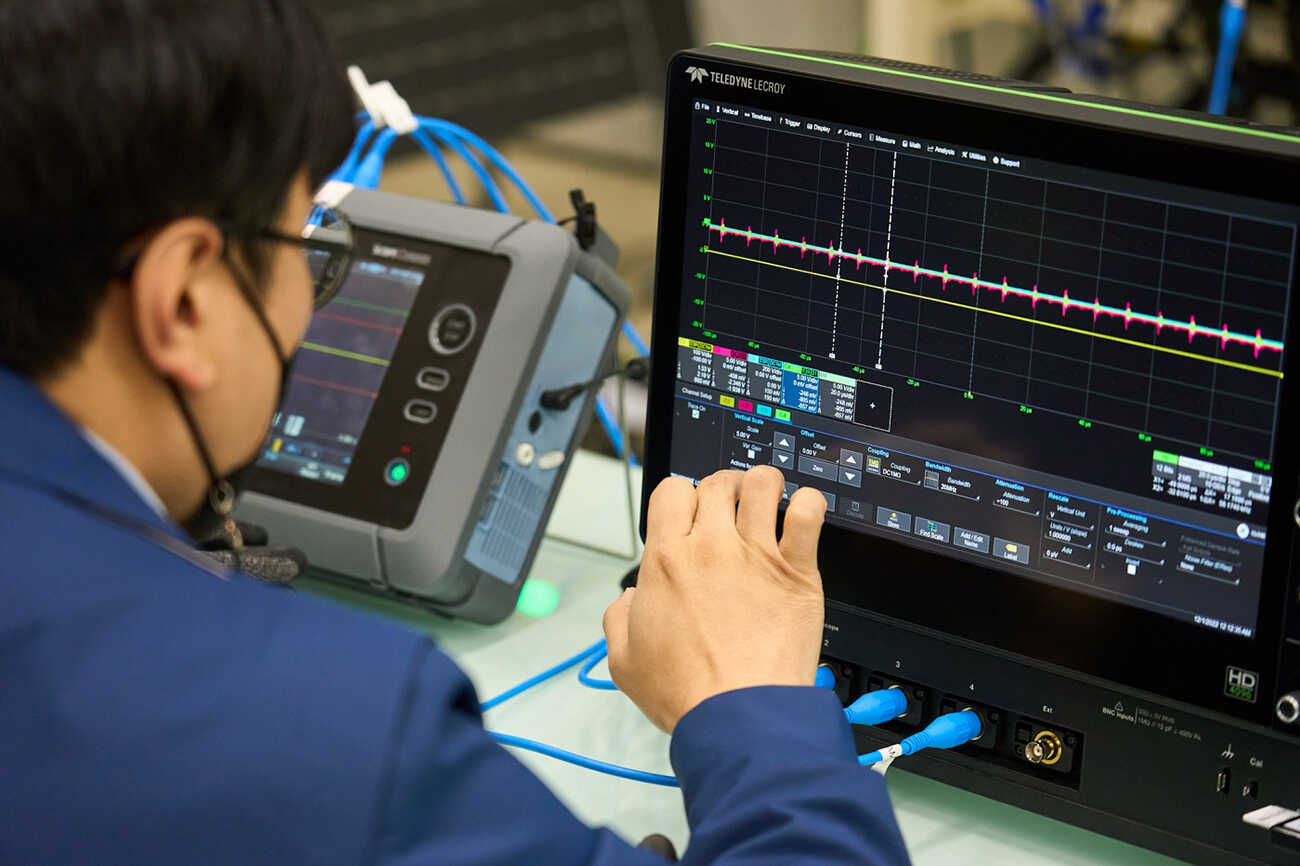
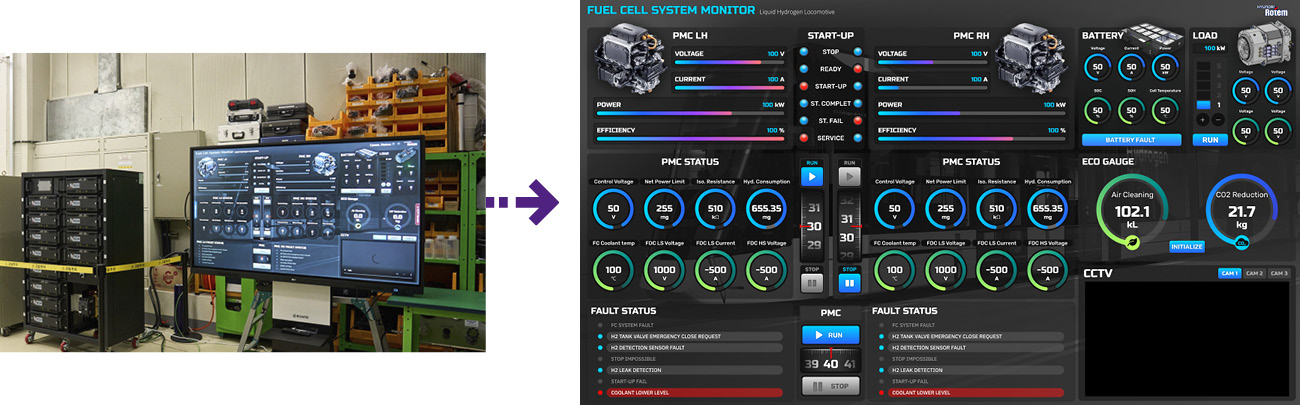
The lab can check the real-time status of the fuel cell system through its independently developed fuel cell control and monitoring system. Through this system, the lab engineers can check the amount of hydrogen fuel as well as the voltage, current, and output of the fuel cell, and even monitor the remote control functions and activity of batteries and loads. Furthermore, this system was designed to be capable of predicting the amount of air purification and reduction in carbon dioxide emission during actual operation of the vehicle. Such functions will be implemented in actual railway vehicles through the Train Control and Monitoring System (TCMS).
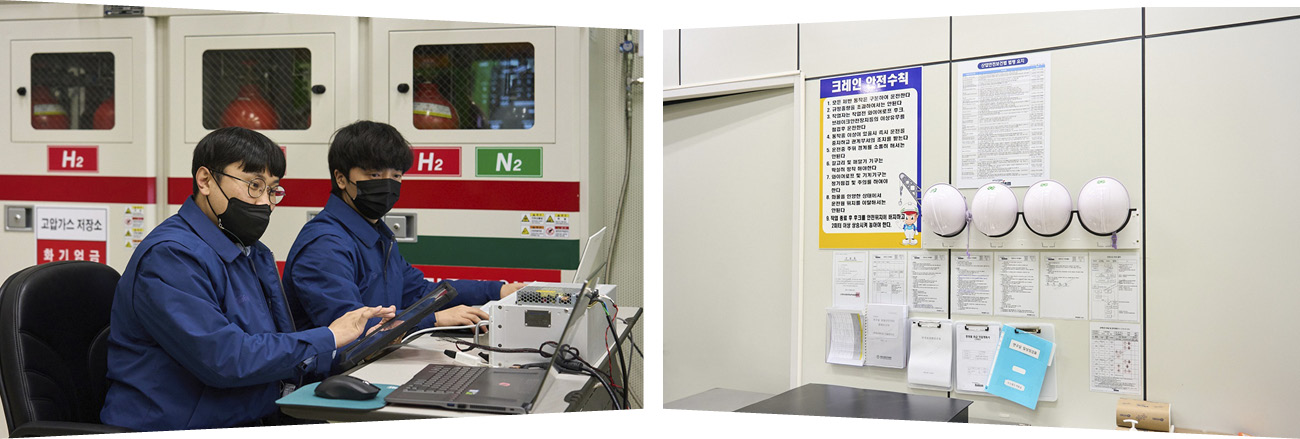
The lab has also focused on enhancing safety due to the nature of hydrogen fueling equipment in which safety is essential. Basic safety devices such as emergency interrupting devices were applied in pipes and exhaust systems for hydrogen fueling as well as numerous CCTVs for monitoring fire, smoke, etc. Also, to prevent gas leak and arc discharge that may occur during a fuel cell system test, the lab has installed mobile ultrasonic cameras as it constructed a thorough safety system for testing.
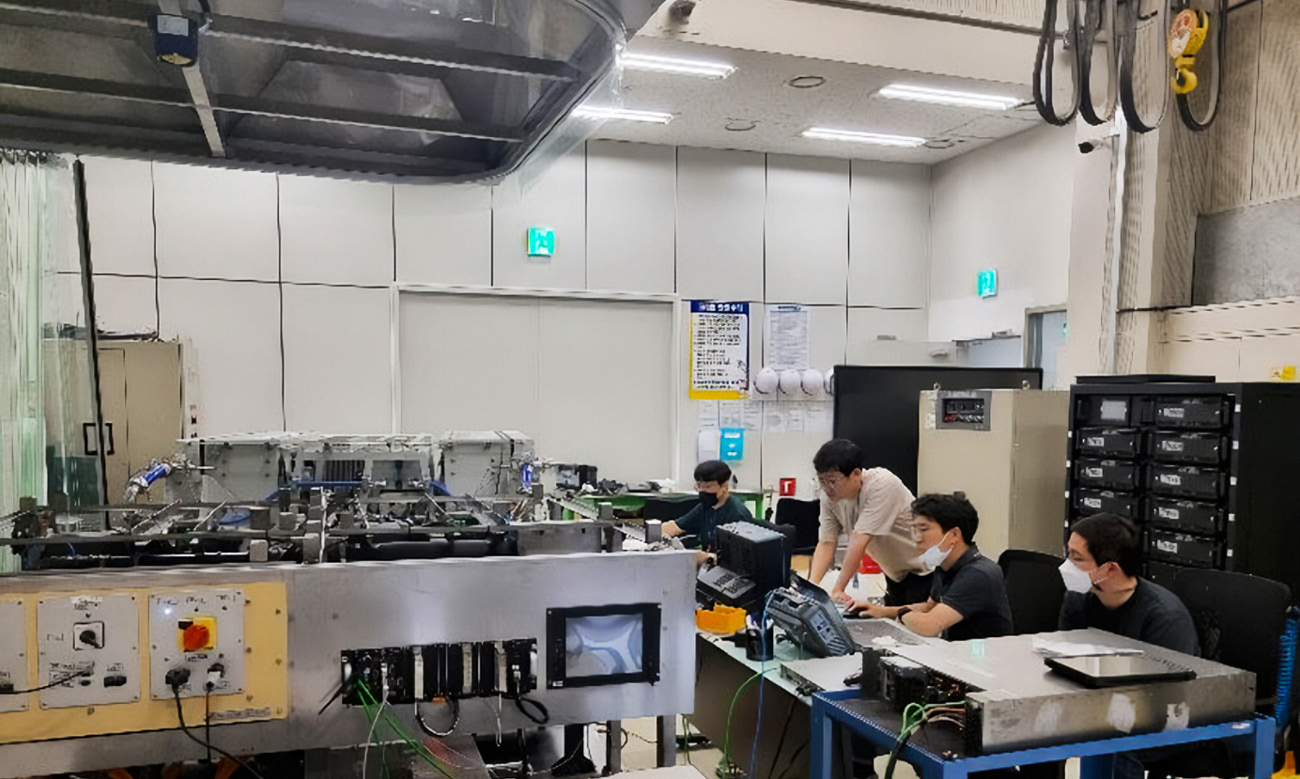
Meanwhile, Hyundai Rotem has been strictly diagnosing lab safety and equipment conformity through the commissioning tests of Hyundai Motor Company, the supplier of PMC. This includes the process of inspecting and improving the basic lab conditions such as internal temperature and atmospheric pressure, along with other conditions required for testing hydrogen fuel systems. Through such processes, Hyundai Rotem has been continuing its improvement activities to complete a safer lab testing system. Also, Hyundai Rotem has previously received approval for 16 testing items including conductivity, insulation resistance, gas leak, air supply, and noise, from the global testing and certification agency of TUV SUD through the official certification test on fuel cell components in July.
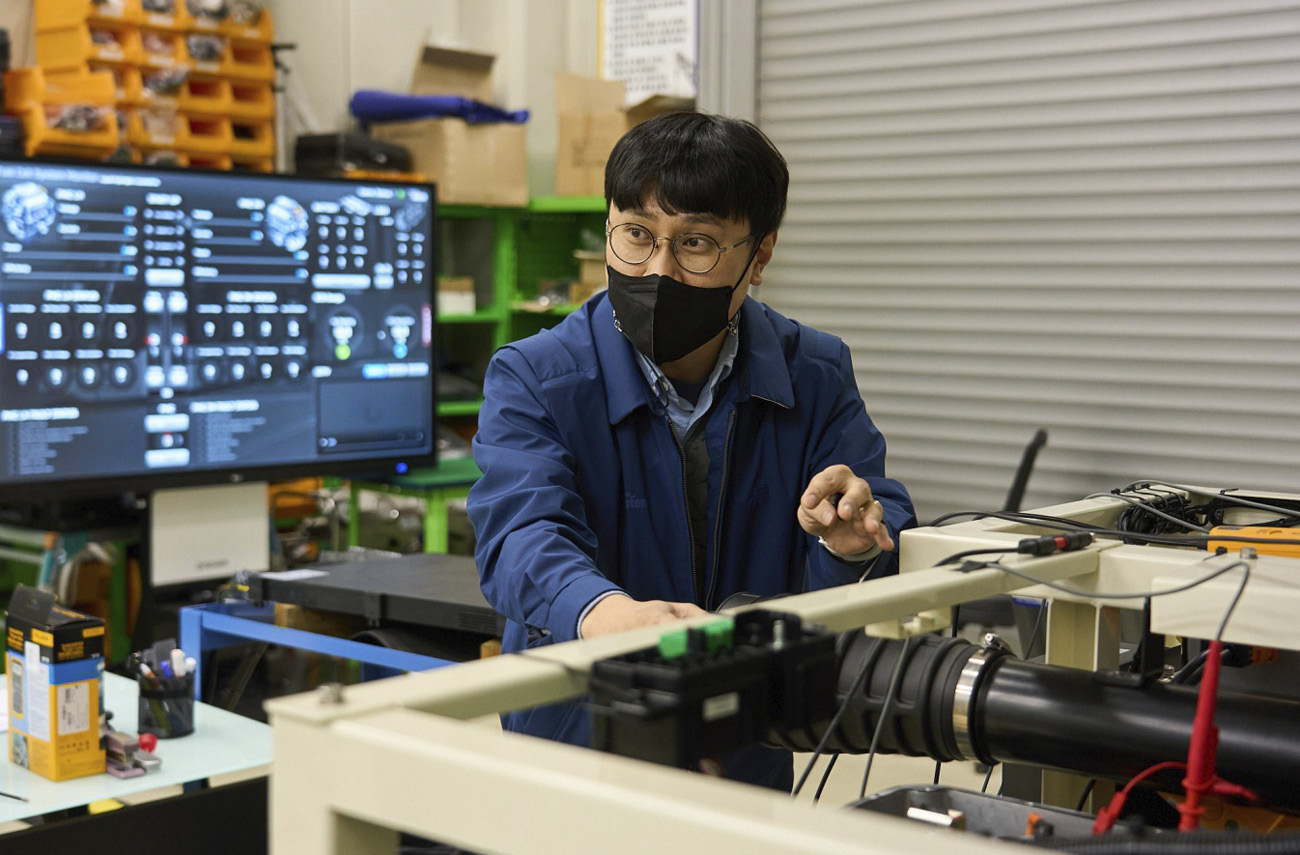
Hyundai Rotem is establishing the foundation for quick implementation of advanced concept hydrogen mobility such as FC-REEV, along with a demonstration of a hydrogen-electric tram through the establishment of the Hydrogen Railway Development Laboratory. Hyundai Rotem is also securing technological stability while also planning to apply an integrated hydrogen control system utilizing digital twin technology and a maintenance system based on big data and cloud to achieve a smart and eco-friendly hydrogen mobility society.