Hyundai Rotem has formulated a strategy to achieve carbon neutrality by 2050. By 2030, the company plans to reduce carbon emissions from its business sites and the value chain by 42% and 25%, respectively, compared to the end of 2022. In the long term, the goal is to achieve complete carbon neutrality by 2050. Hyundai Rotem’s carbon neutrality strategy, disclosed in November 2023, was formulated reflecting the greenhouse gas reduction goals recommended by the global coalition Science Based Target initiative (hereinafter referred to as SBTi)*.
* The SBTi, initiated by organizations such as the Carbon Disclosure Project (CDP), UN Global Compact (UNGC), World Resources Institute (WRI) and World Wildlife Fund (WWF), aims to reduce greenhouse gas emissions based on scientific data, with a target of limiting the global average temperature increase compared to pre-industrial levels to within 1.5°C.
Hyundai Rotem, declaring carbon neutrality by 2050, is expanding its portfolio of environmentally friendly products and services, including hydrogen mobility, hydrogen infrastructure, and power distributed high-speed trains. The company is actively pursuing carbon reduction throughout the lifecycle of its entire product range. These initiatives have already shown tangible results, as Hyundai Rotem achieved an ESG (environment, social, governance) comprehensive rating of A for three consecutive years in the 2023 ESG evaluation and rating announcement by the Korea Institute of Corporate Governance and Sustainability (KCGS).
The Rail Solution sector, in particular, plays a significant role in Hyundai Rotem’s advancement as a leader in sustainable management. As of 2022, 54% of Hyundai Rotem’s consolidated revenue was found to be eligible for the Korean K-Taxonomy*, with the Rail Solution sector accounting for an impressive 95% of green revenue in railcar sales. This proportion is expected to increase further with the expansion of environmentally friendly businesses, including hydrogen.
* Guidelines established by the Korean government to promote carbon neutrality Defines the scope of green economic activities contributing to the six environmental goals: greenhouse gas reduction, climate change adaptation, sustainable water conservation, resource circulation, pollution prevention and management, and biodiversity conservation.
Hyundai Rotem introduces two representative eco-friendly core technologies that the company has consistently invested in, beyond hydrogen railcars.
1. Green Technology Certified “Zero Speed Regenerative Braking” for Propulsion Control Device
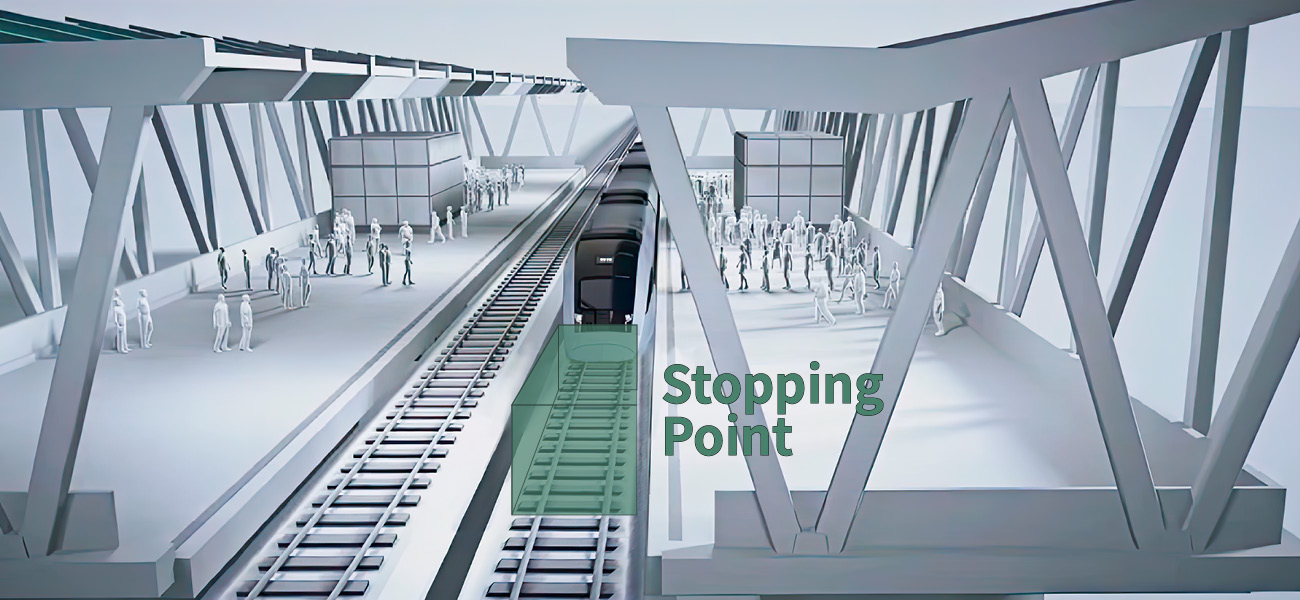
The “Zero Speed Regenerative Braking” technology involves continuously using regenerative braking from the moment an electric vehicle comes to a stop until the complete standstill. Hyundai Rotem initiated the development in 2018, applied the technology to Seoul Metro Line 2 cars (214 units) the following year, and completed patent registration in 2021. In 2022, it received Green Technology Certification,* acknowledging its environmental friendliness.
* Green Certification, organized by the Korea Institute for Advancement of Technology, certifies and supports promising green technologies or projects under the “Low Carbon Green Growth Basic Act.” Green Technology Certification specifically recognizes technologies that minimize greenhouse gas and pollutant emissions throughout the entire process of social and economic activities.
Regenerative braking involves utilizing the power generated when the traction electric motor transitions from the propulsion mode to the braking mode (when the vehicle speed decreases). This power can be used as traction energy for adjacent vehicles or stored in batteries installed in substations or vehicles. Regenerative braking is commonly found in electrically powered vehicles, including hybrid electric vehicles (HEV), plug-in hybrid electric vehicles (PHEV), battery electric vehicles (BEV), and fuel cell electric vehicles (FCEV). It is widely used in railcars such as electric locomotives and high-speed trains. In South Korea, regenerative braking technology has been applied since the early 1980s, beginning with the Seoul Metro Line 2 train cars.
A smart solution resolving the drawbacks of conventional regenerative braking technology
The domestically operated VVVF inverter-controlled electric railcars were fundamentally equipped with regenerative braking, which reverses the generating action of the traction motor (propulsion electric motor) during braking. However, accurate control of regenerative braking at low speeds was challenging, leading to the simultaneous use of air braking (frictional braking) alongside regenerative braking. At the point of stopping, typically between speeds of 10-15 km/h, regenerative braking gradually decreased. From around speeds of 3-5 km/h, only full cross-control air braking, without regenerative braking, was used to bring the vehicle to a complete stop. This method inevitably resulted in friction noise and the generation of fine dust due to brake pad wear. In addition, the braking deceleration was not uniform, affecting precise positioning during stops.
Hyundai Rotem’s “Zero Speed Regenerative Braking” technology diverges from conventional methods by utilizing regenerative braking all the way to zero speed. Thanks to this, there is no mechanical friction noise and it significantly contributes to reducing fine dust from brake pad wear. Moreover, by generating power through regenerative braking all the way to zero speed, there is an expected effect of saving power consumption. It offers the advantages of precise stopping and improved ride comfort during stops. It can be implemented through software without the need for additional devices or components in existing railcars, demonstrating excellent technological applicability.
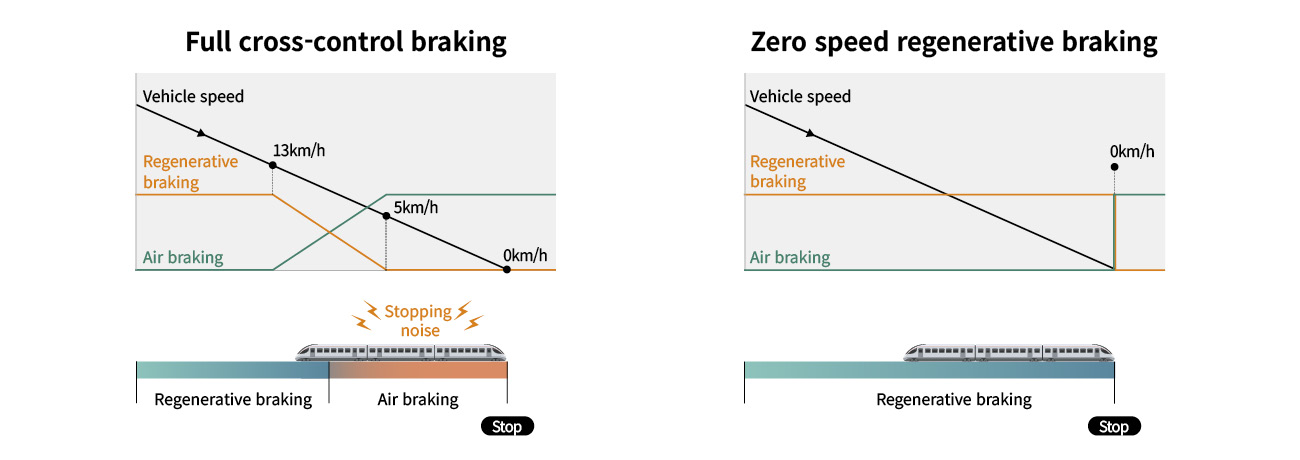
Technology Performance Verified through a precise test
The zero speed regenerative braking technology was initiated in March 2018 and completed in July 2019. Subsequently, real-world testing was conducted on 214 railcars equipped with zero speed regenerative braking and 280 existing cars with full cross-control braking on the Seoul Metro Line 2. Precise tests were carried out to measure power consumption, fine dust generation and noise levels.
Firstly, regarding power consumption, the results revealed that the railcars equipped with zero speed regenerative braking showed an average power consumption reduction of 4.163 kWh on the Seoul Metro Line 2, both inbound and outbound, compared to the conventional VVVF-powered cars. When translated into a single trainset, this amounted to an approximately 20.8 kWh reduction in power consumption. Based on Hyundai Rotem’s supply of 21 trainsets, if operated seven times a day for 300 days annually, the expected annual power savings would be significantly enhanced, reaching 917,280 kWh, an improvement of 3.58% compared to the conventional vehicles.
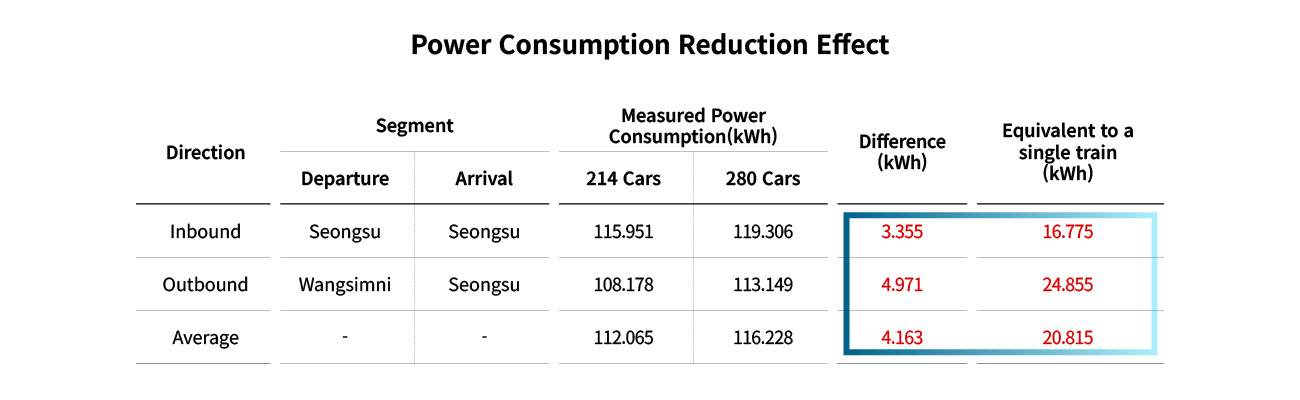
Brake pad wear tests were conducted from April 2020 to May 2021. The annual brake pad wear of a single trainset consisting of a power car and non-power cars was measured. The results indicated that the brake pad wear of railcars equipped with zero speed regenerative braking was 23.4 kg less than that of the full cross-control braking vehicles. This translates into an annual reduction of 491.4 kg of brake dust for 21trainsets equipped with zero speed regenerative braking.

Stationary noise testing was conducted at two locations on Seoul Metro Line 2: Gangbyeon Station (semi-enclosed screen door) and Nakseongdae Station (enclosed screen door). In the case of Gangbyeon Station, the noise from the vehicles equipped with zero speed regenerative braking was measured to be at least 8.1 dB to a maximum of 13.2 dB lower compared to the conventional vehicles. At Nakseongdae Station with enclosed screen doors, the gap widened further, showing an excellent noise reduction effect ranging from 10.6 to 23.7 dB. As the sound energy decreases by 50% when the noise is reduced by 3 dB, it is expected that through zero speed regenerative braking technology, an 80% reduction in noise can be achieved.
Full Cross-control Vehicles (280R)
Zero Speed Regenerative Braking Vehicles
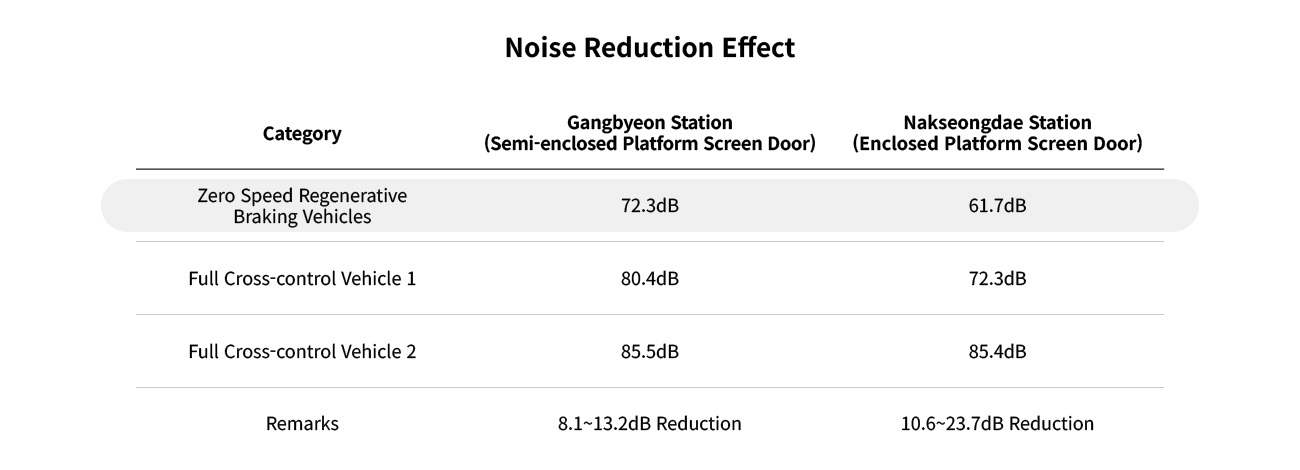
In addition, during the precise stopping tests conducted on Seoul Metro Line 2, the vehicles achieved a 100% precision stopping rate, stopping within 30 cm at a total of 1,634 stations. Thanks to meticulous jerk (acceleration per hour) control, the zero speed regenerative braking vehicles maintained regenerative braking up to zero speed, resulting in a gentle slope of deceleration at the stopping point, as shown in the deceleration jerk graph below. This confirms a noticeable improvement in riding comfort.
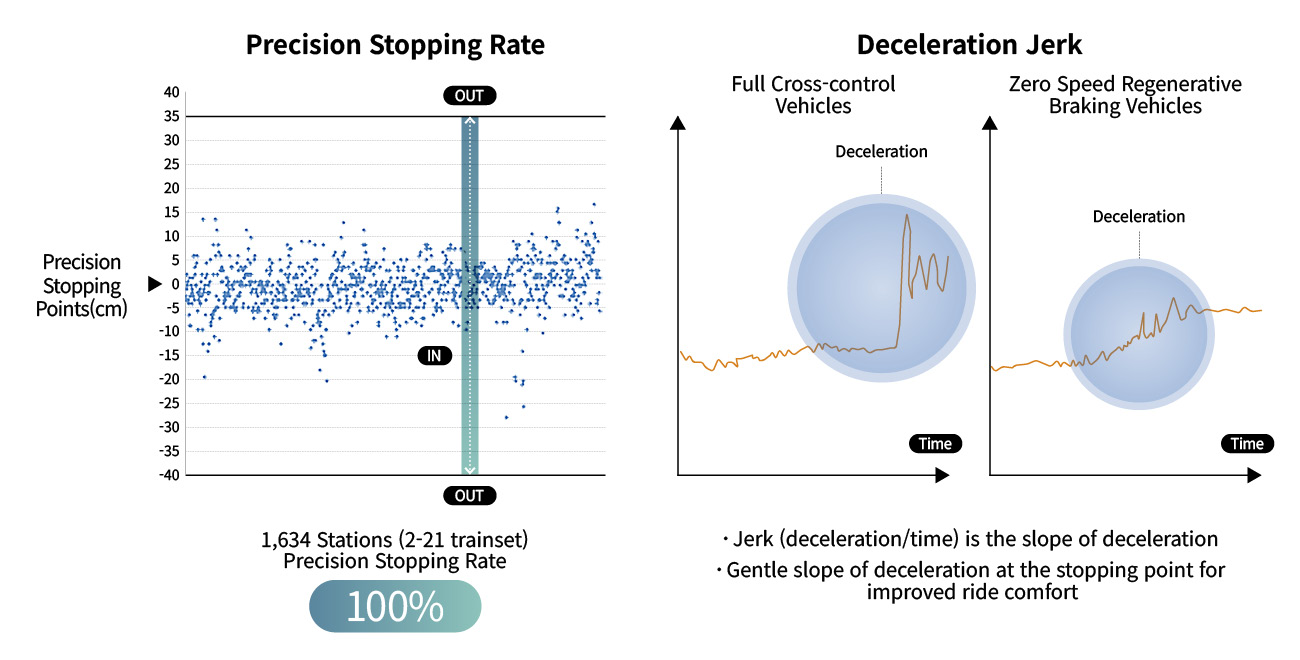
The zero speed regenerative braking technology brings about a distinct green impact
It is more meaningful in terms of decarbonization. The trains equipped with this technology can save an annual power consumption of 917,280 kWh, reducing annual carbon dioxide emissions by 406,997 kg (based on 0.4437 kg of carbon dioxide emissions per kWh). This is equivalent to planting 61,666 pine trees annually.
The minimization of brake pad wear leads to a reduction in fine dust emissions (491.4 kg). The reduction in fine dust obtained from operating vehicles with zero-speed regenerative braking technology is comparable to the effect of a forest absorbing pollutants, equivalent to 2.9 hectares (based on an annual pollutant absorption capacity of 168 kg per hectare of forest). Considering that a significant portion of the train operation section is in underground spaces with difficulties in ventilation, the environmental improvement effects of zero-speed regenerative braking technology are even more significant.
The reduction in friction noise at the stopping point (8.1-23.7 dB) alleviates auditory discomfort for passengers, and the dramatic improvement in precision stopping provides operational accuracy for subway operators.
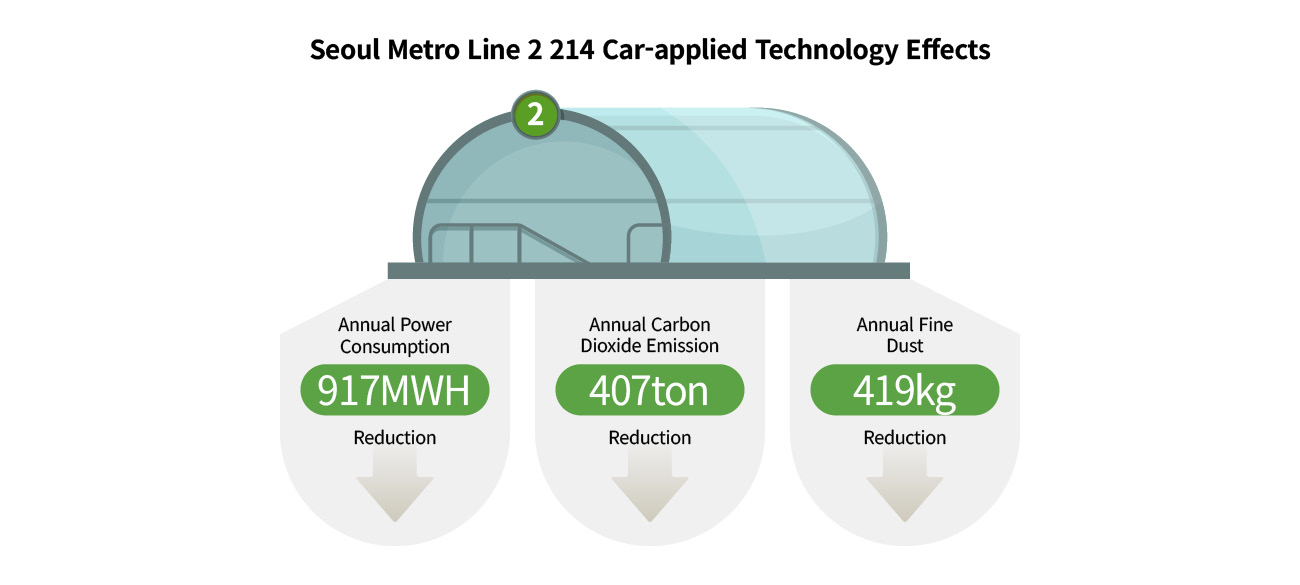
The zero-speed regenerative braking technology, which obtained “Green Technology Certification” at the end of 2022, is already in operation on Seoul Metro Line 2 and the Istanbul Metro(Mahmutbey) in Turkiye. The target vehicles are expected to gradually expand. The GTX-A train equipped with zero-speed regenerative braking technology is set to operate on the opening GTX-A line at the end of March 2024. Additionally, the general type 50 cars on Seoul Metro Line 4 Gwacheon-Ansan Line and the Suin-Bundang Line with 24 cars are currently undergoing testing for actual operations.
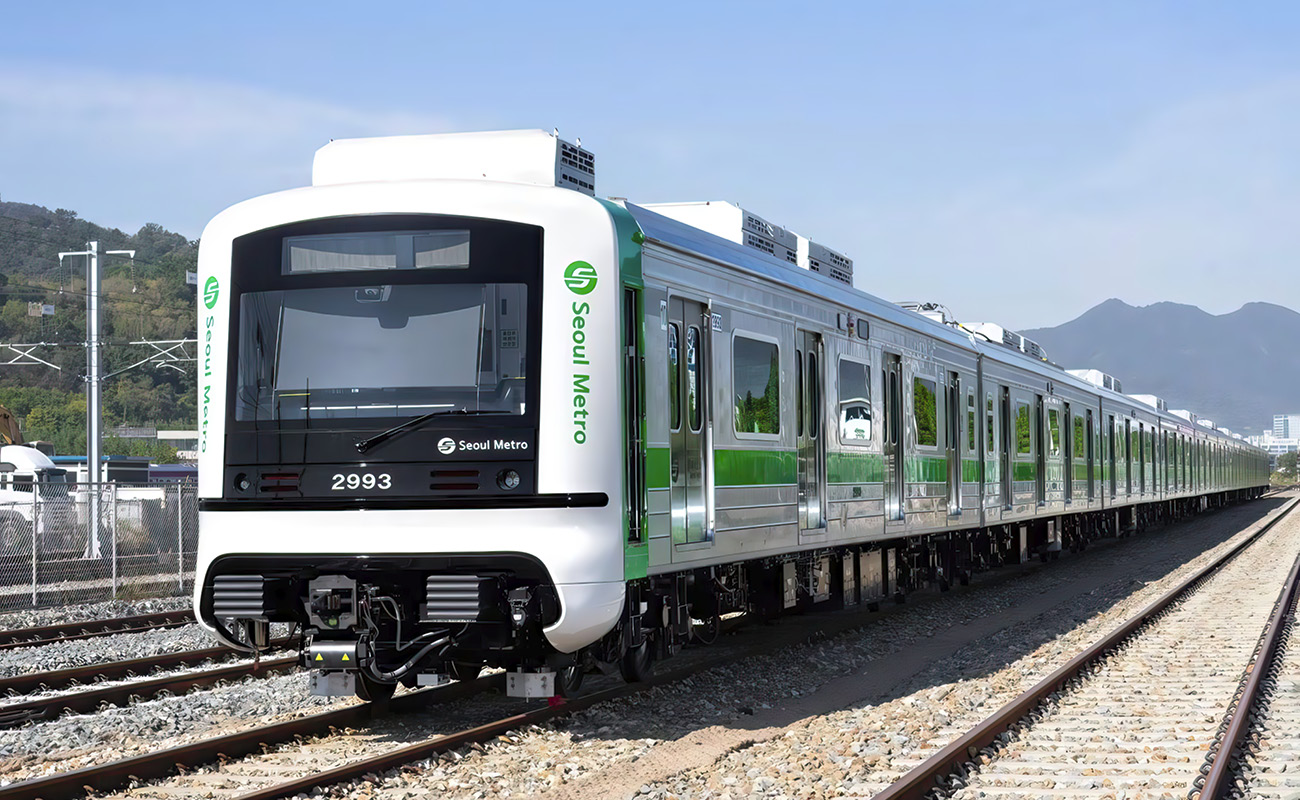
2. “Energy-saving Automatic Train Operation” Technology, Winner of the Top-10 Railway Technologies Award in Korea
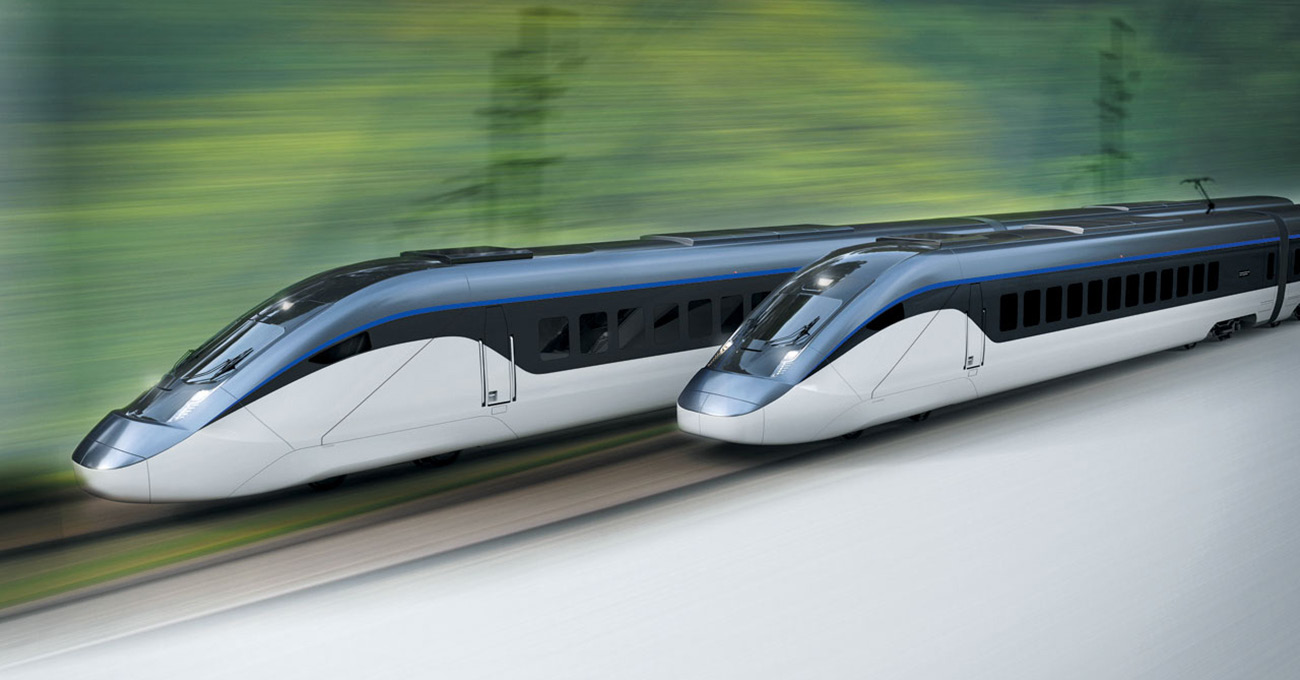
The “Energy-saving Automatic Train Operation” technology is one of Hyundai Rotem’s representative railway technologies that won the “Top-10 Railway Technologies Award” in 2023. The “Top-10 Railway Technologies Award” has been presented by the Korean Society for Railway since 2015 and Hyundai Rotem has proven its advanced railway technology development by winning the award a total of five times, including the year 2023.
The award-winning “Energy-saving Automatic Train Operation” technology in 2023 generates a driving pattern that minimizes power consumption before the train operation by considering the characteristics of the train’s motor, gradient, track conditions, and train characteristics. It then performs automatic train operations (ATO) according to this pattern. This technology was selected as a national research project and underwent research and development for 2 years and 9 months from April 2018 to December 2020. Currently, it is conducting power consumption reduction verification through on-site tests for follow-up research and development projects.
Challenges in reducing power consumption with existing automatic train operation technology and their solutions
Existing ATO technology focuses only on adhering to track speed limits when generating driving patterns (operating profiles). Typically, it aims to comply with the track’s restricted speed, leading to repetitive control of acceleration and braking based on the difference between the target speed and actual speed. This approach may result in lower energy efficiency compared to the manual operations by experienced engineers with years of operational experience. In particular, in short-distance sections with high track speed limits, the frequent transitions between acceleration and braking control increase the train’s power consumption significantly.
Hyundai Rotem’s energy-saving automatic train operation technology addresses this issue by receiving information necessary for energy-efficient operation in advance and controlling train operation based on the generated operating profile. The process can be summarized as follows:
1. Receive route information* from ground devices for the train to operate
* Information on track sections based on distance, including speed limits, gradient, curvature, etc.
2. On-board devices receive the weight value of the train, including the changing passenger weight during operation.
3. Calculate the operating profile that the train will use for automatic operation before the train operation, using information received from ground devices and the train.*
* Reflection of train characteristics such as traction force, rotational mass based on the train’s driving inertia, driving resistance, and gradient resistance during calculation
4. Calculate an energy-efficient operating profile (train propulsion/control braking pattern) that allows a reduction in power consumption during train operation
5. Control the train to follow the operating profile with the applied energy-efficient automatic train operation technology during train operation, maximizing the effect of energy savings
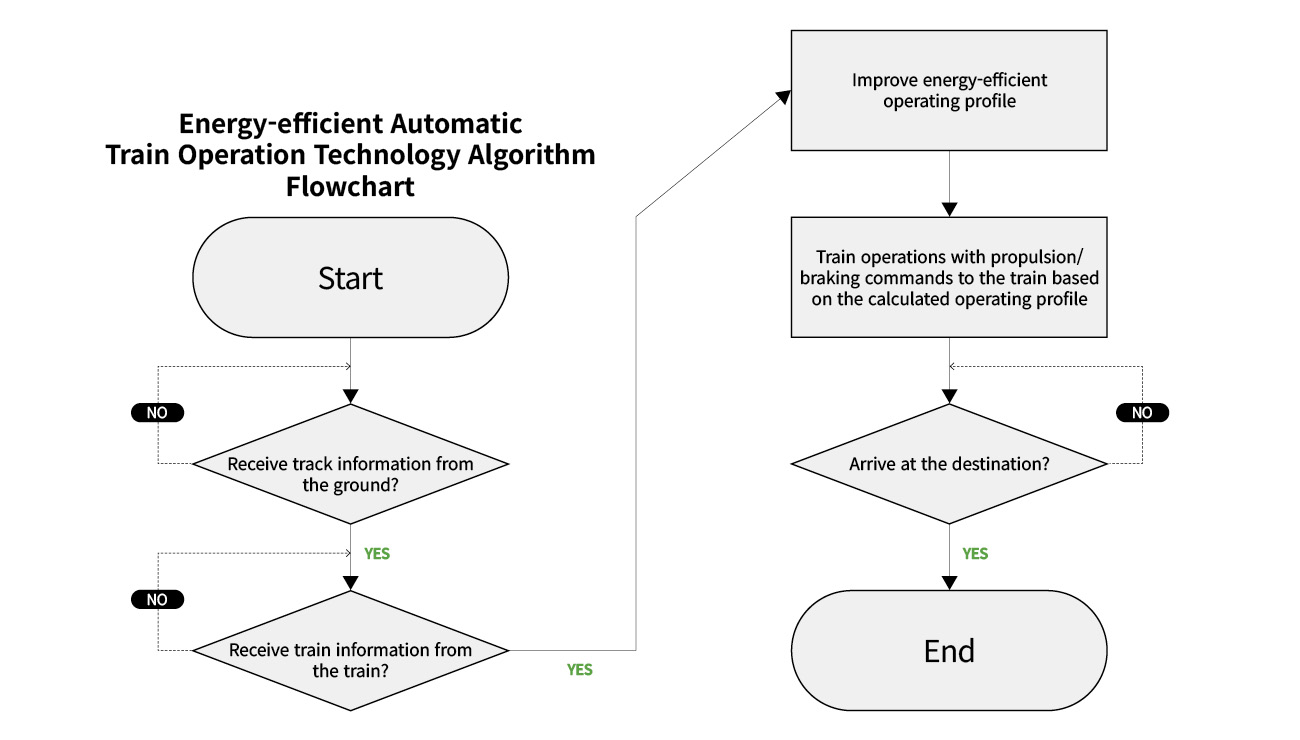
Expected Effects Verified through Simulation
So, how much energy-efficient operation can be achieved with the energy-saving automatic train operation technology? The following figures compare the records of operation using the conventional automatic train operation technology (Figure 1) with the simulation results of operating according to the profile of the energy-saving automatic train operation technology (Figure 2).
Upon comparing the two figures, it can be observed that the energy-saving automatic train operation technology uses less propulsion at the start and does not use propulsion in the previous section before initiating braking. By reducing the number of propulsion controls and maximizing non-braking driving sections, the energy consumption of the train can be minimized. The simulation results demonstrate that the energy-saving automatic train operation technology can consume less power compared to the conventional automatic train operation technology.
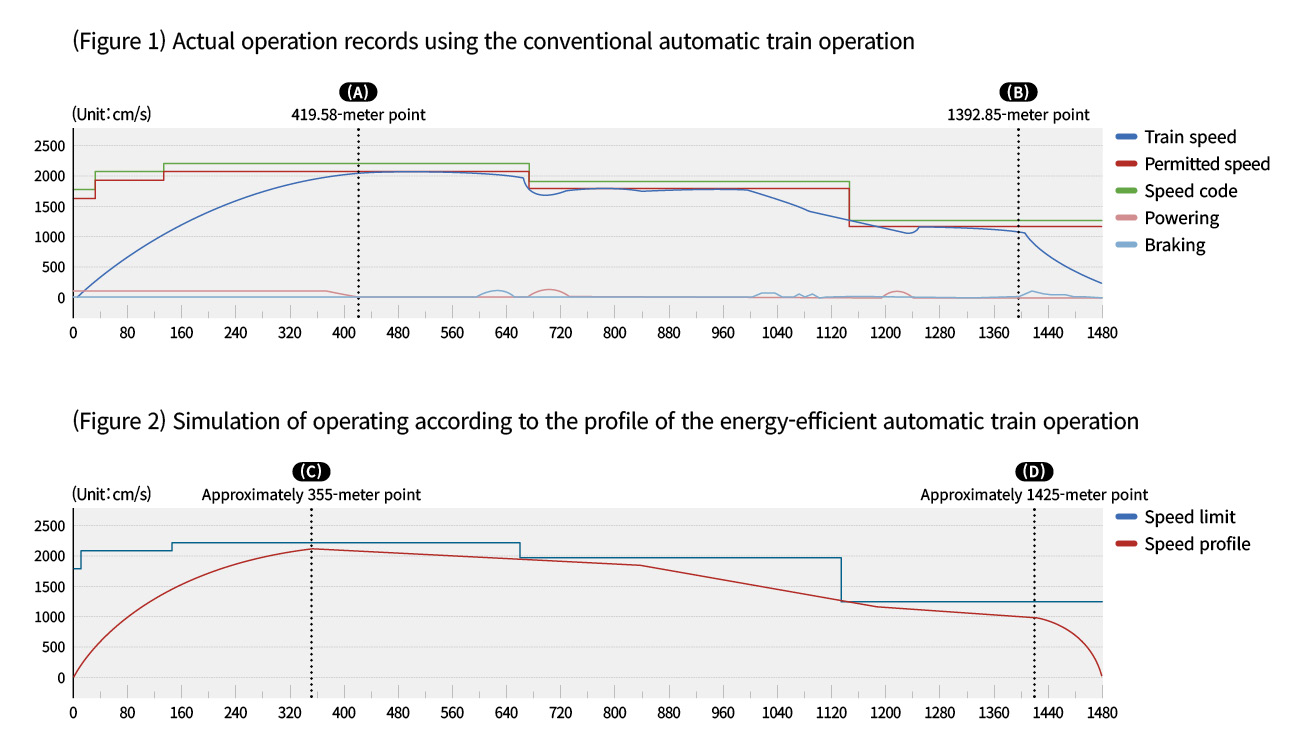
Significant reduction in power consumption and operating costs compared to the conventional ATO
The on-site test of the energy-saving automatic train operation was conducted on Seoul Metro Line 3, targeting train No.313, operating on the up and down lines of four stations (Juyeop – Jeongbalsan – Madu – Baekseok) for a total of three sections (3.883 km). The test confirmed the reduction in energy consumption through normal mode (regular operation) and eco mode (efficient driving pattern operation), comparing the accumulated power consumption values for each mode. The average unit price per kWh was estimated at 131.7 KRW.*
* KOSIS National Information Portal Electricity Consumption Status (Subway) average unit cost per kilowatt-hour (kWh)
The test results showed a total power reduction of 13 kWh for both the upline (Baekseok to Juyeop) and downline (Juyeop to Baekseok). For the upline, there was a 9% improvement with 7 kWh less power consumption compared to normal mode, and for the downline, a 7% lower power consumption with a saving of 6 kWh compared to normal mode. On a test section basis, moving through a total of six stations and achieving an average power reduction of approximately 2 kWh per station, the energy-saving effect was notable.
When applied to the actual operational situation of Seoul Metro Line 3, considering approximately 2,150,000 KRW per day, about 64,670,000 KRW per month, and around 770 million KRW in cost savings per year can be expected.*
* Average unit cost per kilowatt-hour (kWh) is 131.7 won, with 33 stations per one-way travel, 248 one-way trips per day, based on 8,184 station segments per day

Effect of Carbon Emission Reduction Equivalent to Planting 250,000 Pine Trees
The energy-saving effect is also noteworthy. When reflecting the confirmed per-station average energy savings (2 kWh) from the current test on the actual operation situation of Seoul Metro Line 3, an annual reduction of approximately 5.89 million kWh* in power consumption can be achieved.
* Based on 2 kWh of power consumption per station segment, 33 one-way travel segments per session, 248 one-way travel sessions per day and a total operation for 360 days annually
This means that by introducing the energy-saving automatic train operation technology, it is possible to suppress the emission of approximately 3,130 tons of carbon dioxide annually. This is equivalent to the carbon-neutral effect expected when planting around 250,000 pine trees.*
* Based on the carbon absorption index of central region pine trees from the National Institute of Forest Science’s “Carbon Tree Calculator,” Korea Forest Service
The expected benefits of the energy-saving automatic train operation technology go beyond just reducing power consumption and carbon dioxide emissions. Reducing unnecessary train braking can minimize the cost of replacing brake pads, and the predictability of the lifespan of train components is much smoother with a consistent operating pattern. The improvement in the passenger experience due to the reduced number of transitions between acceleration and braking during train operation is also a positive aspect.
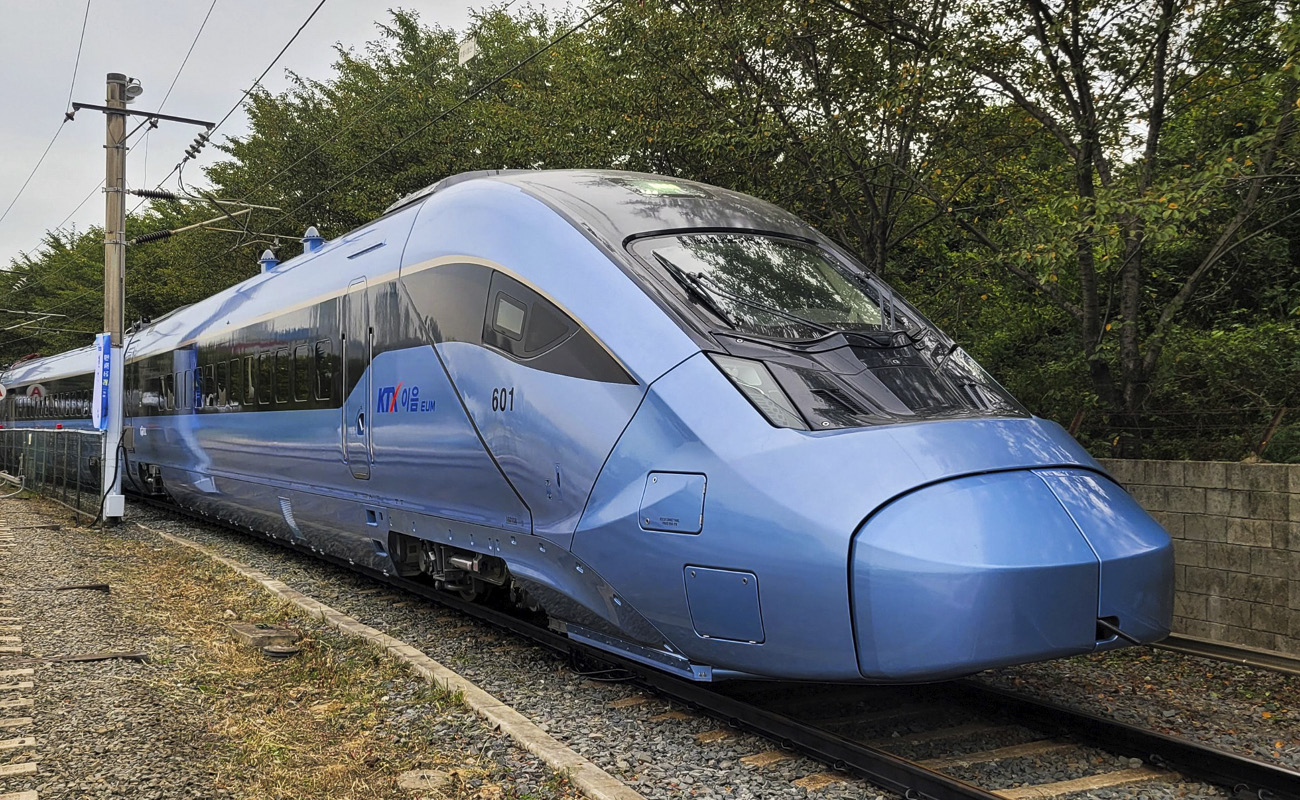
Having completed four years of development and verified through in-train tests, the energy-saving automatic train operation technology is expected to contribute to advancing the carbon-neutral era when applied to urban railways, general railways, and high-speed rail routes, including EMU-320.