Recently, as the need to reduce greenhouse gas emissions and energy consumption has emerged due to global environmental regulations, various efforts have been made for efficient energy consumption as well as eco-friendly power sources of various transportation systems such as aircraft, automobile, and railway. Among them, interest in weight reduction, which is the most effective, has been growing. The weight reduction of railway vehicles not only has an eco-friendly effect, but also has effects such as reduction of propulsion energy, reduction of vibration and noise, and reduction of track maintenance costs, so that Korea as well as traditional railway advanced countries such as Japan, Germany and France are continuing research and development. In addition, the weight management process, which is a method of evaluating and managing the entire process for reducing the weight of railway vehicles, is a very important factor in the design of railway vehicles. We looked into how the weight management process of railway vehicles is operated, and what effects will be obtained through reducing the weight for the stability of the train and the weight reduction from it.
The Importance of Railway Vehicle Weight Management
The weight of railway vehicles has a significant impact on the performance of trains. Therefore, minimizing the difference between the total weight of the vehicle predicted at the design stage and the actual weight of the vehicle that has been manufactured is a very important indicator to determine the success of weight management. In addition, by examining the weight distribution of the vehicle from the design stage and arranging the positions of various devices so that they are evenly distributed on the front and rear bogies and left and right wheels, it can prevent uneven wear of wheels and bearings that may be caused by weight imbalance during operation. In addition, the weight of railway vehicles is closely related to dynamic characteristics, structural strength, non-flammable/flammable fire code, and power consumption, which are essential items that must be met according to the requirements of the client when designing the vehicle. In order to manufacture such an economical, safe, and high-efficiency vehicle, the most basic and priority design technology to consider is weight management.
The Progress of Weight Management of Railway Vehicles
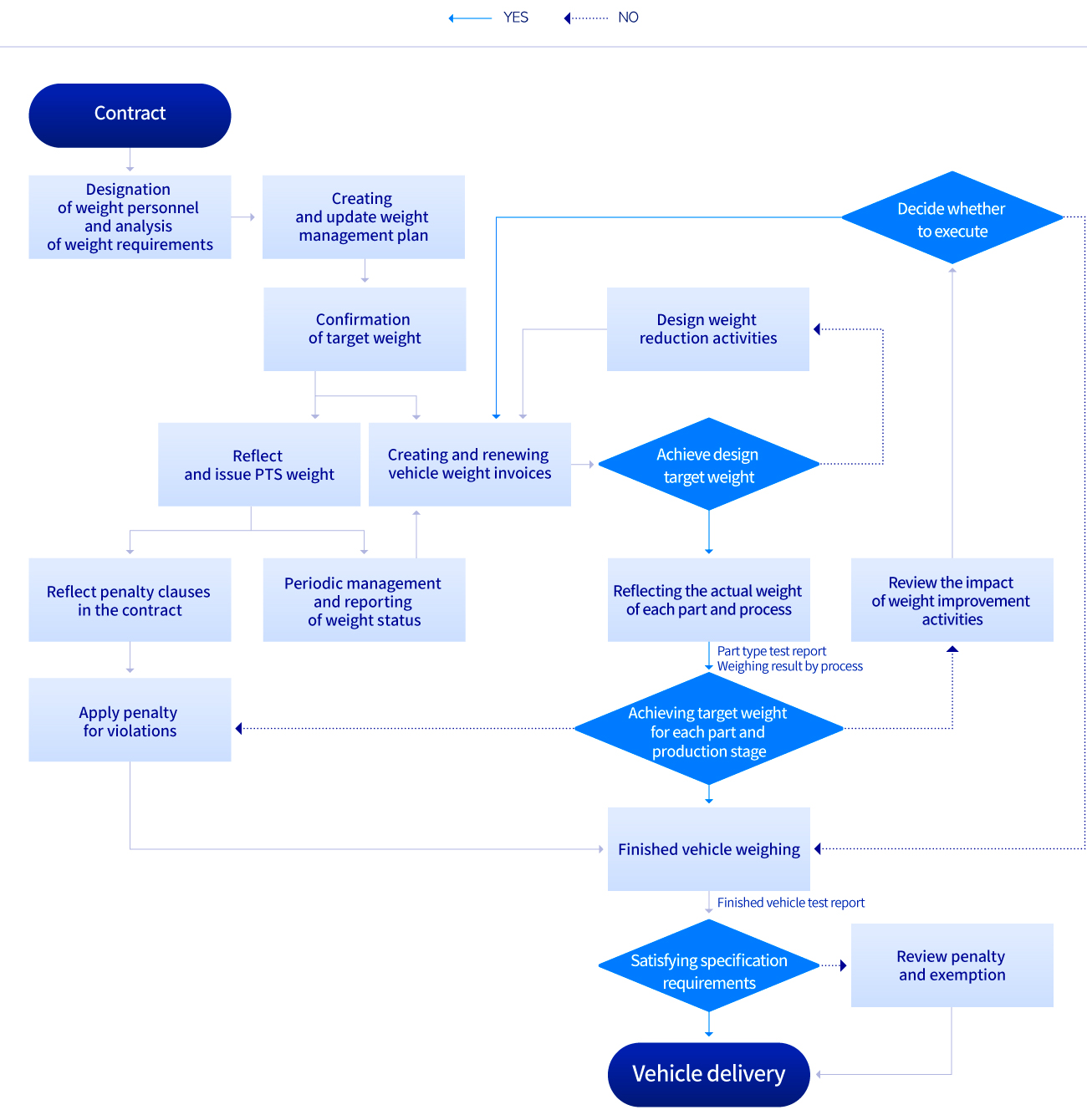
Weight management proceeds in each design stage, such as bidding/target weight, design (preliminary/detailed) weight, and actual measured weight. In the bidding and preliminary design stage, weight information of past similar projects suitable for the requirements is used. In this stage, reliable weight management is difficult because the design of all parts is not completed. However, in the detailed design stage, more accurate design weight information can be collected in units of parts so that the actual weight information of the parts can be confirmed. The collected part weight information is used to create the weight information of the finished vehicle, and the consistency of the measured weight information is confirmed throughout the manufacturing process. In other words, when the weight of the completed vehicle meets the requirements, the weight management is terminated after frequently checking the weight information and going through the weight reduction process for weight reduction and energy efficiency.
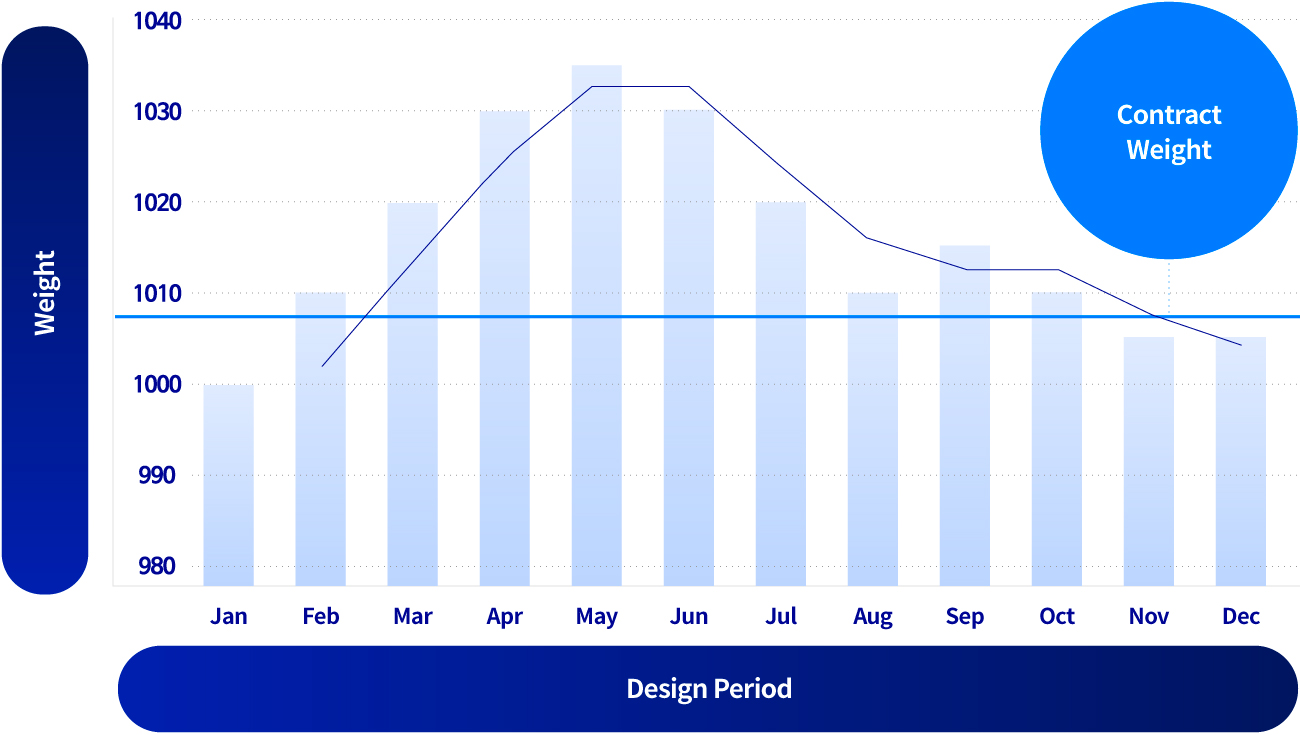
The start of reducing the weight of railway vehicles depends on whether the required weight is met. In general, the weight at the design stage shows a certain trend, and in most cases, weight reduction is determined by comparing the target weight with the design weight. The expected weight reviewed in the bidding stage tends to gradually increase as the design maturity increases, unlike in the initial design stage. Through this, the weight that needs to be reduced can be identified. Design change items for weight reduction are found through workshops, and priorities are selected in consideration of various risks for each design change item. Among them, the weight reduction method with the least risk and the greatest effect is adopted, and the weight reduction goal of railway vehicles is achieved through design changes.
Weight Reduction of Railway Vehicles
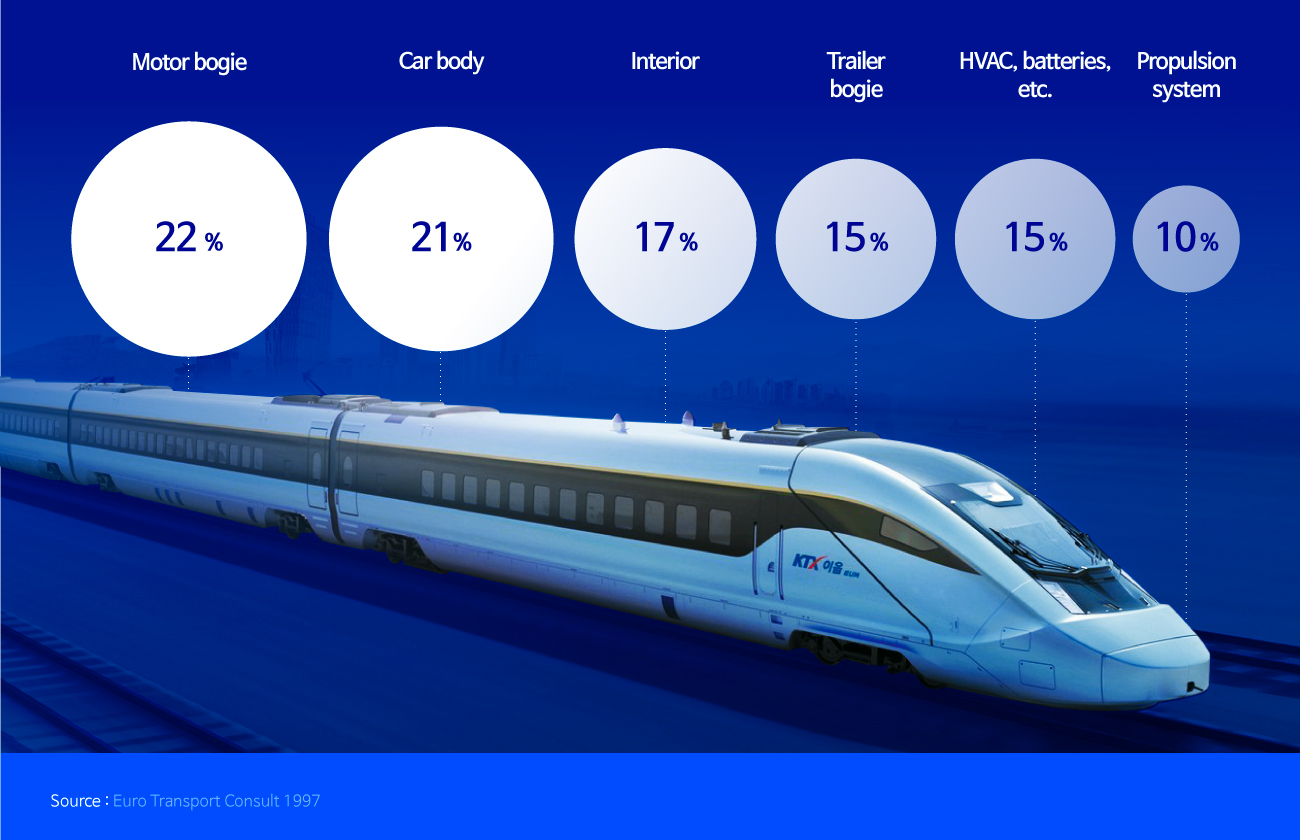
Reducing weight is the most important factor in weight management of railway vehicles. The weight proportion of trains is the largest with 22% of power systems such as motor bogies and motors, followed by 21% of car body and 17% of interior components and interior materials such as chairs. In addition, trailer bogie account for 15%, HVAC and other components such as batteries 15%, and propulsion systems account for about 10%. Therefore, weight management should also prioritize the car body and the bogie sector, and then examine the propulsion and energy systems that determine train performance.
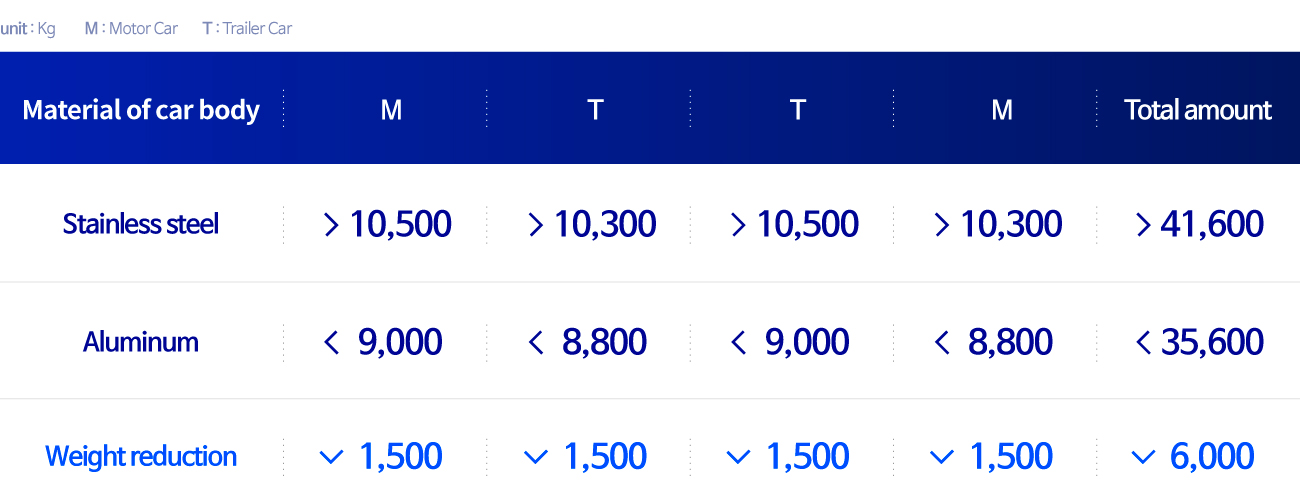
1. Weight Reduction by changing the Vehicle Body Material and Structure
The weight reduction of railway vehicles is also affected the most by the ca body material and structure, just like automobiles. Therefore, when designing a vehicle, it analyzes major performance changes of trains according to car body material and structure with a focus on crash safety requirements and examines them in detail. If the car body material is changed from stainless steel to aluminum, the weight reduction effect is great. A strong skeleton, an extruded profile of a double skin structure, is added to the main parts of the car body to reinforce parts that may be vulnerable due to material changes. As a result, not only the car body strength is improved, but also the secondary effect of noise reduction is obtained. In addition, through optimization of the design of the underframe and side frame, it is possible to reduce the weight while maintaining appropriate stress.
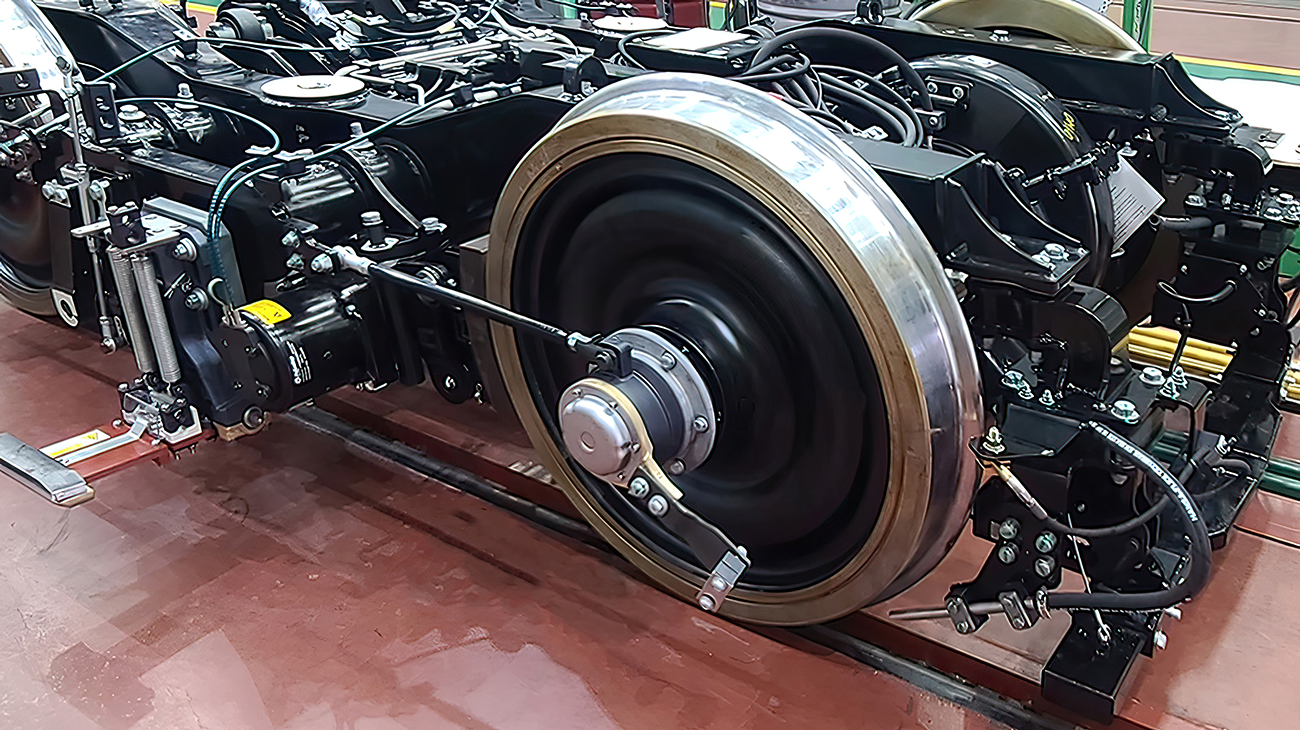
2. Weight Reduction of Bogie
The bogie, along with the car body, occupies a large proportion in the weight of railway vehicles. The weight of the bogie is high in the proportion between the wheel and axle (axle and wheel) and the bogie frame. Reducing the weight of the wheel and axle is a very important factor in reducing the weight of the entire vehicle as well as the bogie and has a great impact on ride comfort and driving safety. The weight reduction of the wheel and axle can be achieved by applying a hollow shaft to the axle, applying the wheel disk of the wheel, or changing the material or shape.
The suspension, which is a component of the bogie, can also be reduced in weight. Suspension of railway vehicles is generally composed of a primary coil or rubber spring and secondary air spring. If a rubber type is applied instead of the primary coil spring, it becomes lighter than when a coil is applied. In addition, if an aluminum alloy material is applied to the gearbox, which occupies a large volume in the bogie, the weight is reduced. It is also a way to simplify the design of the bogie frame by changing the structure of the bogie to an inboard type.
3. Weight Reduction of Electric Equipment
For heavy-duty electric equipment, the weight can be reduced by changing the box material to aluminum, and the auxiliary power supply can be made lighter through the resonant circuit. For reference, it is possible to reduce the weight by at least 5% to a maximum of 20% through modular design through diversification of cooling methods.
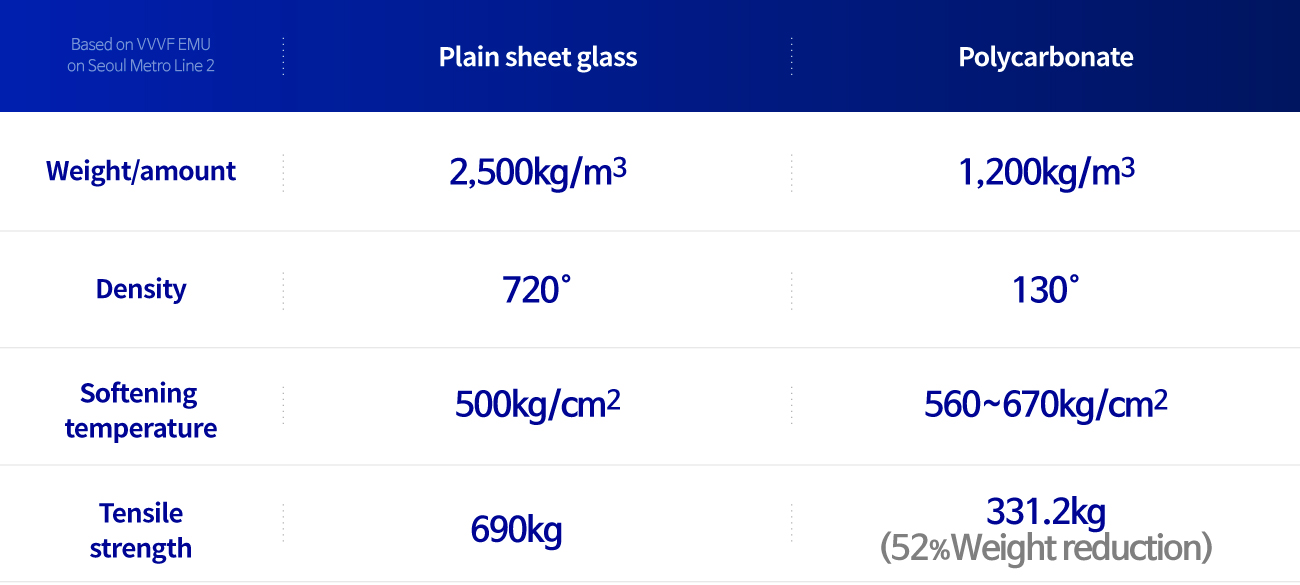
4. Weight Reduction of other components
Among the main components that make up a railway vehicle, other components except for car bodies, bogie, and electric equipment include indoor interior materials, floor materials, entrances, air pipes, and chairs. These components can achieve weight reduction mainly by changing the material (density). For example, the interior material is replaced with an aluminum phenol sandwich panel from polyester reinforced plastic to improve weight reduction and fire safety at the same time, or the window is changed from glass to polycarbonate to secure passenger safety when damaged.
Eco-friendly effect of railway vehicles weight reduction
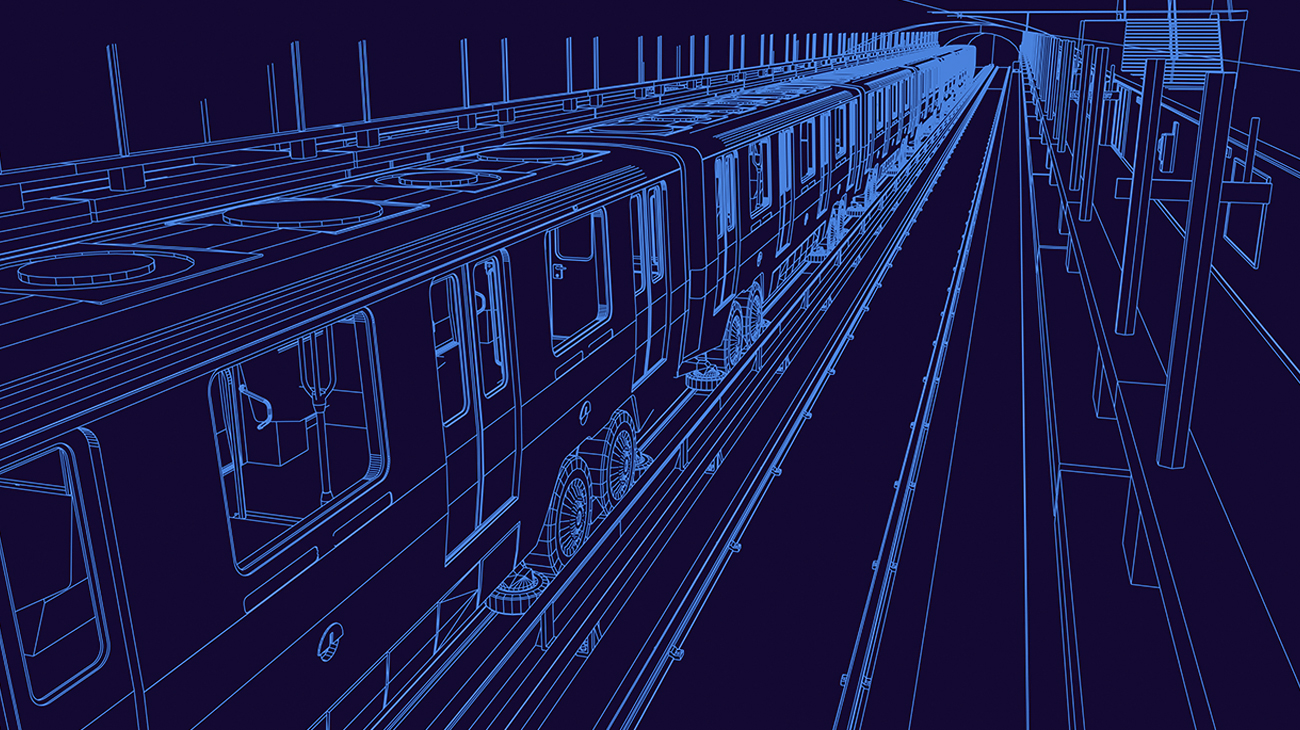
The weight information of railway vehicles calculated for weight reduction is also useful for managing carbon emissions and recycling/reuse rates throughout the operation from the manufacture of railway vehicles. For example, Hyundai Rotem analyzed the amount of carbon generated during train operation using information on the weight and material of all systems in the Taiwan Railways Administration (TRA) train project. Based on this, railway operators have established quantitative indicators to control greenhouse gas emissions generated while trains are driving and to purchase as many carbon credits as needed. Hyundai Rotem meets the requirement by analyzing and presenting the recycling/reuse rate required by the client according to ‘ISO 22628’ in the bi-level EMU project in Sydney, Australia.
Recently, according to the global trend, eco-friendliness is emerging as an important value, and the importance of weight management technology for weight reduction is increasing. The eco-friendly effect of lightweight trains is clear. Reducing the energy consumption rate by the weight reduction of railway vehicles means that it is possible to travel longer distances with less energy and reduces the amount of carbon emitted during energy production and use. As such, Hyundai Rotem is focusing on developing safer and more economical eco-friendly railway vehicles through the development of various lightweight technologies such as design optimization and new material development.