As the negative trend in climates continues because of global warming, the severity of natural disasters is increasing year after year. According to the Proceedings of the National Academy of Science, a 2℃ increase in the average global temperature endangers 20-30% of the creatures on earth. The primary cause of global warming is environmental contamination such as air pollution. To address the problem, the United National Framework Convention on Climate Change (UNFCCC) joined by 195 signatories agreed to keep the average temperature rise of land surface below 1.5℃.
Major countries in the Europe and America are restricting carbon dioxide (CO2) emissions under green car policies, aiming at carbon neutrality in 2050. Korea is also implementing regulations and policies to make a sustainable earth. Companies are trying to fulfill their social responsibilities and the railway industry is swinging by wind of green energy. The railway is an infrastructure that transports large numbers of people and cargos, so a green railway can be the key element to greening a country’s economy and social structure.
Recyclable and re-usable materials are essential, not optional
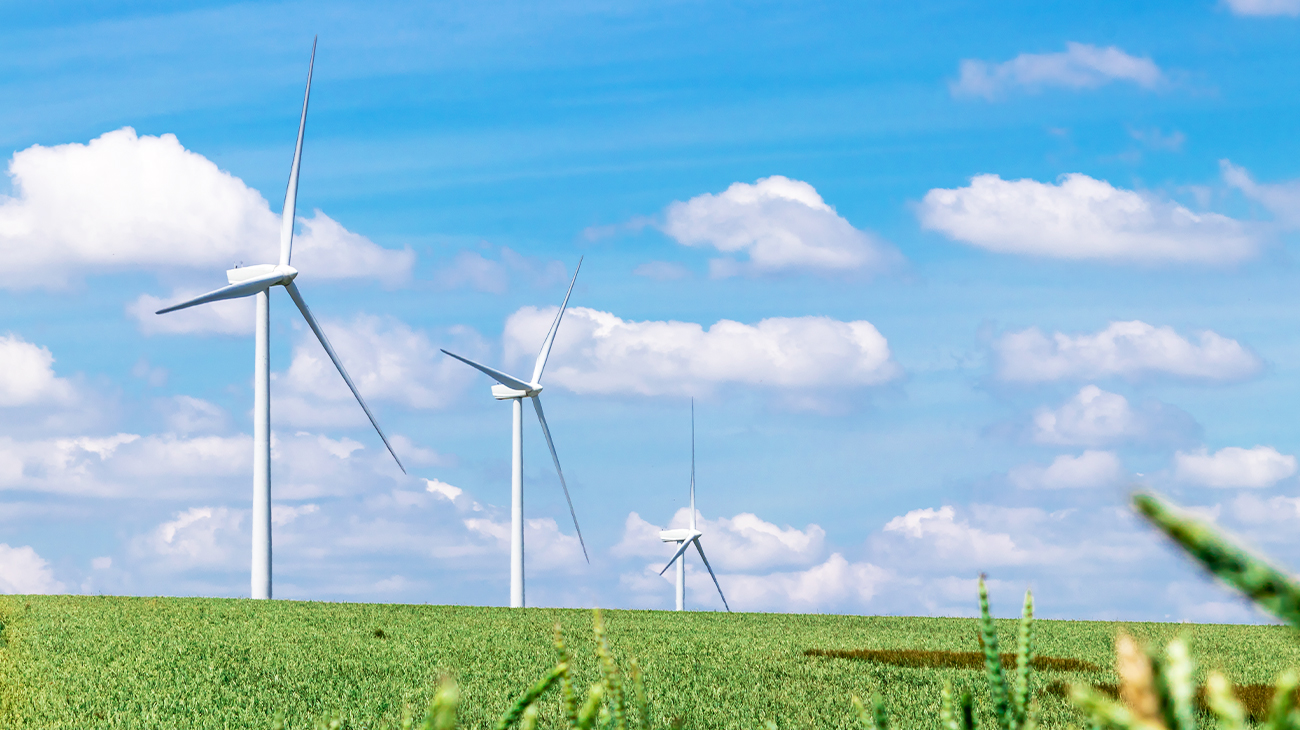
The causes of environmental contamination can be largely divided into industries and living activities. The former is mostly engineering industries that produce pollutants in the manufacture and transportation process, and the latter is activities in farms and households. Among them, carbon dioxide is the most emitted gas in the industrial manufacture process such as raw materials processing and factory operations. Another cause is the transportation industries that do not just produce enormous carbon dioxide emissions in the air, but also other pollutants in the disposal process. According to a survey of institutions in the UK, end-of-life trains that are poorly managed or treated produce waste as much as that from about 20 cars. Transportation can be the cause of environmental contamination even after disposal, not to mention during operations.
End-of-life trains were buried in the landfill in the past. However, this has an adverse effect in the environment and many countries, starting from Europe, are encouraging to re-use and recycle train waste to prevent pollution. Plus, recycling trains reduces materials purchase costs and production costs. In this regard, many railway makers in the world are trying to fulfill their social responsibilities and increase the operating efficiency of trains. Hyundai Rotem, Korea’s representative railway maker, is aggressively seeking the way to make parts of train components with recyclable materials to enable recycle and re-use at a certain rate.
The recycling and regeneration rate of trains set by international standards
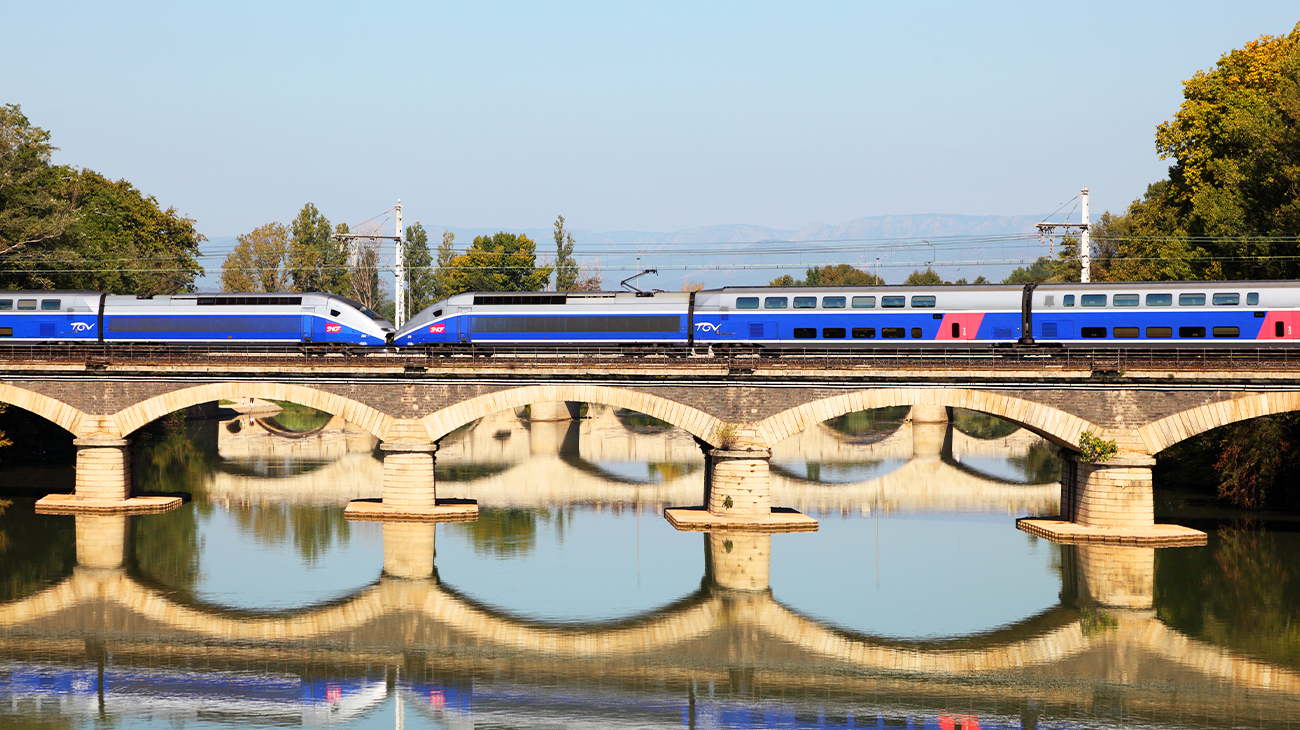
Discussions on recycling automobiles first began in Europe. In September 2000, Europe legislated the Basic Guidance on Scrapped Car Recycling Monitoring and Re-use Rate and mandated to recycle scrapped cars by over 95% and re-use materials over 85% since 2015. It aims to reduce shredded car residue and transform them into resources by separately collecting and recycling plastic, glass and rubber parts that are buried or burnt as waste. In addition, it restricts the use of a specific materials and heavy metals from the design phase of manufacturing a new car to avoid any harmful substances in shredded car residue.
The disposal and recycling process of end-of-life cars consists of liquid waste collection, compression and cutting process. The International Organization for Standardization (ISO) established the ISO 22628 Recyclability pertaining to the calculation method of car recycling and regeneration rate in 2002. It classifies the process as follows and calculates the rate qualitatively by surveying and analyzing the materials of all components such as weight and density.
• Pre-treatment → Dismantling → Metal separation → Non-metallic residue treatment
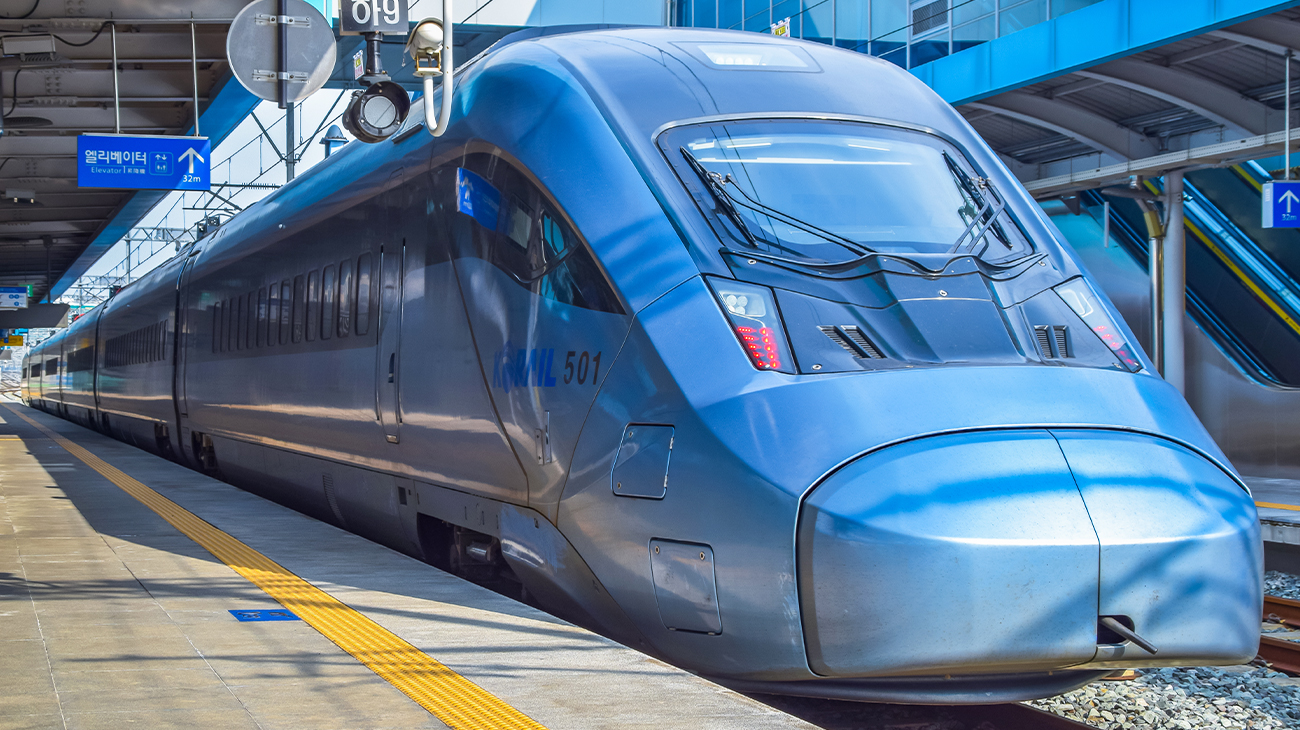
Trains are made with far more different materials and components than cars. Thus, eco-friendly disposal is more important in trains, but they were disposed of as is, without specific treatment. In 2013, the Union des Industries Ferroviaires Européennes (UNIFE) suggested the guidelines on the Train Recycling and Regeneration Rate Calculation Method for the following process based on ISO 22628.
• Pre-treatment → Dismantling → Shredding → Post-shredding
When calculating the recycling and regeneration rate of trains, material recovery factor (MRF) and energy recovery factor (ERF) are applied, unlike in cars.
Materials of trains under environmental regulations from metal to synthetic rubber
Main materials of train and application rate
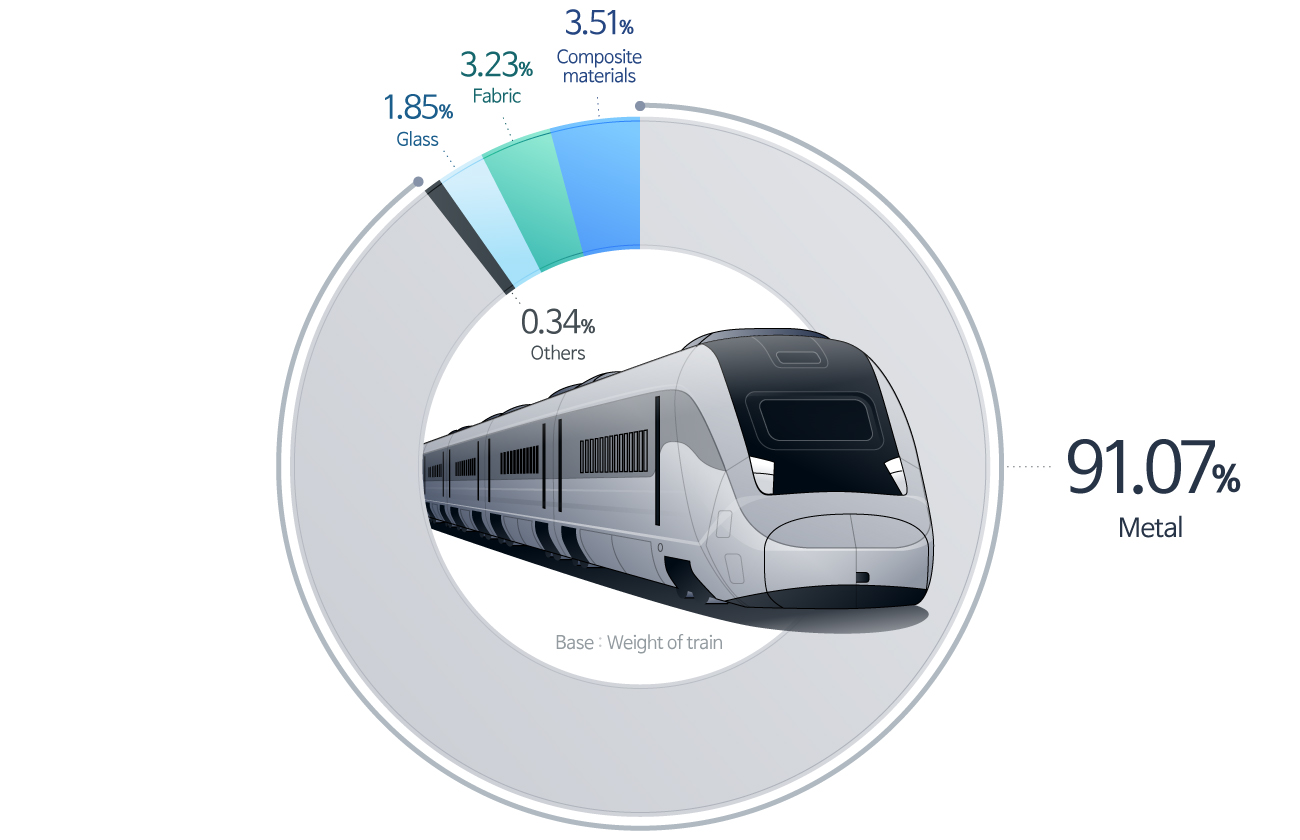
Various materials are used to make a train such as metals, composite materials, rubber and glass. The proportion of each material is different by the type of trains, but when the weight is considered, metal makes up the most. Metal accounts for 60% of the bodies and bogies and including other components, over 90%. Mild steel, stainless steel and aluminum are mostly used for the metal materials. Due to the nature of trains, the metal materials are required to meet the strength requirements to endure shocks, pass environmental impact assessment and have a certain level of recyclability.
Example of materials analysis by components of Passenger Train
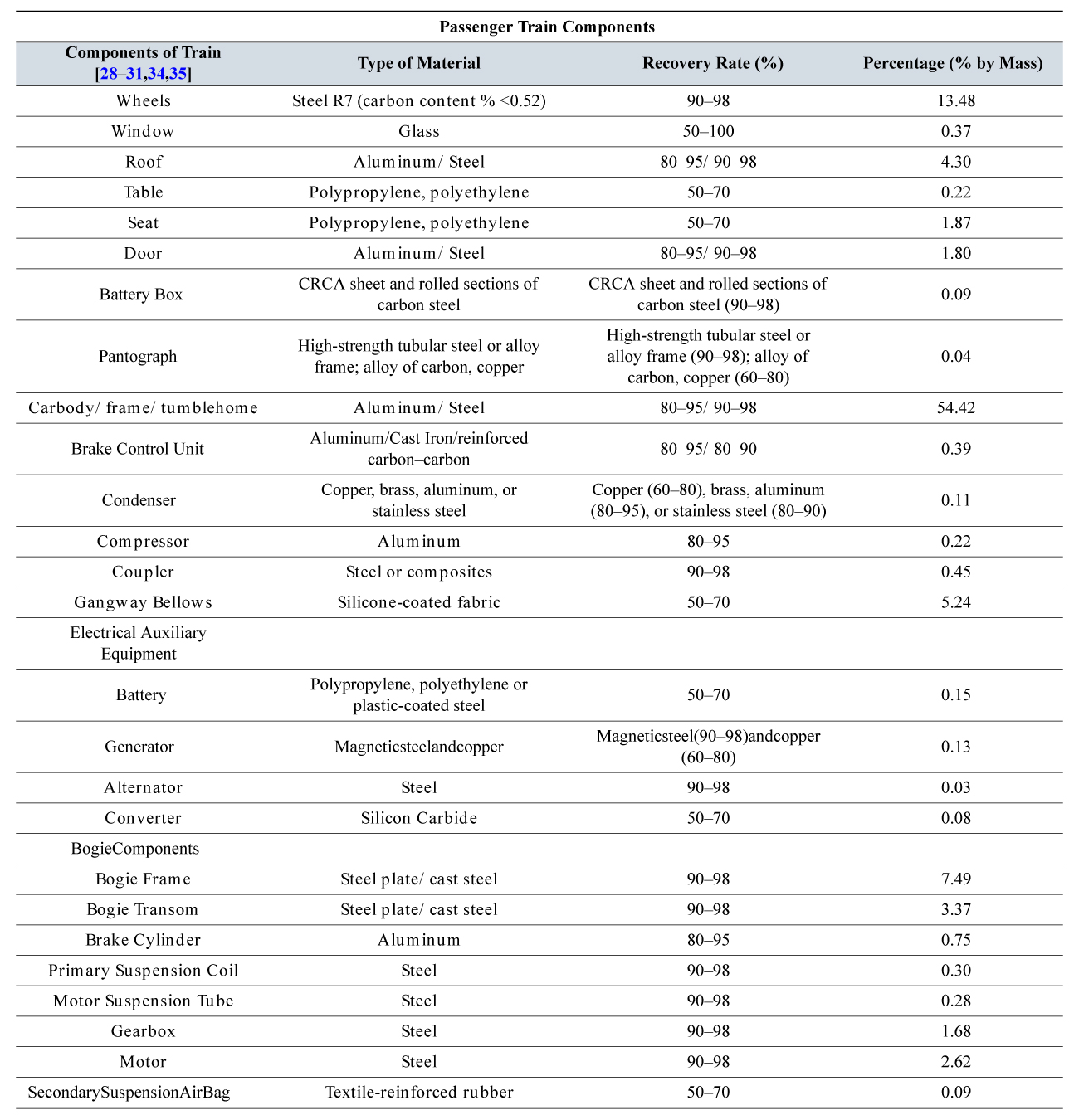
In 2019, the European Union (EU) extended the application of ISO 22628 Recyclability, which lays out the recycling and regeneration rate calculation method for cars, to trains (ISO 21106) and is promoting to increase the proportion of recyclable and re-usable materials in trains. For example, Alstom in France calculated the recycling rate, which is one of the main indices for environmental product declaration (EPD) of its specific project train to be around 97% by applying ISO 22628.
Hyundai Rotem manages the materials of trains from the design phase
Recyclability analysis of train based on ISO 22628
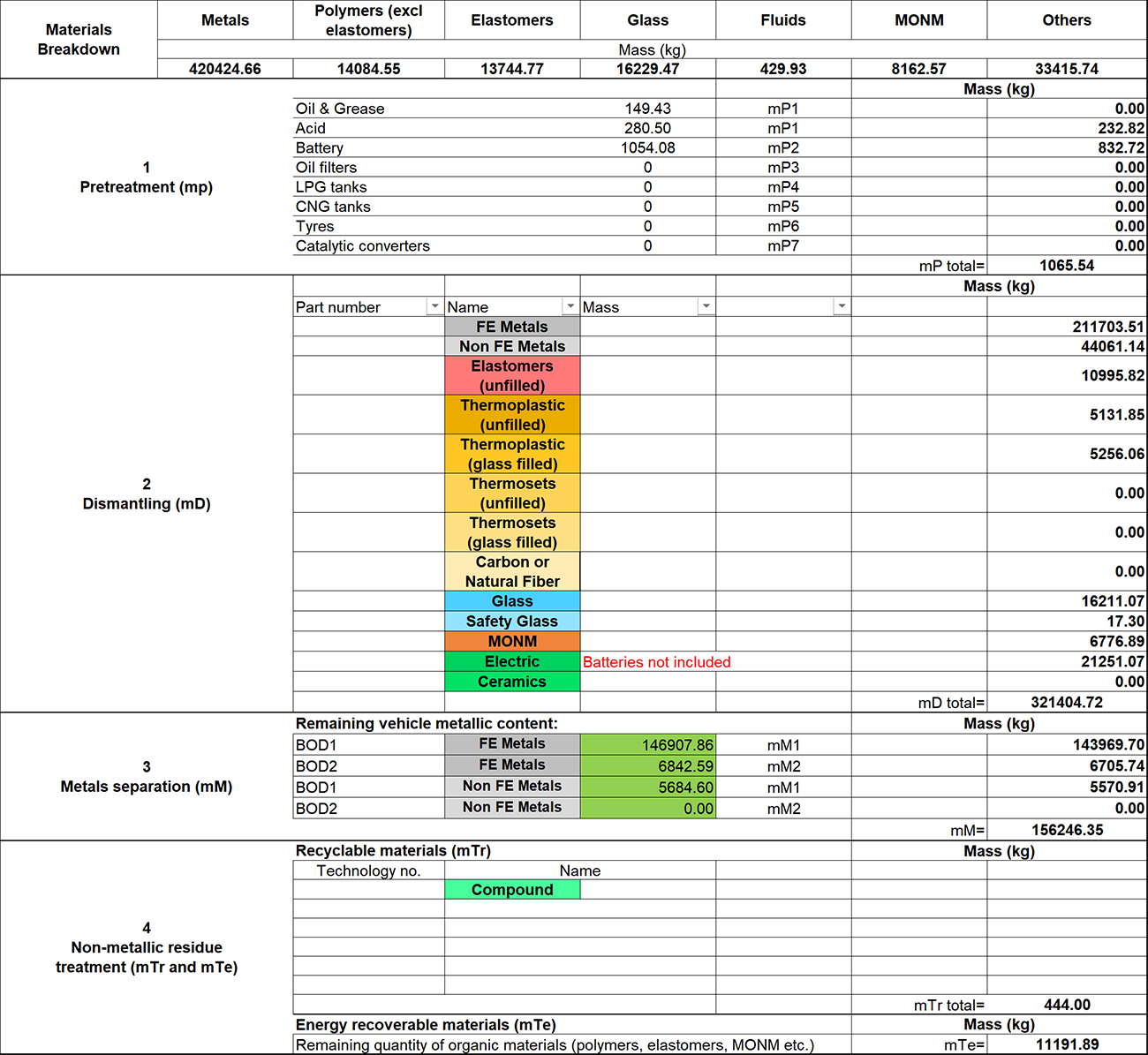
In a recent overseas electric vehicle project, Hyundai Rotem conducted life cycle assessment (LCA) and environmental product declaration (EPD) according to the customer request. All information in 27 sections of the product breakdown structure (PBS) on the materials and mass of components of trains were utilized. For component transportation-related requirements, the distance of transportation (km) was calculated considering various use of transportation such as vessels and trucks. Materials data used in the manufacture process were used and for waste disposal performance, the disposal history data of Changwon Factory were used. The list of materials used for about 35 years and mass were classified according to the PBS classification system, and maintenance periods were applied. Based on the analysis of recyclable materials and components by the type of train and by applying ISO 22628, Hyundai Rotem calculated the recycling and regeneration rate to be about 97%, which surpasses the 95% required by the customer.
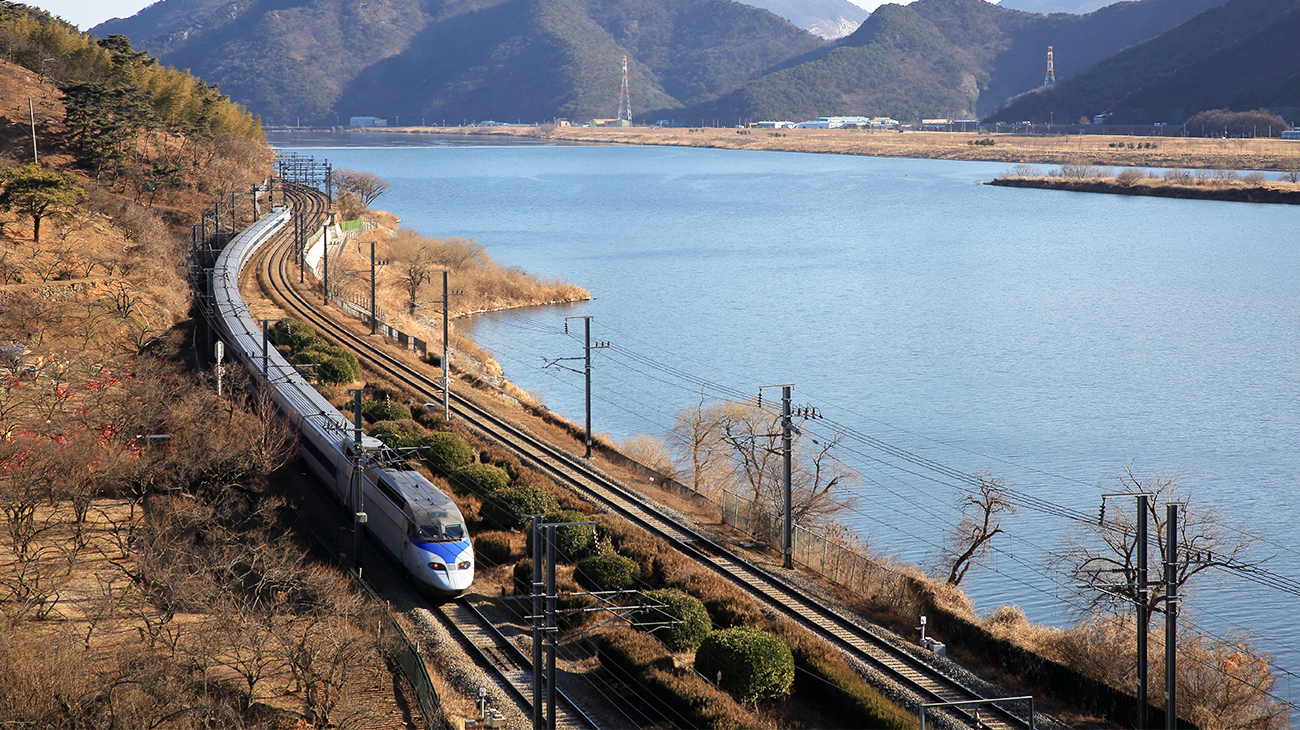
As above, Hyundai Rotem is manufacturing an eco-friendly train and managing the recycling and re-use rate to achieve carbon neutrality. It investigates carbon emissions during the raw materials manufacturing process of each component using all materials data of components needed to make trains such as weight and density and analyzes the recycling and re-use rate based on it. It is forging a virtuous cycle to green trains and make a sustainable railway ecosystem through pre-emptive and all-encompassing approaches as above.