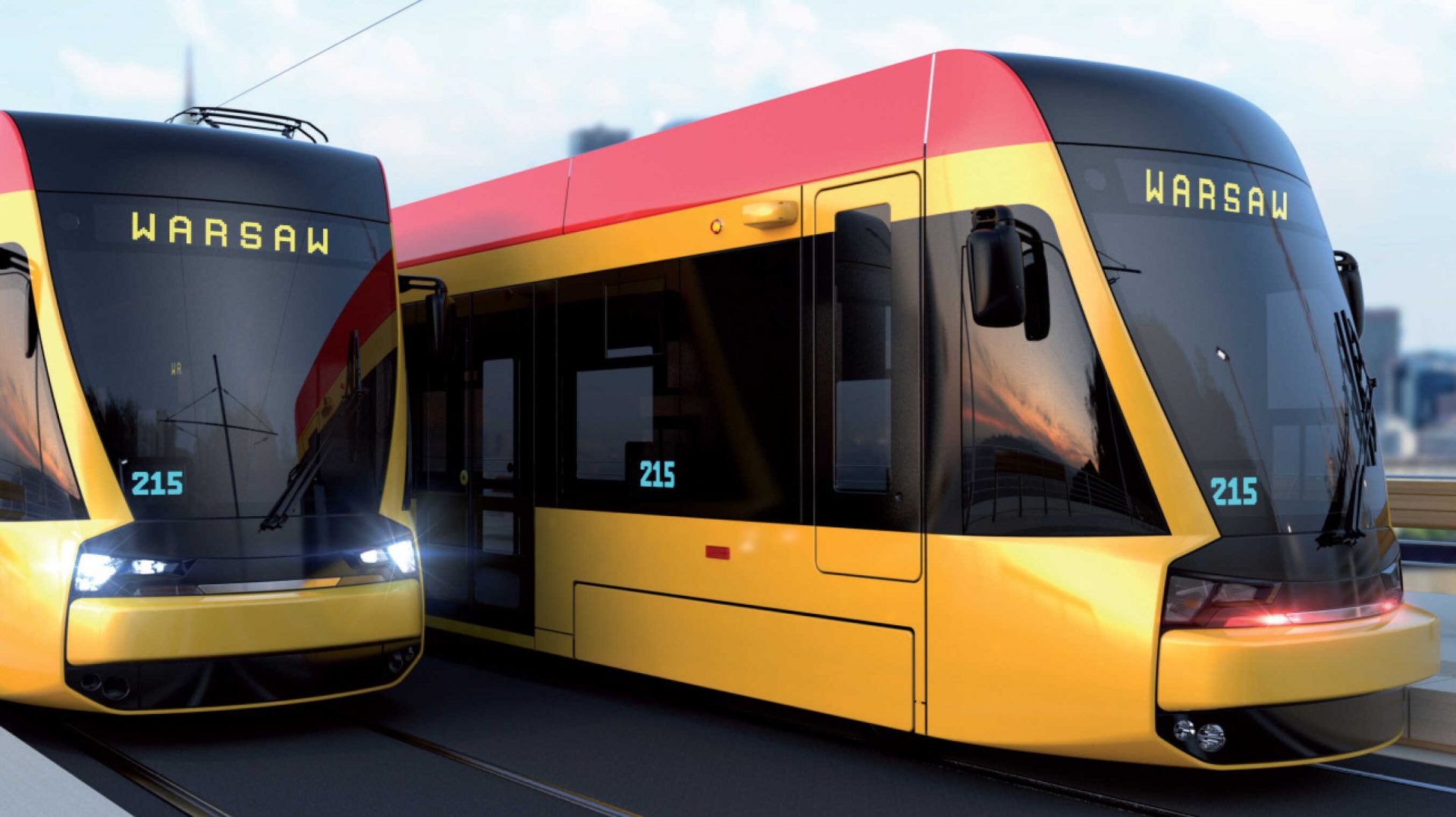
In our previous discussions, we introduced Hyundai Rotem’s crash safety design technology and crash energy management (CEM), (https://tech.hyundai-rotem.com/en/new-normal/crash-and-safety-design-standards-for-railway-vehicles-and-hyundai-rotems-crash-energy-management/) which aim to minimize the risk to passengers in the event of a crash.
This time, we will explore Hyundai Rotem’s railway vehicle shock absorber development, designed to more effectively absorb crash energy, among those safety design technologies for minimizing passenger risk.
What is a shock-absorbing member?
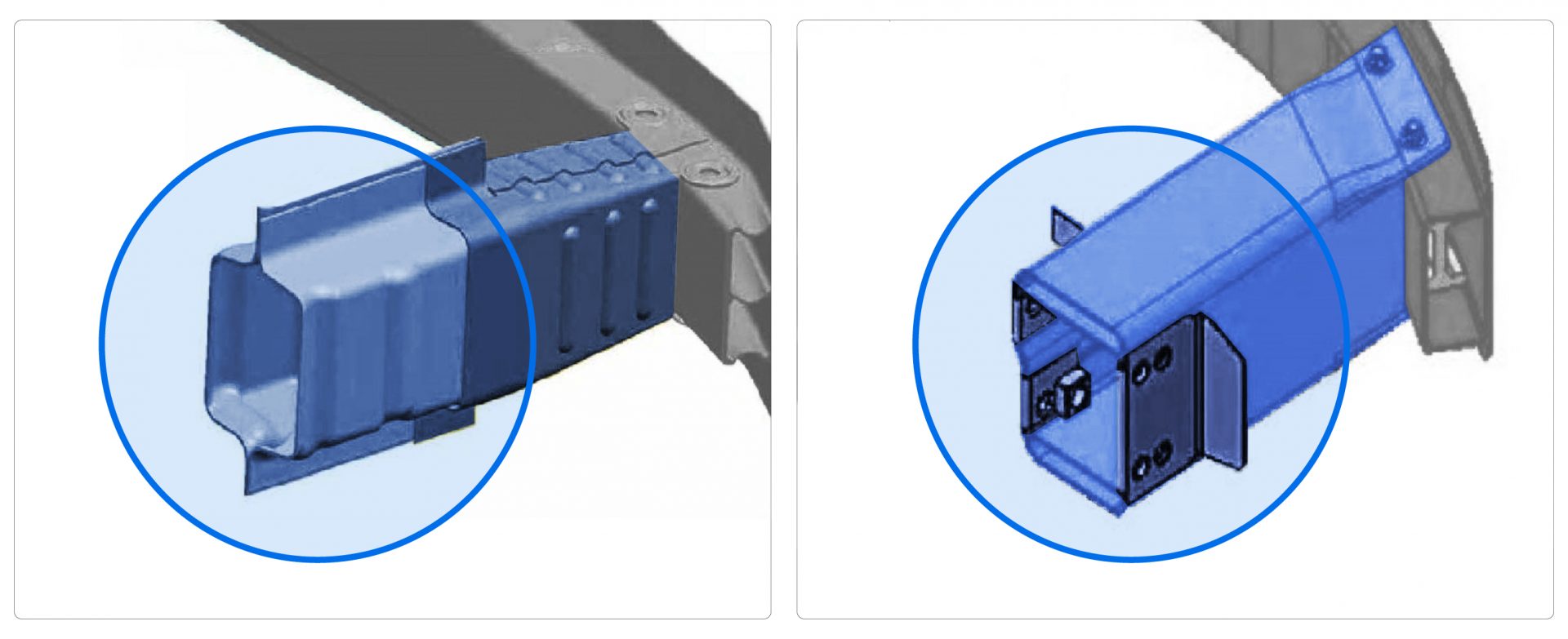
Railway vehicles are equipped with various shock -absorbers to absorb crash energy and manage crash load in collisions, including shock-absorbing members, expansion tubes, elastic rubber absorbers, hydraulic buffers. Shock absorbers vary in design depending on their installation location and purpose. The CEM system collectively refers to crash energy absorption systems that effectively activate energy absorbers installed across a car to prevent crash energy from concentrating at specific points.
Among them, shock-absorbing members are installed in the front part of a car, playing an important role in activating the CEM’s absorption mechanism. They are typically designed with a crush mechanism and bolted to the front part of a car to facilitate easy detachment. They are usually made of easy-to-process welded steel structures. Improper design can lead to irregular deformation under the load generated during the crush process, resulting in an incomplete absorption of crash energy. Therefore, separate dent and bending processes are applied to ensure that the intended deformation occurs under load.
An aluminum shock-absorbing member that addresses the shortcomings of existing shock-absorbing members
Existing steel shock-absorbing members offer high processibility for diverse manufacturing needs, but have limitations in design flexibility due to high quality assurance costs and large crash load, hindering their application in lighter vehicles such as trams and light rails.
Recognizing the need for a new railway vehicle shock absorber to address these problems, Hyundai Rotem initiated the development of a new shock-absorbing member capable of absorbing an average load of 200kN (for 5-module trams) and 300kN (for 7-module trams).
The compressive strength of the vehicle body varies by type of railway vehicle, with the lowest requirement being 200kN for trams and the highest requirement being 2,000kN for locomotives. Railway vehicle shock-absorbing members are generally designed to have a lower crush force than the compressive strength of vehicle body, so that the shock absorber is activated in a crash, absorbing crash energy, and controlling crash energy and crash load. Therefore, to increase usability, Hyundai Rotem aimed at the average crush force of the lowest strength requirement for railway vehicles, 200KN and 300KN, in developing the new shock absorber.

As a result, a new aluminum railway vehicle shock-absorbing member has been developed using the unit aluminum extrusion manufacturing method, which enables length adjustments to meet specific absorption capacities of different vehicle types, and further allows for both standalone or combined installation options, enhancing effectiveness. The unit is set to be applied to commercial tram models soon.
Hyundai Rotem expects that this shock-absorbing member development will facilitate uniform and efficient absorption of crash energy from crush loads and also reduce vehicle weight, leading to enhanced productivity and improved economic efficiency in railway vehicle manufacturing.
Aluminum material for optimum shock-absorbing performance

The material was also carefully selected to optimize absorption effect. To use extrusion molding, which ensures stable performance and facilitates mass production, the choice for the body material was between aluminum and aluminum alloy steel. Aluminum is weaker than steel, but it is lightweight and can be extruded, so it is good for reducing manufacturing processes and ensuring quality control.
Over-riding prevention devices are added to the front of the shock-absorbing member installed at the front of railway vehicles, significantly reducing the risk of over-riding. Therefore, ensuring the member’s stable crush action is a critical design element. A defect in the crush-type absorbing member that experiences large scale deformation can fail the intended deformation, significantly reducing the absorption performance. Additionally, irregular crush action may disrupt the overriding phenomenon in vehicles.
Aluminum is an excellent choice for manufacturing absorbers using the extrusion process. It reduces the need of manual labor that can lead to manufacturing deviations, such as material processing and welding, and offers greater design flexibility for shaping the cross-section through the mold. It further offers an advantage of excellent corrosion resistance, which enables it to maintain its appearance stably for about 30 years, the typical lifetime of railway vehicles, since the absorbing member is externally fitted to protrude from the vehicle exterior.
Mechanism and effect of the new aluminum shock-absorbing member
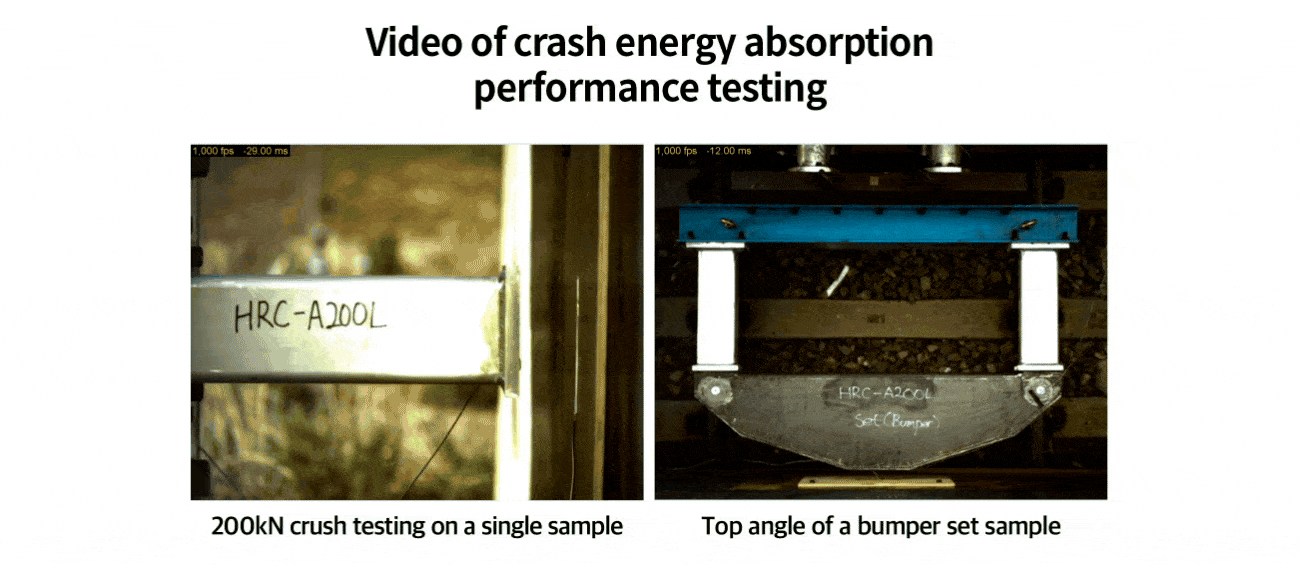
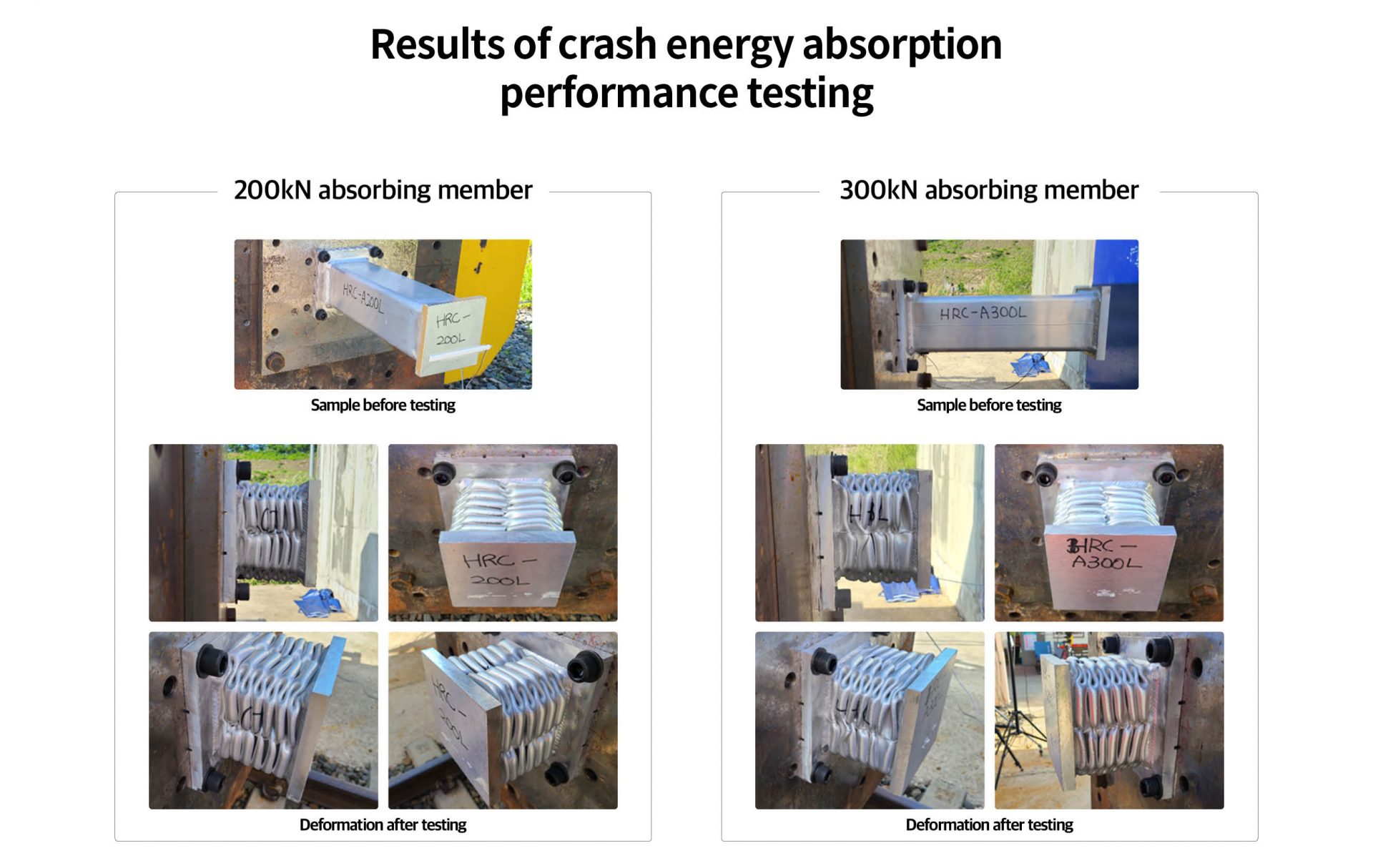
The collision testing of the shock-absorbing members designed for 200kN and 300kN revealed even bending in the crush zone at crush and a more stable crush load than the existing shock-absorbing members, which translates into a high absorption capacity.
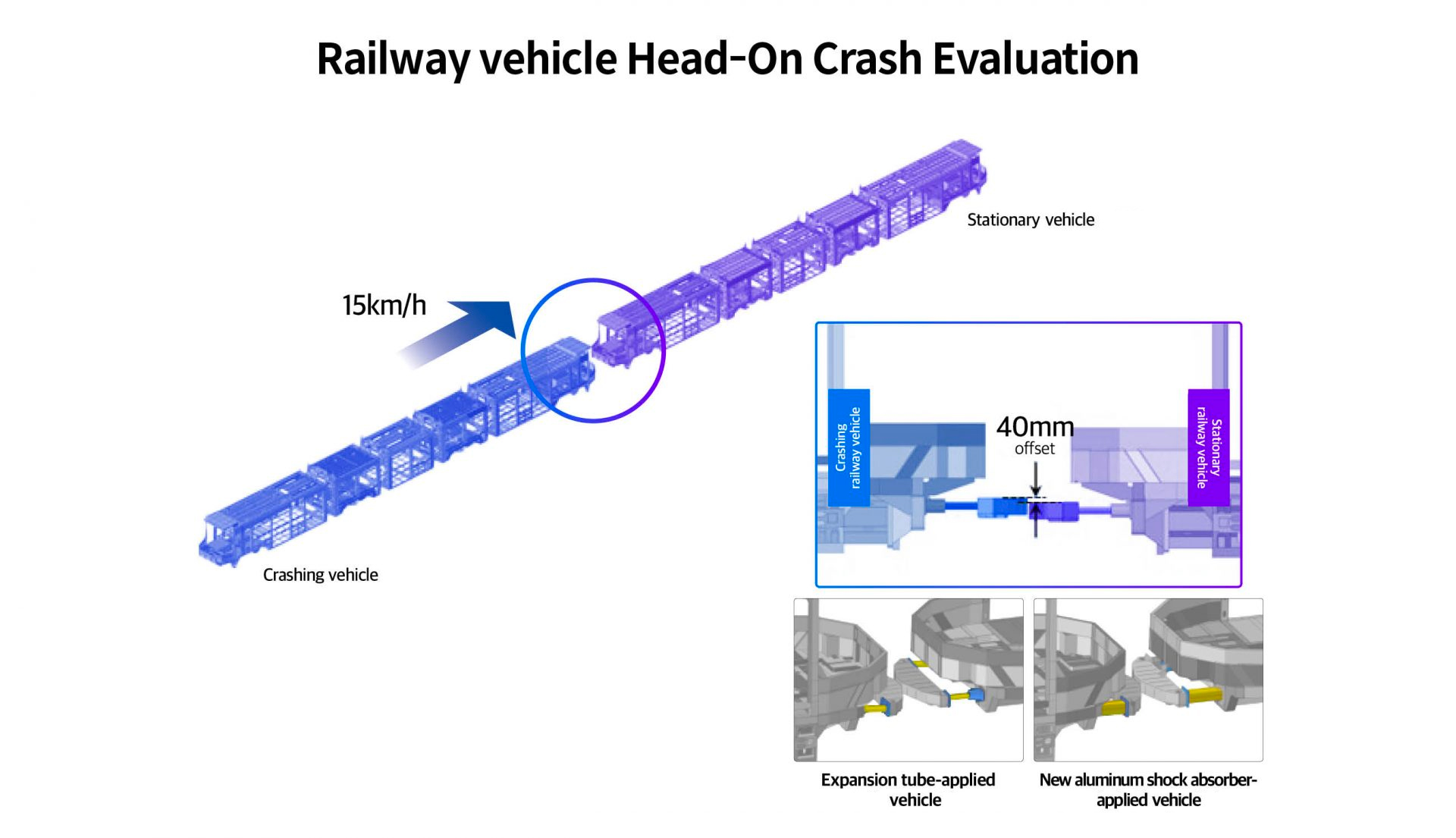
Moreover, a safety test was conducted under the same crash conditions after replacing the expansion tube used in existing trams with the new shock-absorbing member. The result showed the superiority of the new shock-absorbing member. While the expansion tube-type absorber, which requires a larger installation space, caused permanent deformation in a small area of the bumper at collision, the new shock-absorbing member, which allowed the installation of a high capacity absorber within the same space, caused permanent deformation in the crashed bumper beam area only, sparing the vehicle structure. This demonstrates its superior crash safety performance.
Through its multi-layered and meticulous research and development, focused on safer railway vehicle production, Hyundai Rotem has developed a new aluminum shock-absorbing member that not only enhances crash safety but also guarantees exceptional quality. The new shock-absorbing member’s significance lies in its application of both a new structure and a new material, aluminum. Hyundai Rotem plans to expand and further the research on crash energy absorbers from trams to engine locomotives.
Hyundai Rotem plans to continue on research and development for optimized crash safety designs to minimize damages in collisions, ensure the organic collaboration between safety devices within the vehicle crash safety system and provide safer railway vehicles.