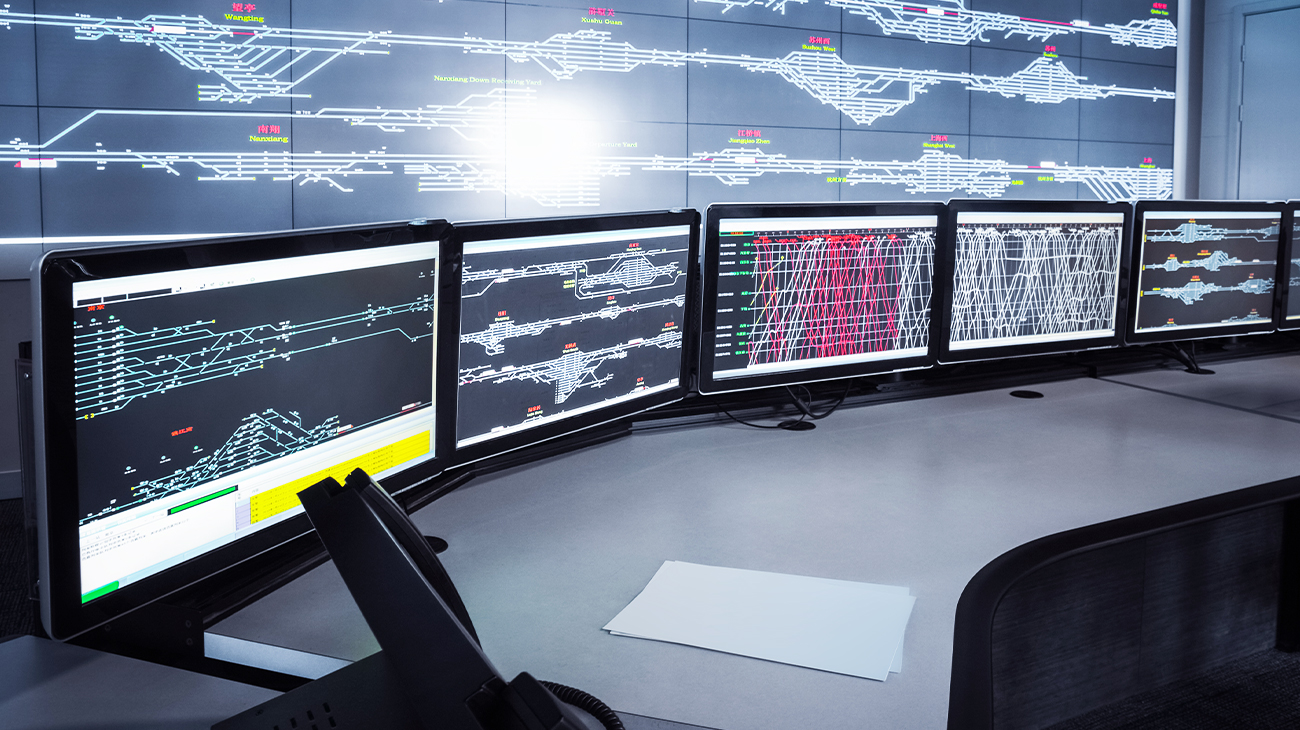
The train signaling system acts like a brain if a train is a human body. It determines when the train departs and stops and guarantees the safe operations of the train. The train signaling system is essential for safe operations and operating efficiency. The train signaling system controls the optimum operating schedule while maintaining a safe distance between the preceding and following trains on designated tracks.
Meaning of headway in train signaling system
The train signaling system to secure safe travel distance between trains begins with measuring the availability and shipments through ‘headway.’ The headway is also known as the time interval or dispatch interval between trains. The optimum result of all railway vehicle systems is the stable maintenance of the headway. In other words, it is necessary to establish a system for the headway to be maintained securely, which makes it possible to retain the track utilization rate at an appropriate level even when the braking system performance declines. (24-hour usage rate, including the train utilization rate for service operations and maintenance).
What is the minimum headway?
Calculating train intervals refer to dynamics, such as a regular train operating speed and an average inclination of standard acceleration and deceleration between stations. The headway is the interoperation intervals between the preceding and following trains on the track regarding these variables. The minimum value is the minimum headway.
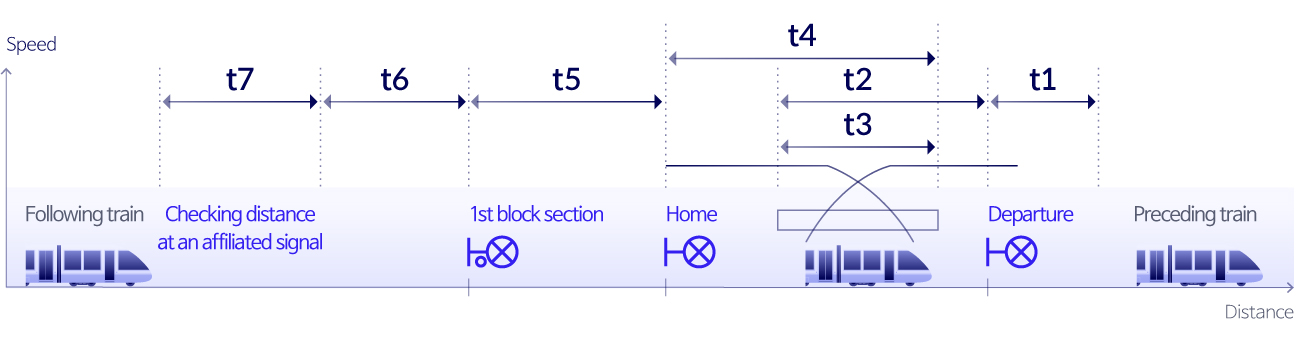
For efficient track operations, trains must run as many as possible and the departure interval must drop as small as possible. The minimum headway between the preceding and following trains depends on the operating interval. The maximum number of operating trains must consider the signal interval, signal display system, number of arrivals and departures, vehicle performance and stopping time.
For example, in a single-track railway where trains travel in both directions on the same track, the minimum operating interval is the survey diagram of the minimum headway affected by the time curve. It contemplates the time at which the preceding train passes the departure signal. The following formula can express the minimum operating interval.
The minimum operation headway(TR)=t1+t2+t3+t4+t5+t6+t7
t1: time when the affiliated signal changes
t2: the time when the rear of the departing train enters inside of the departure signal after departure
t3: stopping time
t4: the time when the front of the train enters inside the home signal until it stops
t5: the time when the train travels between the 1st block signal in the rear and the home signal
t6: the time when the train travels the distance at the planned speed, decelerating to the affiliated signal by the first blockage signal (the caution signal is 45 km/h for this case.)
t7: the time between when the driver recognizes the affiliated signal and puts on the brakes (approximately 3 seconds)
The minimum operating headway is calculated by exploring all points and situations where the speed of the preceding and following trains is detected. The maximum estimated value is the minimum headway of the route (all points and conditions include the distance between stations, stations, operations, etc.).
Required minimum headway examination, Guaranteed Emergency Brake Rate (GEBR)
In train operations, the headway follows the performance requirements of the train signaling system, which usually demands the minimum operating interval for train availability. The railway vehicle deceleration is crucial to meet the requirements and can be calculated with the braking distance. When studying the braking distance, service braking with regenerative braking and emergency braking with fast response speed through pure air braking should be considered. GEBR, one of the emergency braking distance performance standards regarding the safety margin, must be reviewed.
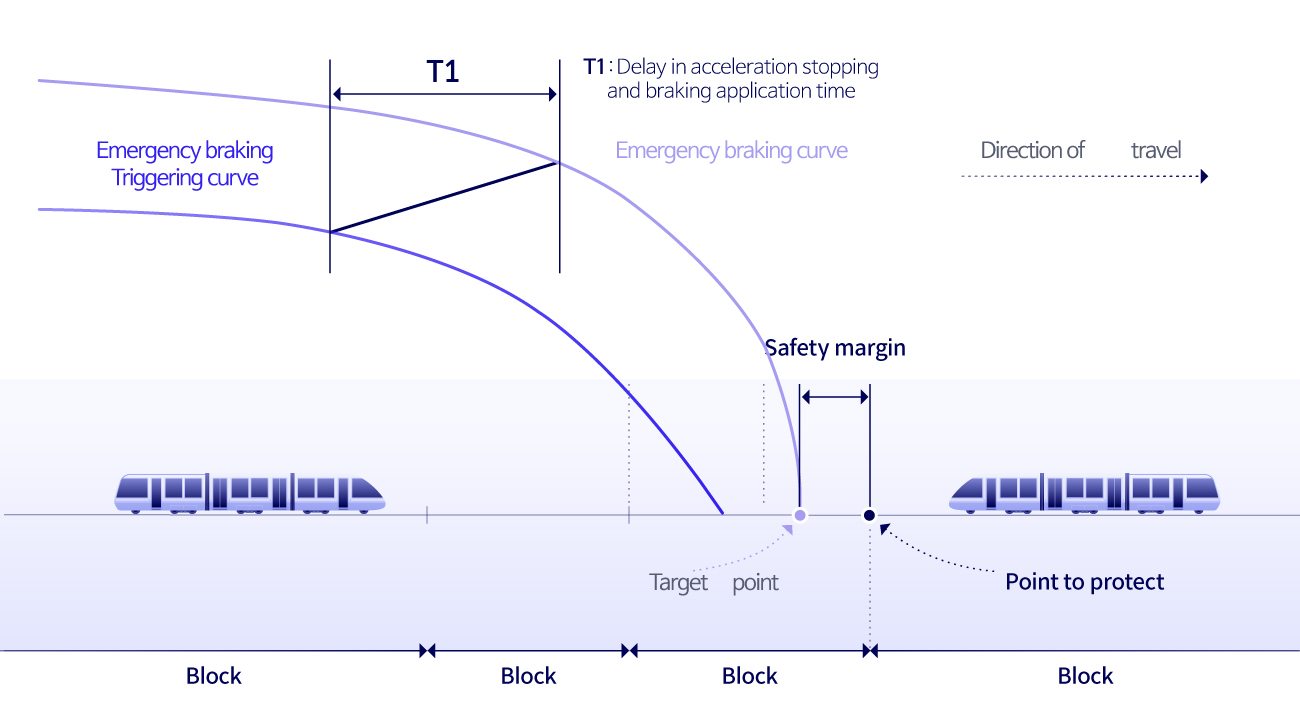
GEBR is the guaranteed emergency braking rate, which ensures the emergency braking deceleration value even in a braking system failure. The brake system failure applied to the GEBR value measurement means a reasonable level of oversight and does not include the overall braking system failure. The criteria for calculating the emergency braking rate generally refer to the requirements, such as one brake failure, maximum load, flat ground and dry track. In addition, wheel and rail conditions affecting braking performance can be considered.
The required GEBR value is usually advised by the signaling system requirements or decided by the train operator. There is no must-requested value for GEBR. Different values can be produced regarding train types, loads and railway track conditions. Two factors are vital for GEBR determination. The first one is a brake system failure scenario and the other one is the expected minimum adhesion coefficient value.
Correlation between Coefficient of adhesion and brake force

If the brake power is higher than the adhesive force (cohesion coefficient × vehicle weight), a slip effect occurs, which reduces the vehicle speed. A sliding phenomenon occurs even in the opposite case, lowering the train speed. These phenomena may affect the braking distance and challenge it to comply with the minimum headway. For the adhesion coefficient value affecting adhesion, refer to the general adhesion coefficient table presented in ‘Railroad Engineering (2006, Author Sabeom Seo)’ below. The value differs depending on the weather and operating conditions. Notably, the deviation becomes severe with regard to management conditions created by the operator who manages the track conditions. For GEBR improvement, it is necessary to establish a system that can resolve an emergency with a more reliable braking system during emergency braking in consideration of the railway characteristics, using adhesive braking between wheels and rail. Maintaining the adhesion coefficient of the wheels and rails under the worst condition at an appropriate level is mandatory for track management.
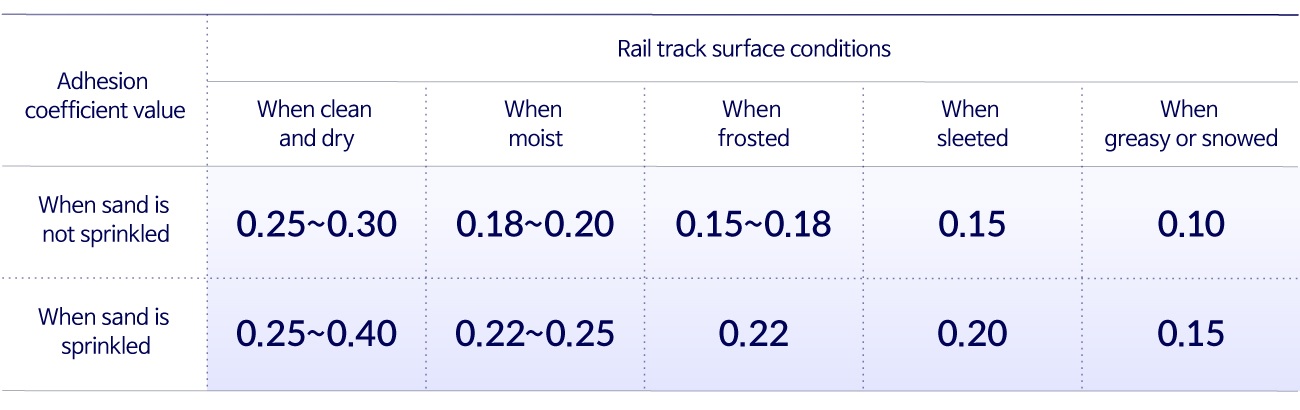
Braking system and train signaling system
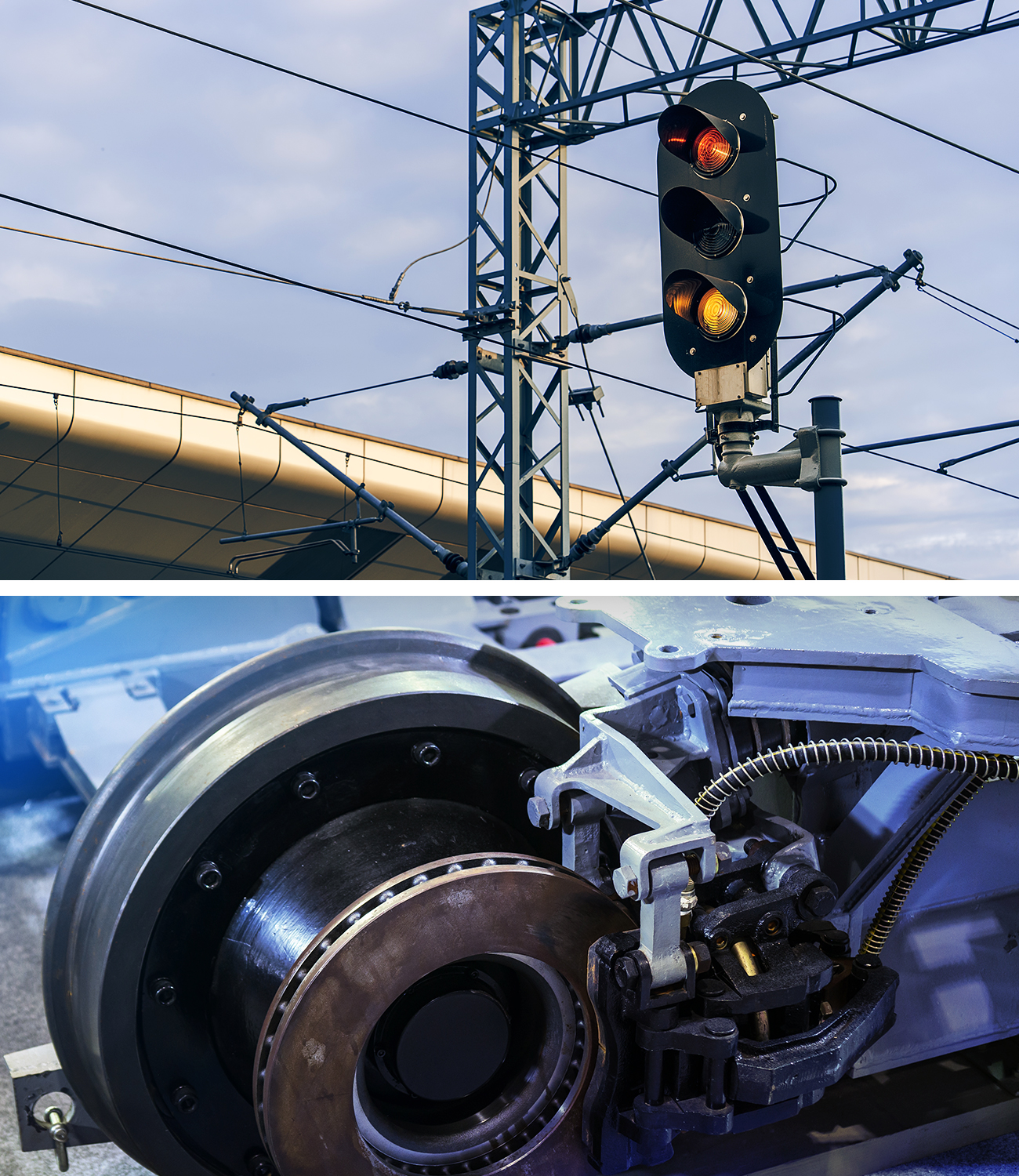
The safety distance between trains includes a safety margin considering the uncertainty of the braking distance. The safety margin is an essential safety device to prevent train collisions but is also a factor in reducing operating efficiency by observing the minimum headway. In other words, when the braking distance is uncertain, the safety margin must be extended, leading to an unnecessary increase in the headway. Increasing the reliability of the train’s emergency braking power decreases the safety margin, which affects the operating interval calculations. The braking system performance helps to build an efficient train signaling system.
Hyundai Rotem continues its efforts for effective train operations by standardizing Korean train signaling systems with Korean-style system construction, such as KTCS-2 and KTCS-M and constantly investing in research and development for the design and application of the advanced braking system. Hyundai Rotem has been building a safer signaling system and braking system by satisfying Safety Integrity Level (SIL) requirements. The company has been developing ‘Zero Speed Regenerative Braking’ technology and more, such as eliminating the dead time of regenerative braking occurrence at the beginning of braking in both high and low-speed and minimizing air braking. Hyundai Rotem plans to create a safe and efficient train operating environment through developing innovative technology for train signaling systems and serial interfaces with braking systems in various train operating environments.