All transport operations face challenges in efficient and economic maintenance. In particular, rail cars carrying numerous passengers and cargo require extra attention and precaution for safety as prior inspection and post analysis are directly linked to the safety of passengers. Recently, smart maintenance technologies in the 4th industrial revolution such as internet of things (IoT), wireless network, big data and cloud are widely introduced in the railway industry because the maintenance methods are being evolved in line with the advances in technology, as well as operating methods.
In addition to that, endless demands of train operators and maintenance mechanics have led the development in smart maintenance systems. As a result, the maintenance pattern has been gradually shifted from post analysis in the past to prior (preventive) maintenance and predictive maintenance in an attempt to reduce costs and risks. Hyundai Rotem began to develop a CBM-related technology in 2018 and completed it in the first half of 2021. They are planning to complete the verification of the system’s availability and maintainability through various projects in and out of the country by 2024. Through this, they attempt to solidify their position as a leading company in smart maintenance field in domestic, and further increase the reliability of the system in the overseas market as an emerging digital service company.
The most advanced maintenance solution, CBM system
Changes in the trains maintenance methods
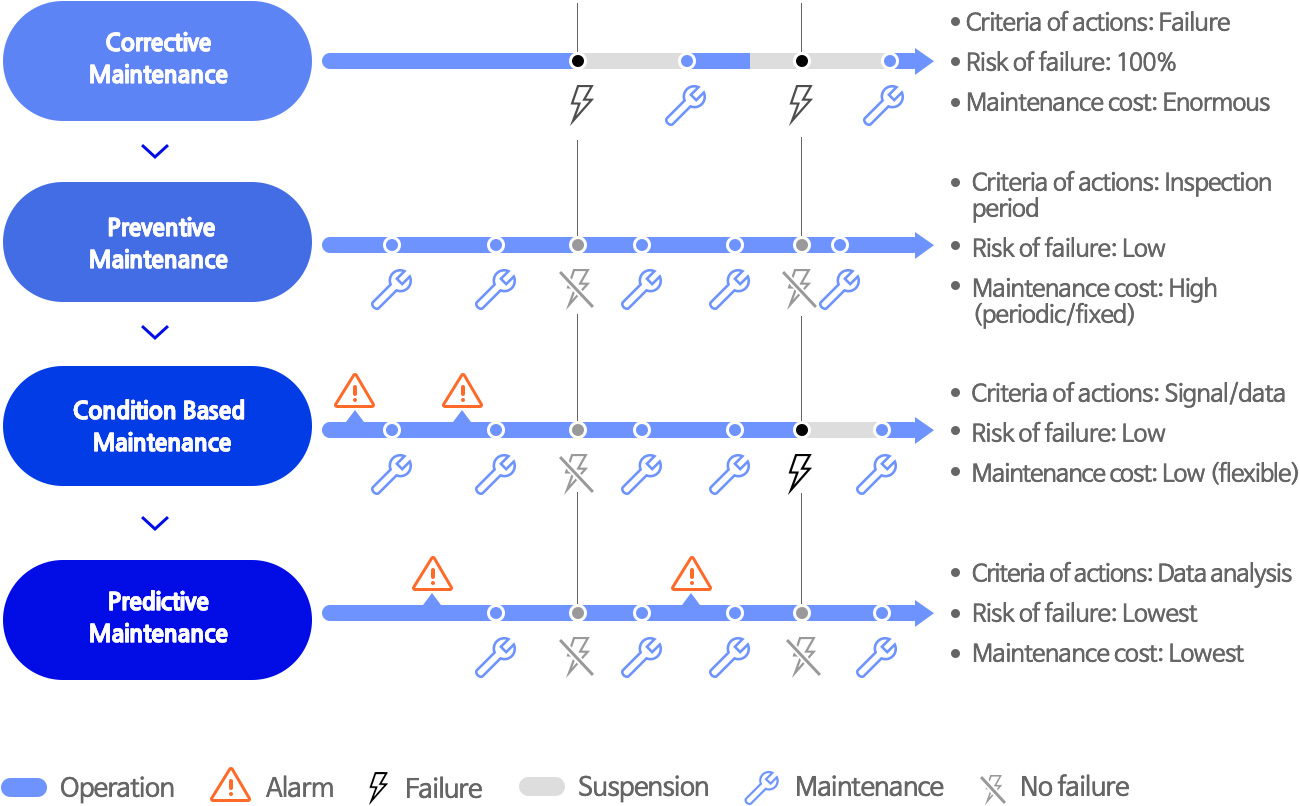
In the past, trains were maintained by corrective maintenance where trains were inspected when a failure occurs and preventive maintenance where trains were inspected at a set interval. Preventive maintenance is a passive measure to prevent a component’s defect and failure by replacing, adjusting and inspecting the component at a set interval regardless of the components’ condition. Accordingly, it had a disadvantage in that it causes idle time during the maintenance activities performed regardless of the components’ remaining life.
The next advanced form of maintenance method is Condition Based Maintenance (CBM). The CBM method is to check the condition of cars and main devices using various sensors and maintain trains in optimum condition by collecting and analyzing data of failures and maintenance activities. Hyundai Rotem developed the CBM system considering the following 4 steps:
• Data collection
• Data preprocessing
• Condition diagnosis and failure prediction
• Maintenance application
The CBM technology enables predictive maintenance where it is possible to early detect a defect through real time monitoring and predict the progress of defects in components by tracking the deterioration conditions. The characteristics of such maintenance are that it can reduce costs by considering a defect in functional components as well and maximize operating efficiency by effectively managing a maintenance plan with prediction of component life. For this reason, the CBM is called an ultimate maintenance method.
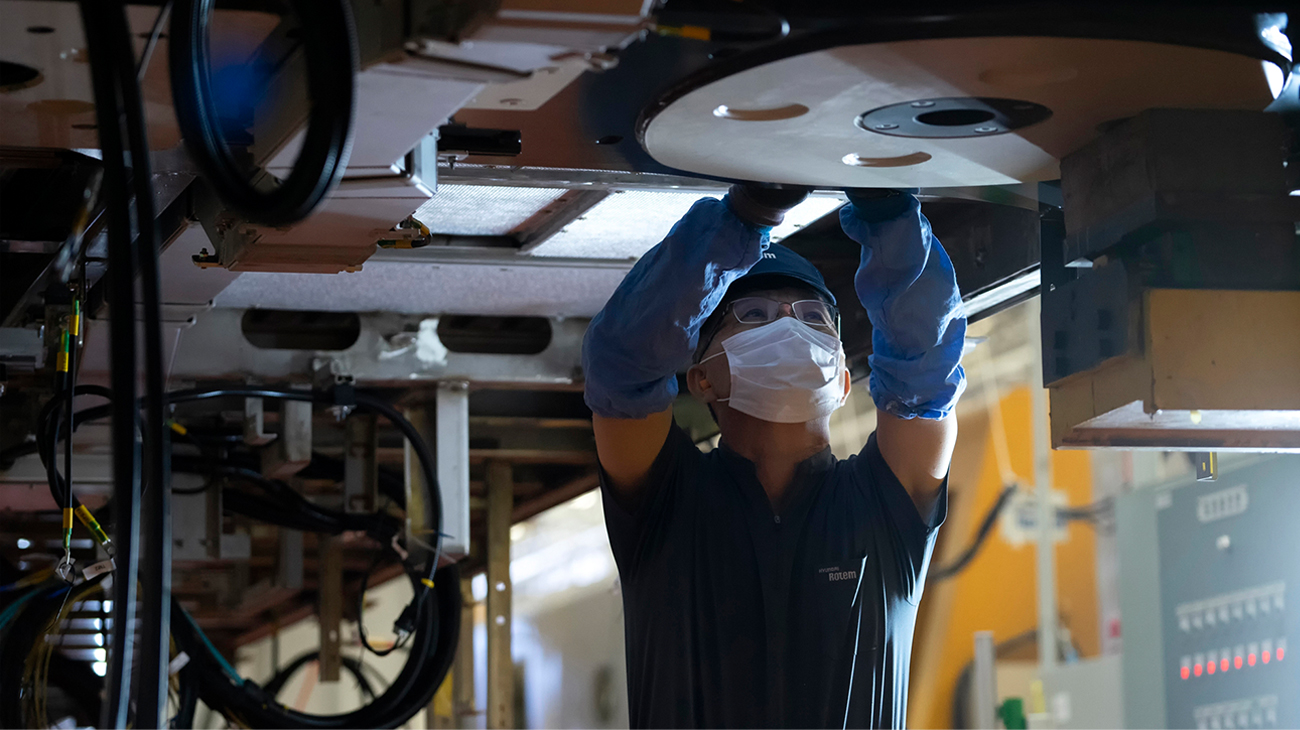
The CBM system plays the largest role in optimizing the life cycle cost (LCC) of trains because it can predict the main components’ remaining life and determine the most efficient inspection and replacement intervals in advance. Therefore, it can reduce the maintenance cost and spare parts in stock up to 30% while increasing the life of components up to 40%. This is why efficient maintenance has emerged as an important issue in the design and development field, as well as the trains operation field and Hyundai Rotem has developed a smart maintenance technology.
Fusion of industry 4.0 technologies such as big data and machine (deep) learning
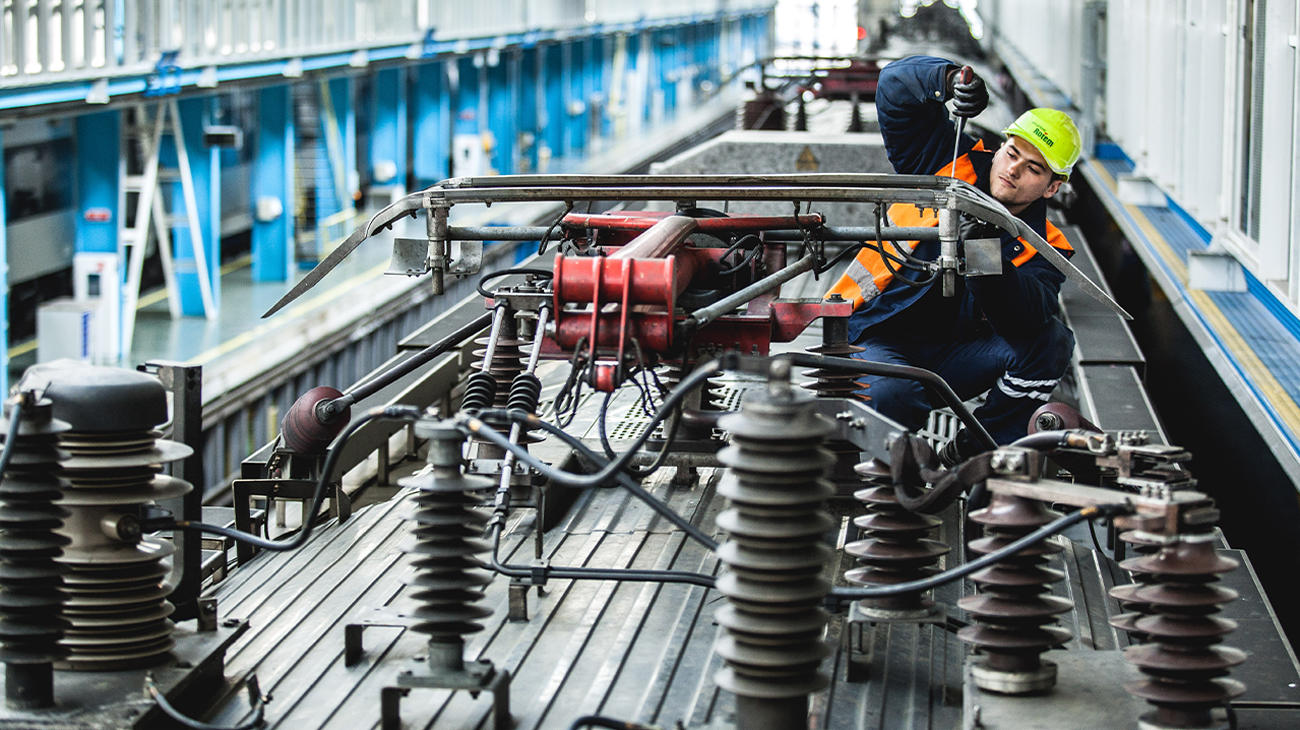
Big data are a primary element of CBM system that runs based on failure and condition data of trains and components. Big data analysis is performed in 3 steps as follows:
• Data collection
• Data preprocessing
• Data analysis
To perform necessary functions by step, complex and various tasks are required. Thus, Hyundai Rotem made a list of sensor master prior to system development and selected a sensor type and application method and data collection and preprocessing methods. Subsequently, they determined the requirements of data analysis solution by step, necessary for analysis of collected data. In addition, all data of trains in operation were needed for condition-based maintenance. This was done by wired/wireless sensors connected to main components, analogue digital converter (ADC) that collects and sends data from sensors and edge server that collects and manages all train data.
Conceptual drawing of the CBM
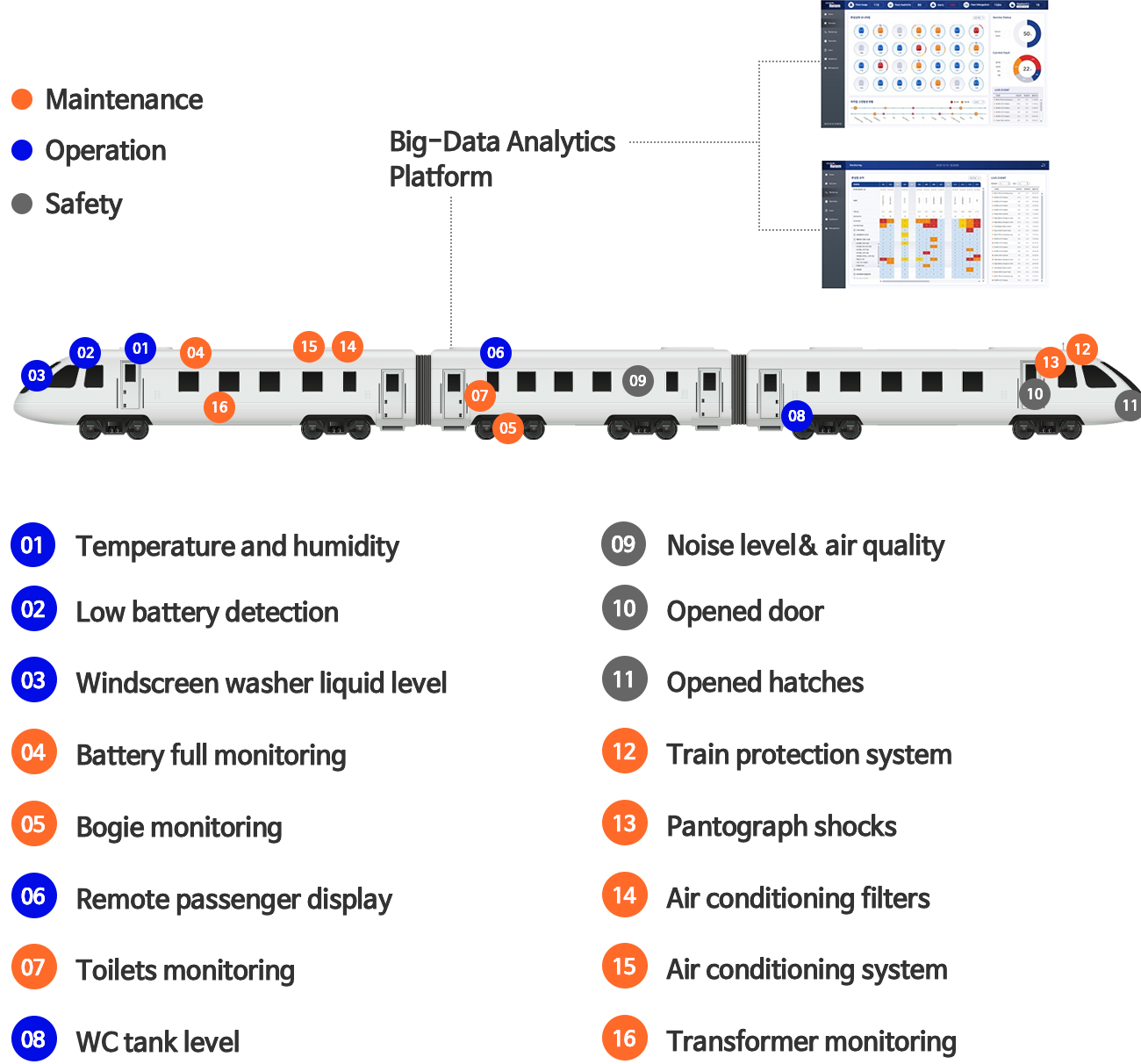
Hyundai Rotem has developed an on-board CMB system as well as on-ground CBM system (on-premise and cloud system). The on-board system preprocesses, analyzes and saves the condition data collected by sensors directly connected to main systems in trains. The on-premise and cloud system gathers and manages data through the main analysis server that collects, stores and analyzes data. Also, it visualizes data to enable the most efficient operation and maintenance for users.
Structure of the CBM system
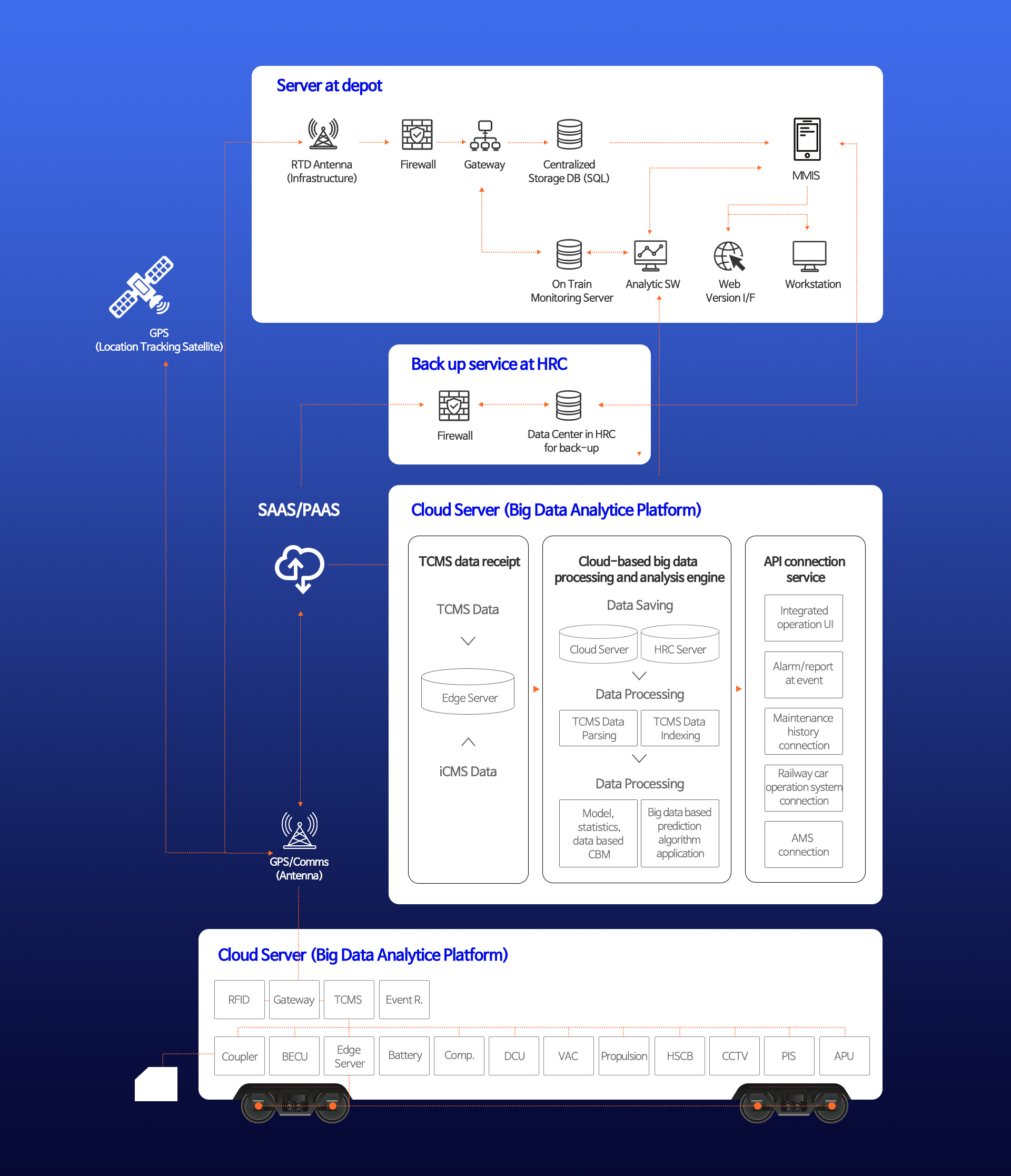
For successful performance of the CBM system, useful data should be collected and classified. For this, Hyundai Rotem has created a database (DB) architecture. An enormous amount of data is collected according to the set DB architecture. The massive data collection facilitates classification and analysis of various data on the location of cars and main systems, acceleration, flux, voltage and noise, etc. Of course, it collects the condition data of train’s axle bearing, decelerator’s temperature and vibration frequency that are directly associated with safety real time. Monitoring the bogie condition is essential for efficient maintenance cost, not to mention safety.
Train data collection and preprocessing process in CBM System
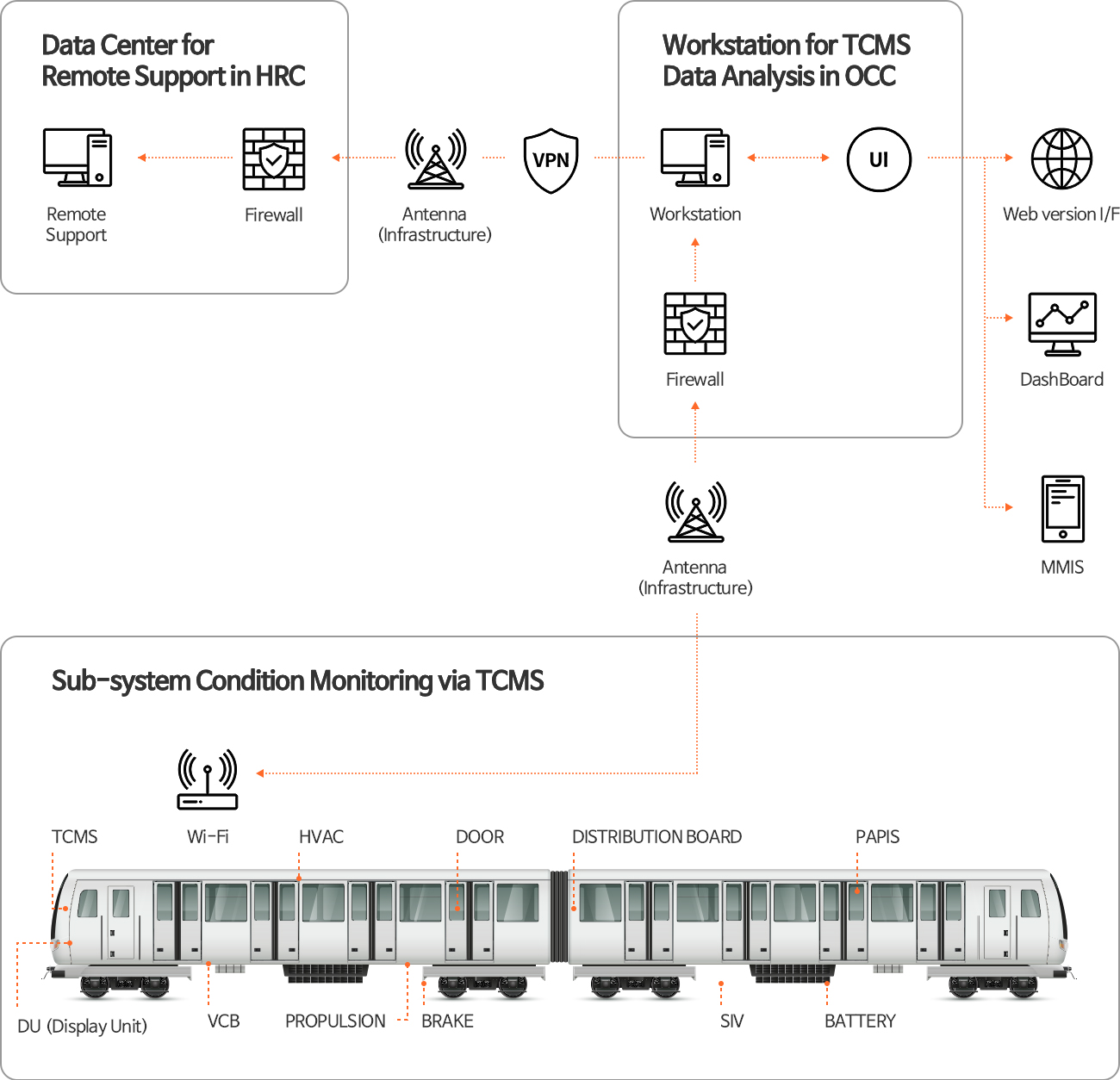
Data collection is performed by car. Data are collected from various sensors in trains and main systems by data collection devices. Collected data are sent to an edge server in the driver’s cab for preprocessing and analysis process. Subsequently, key data on the condition of main systems are sent to the operators in the driver’s cab through a monitor. Relevant data are sent to the railway operators and maintenance mechanics real time through a wireless transmission device or to the on-premise server when the train enters into the station. This process enables preventive maintenance by predicting failures and inspecting main component deterioration. If an unexpected failure occurs, it automatically analyzes the cause of failure and shows the need of emergency action and recovery in connection with a failure reporting analysis and corrective action system (FRACAS).
Hyundai Rotem developed a data analysis logic and algorithm that can diagnose the condition of main devices and analyze failures in the above process, along with an efficient dashboard that shows the process. Also, they enhanced data security using blockchain technology and achieved a stable transmission speed. Moreover, they increased the reliability on diagnosis by applying a deep learning technique to analysis of enormous data. For reference, all data collected in the central server are analyzed and evaluated in a way that can maximize the feasibility of LCC by reducing maintenance costs.
According to market surveyor Global Market Insight, the trains maintenance market size is expected to rise from USD 35 billion in 2019 by 8% per annum by 2026. Namely, the market has endless potential. The CBM system provides new opportunities to companies and safe ride environment to passengers. Hyundai Rotem is creating a CBM system by combining industry 4.0 technologies such as IoT, big data, cloud and edge computing. They are planning to reposition themselves as a total railway service provider by providing operation and maintenance services, in addition to rolling stock manufacture.