The digital world is turning into reality. With the advancement of technologies such as the internet of things (IoT), big data and cloud, it is shifting from imitating to completely interplaying with reality like virtual reality and metaverse. Among them, Digital Twin, which is a virtual representation of reality, is emerging as a mainstay of digital transformation. Because it can verify tens of thousands of scenarios that can occur in reality in a short-term and be applied to various fields extensively. In line with this, Hyundai Rotem is preparing for a clean and safe hydrogen society using a digital twin.
Digital twin emerging as a key to Digital Transformation
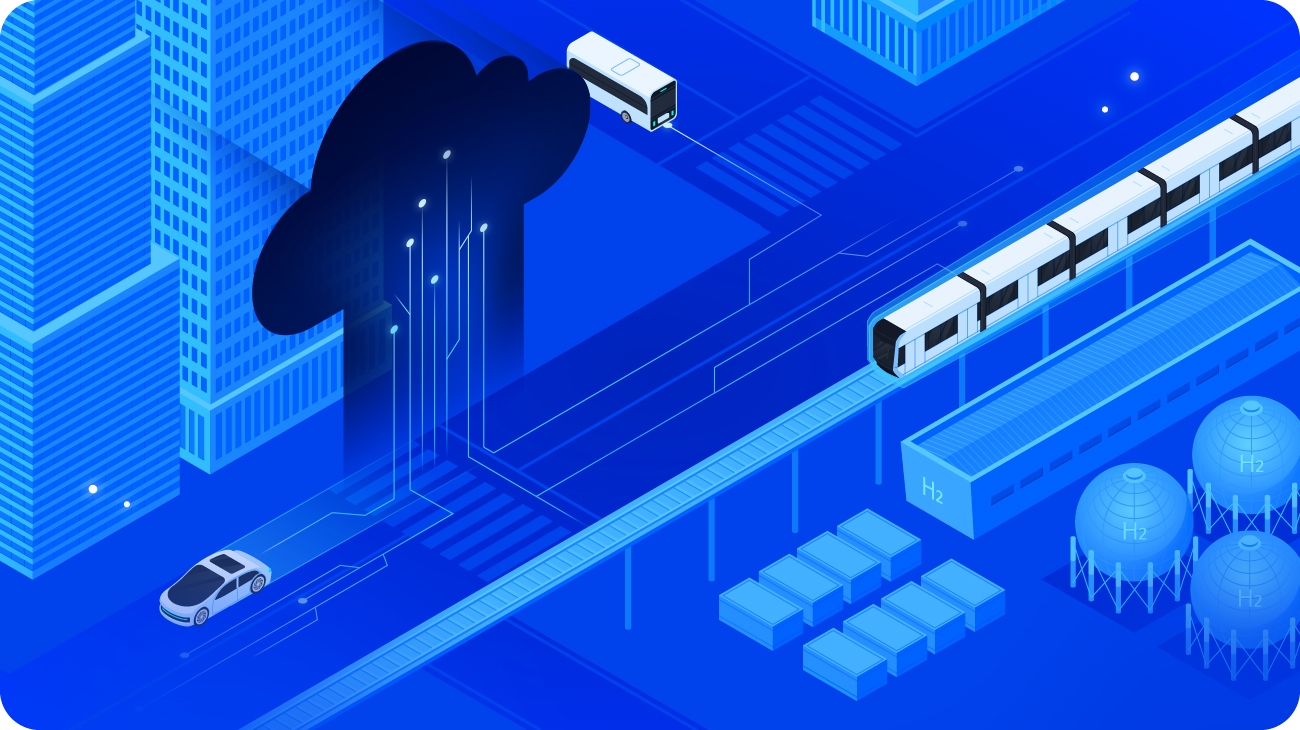
Digital transformation is one of the widely discussed topics across the industries in recent days. It means converting all corporate assets into data for better management and operations, from materials and human resources, as well as products and services. The IBM Institute for Business Value defines digital transformation as a strategy to change business models and set a new direction for business by integrating physical elements digitally. Namely, it is to create a new value through digital integration and gain future competitiveness thereby.
The core technology to realize the digital transformation is the digital twin. Gartner, an American market survey company, listed digital twin in the 10 prominent future technologies for three years from 2017. Also, Mckinsey, a global consulting company, predicted that digital twin will create an economic value of USD 3,900 billion (approx. KRW 4500 trillion) by 2025. As above, digital twin is essential for corporate survival amid the 4th industrial revolution that is underway.
Digital twin conceptual drawing
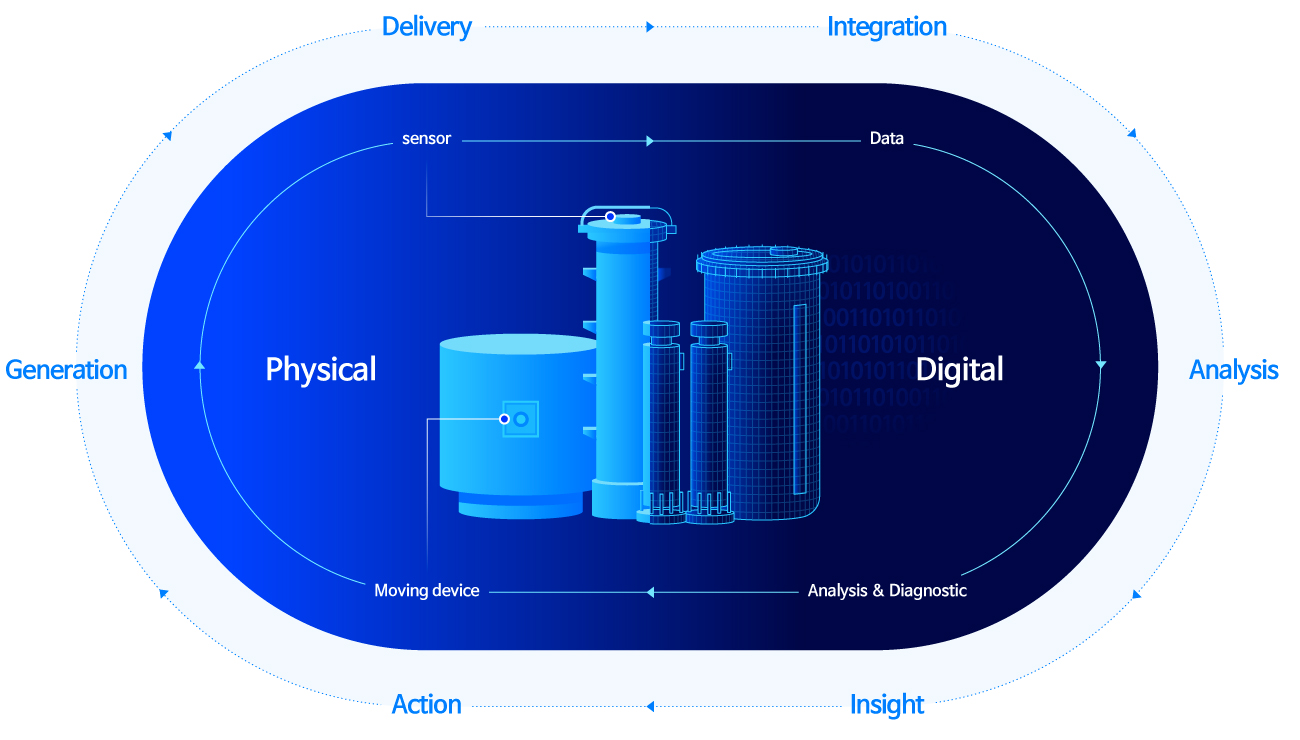
Digital twin is a technology that creates the real world in a virtual space accessible by computers and other IT devices. It applies the actual design of real objects such as machine and equipment, mechanisms and software such as application program. Remarkably, it does not just copy the look of the real world, but also applies the laws of physics in the real world. It embodies the environments and constraints of the real world from time and climate to light reflection, gravity and momentum according to material properties. Thus, digital twin requires data to connect the real world and virtual world, as well as visual objects and employs the key technologies of the 4th industrial revolution such as IoT, artificial intelligence, big data, cloud, fifth-generation communication and mixed reality.
3 Levels of digital twin
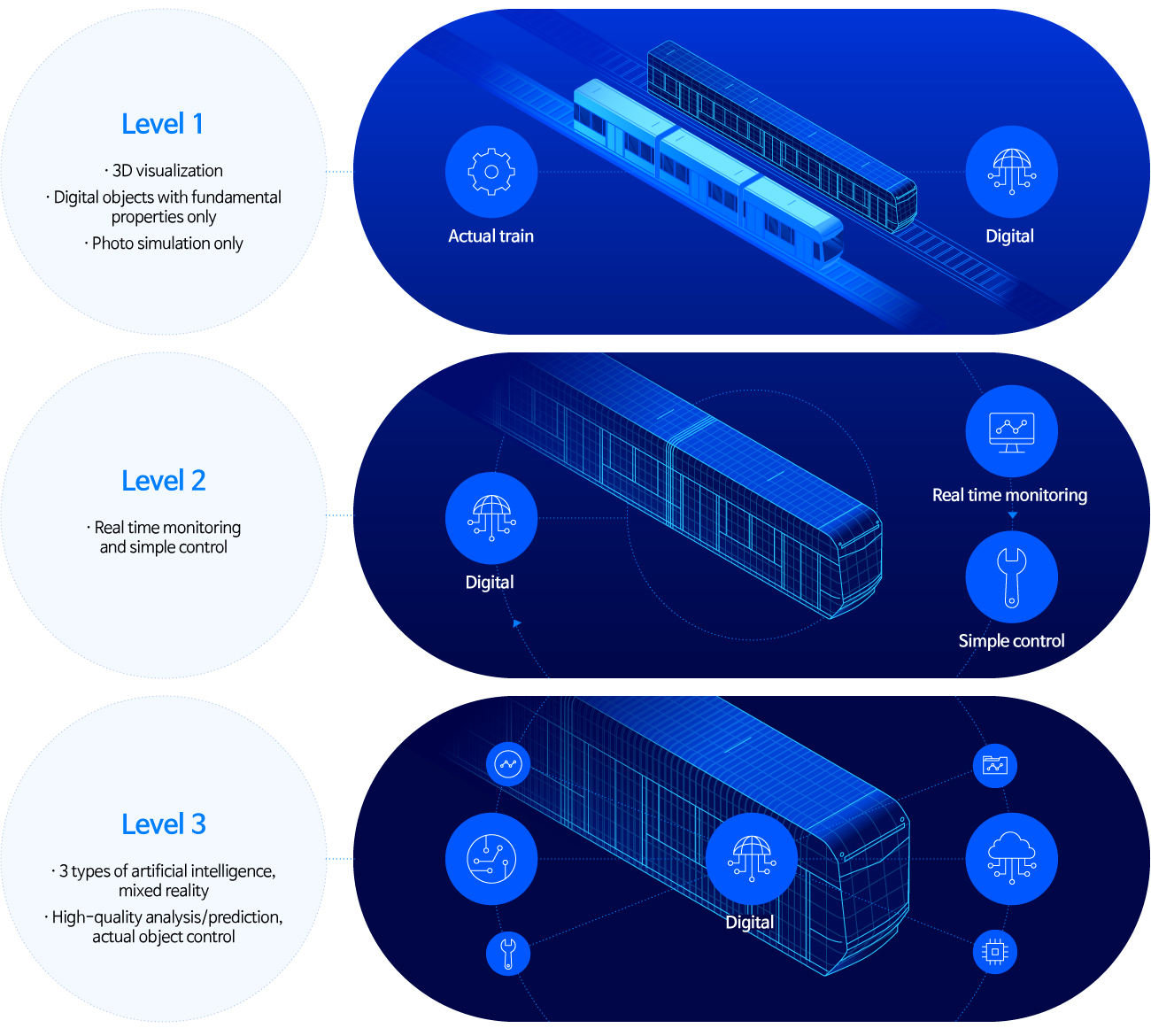
Digital twin can be divided into three levels according to the integration level. Level 1 creates a digital object with the fundamental properties only and provides 3D visualization for prior simulation. Level 2 allows real monitoring and simple control. Level 3 allows high-quality analysis and prediction and actual object control using artificial intelligences, mixed reality, etc. It is the ultimate goal of the industries as it allows to simulate products, programs and policies for prior verification and establish a response plan based on the simulation results by predicting possible errors in future. In addition, digital twin is highly scalable and thus can be utilized in various industries from design to manufacture, trial operation, maintenance and training. It is a solution that integrates all data with visual data organically.
Hyundai Rotem preparing to build a hydrogen society using a digital twin technology
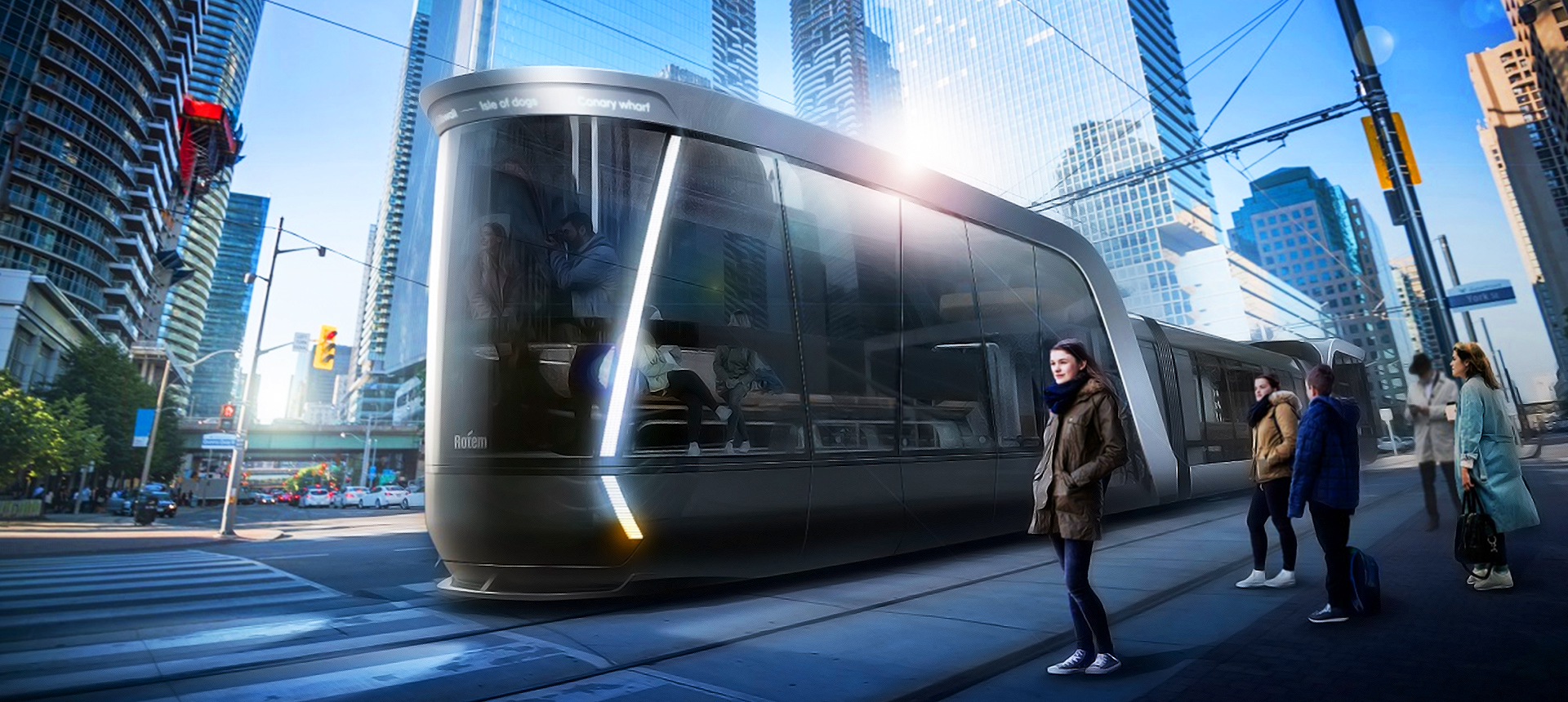
The wind of digital transformation is also blowing in the railway industry, which is the nation’s key industry. As the leader of the nation’s railway industry, Hyundai Rotem is digitalizing the trains and its main systems. In particular, it is developing a hydrogen control system that can monitor the hydrogen infrastructure at one point, from hydrogen electric trams to hydrogen production and station using a digital twin. Although hydrogen is a clean energy regarded as a new energy source of future society, there is not much progress in building the hydrogen infrastructure due to the lack of understanding of its stability and safety of main systems. Moreover, hydrogen electric trams and hydrogen production facilities consist of various components interconnected in a highly organic and complicated structure, which makes it hard to find a failure or defect even when a system failure or abnormality is detected and requires a considerable amount of time in analyzing and fixing the cause.
Hyundai Rotem is preparing a digital twin using condition-based maintenance (CBM) technology as the key technology for safe transition into a hydrogen society. Digital twin allows a design and modeling that can check various interactions between major components and trains and other components during the life cycle of the main components and can deduce a prediction scenario through real time diagnosis and analysis. Hyundai Rotem’s digital twin in essence secures the reliability and safety of the entire system by more effectively managing the main components of trains.
Hydrogen Enterprise Management System, an extension from a real time diagnostic monitoring technology
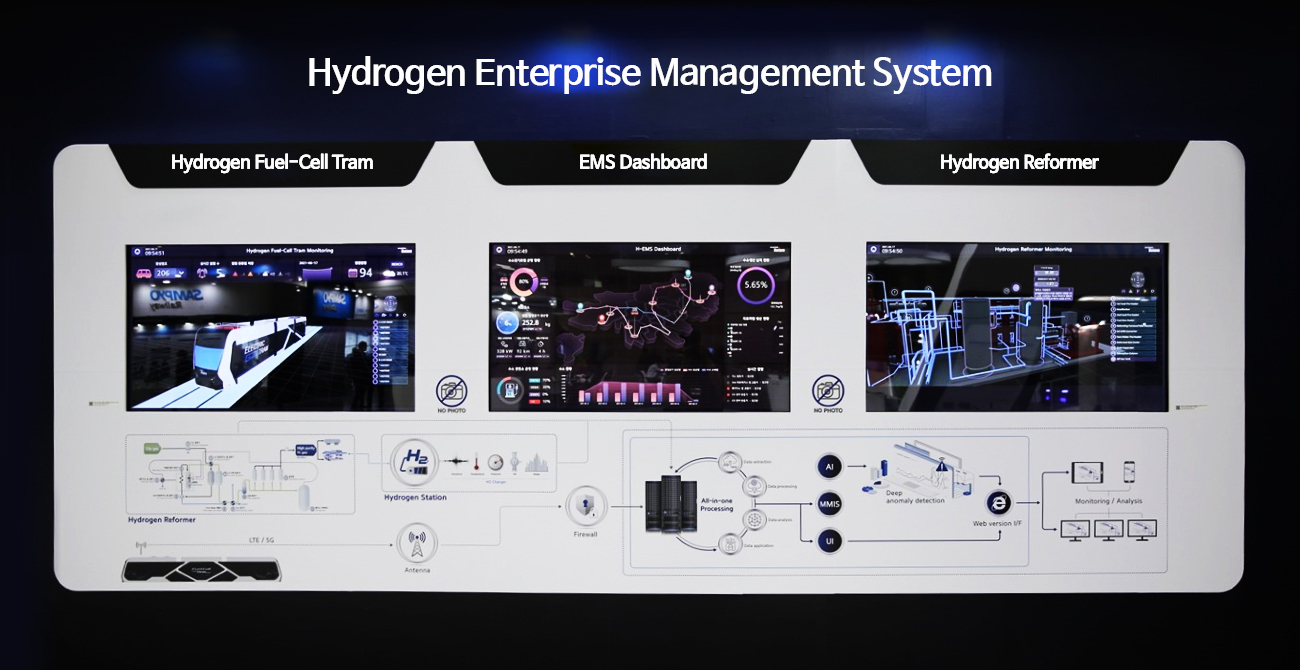
Hyundai Rotem’s Hydrogen Enterprise Management System is a digital service to enable efficient operations and optimum maintenance using a digital twin created by monitoring the operations and conditions of hydrogen electric trams and production facilities in real time. It checks the hydrogen infrastructure in whole real time and visualizes the results on a user-friendly dashboard to enable instant response and assistance to any contingencies. After all, the Hydrogen Enterprise Management System is a hybrid technology that integrates a digital twin that enables a simulation under various conditions by collecting system data and CBM technology that allows corrective/preventive maintenance based on real time condition data.
The Hydrogen Enterprise Management System collects and analyzes data by monitoring the operation data of hydrogen electric trams, condition and failure data of main devices and deterioration of main components real time. Also, it can monitor and diagnose the station facilities for hydrogen electric vehicles and trams, as well as hydrogen production facilities that extract hydrogen from city gas, to allow for more efficient and safer management. A digital model of operating environment and entire process of system is generated in a virtual operating environment using the IoT-based sensors and ICT-based data collection methods inside the infrastructure and various external operating environments are entered. Then, various simulations are performed using the model to predict a possible failure in advance by checking an error from actual processes and provide a user-friendly visualization tool for increased reliability of system and operating efficiency. The final analysis results can be utilized to set up a response and action plan in reality.
Introduction effect of a smart control system using a digital twin
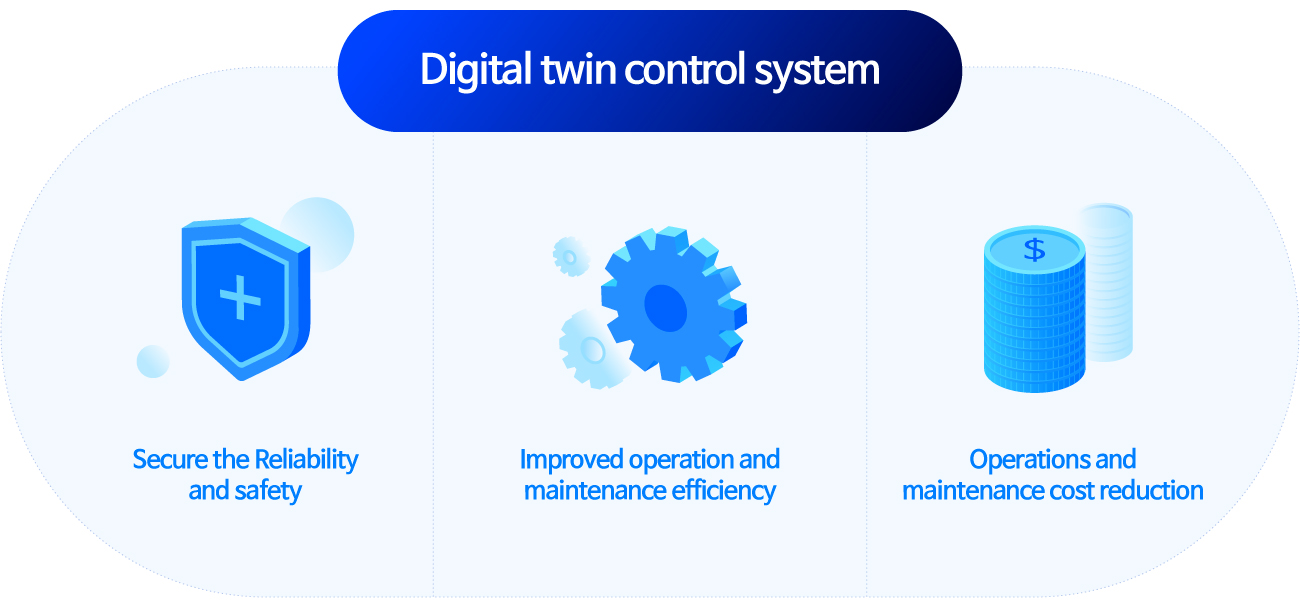
The digital twin-based Hydrogen Enterprise Management System can be widely used in various ways during the life cycle of the main facilities. It improves operating efficiency when applied to real time monitoring and diagnosis and maintenance efficiency when applied to remote maintenance support, which leads to cost reduction and quality and availability improvement.
Additionally, it can contribute to the general operations of main hydrogen system and efficiency indicator management through a user-customized data visualization dashboard. Further, it is expected to be used for value creation of new market and bring a change in business models. Hyundai Rotem is accelerating the development of technology that organically combines a digital twin with visualization and diagnosis/prediction algorithm, as well as data collection through real time diagnostic monitoring, and carrying out technology and market standardization.
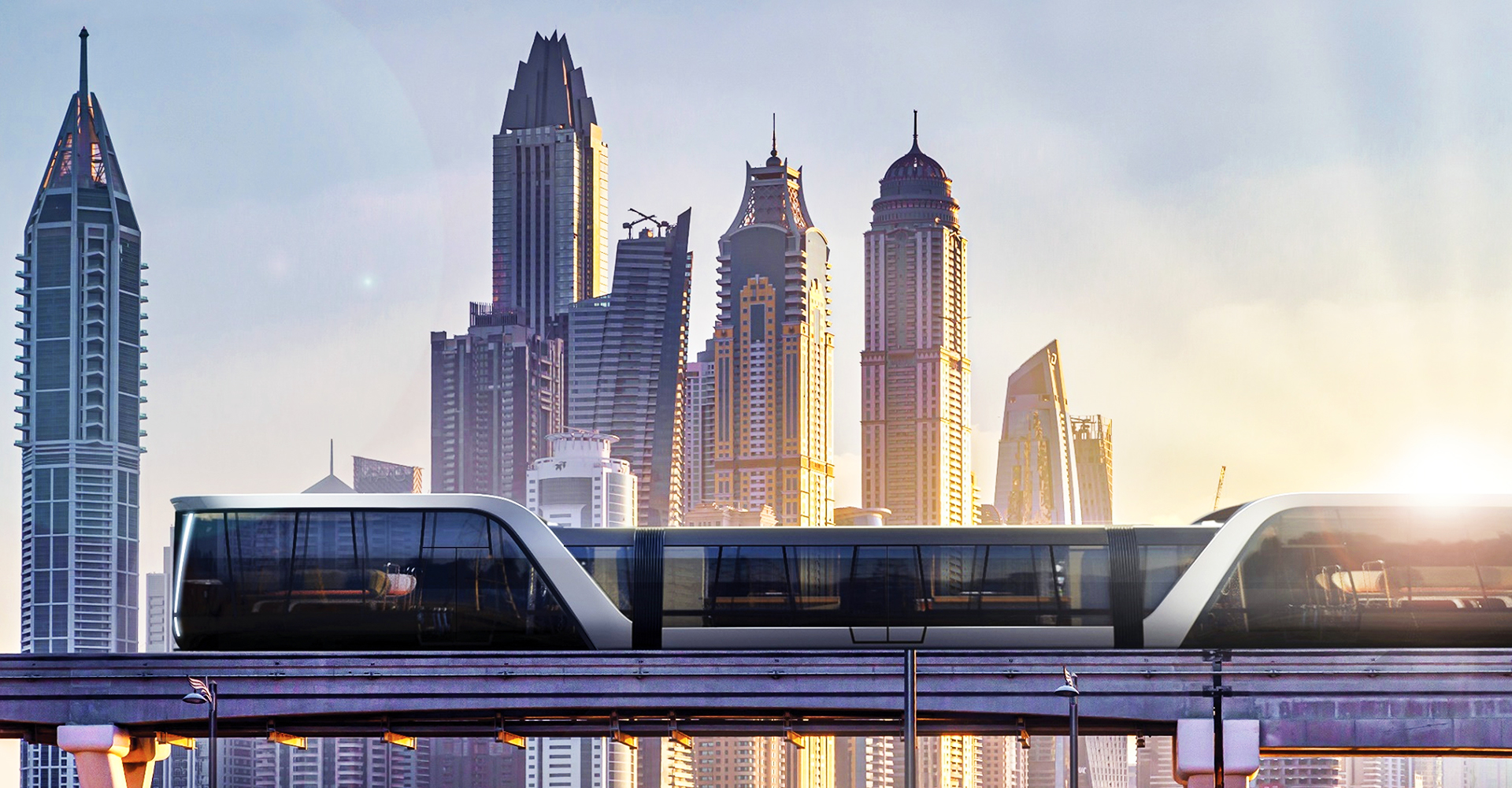
Focused on hydrogen, a clean energy, with a blueprint for future hydrogen society, Hyundai Rotem is developing various hydrogen infrastructure facilities such as hydrogen electric trams, hydrogen production facilities and hydrogen stations. Developing the smart hydrogen control system using a digital twin and real time diagnostic monitoring technology is strengthening the basis of a safer and more convenient hydrogen society. Turning into a hydrogen society is essential to give sustainability to our living foundation. To bring it into reality, Hyundai Rotem is planning to continue to put its all technologies and resources into integrating smart and eco-friendly technologies.