As a means of transportation responsible for the movement of a large number of passengers, ensuring the operational safety of the GTX trains is crucial. Considering it is a semi-high-speed train operating at a maximum speed of 180 km/h and a scheduled speed of 100 km/h, special maintenance is required to keep the trains in optimal condition at all times.
Hyundai Rotem has incorporated over 20 years of accumulated expertise in the development of commuter and high-speed trains into the production of GTX trains. Additionally, it has applied the smart maintenance system technology, which was formalized in 2018, to the GTX-A line. Advanced railway vehicle maintenance technologies such as “Condition-based Maintenance Systems” and real-time train track detection technologies utilizing AI deep learning image processing, known as “Facility Monitoring Systems,” are prominent.
Both technologies are characterized by their integration with big data analysis platforms to maintain GTX railway vehicles and infrastructure in optimal conditions. In addition, there are plans to explore LCD display systems that utilize integrated Ethernet networks within the vehicle and 5G/LTE networks to provide passengers with operational information in the most efficient and effective manner possible.
The Smart Reliability Monitoring System Checks the Vehicle Status Every Second
Given that the condition of railway vehicles is directly related to passenger safety, thorough pre-inspection, post-analysis, and maintenance are required. An efficient management system for this purpose can maintain railway vehicles in optimal conditions throughout their life cycle, thereby minimizing management costs and risks.
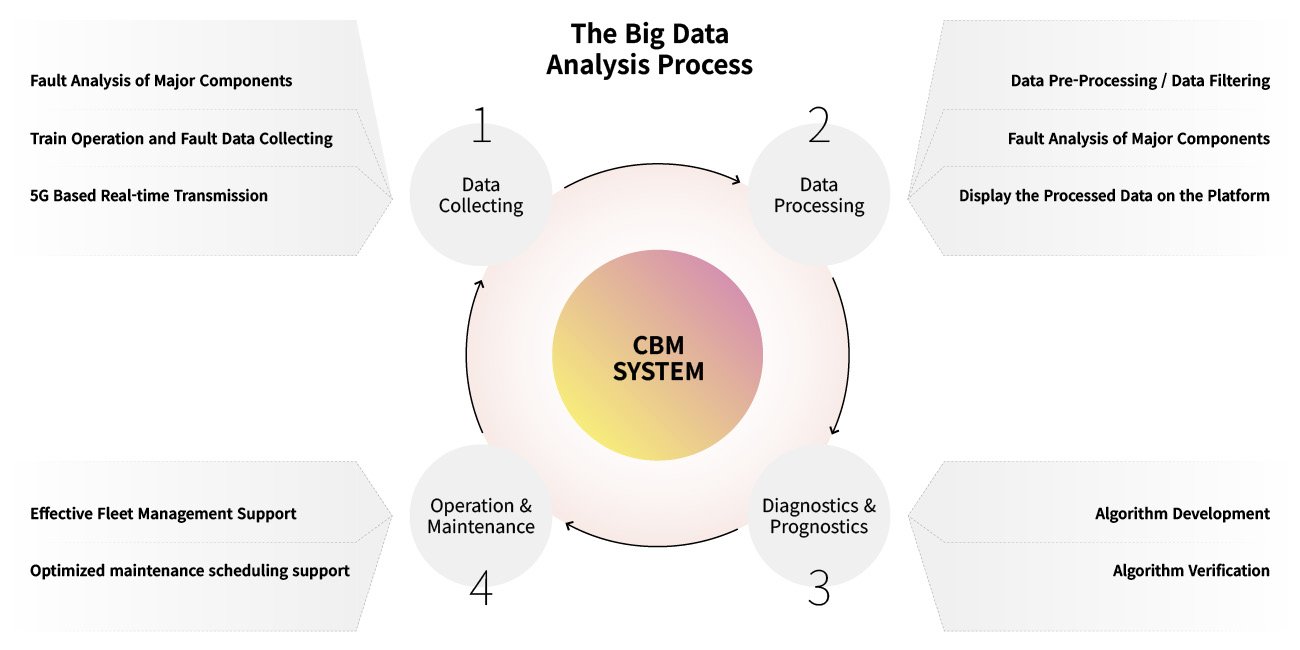
Hyundai Rotem has been researching since 2018 to optimize the maintenance system of railway vehicles and completed the development of the Condition-based Maintenance (CBM) system in 2020. This system, utilizing wireless networks, big data, and the cloud, is a platform capable of both condition-based maintenance based on real-time train monitoring and predictive maintenance based on big data analysis.
Vehicles collect status information from various sensors and data collection devices connected via integrated Ethernet networks. The collected information is transmitted to on-ground servers via 5G network transceivers, and a depot performs necessary operational and maintenance actions based on real-time analysis data from the server.
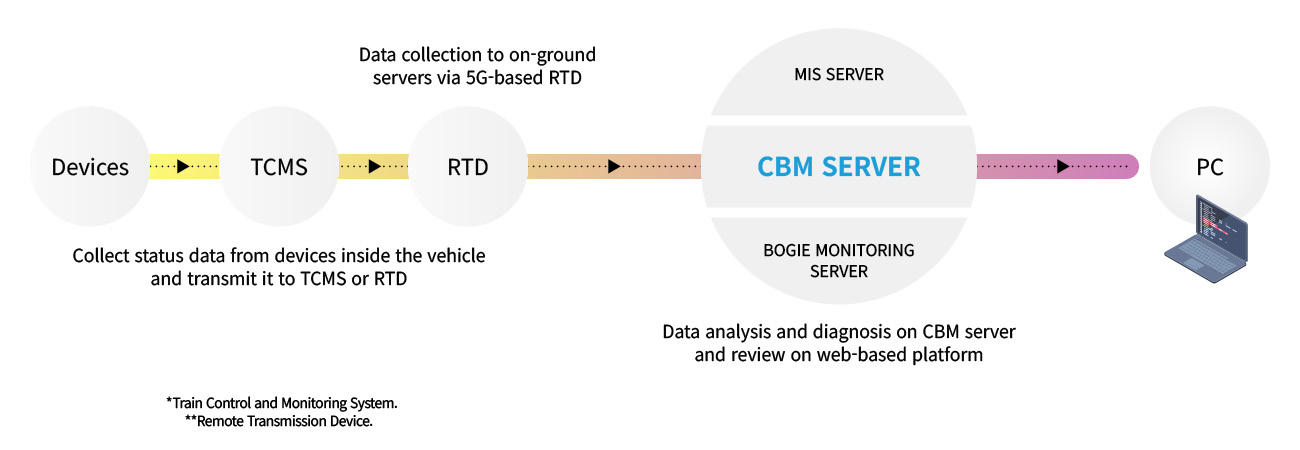
Since all information is collected and transmitted in real time, appropriate actions based on vehicle condition can be promptly taken even during operation. Big data accumulated with vehicle status information and maintenance history is utilized for predicting and optimizing maintenance cycles, enhancing diagnostic accuracy. For this purpose, the GTX-A’s SMART Reliability Monitoring System collects information from 21 devices as follows:
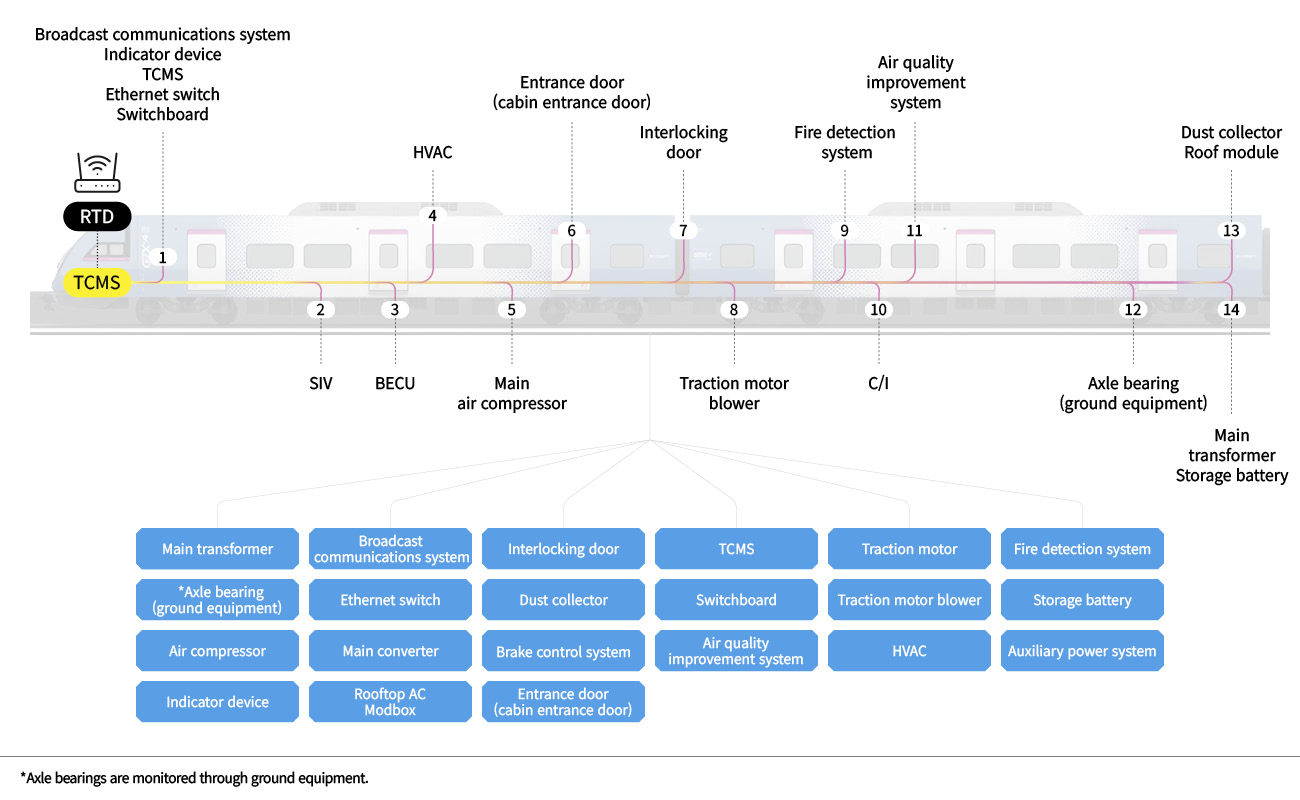
The information collected from the main systems can be broadly categorized into five types, and the trend of changes in the status data of each device collected over a long period allows for optimized maintenance by analyzing the relationship between actual failures (or abnormal behaviors) and status data.
Types of information collected by the Smart Reliability Monitoring System from major systems
Status data: Information such as temperature, current, and operational status of a system
ailure data: Information such as shutdown due to overcurrent or malfunction of a system
Tracking data: Detailed status information before and after failure occurrence
Maintenance data: Maintenance history, replacement history, etc.
Inspection data: Results of Pre-Dispatch Testing (PDT) before train operation
※ Systems without controllers (such as peripheral compressors, power supply systems) do not have tracking data.
※ Since axle bearing data is collected on the ground, only status data and maintenance data are available.
Most of the major systems that make up the GTX-A train are integrated and connected via Ethernet communications network. It adopts the international standard protocol developed specifically for railway vehicles, TRDP (Train Real-time Data Protocol), enabling a simplified system structure. Maintenance accessibility has been enhanced through unified communications cables, and it is also capable of high-speed transmission of large-capacity data with stability among interconnected systems.
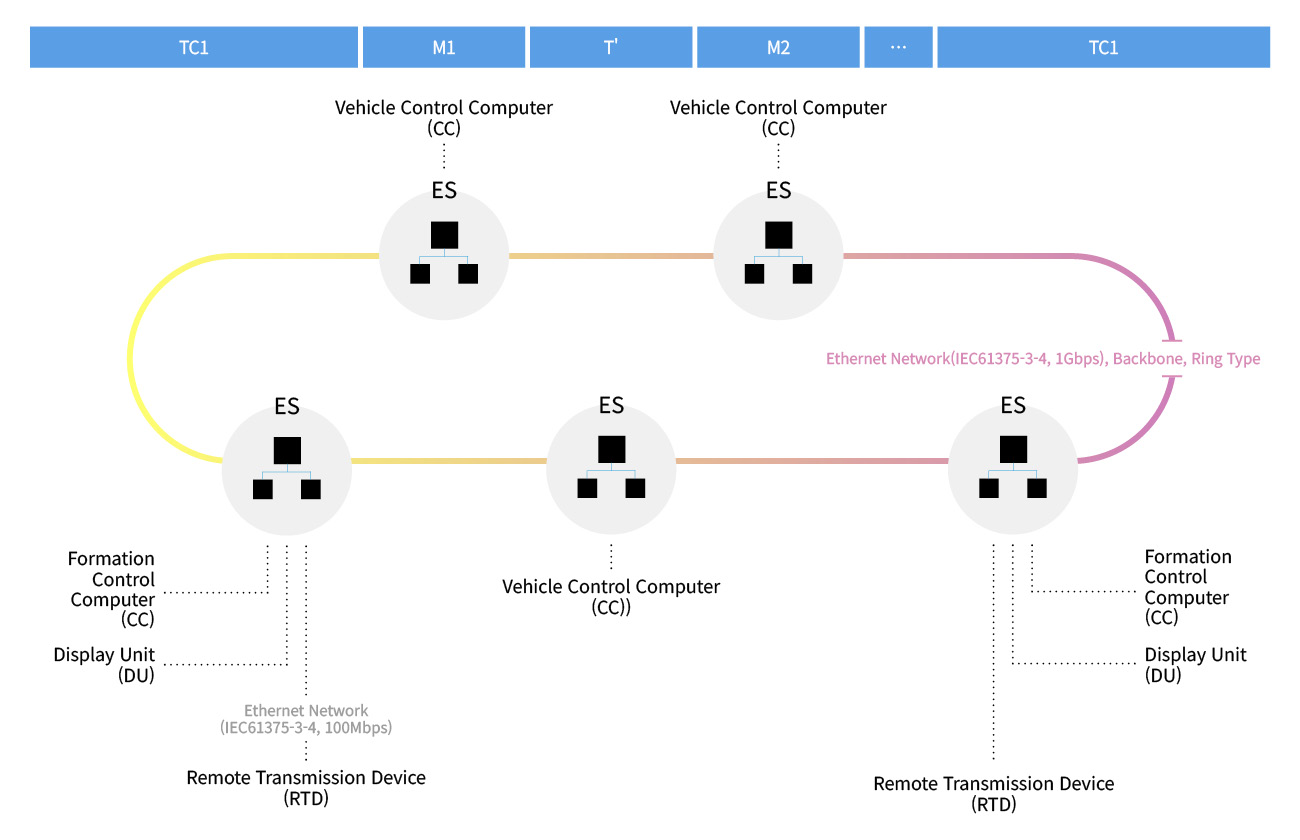
TCMS utilizes an integrated network to monitor the status of 21 major systems within the vehicle, and the Ethernet-integrated network transmits vehicle status information to on-ground devices via wireless communications, utilizing vehicle data transformed into big data to enable efficient maintenance.
Data is collected every 500 ms and transmitted to TCMS or RTD at 1-second intervals for each system, adopting a “system-specific periodic transmission” method. As more data is transmitted, vehicle condition monitoring becomes more sophisticated, improving the coherence of big data.
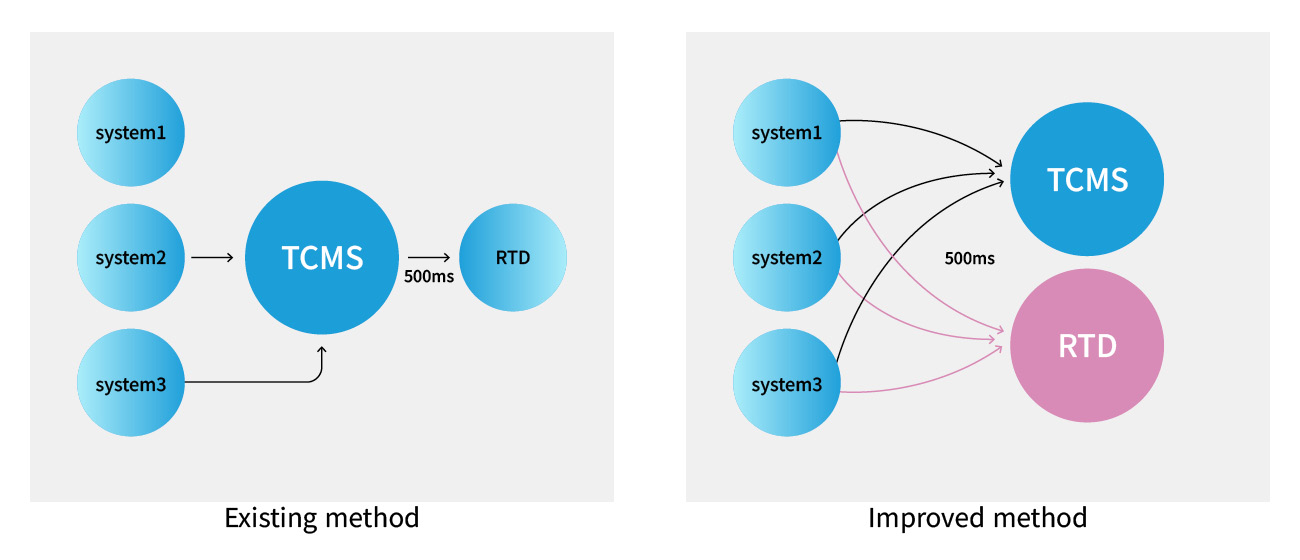
Status data collected from the train are transmitted to the CBM server of the ground base via the 5G/LTE wireless communications device, allowing real-time data transmission during train operation.
Once collected, data on the server is organized into a database according to its characteristics for quick search and accessible to users via PC access to the server. Users can access the server from their PCs to review data with added maintenance history. The collected and accumulated big data is classified and predicted using AI technology such as machine learning and deep learning, and provides time-series analysis. At this time, functions such as generating alarms during fault diagnosis based on algorithms for major systems and managing them, and a big data search engine for big data analysis environments are provided.
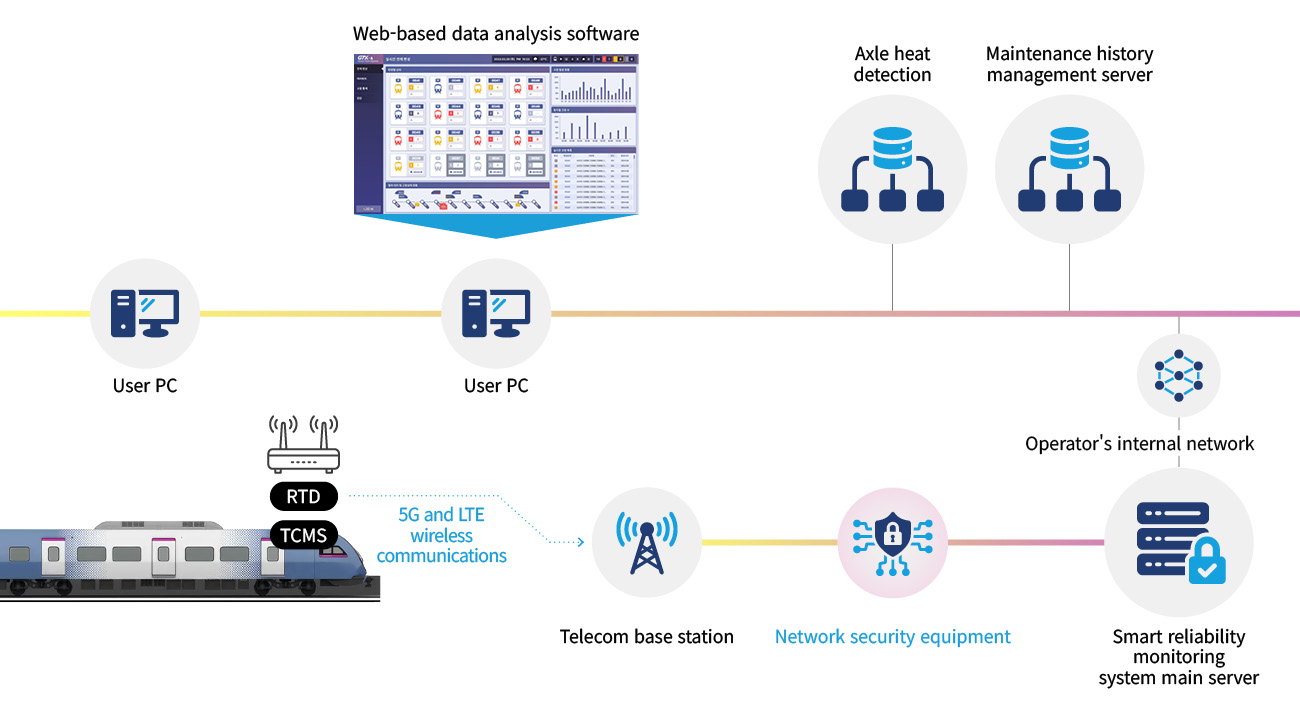
Users at a depot can access the server through web browsers such as Chrome and Edge on PCs. Data is reviewed using dedicated platform software configured within the server. The collected data is appropriately visualized with tables, charts, colors, etc., making it easy to understand the current status and situation of the vehicle. In addition to providing statistical information, the embedded proprietary logic automatically analyzes data from major systems, making it easy to determine their current status.
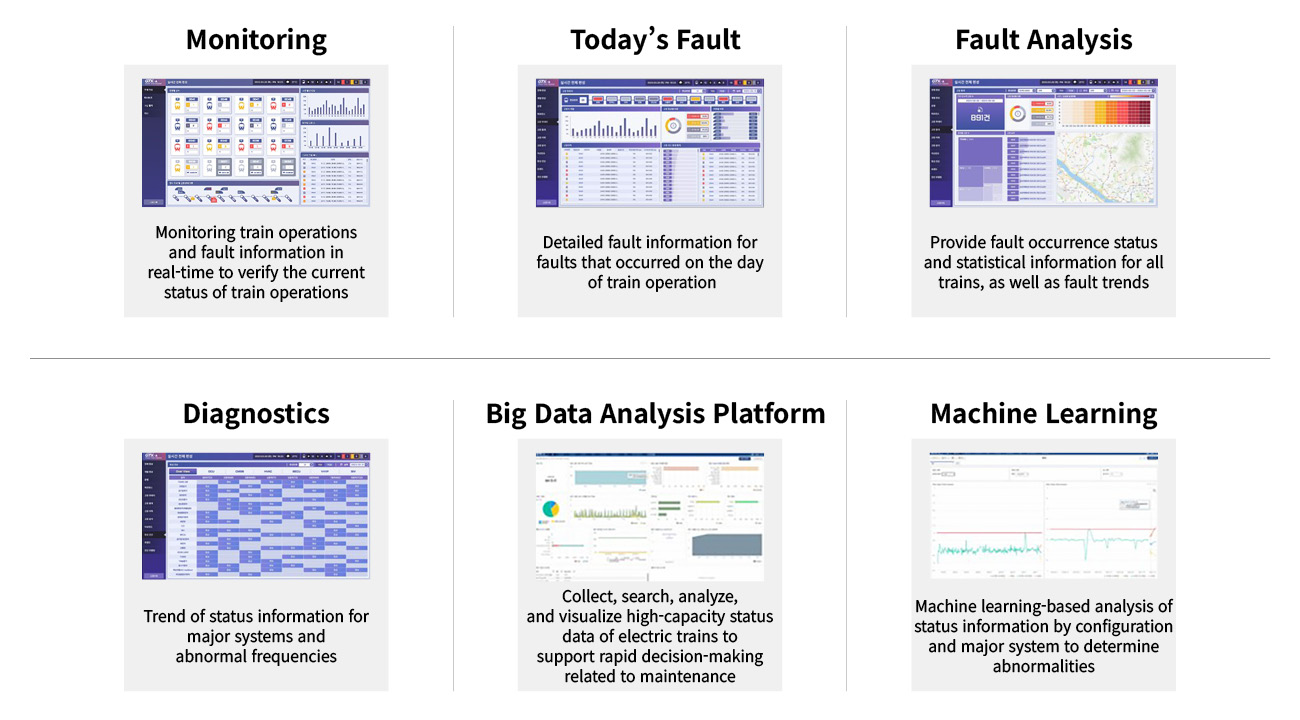
The ultimate goal of the condition-based maintenance system is to enhance maintenance efficiency by utilizing vehicle data This is difficult to achieve with data collected over a short period. Hyundai Rotem plans to collect and analyze operation data over 8 years in collaboration with GTX-A operators to further enhance system reliability.
Facility Monitoring System Using AI Camera Technology to Detect Anomalies in Track Lines and Rails
The GTX train can operate at a high speed without concerns of noise or vibration, as it runs on a deep-level track unaffected by other facilities. Its streamlined design with rails close to straight, minimized air resistance, and an efficient aluminum extruded body allow for smooth acceleration, minimal shaking, and high-speed travel.
As it runs twice as deep underground (40 m below ground) as a regular subway, safety operations should be given special attention. Hyundai Rotem has installed a facility monitoring system equipped with imaging and analysis devices at the front and rear of GTX trains to monitor real-time anomalies in key facilities such as track lines and rails.
A track line refers to facilities installed along the rail to supply power to the train and the structures that support them. Trains primarily use overhead lines, known as the catenary system, to suspend the track line and structure in the air. However, the GTX-A line uses a rigid wire called R-bar rigid track line instead of the typical catenary system.
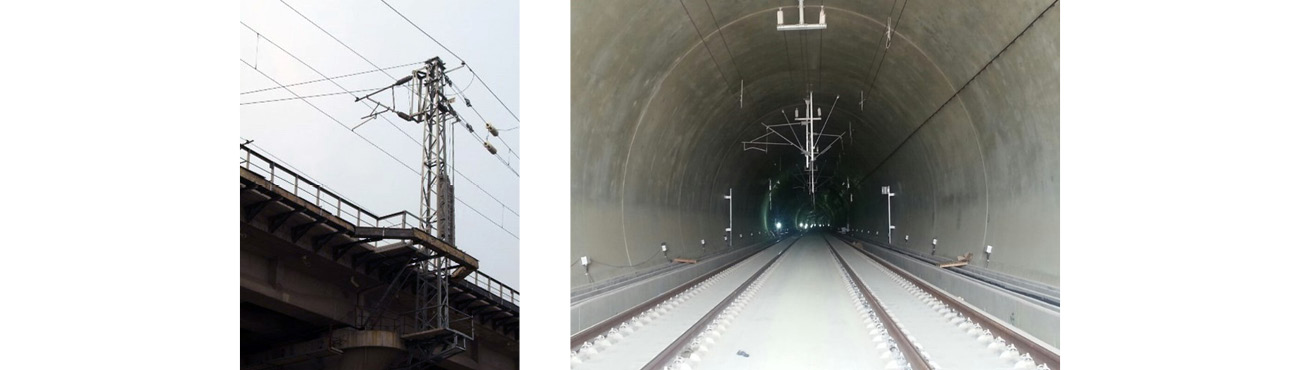
The facility monitoring system installed on the GTX-A train performs real-time inspection of anomalies in two key facilities: track lines and rails. Using AI and deep learning, it uses non-contact optical cameras for image processing to check the condition of facilities, enabling detection of facility anomalies even during GTX electric train operation at its maximum speed (180 km/h).
The detection system is installed on the roof surfaces of TC1 and TC2 vehicles at the front and rear of the GTX trains. Each TC1 and TC2 vehicle is equipped with video (camera and lighting) equipment and LiDAR equipment, each with different roles. LiDAR equipment, which recognizes objects through 3D scanning, detects anomalies and risks around the rails and other facilities. Optical imaging equipment inspects the condition of rails and surrounding facilities and checks for anomalies in the track line.
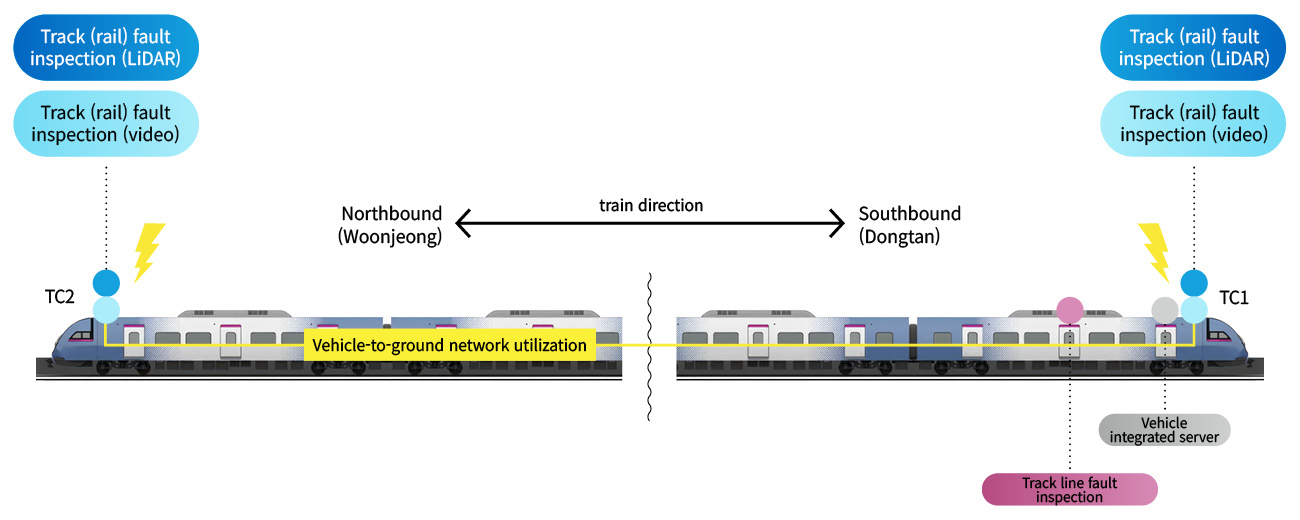
Rail inspection is conducted on both TC1 and TC2. It checks for obstacles on the rail, as well as whether the running rail is damaged. Track line fault inspection is performed by separate optical equipment installed on TC1. It examines whether there is detachment of R-bar track line, its flexural condition, bracket sagging, and dropper disconnection.
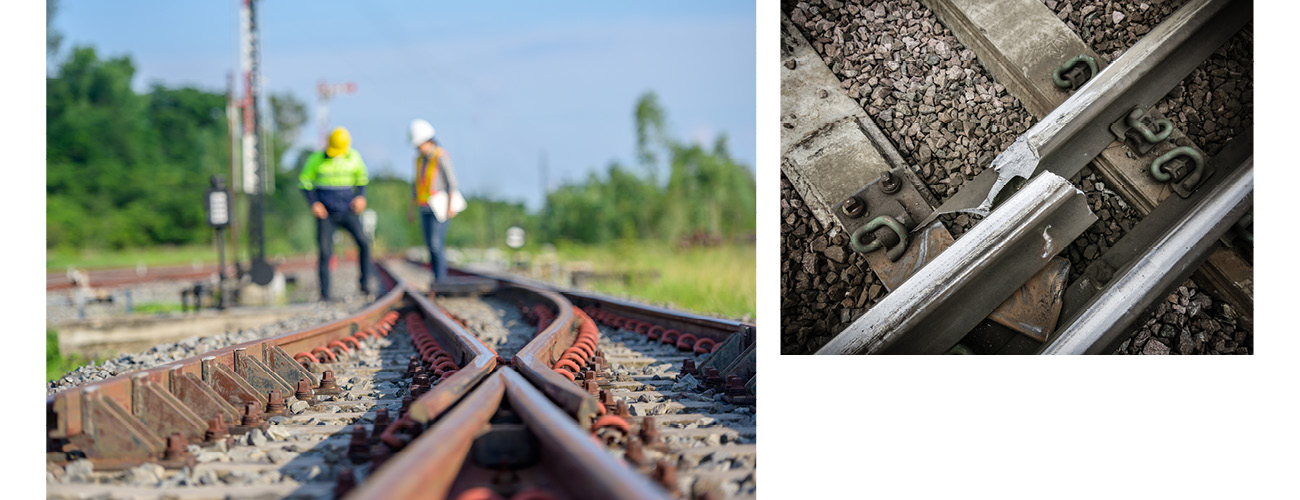
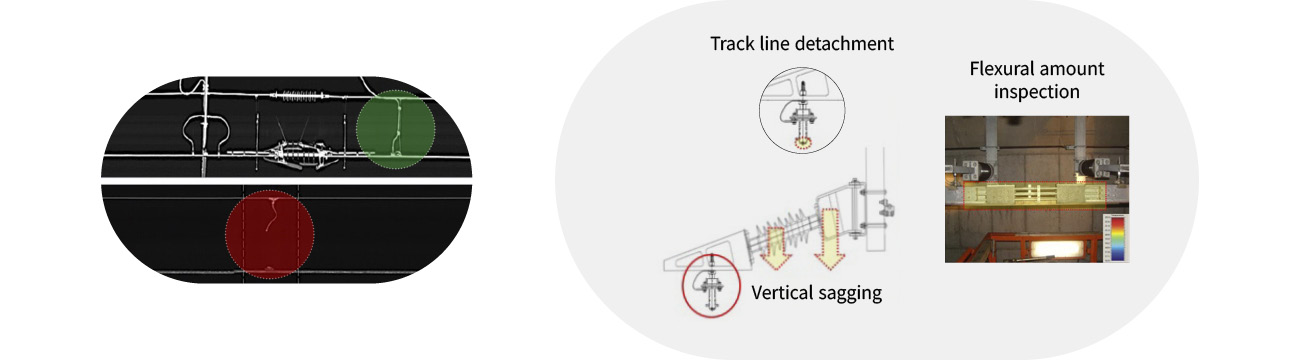
Status information collected from TC1 and TC2 is transmitted to respective vehicle integrated analysis devices via Ethernet networks inside the vehicles, undergoing AI deep learning image processing. Track line related information is handled by TC1’s vehicle integrated analysis device, while rail-related information is managed by TC2’s vehicle integrated analysis device.
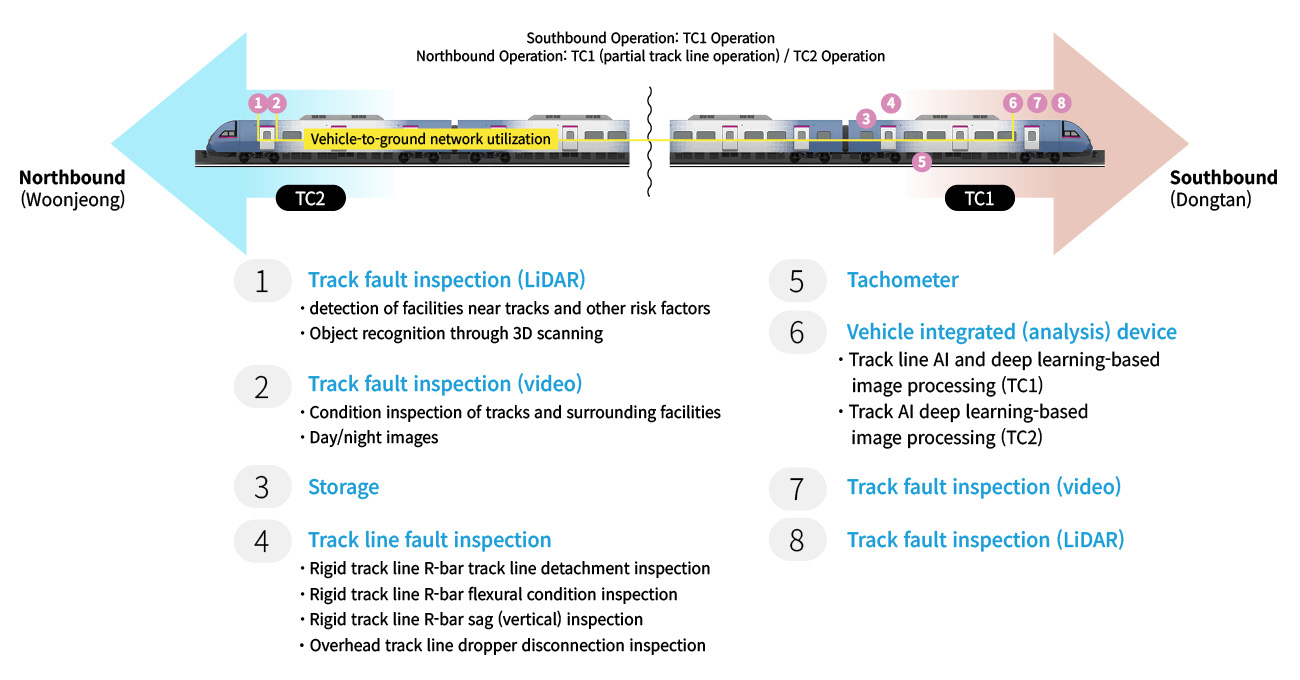
Data collected, processed through image processing by the vehicle integrated analysis device, along with train operation data collected by TCMS and measurement data for inspection, are transmitted to the integrated control center on the ground via 5G/LTE networks. All analyzed data is transmitted in the form of “real-time event alarms” to ensure optimal railway safety operations and can be monitored on monitoring devices at the integrated control center on the ground, similar to a condition-based maintenance system.
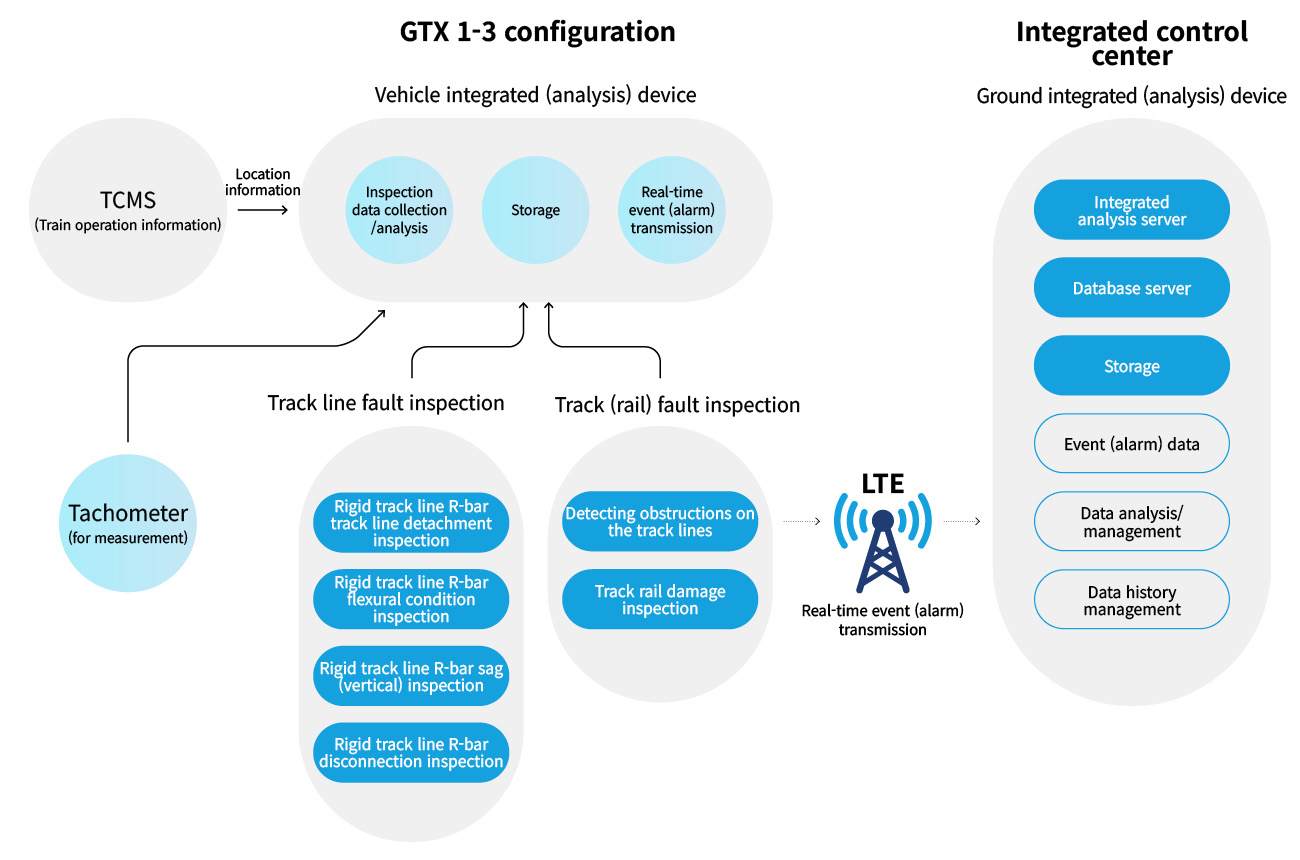
37-inch LCD Display Communicating via Ethernet & 5G Networks
GTX-A trains can carry up to 1,062 passengers with an occupancy rate of 100% (8 cars per formation). Compared to Seoul Metro Line 1, which can accommodate 1,576 passengers with a 10-car formation, GTX offers a more comfortable passenger environment. However, unlike Seoul Metro, which connects many hubs within the city center, GTX operates as a metropolitan express train with fewer stops at Seoul’s downtown terminal (or departure) stations, where a large number of passengers board and alight simultaneously.
To minimize confusion during boarding and alighting, the doors of GTX-A trains are wider than those of typical railway vehicles. The interior entrances of the cabins are designed considering efficient pathways. Additionally, each car is equipped with 2 LED displays and 10 LCD displays. These are intended to provide sufficient operation information for passengers boarding and alighting.
Especially, the wide-type LCD displays utilize a large 37-inch screen to convey various information. They display speed, cabin congestion, indoor air quality, time, next station, and door information (opening announcement, open, closing announcement, malfunction) in both Korean and English graphics received from the integrated controller. It is also possible to broadcast advertisements based on the data transmitted by the integrated controller.
The LCD displays use an IP-based Ethernet network inside the vehicle, similar to a condition-based maintenance system or facility monitoring system, controlled uniformly through the integrated controller. It is noteworthy that content is updated via the RTD system’s 5G/LTE network.
During operation, information such as the entire route map and related information (time, congestion, videos) are displayed, and upon arrival at a station, alternating displays of the arrival station and terminal are shown. Each piece of information is sequentially provided according to pre-designed train operation scenarios to efficiently deliver operation-related information to passengers.

When the train departs, transfer line information for each stop is provided along with the entire route map for 3 minutes. Exit information display is also planned. Gusung station and the Woonjeong~Seoul Station section and Samseong Station are scheduled to sequentially open.

Displayed along with the direction of the doors to be opened immediately after departure. When the train is traveling at speeds above 100 km/h, the logo is displayed in the upper left corner instead of the driving speed.

After announcing the arrival station, passenger congestion levels are indicated based on cabin location. Passenger congestion is categorized as “Spacious,” “Normal,” or “Congested.”

This screen is displayed upon the arrival or entering platform area. When the doors begin to open, the bottom of the screen blinks from green to bright yellow at 1-second intervals.
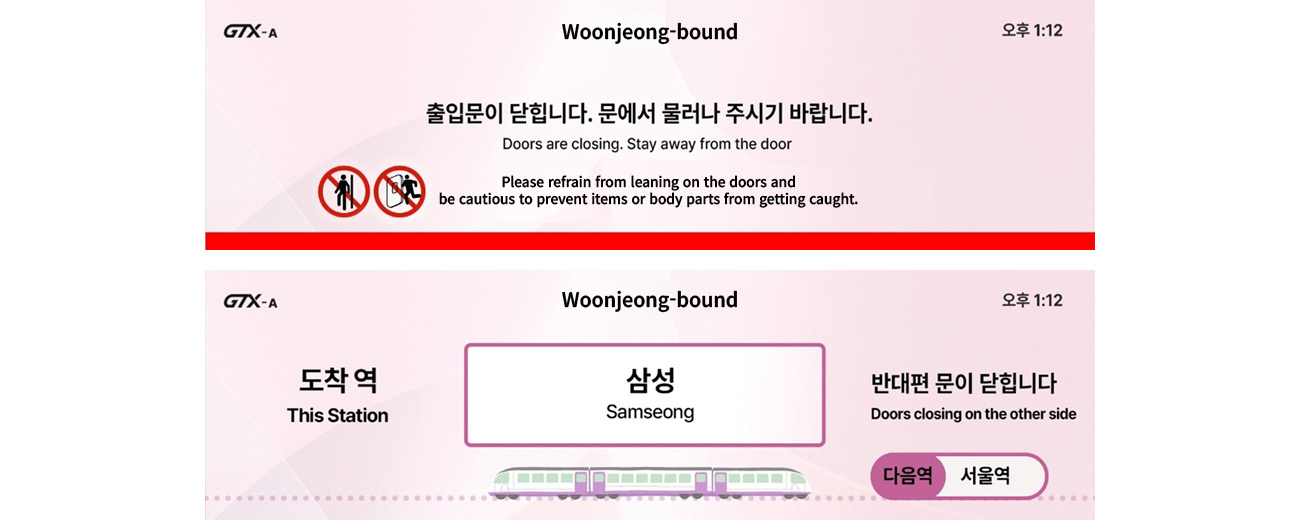
The display at the door-closing direction (top) broadcasts safety messages such as “Doors are closing. Please step away from the doors.” The opposite display shows door opening/closing announcements, arrival station, and next station information.
Maintenance costs for railway vehicles account for approximately 30% of the total lifecycle costs. Advanced maintenance technologies based on the integrated network and big data platform, as introduced earlier, are at the heart of the GTX service leading the transportation revolution in the capital region. In particular, state-of-the-art maintenance technology is a core competency in the field of innovative railway services, alongside autonomous driving-based signaling systems, on which Hyundai Rotem is focusing. Hyundai Rotem plans to continue proactive research and development in various railway industry sectors to achieve its vision of “enhancing global technological competitiveness through securing future-leading technologies.”