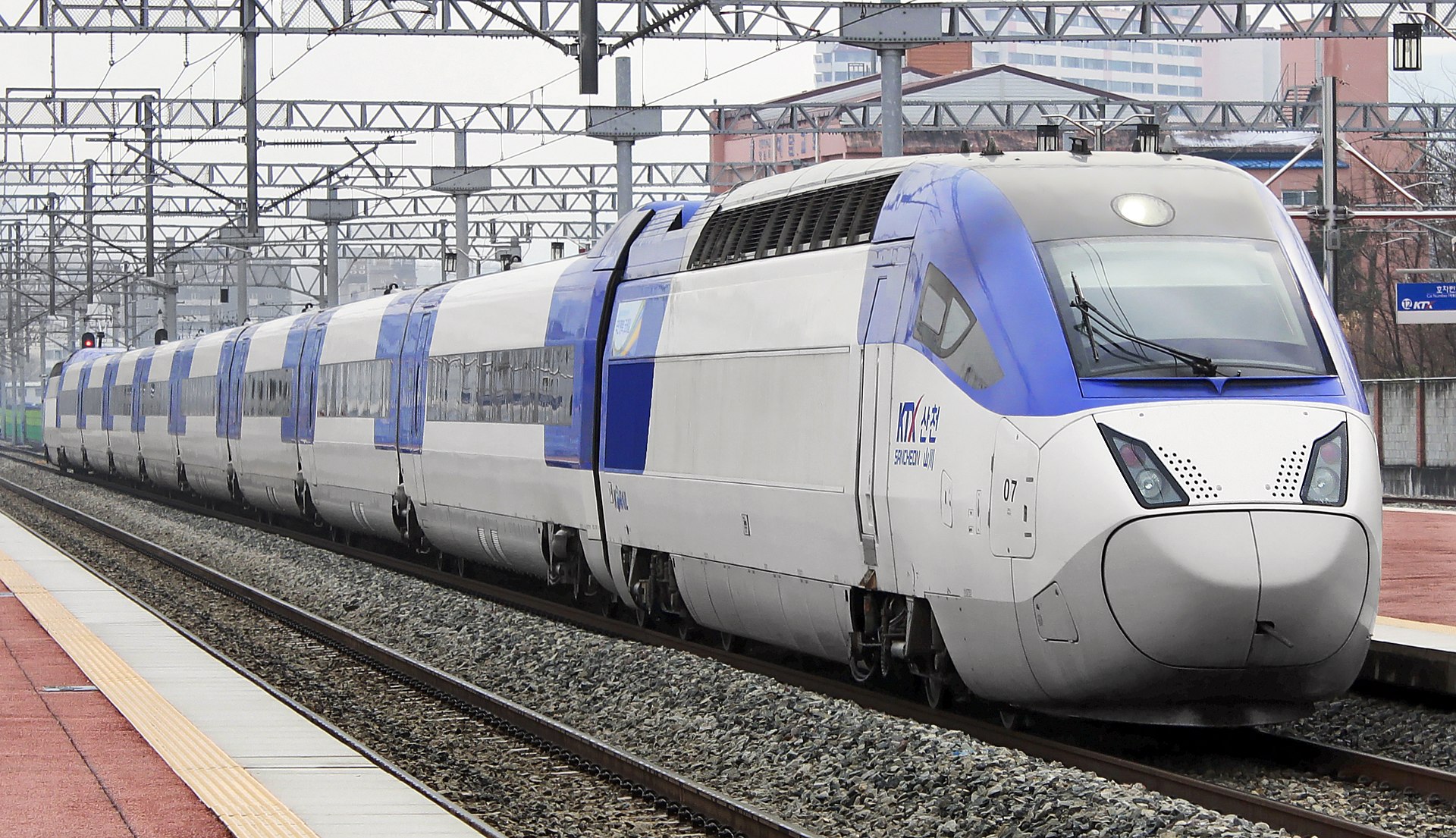
Railway vehicles, with the highest passenger capacity on land, transporting a large number of people, demand higher safety standards than any other transportation mode. Due to its unique feature of having to adhere to railroad safety laws, regulations, and standards, as well as the inherent safety of designated tracks, railway, along with airplane, has the one of the lowest accident rates.
Crash and Safety Design Standards for Domestic Railway Vehicles
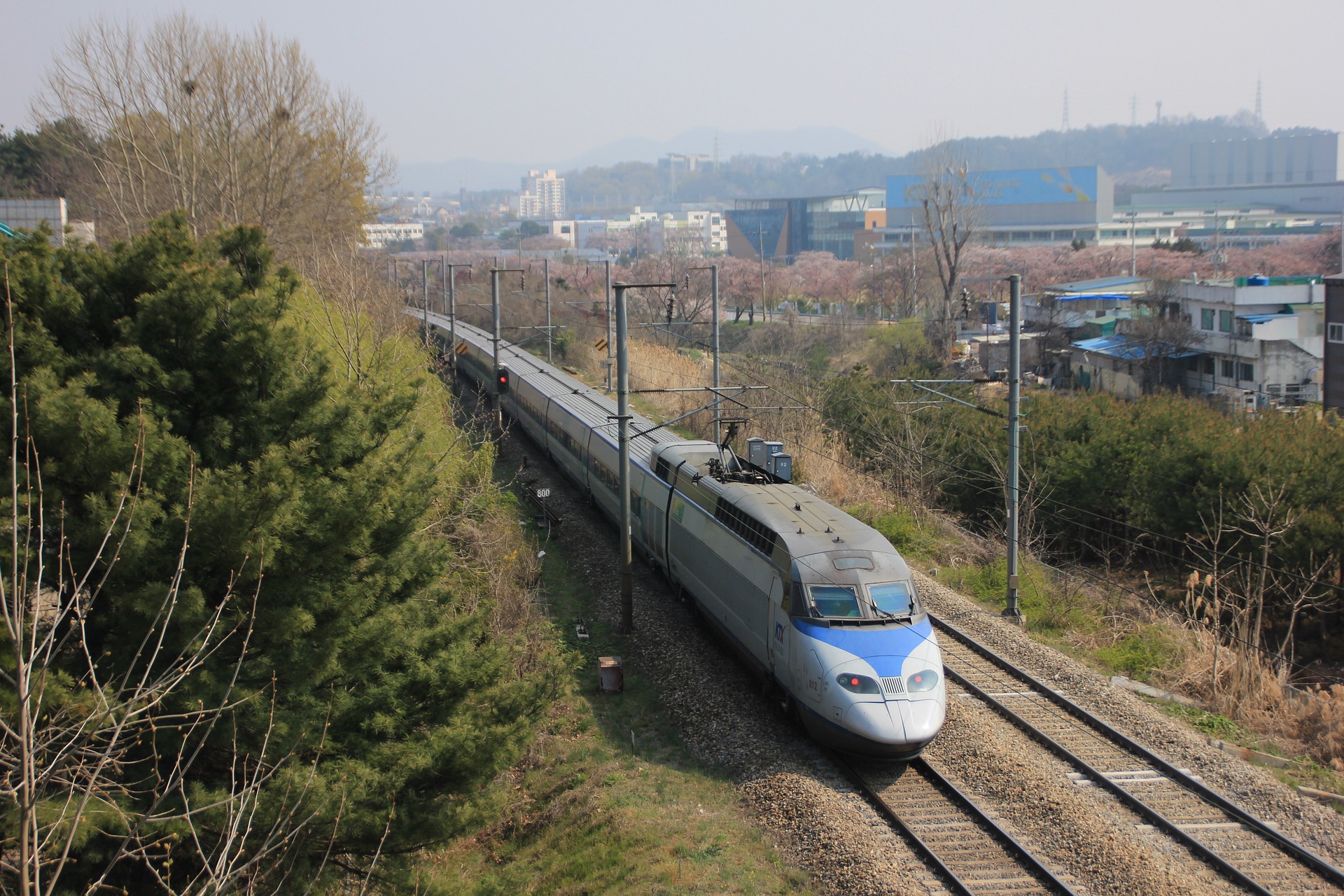
Crash and safety design standards for domestic railway vehicle gained prominence with the introduction of KTX, which acted as a catalyst for interest in crash safety design for domestic railway vehicles. The need for enhanced safety measures became apparent due to the rising incidence of railway fires and derailments caused by increased train speeds. Consequently, the Railroad Safety Act was introduced to systematically address this need. The Railroad Safety Act’s standards require to the installation of energy-absorbing structures at the front and rear of trains to mitigate collision energy in accidents.
Outlined in the railway vehicle technical standards by the ministry of land, infrastructure, and transport, the criteria for crash and safety design are as follows:
1) Railway vehicle shall be designed to meet the following specific criteria to minimize the effects of collisions.
(1) the deformation of the part where the engineer and passengers are located, the phenomenon of climbing between railway vehicle, and the derailment should be minimized.
(2) minimize the intrusion of the railway vehicle’s body structure into passenger areas
(3) Locomotives, motor cars and passenger coaches (including motorized passenger car), and trailer cars (including control trailer cars) used on high-speed trains should disperse and absorb collision energy to minimize injuries to passengers and crew members
(4) In the event of a collision that exceeds the allowable load limits of connecting devices, the vehicle body should be designed or mounted with an additional energy absorber to minimize injury to passengers and crew members
2) Manufacturers must assess whether high-speed trains comply with the standard prescribed in previous paragraph in accordance with the Standardized Crash Memorandum.
In order to meet the safety standard specified above, manufacturers began to employ connector energy absorption structures, hydraulic side buffers, and collision absorption structures in lead cars. Additionally, employing diverse materials and thicknesses at both ends of the cabin body ensures collision energy is not transmitted to the cabin first. It leads to collision displacement and allows the collision energy to be absorbed sequentially.
Crash and Safety Technology to Secure Maximum Safety in Accidents
In the realm of train operations, various types of accident can occur. Since safe design, based on the following accident scenarios, can reduce the accident rate, it is crucial to predict and analyze potential accident scenarios during the design process.
Head-on Collision
This is a situation where two trains crash into each other frontally, and can cause the most serious consequences among train collisions. This type of accident poses one of the gravest threats to passenger safety. Addressing this scenario requires proactive countermeasures to minimize severe consequences.
Different Type Vehicle Collisions
This is a situation where two different types of train are operating together and can result in accidents due to factors such as control errors. Analyzing the collision safety of each coach in mixed operations is essential to formulating effective safety measures.
Large Obstacle Collisions
This is a situation where a coach collides with a sizable object such as a truck or trailer at a railroad crossing. It can cause great danger to the driver of the other vehicle, as well as damage to and derailment of the train.
Small Obstacle Collisions
This is a situation where a train unexpectedly crashes into smaller obstacles like wildlife or track obstructions. As this type of accident increases the risk of derailment, safety standards to mandate the mounting of devices to high speed trains to remove or deflect small obstacles are in place, to minimize damage and secondary accidents following such collisions.
A variety of potential accident scenarios is useful in evaluating safety during the design process and devising safety measures. Comprehensive preparation for various accident situations fosters safer operating conditions.
Safety technology in railway vehicle has undergone continuous development to enhance protection against potential accidents. Beyond ensuring passenger safety during crashes, various technologies are under development encompassing accident prevention and avoidance.
Active Safety Technology
Active safety technology aims to prevent accidents before they occur. In the past, only mechanical braking systems were considered active safety devices. However, advancements in technology have introduced systems, which can reduce the danger of accidents.
In the automotive field, Forward Collision Warning (FCW), Forward Avoidance Assist (FCA), and various active safety technologies which link braking and vehicle control systems are applied, and more advanced active safety technologies continue to emerge in preparation for the era of autonomous driving.
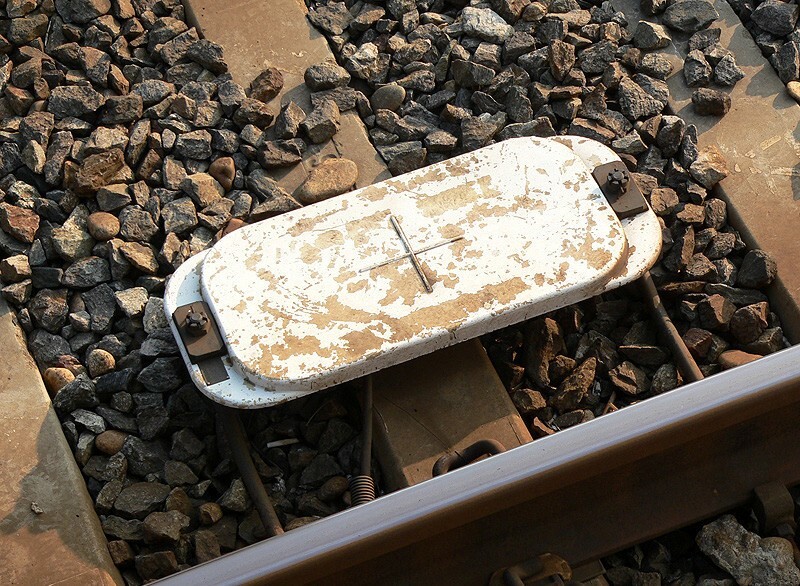
The railway field uses communication systems between vehicles and control centers. With Auto Train Stop (ATS), Automatic Train Control (ATC), and Automatic Train Protection (ATP), which control train speeds physically and electronically to prevent collisions, safety in train operations is enhanced.
Passive Safety Technology
The evolution of passive safety technologies, aimed at reducing vehicle damage and passenger injuries during accidents, is an ongoing process. These technologies focus on minimizing the impact transmitted to the body during collisions, ensuring passenger safety in the event of an accident.
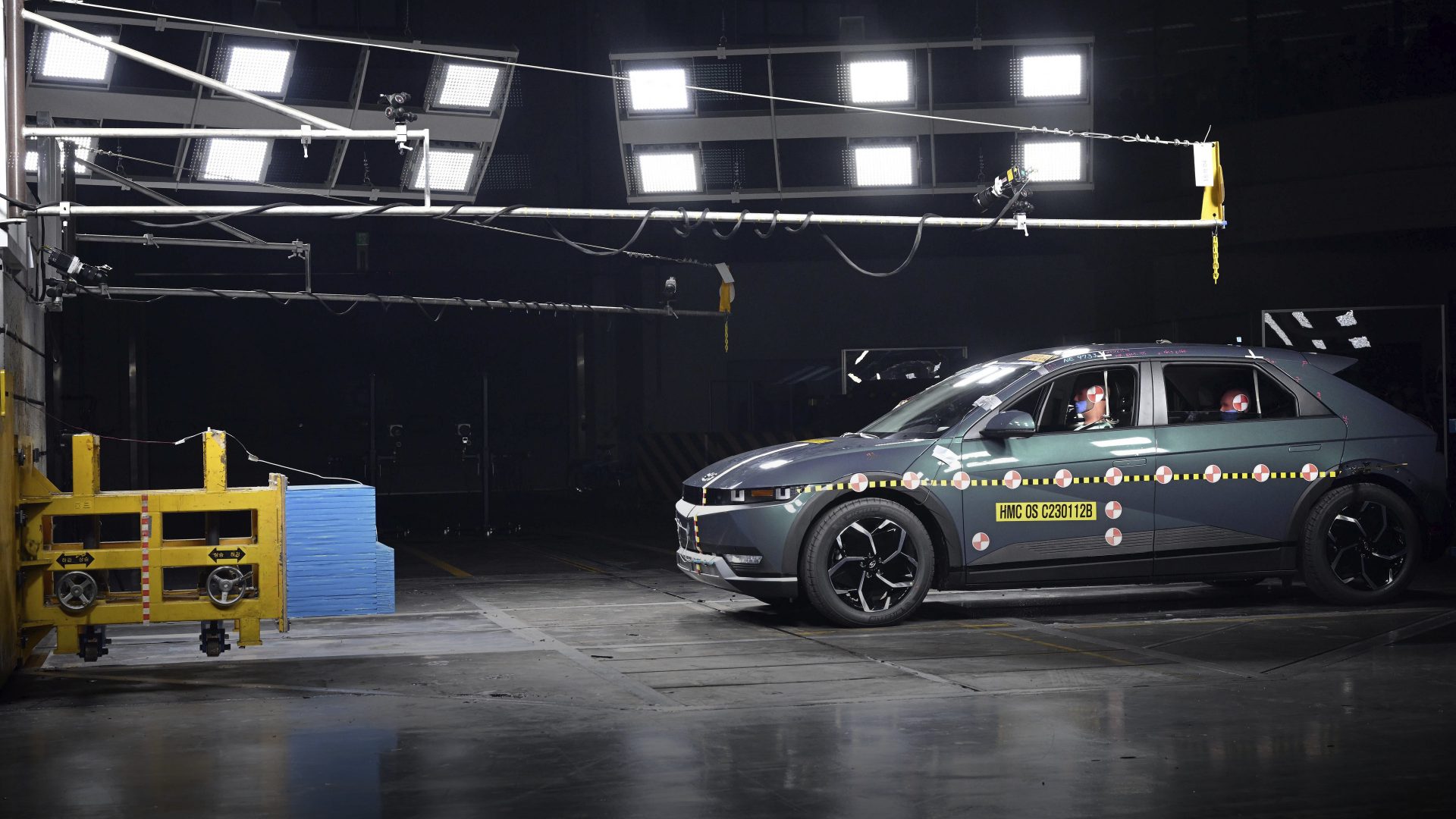
In the automotive industry, a design structure called a ‘crash box’ is employed at the whole car body. This structure absorbs the energy generated during a collision, safeguarding passengers. Additionally, devices like seat belts and airbags that directly protect passengers by mitigating collision impacts are examples of passive safety technology.
However, the application of these technologies in railway vehicles is limited. This is because trains typically have long braking distances and lower collision speeds. Furthermore, the way they are operated position differs significantly from that of automobiles, making the direct application of technologies like airbags impractical. Seat belts, while potentially reducing passenger injuries, pose challenges to rapid evacuation during emergency situations such as vehicle damage or fire. To address these limitations, the railway vehicle sector has introduced the concept of Crash Energy Management (CEM). CEM involves incorporating specific design principles into the body structure to minimize accident damage and enhance safety.
Crash Energy Management to Minimize Damage
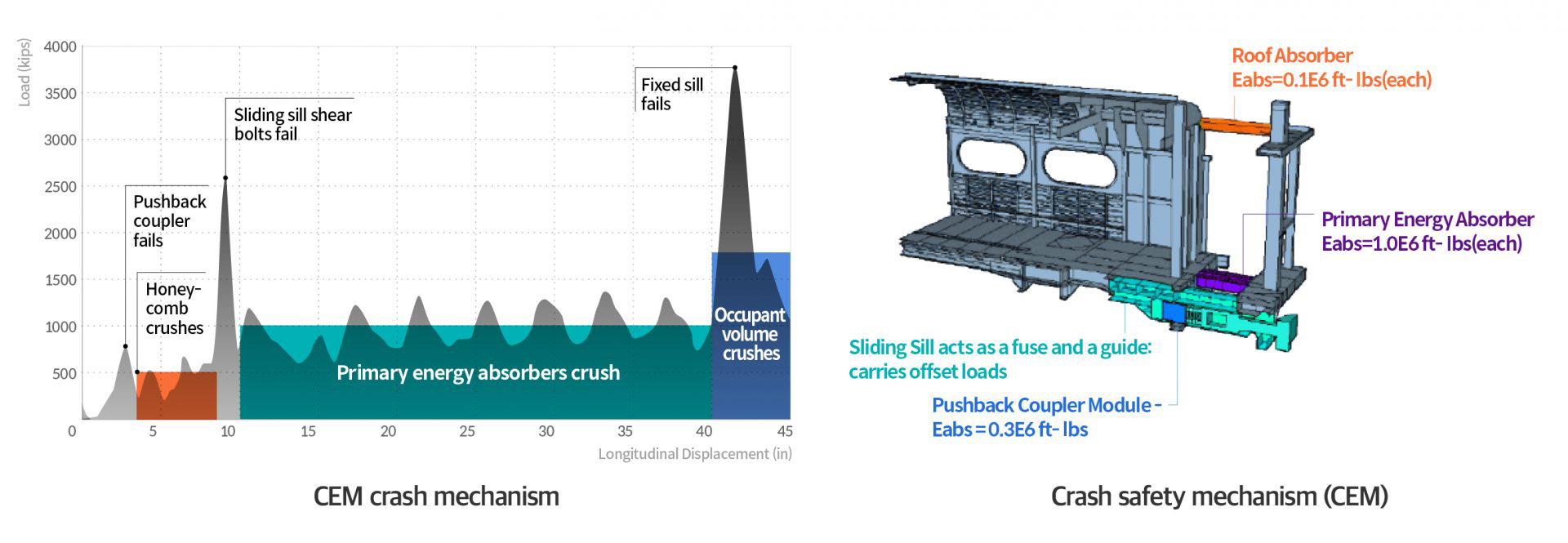
Crash Energy Management System (CEM), which is the core of passive safety technology in the field of trains, is a technology that reduces the energy generated during train collisions as a risk factor. By optimizing the vehicle’s structure to effectively absorb and disperse collision energy, CEM minimizes collision damage, ensuring the safety of passengers and crew members. This works by incorporating ‘energy absorbing structures’ at the front and rear sections of the vehicle, designed specifically to absorb collision energy in case of an accident. Moreover, “vehicle weight reduction,” achieved by incorporating lightweight materials into the vehicle structure, aiming at reducing the energy generated during a collision, is also a factor considered in collision safety design.
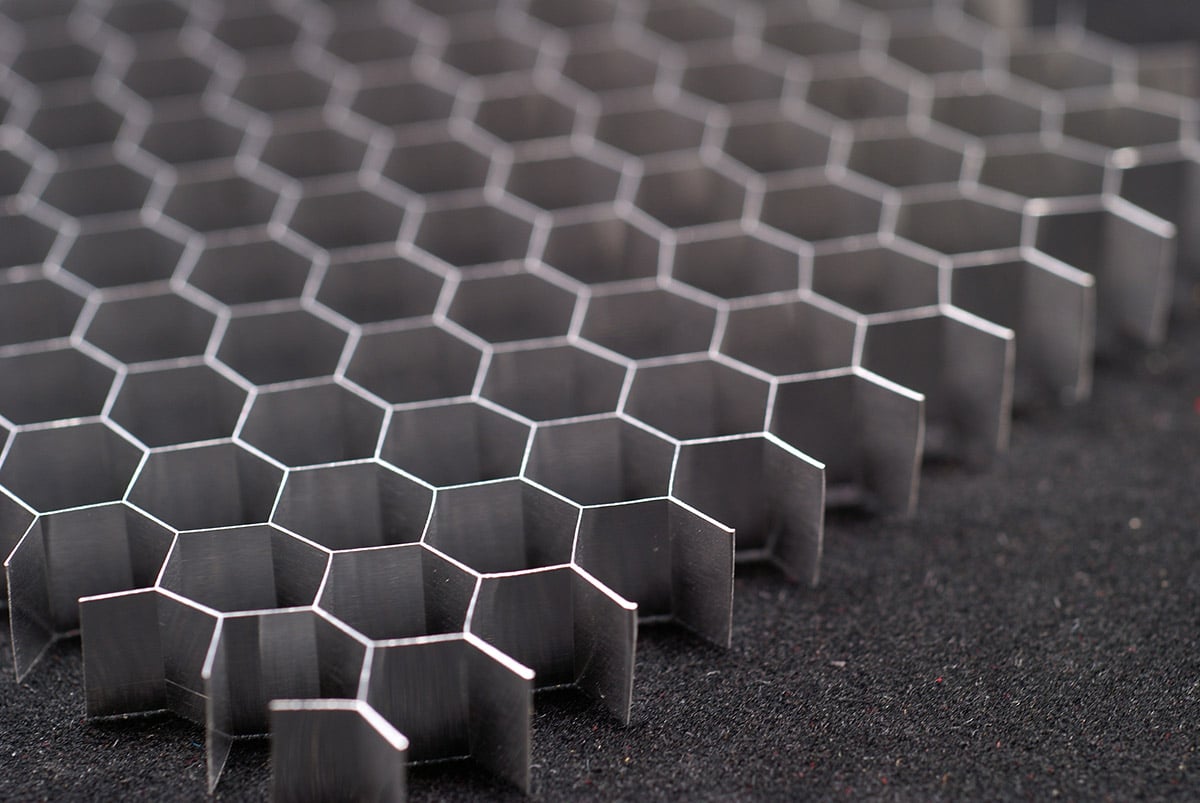
Practical applications of CEM can be found in five main areas. Buffers, positioned at the front and rear of the train, function as shock absorbers; Front Couplers that stabilize the connection between cars, prevent separation during collisions and minimize energy transfer impact; Structural Deformation behind the Coupler/Buffers, featuring a high-strength hexagonal structure, facilitates efficient energy absorption in the event of a collision; Front Honeycomb Structure that applied with a high-strength hexagonal structure to the front of the train to efficiently absorb the energy generated in a collision; and the Body Structure involving specific design elements and material composition to disperse impact and thereby safeguard passengers during accidents. These features collectively enhance safety in collision scenarios.
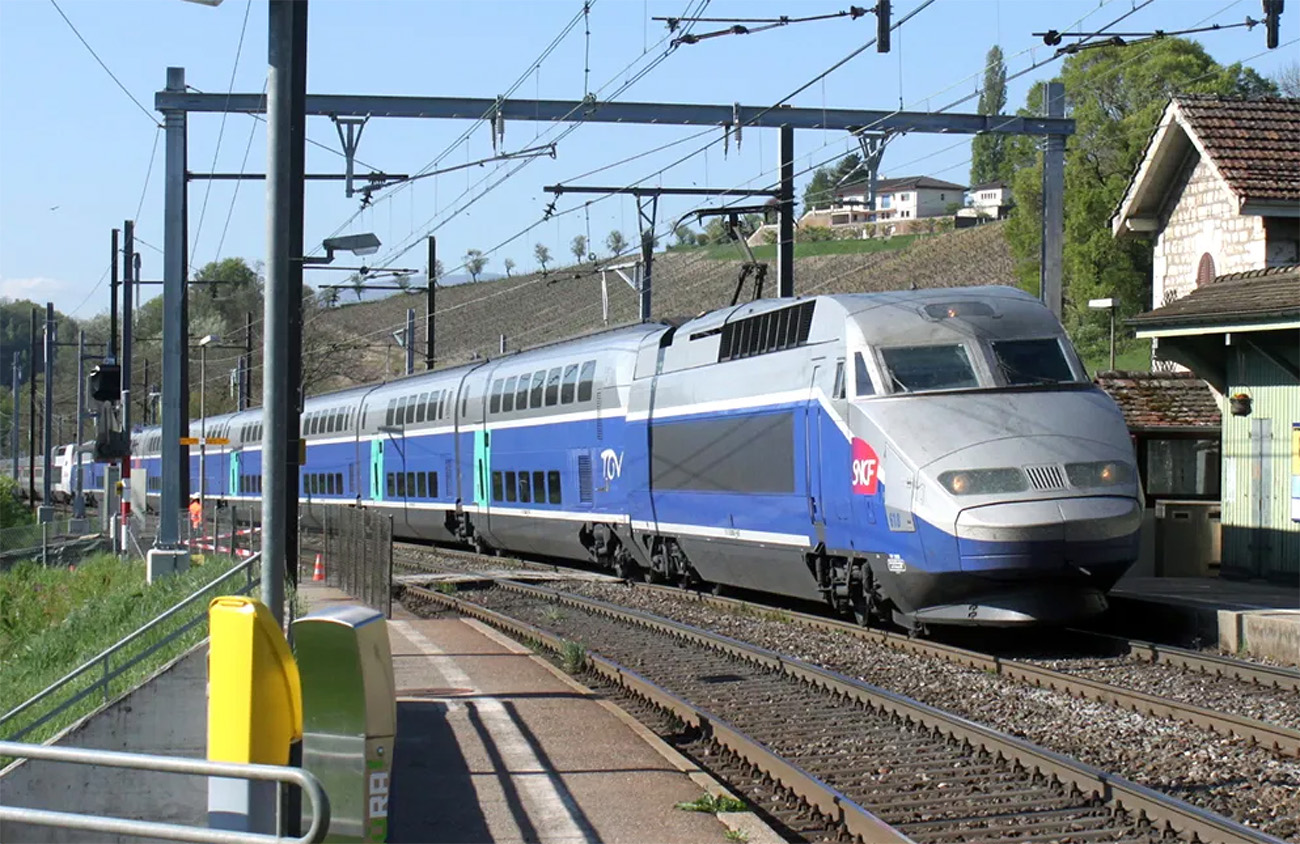
The French TGV-Duplex high-speed train model exemplifies the application of systematic crash safety design based on international standards. This model utilizes a “crash zone” designed by applying different stiffnesses to various parts of the vehicle. The passenger compartment is strengthened while the sub-compartment is intentionally weakened to create a dedicated crash zone. Such crash zones should be considered to achieve enhanced crash durability. The fundamental principle in vehicle development involves strengthening the passenger area while weakening the crash zone.
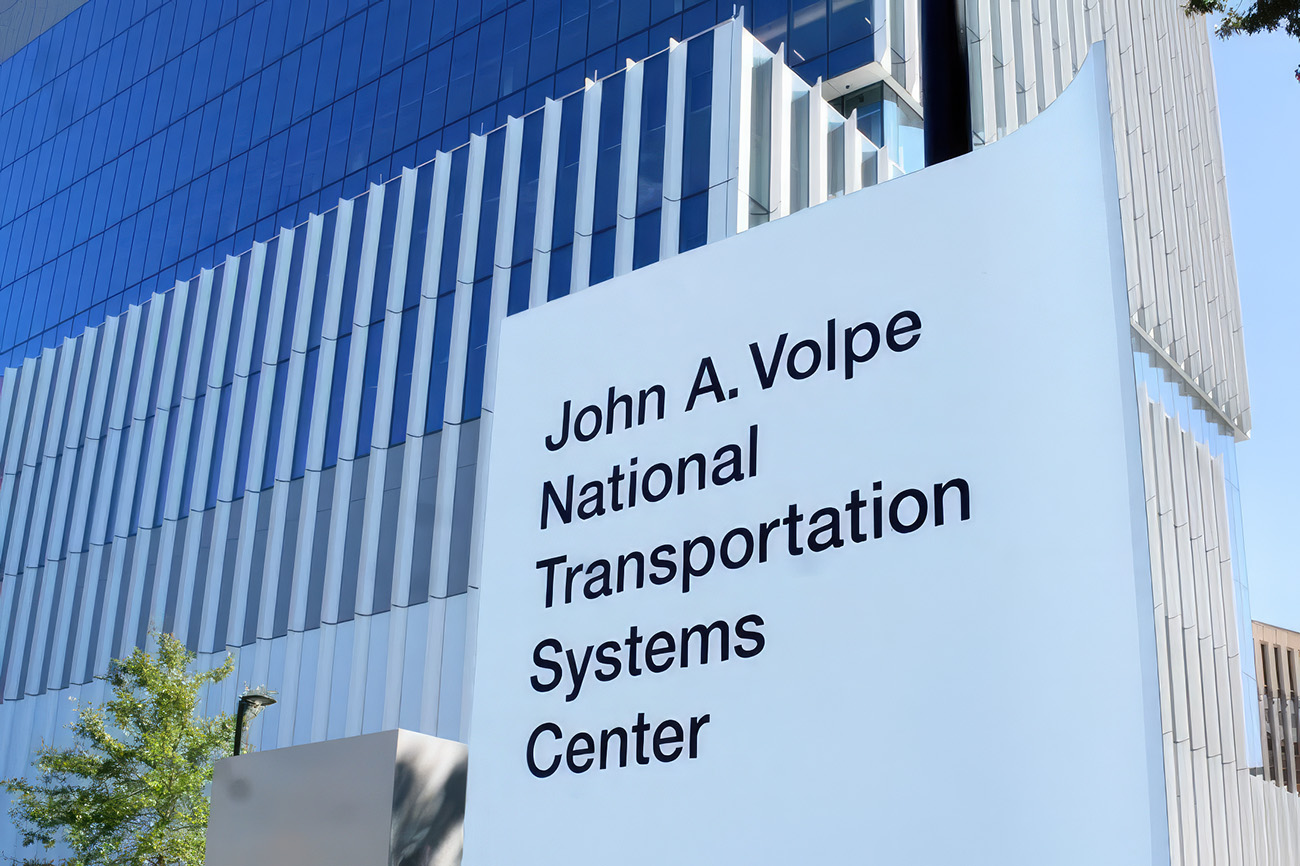
Significant research on crash energy management is underway. In the United States, the Volpe Laboratory, part of the Department of Transportation (DOT), is actively engaged in researching design, analysis, and evaluation techniques for collision of railway vehicle. Notably, efforts have been made to raise crashworthiness standards significantly, with the compressive strength standard being increased to 350 tons, surpassing the UIC (Union International des Chemins de fer) standard of 200 tons. Also, it raised all other crash and safety standards for railway vehicle, establishing an independent standard for crash and safety in relation to all railway vehicles operated in the United State.
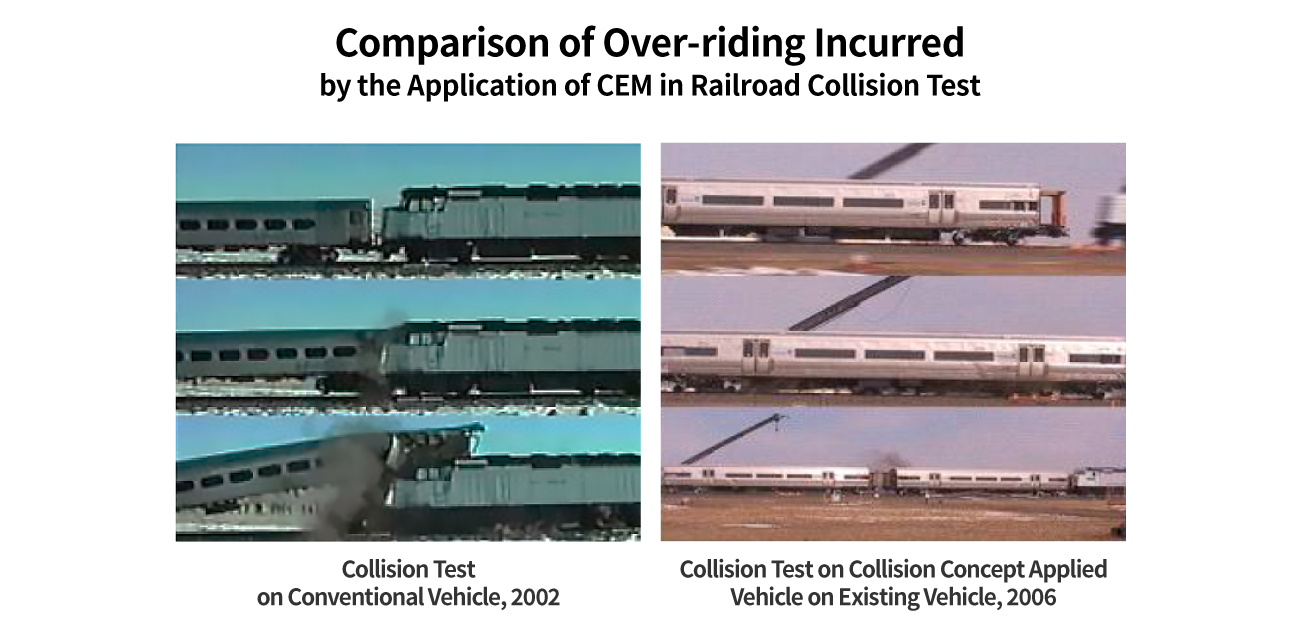
In particular, in 2006, the Volpe Institute conducted a crash test involving CEM-equipped and conventional vehicles, affirming the utility and necessity of CEM. This test was conducted with an actual vehicle and featured a five-car train, which consisted of a stationary cargo, a passenger coach, and locomotives. By making the train crash at a speed of 30 mph(48 km/h), the test showcased the significant safety advantages of CEM-equipped vehicles over their conventional counterparts.
Notably, the anti-climbing device, a component of CEM, proved its ability to minimize damage during collisions. In accidents where two trains crash into each other, a lighter vehicle climbs on top of a heavier one, thereby reducing passenger risk by more than 30 times.
Safety of CEM by Hyundai Rotem has been proved in actual accidents
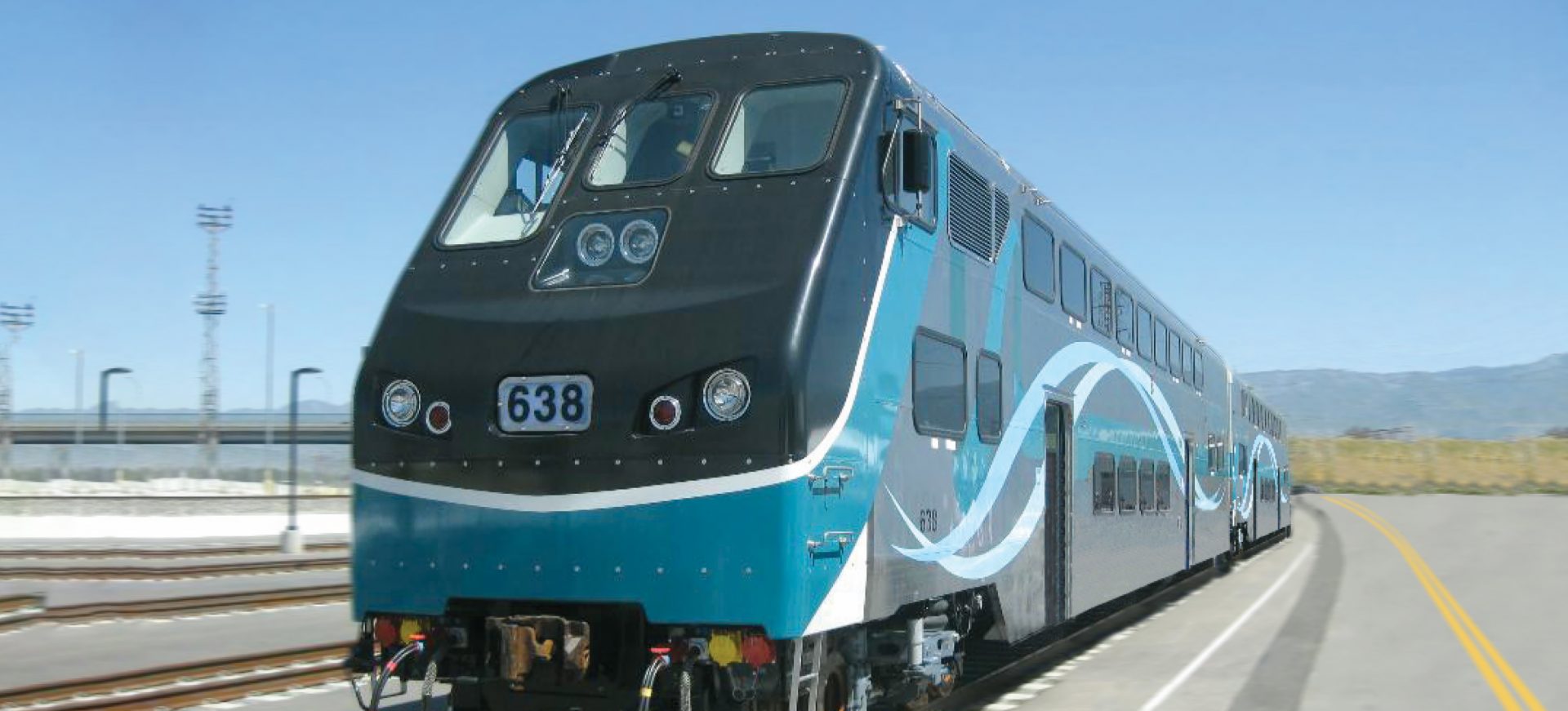
Hyundai Rotem’s application of CEM technology in railway vehicle has made a substantial impact both domestically and internationally. In particular, its safety has been proved during an accident that occurred in North America.
CEM Application Case
A two-story railway vehicle delivered by Hyundai Rotem to Metrolink, California in 2013 was involved in a collision with a large truck near Lancaster Station, California. While the front of the vehicle sustained significant damage, no casualties were reported thanks to the CEM. Significantly, this was the first vehicle equipped with the CEM after Metrolink, the operator, implemented enhanced safety standards. Despite carrying 190 passengers across three second-floor cars, almost none sustained injuries.
Hyundai Rotem focuses on providing safe driving conditions to prevent collision by developing high-tech signals and control technologies and enhancing crash safety to minimize the impact of crash energy in collisions by implementing CEM, which effectively absorbs and disperses crash energy.
The company is solidifying its position as the safest railway vehicle manufacturer in and out of the country, demonstrating its capability to design the safest railway vehicles, not just in virtual scenarios, but also in real-world accidents, through various research and development with priority on passenger safety.