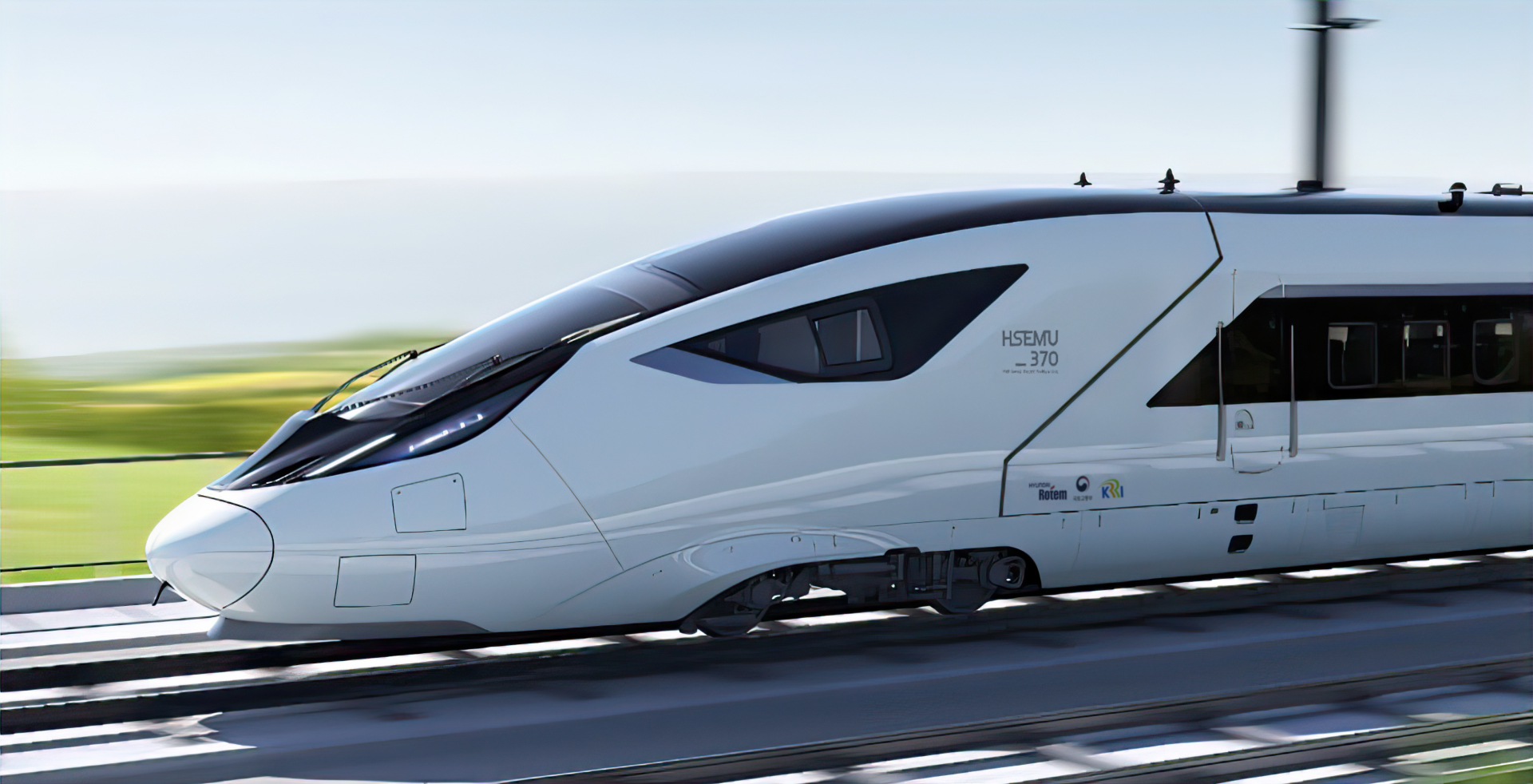

In preparation for the end of the service life of the KTX high-speed trains, which were opened in 2004, the Ministry of Land, Infrastructure and Transport has commissioned (with the supervision of the Korea Railroad Research Institute, “KRRI”) the “Development for core technologies and specification to increase the operation speed of the high speed train over 370kph” in which Hyundai Rotem is participating as a co-research organization. This government R&D project aims to develop core technologies and establish evaluation criteria for the next-generation 370 km/h and above high-speed trains. Through this, the plan is to establish standards for key infrastructure elements such as railcars, tracks, and rails—the essential components of high-speed rail. The aim is to define technical criteria applicable to speeds of 350 km/h and above, securing competitiveness for overseas expansion.
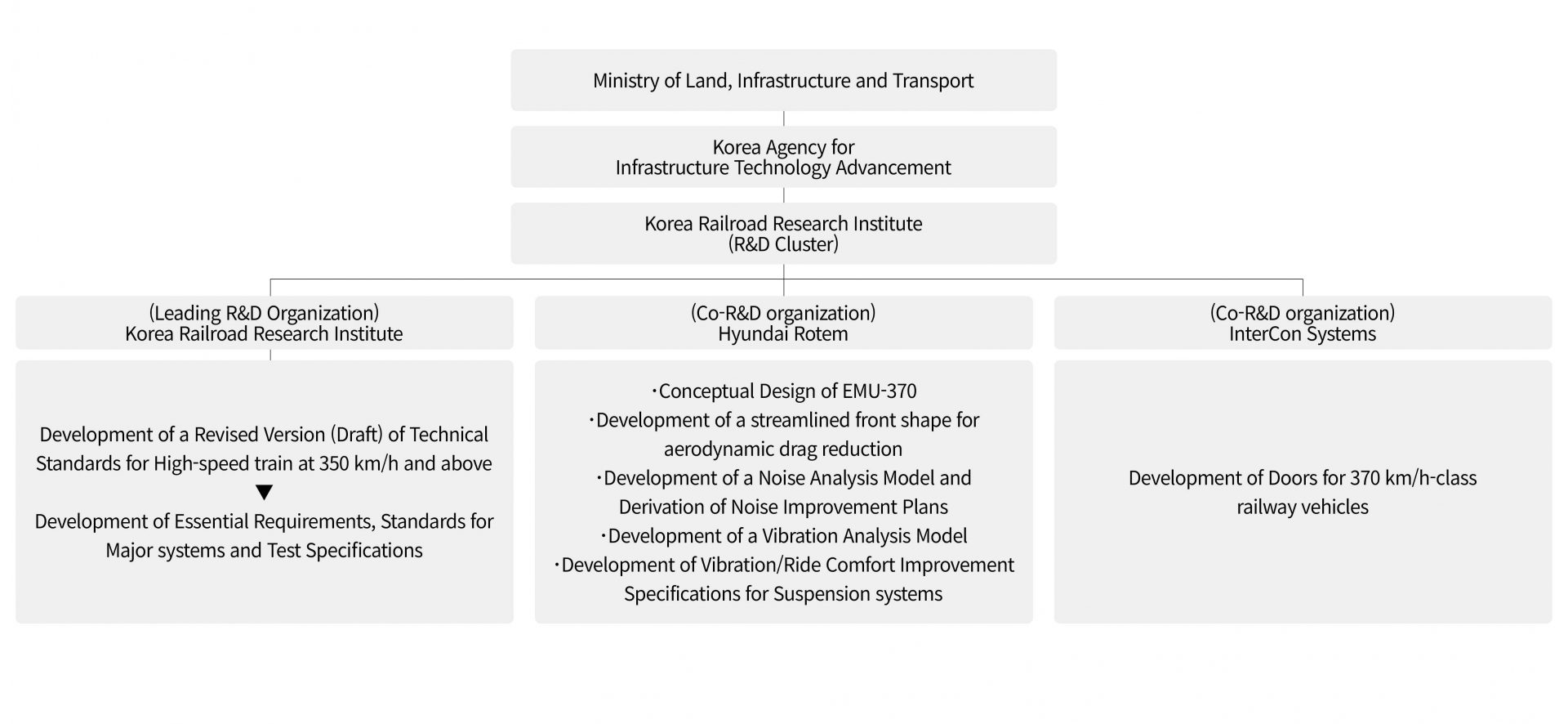
Hyundai Rotem completed the first phase of the task at the end of 2023 as part of a four-year plan from 2022 to 2025 to secure core railcar design technology. Let’s examine the key contents of Hyundai Rotem’s research achievements and the ongoing research and development of core technologies for the commercialization of high-speed rail.
Expected Benefits of Next-generation High-speed Rail Introduction
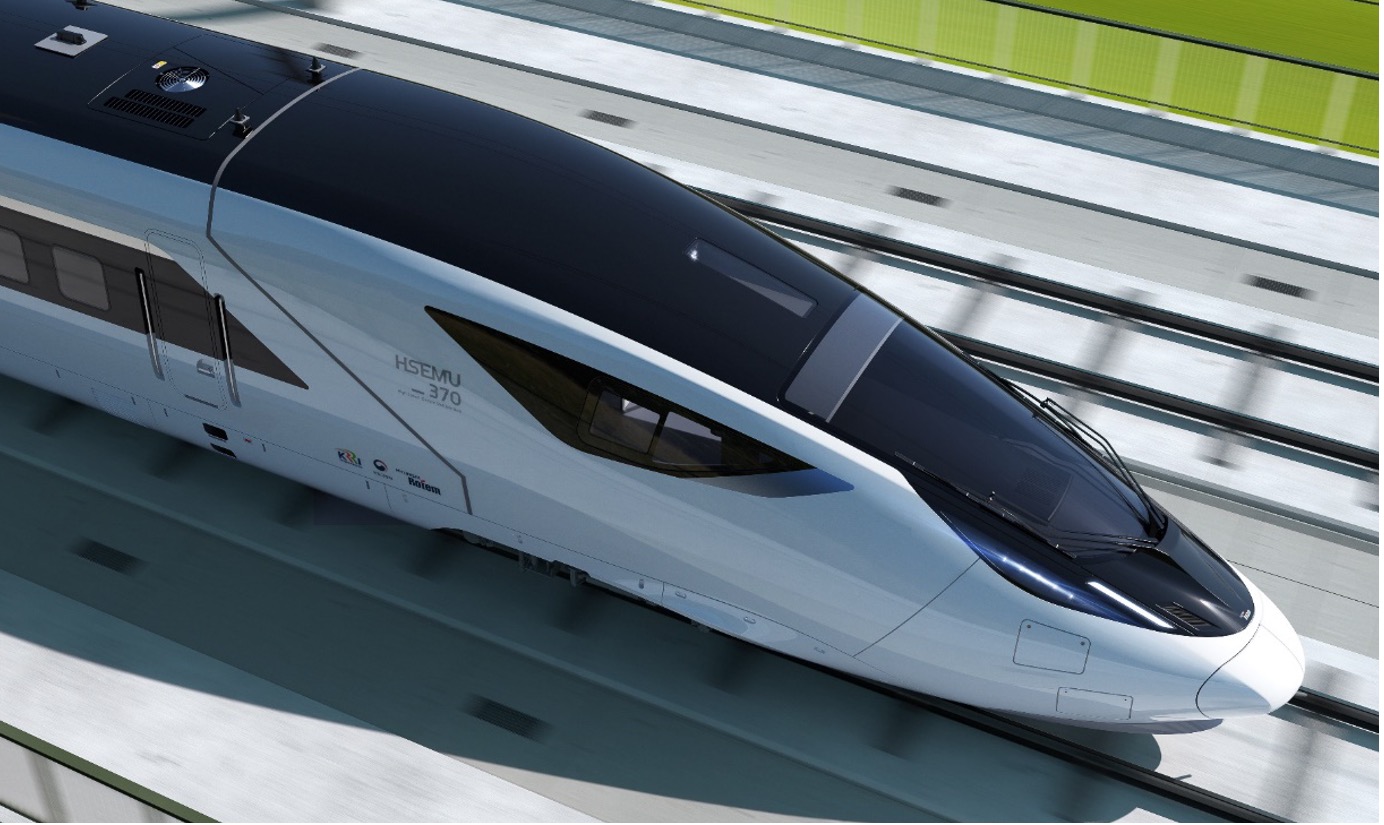
The introduction of new high-speed rail systems can yield significant scientific, technological and socio-economic benefits. From a scientific and technological perspective, securing technology related to high-speed trains with speeds exceeding 370 km/h allows for the possession of world-class high-speed rail technology. Moreover, the technical standards for high-speed rail above 350 km/h have not yet been established or declared internationally, creating an expectation that Hyundai Rotem can lead in setting international standards and norms.

In addition, with the introduction of high-speed trains capable of 370 km/h, it will be possible to achieve travel times of around 1 hour and 50 minutes from Seoul to Busan and around 1 hour and 10 minutes from Seoul to Gwangju. This reduction in travel time will enable the practical achievement of a nationwide integrated metropolitan area. Anticipated effects include the maximization of regional balanced development through the reduction of inter-city travel times, facilitating the relocation of government agencies, enhancing the competitiveness of innovation cities and more.
Project Overview and Key Goals by Phase
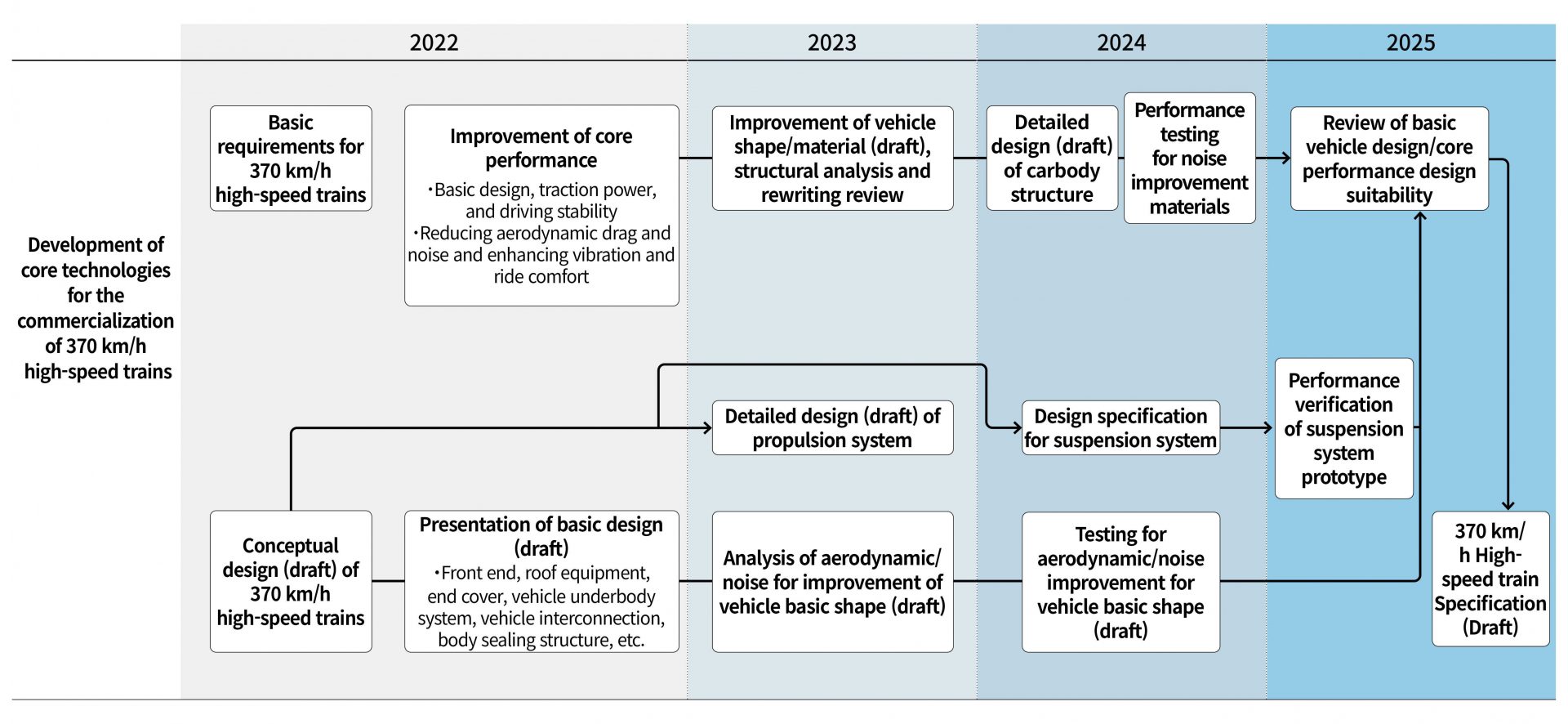
In this project, Hyundai Rotem will secure the core element technologies of the 370 km/h high-speed train (EMU-370) based on the EMU-320, including the conceptual design of the vehicle and safety verification due to acceleration for the commercialization of the EMU-370. Additionally, Hyundai Rotem will support the establishment of new technical standards, considering the 370 km/h high-speed operation environment conducted by the KRRI, contributing to the innovation and safety enhancement of the high-speed railway system.
Over a total of four years, Hyundai Rotem plans to derive the conceptual design of the high-speed train and the main core performance design. At the current second year, the analysis and review of safety performance-related items of the high-speed train have been completed. The interpretation and prediction of performance characteristics related to the operation of the high-speed train (braking performance, running resistance, vibration/ride comfort, noise, aerodynamic characteristics, pressure changes inside the passenger car) have been carried out. Based on these results, from the third to the fourth year, the final outcomes will include “Conceptual Design of EMU-370” “Basic Specification of High-speed train” and “Review of Core Performance Formal Approval Design.”
This aims to achieve the final results of the first-stage research and development conducted by Hyundai Rotem, focusing on the research and development outcome with the highest focus in the areas of traction power, driving stability, running resistance, vibration/ride comfort and noise reduction inside the passenger car.
Research on Running Resistance and Aerodynamic Noise Reduction

The noise generated during the stop of the railcar is influenced by the noise and vibration of equipment such as HVAC (heating, ventilating, air-conditioning), air compressors and various cooling fans. During high-speed operation, the main sources of noise are wheel-rail contact, aerodynamic noise due to air irregularities at speeds over 200 km/h, and noise and vibration caused by the driving system (traction motor and driving gear).
Unlike conventional rail vehicles where noise from wheel-rail contact predominates, high-speed trains prioritize minimizing aerodynamic noise caused by irregular airflow on the railway vehicles surface at speeds exceeding 200 km/h. Therefore, research is conducted to optimize the design for minimizing aerodynamic noise based on an aerodynamic resistance reduction model through analysis and testing.
For EMU-370, aerodynamic resistance reduction and minimizing aerodynamic noise due to acceleration compared to EMU-320 are crucial in vehicle design. To achieve this, the design optimizes the frontal shape, embeds HVAC, modifies the AC mode box structure to minimize the roof protrusion, and improves the airflow around the vehicle by partially applying side covers to the cars in front.
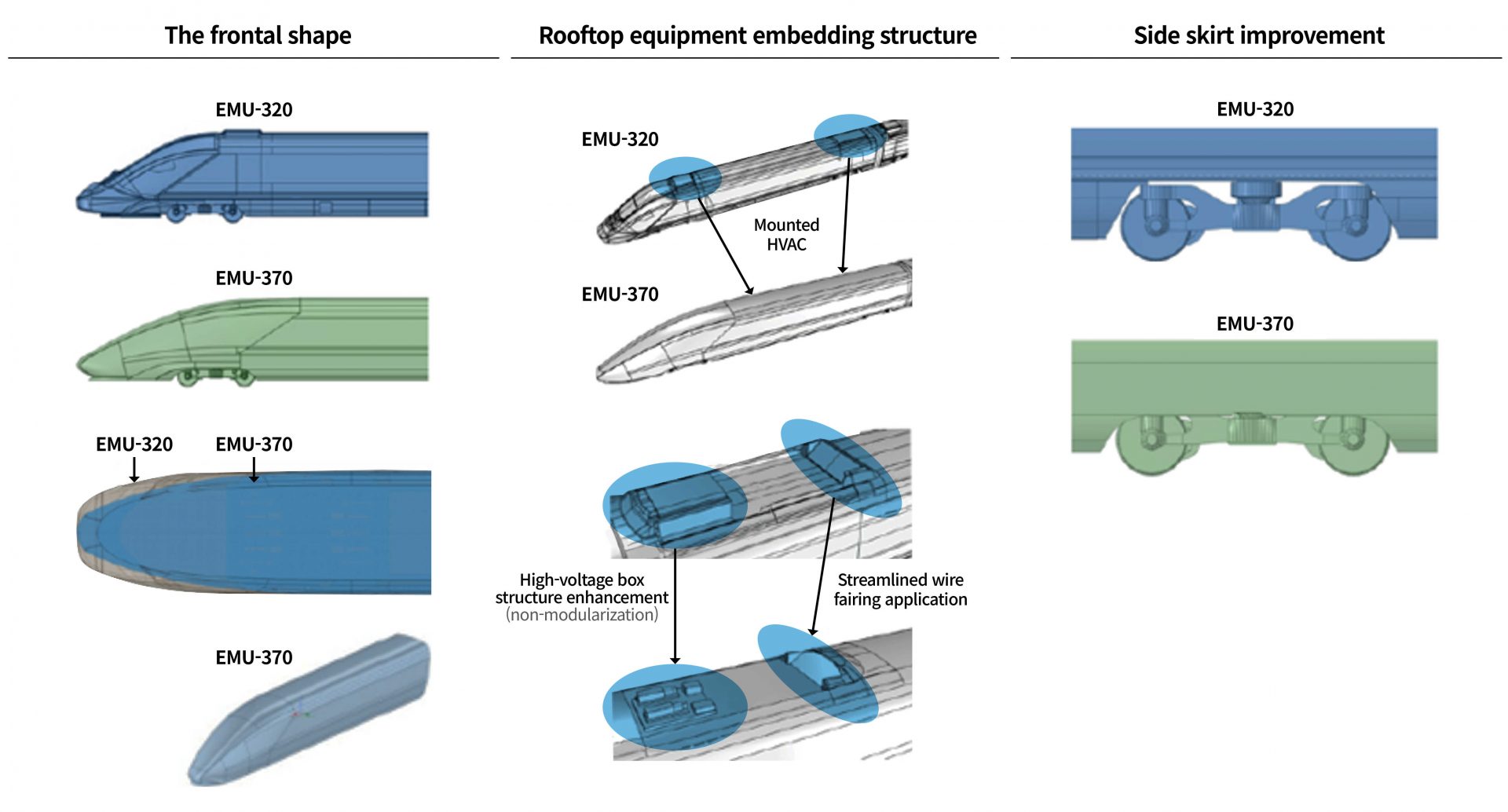
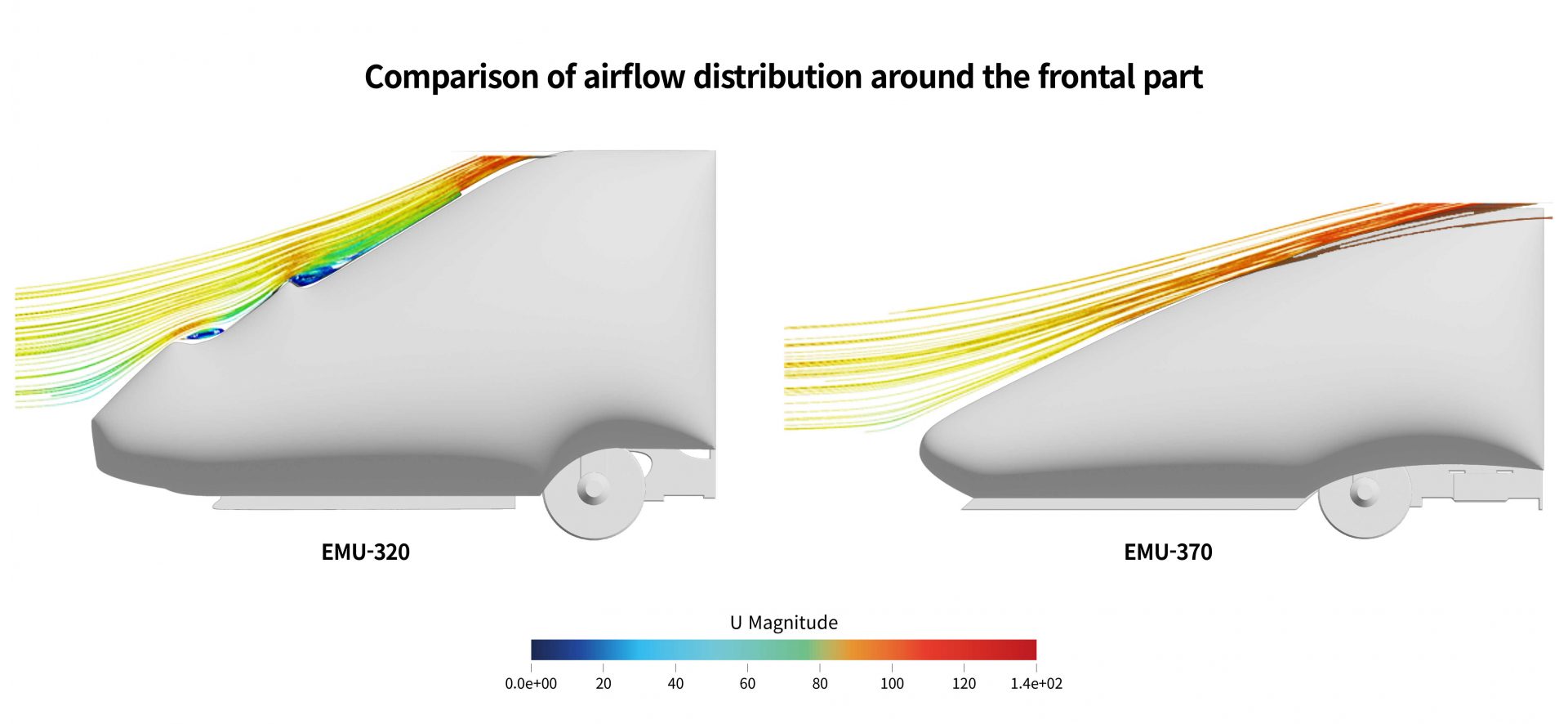

Local pressure changes around the vehicle are the cause of increased aerodynamic resistance and tunnel pressure wave size. It is expected that reducing locally occurring pressure changes through vehicle shape improvements will not only decrease aerodynamic resistance but also minimize the size of tunnel pressure waves.
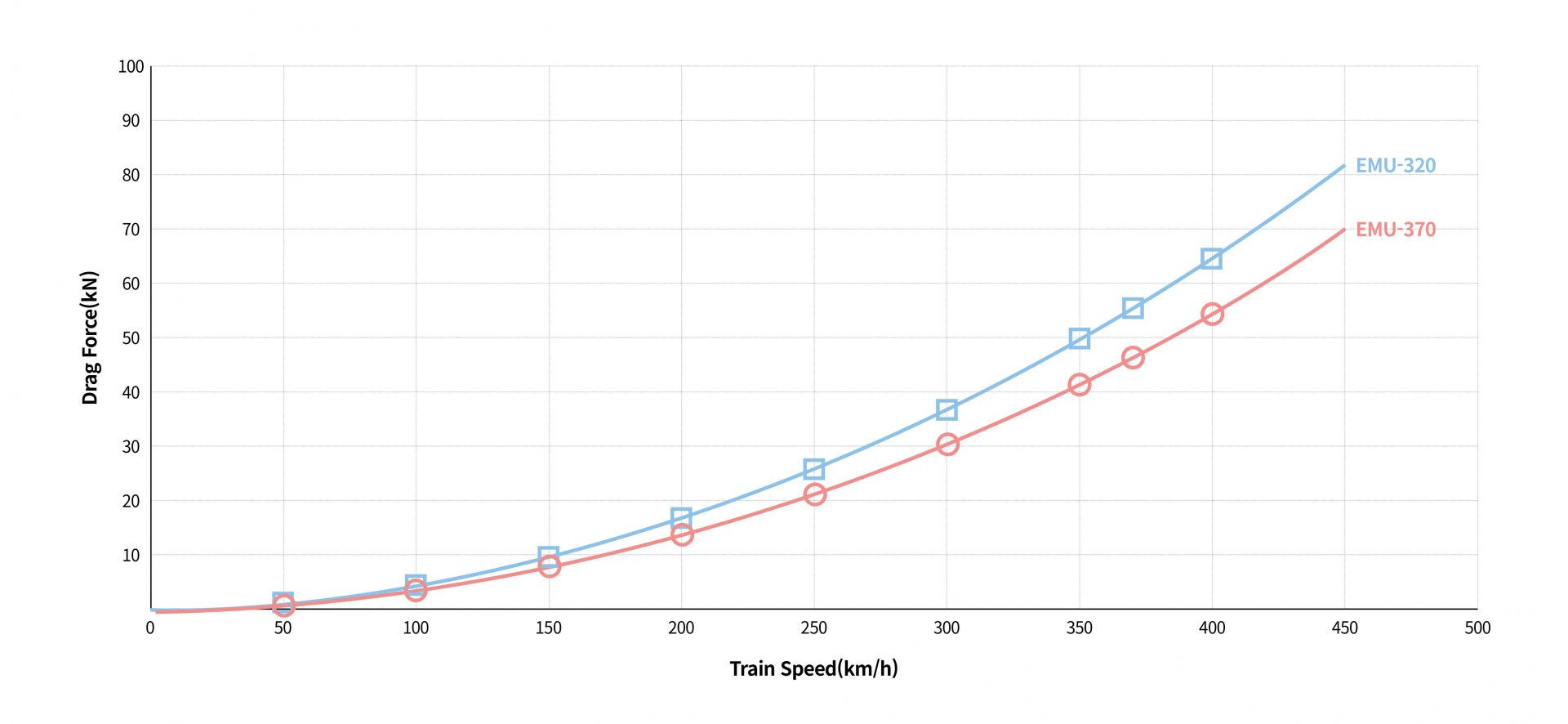
Through the design improvement of the EMU-370 high-speed Railway Vehicles, a 15.1% reduction in aerodynamic resistance compared to the existing EMU-320 at an operating l maximum speed of 370 km/h has been confirmed based on computational fluid dynamics analysis. Based on these analysis results, additional verification will be conducted through reduced-scale testing in 2024. Hyundai Rotem anticipates significant effects on optimizing propulsion system capacity and improving aerodynamic noise through the proposed aerodynamic resistance improvement designs studied by Hyundai Rotem.
Research for Reducing Indoor Noise and Improving Soundproofing
A study was conducted to optimize the cross-sectional profiles of extrusion materials for the vehicle’s floor, ceiling, and side walls to minimize the ingress of noise sources around the vehicle into the interior. Analysis and test results for enhancing low-frequency soundproofing performance confirmed improvement in soundproofing performance through optimization of extrusion materials and skin/rib.
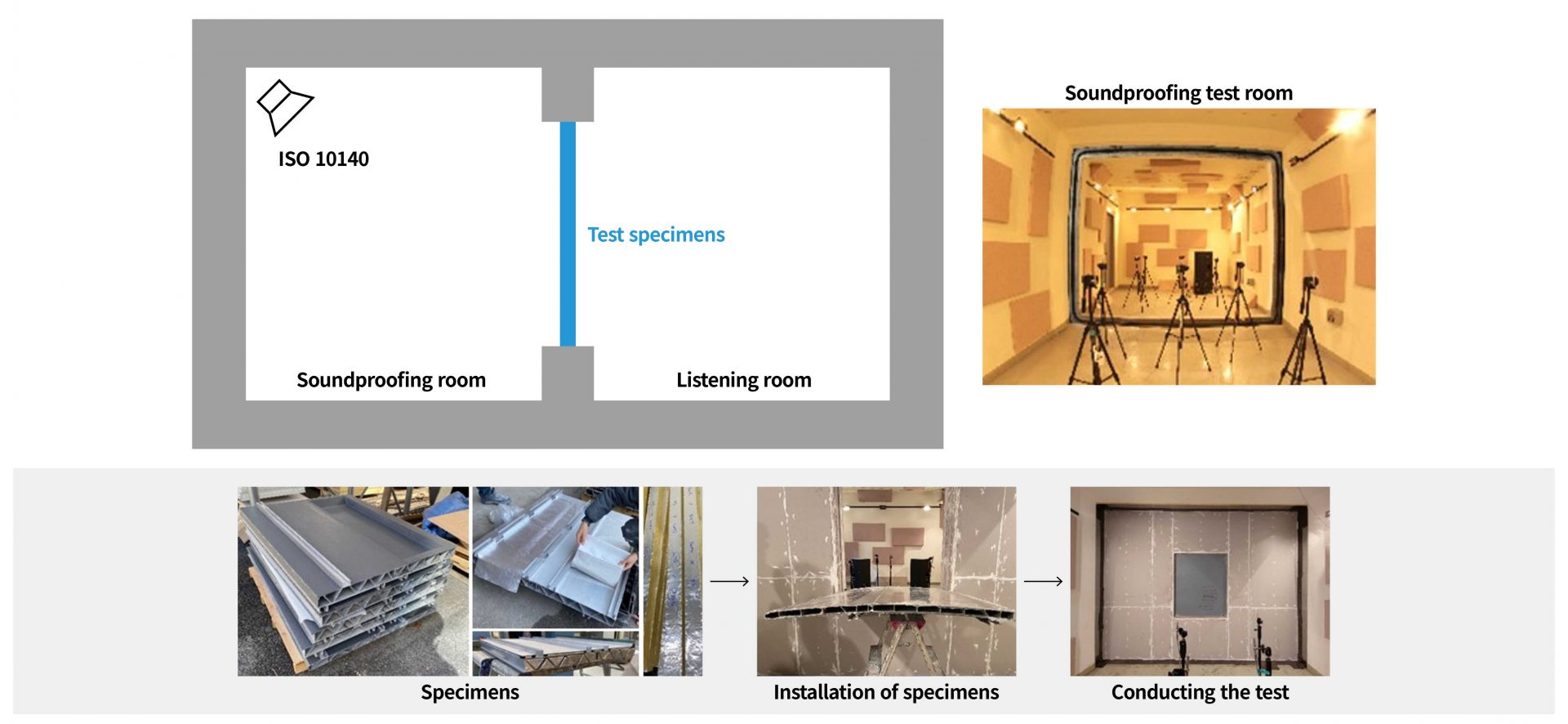
Furthermore, a study on the application of elastic mount technology is included as a key design improvement to reduce structure-borne noise caused by the traction motor. Research on the design elements of elastic mounts to prevent rigid mode resonance of the traction motor in the frequency range of rotating with speeds exceeding 250 km/h has been conducted, providing guidelines for designing the stiffness of elastic mounts to avoid resonance.
Through various design improvements to block and reduce different noise sources, it is expected that passenger convenience will be enhanced even during high-speed travel at 370 km/h.
Development of Frond-end Design for EMU-370
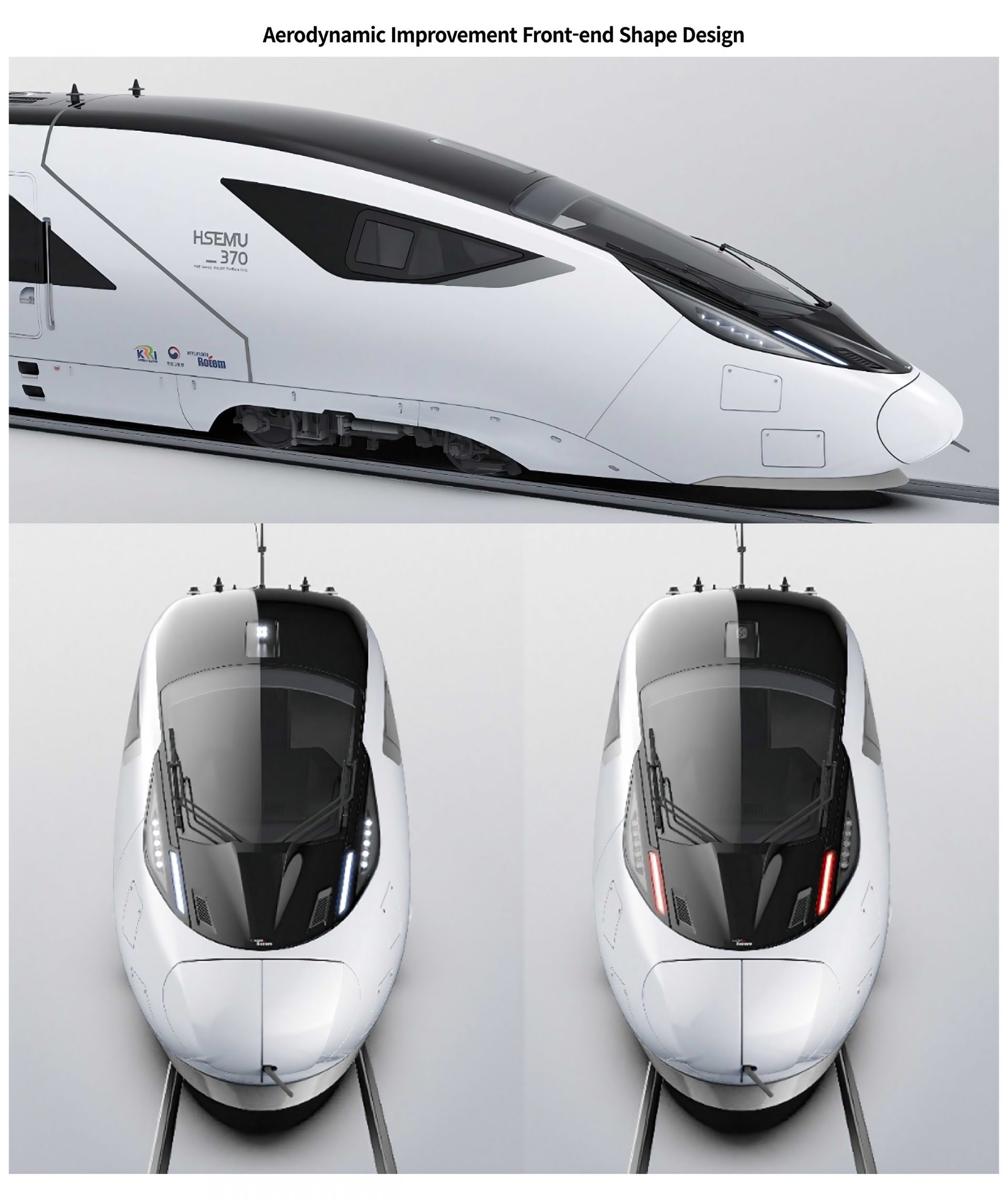
The final design of the EMU-370 front end prioritizes aerodynamic improvements derived from the research process over aesthetic considerations and has been adopted accordingly. Additionally, it has effectively incorporated design features that highlight the vehicle’s dynamic driving performance into the refined geometry design of the high-speed train’s front end.
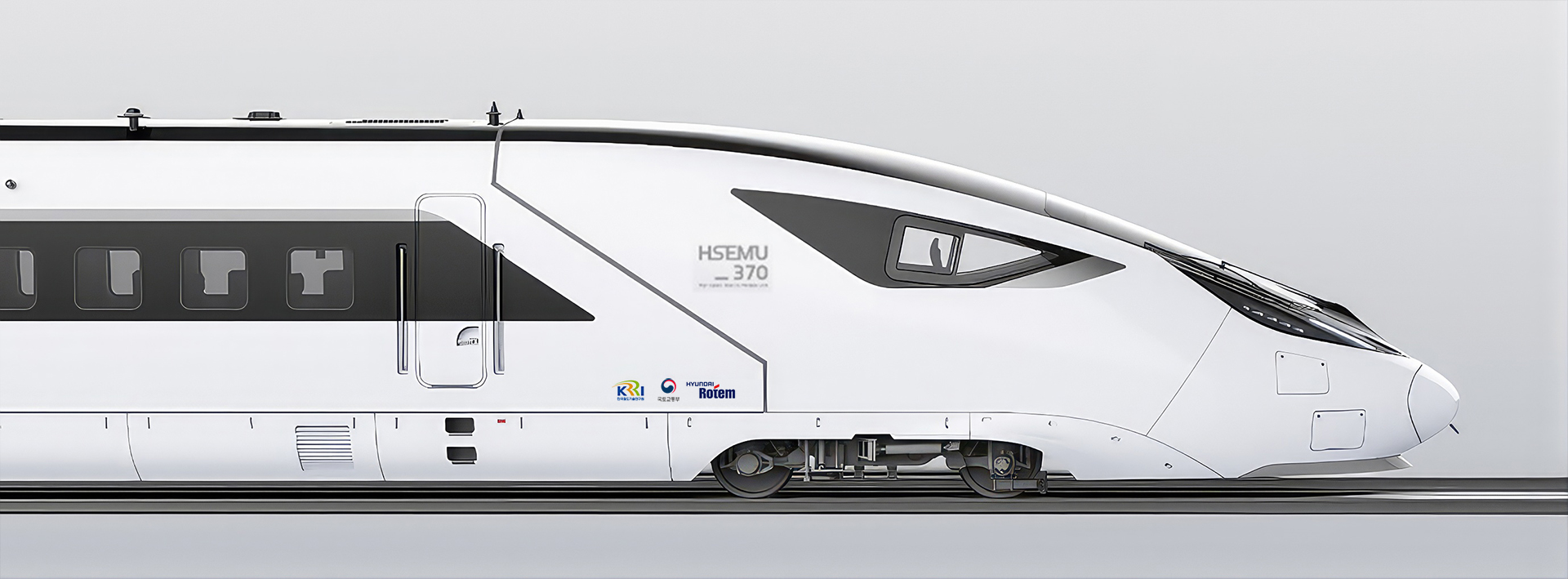
The 370 km/h high-speed train is expected to bring various benefits to South Korea, including increased economic advantages and maximized regional balanced development. Furthermore, it is anticipated to secure world-class technological capabilities and lead relevant international standards. Hyundai Rotem plans to continue its best efforts in the remaining two years to successfully develop the core technology for the 370 km/h high-speed train, paving the way for the mass production of EMU-370 and, ultimately, the overseas expansion of high-speed rail.