“Connecting the Entire Seoul Metropolitan Area within 30 Minutes!” The Origins and Current State of the GTX Project
GTX stands for Great Train Express, officially named the “Metropolitan Area Express Railway.” It is a metropolitan transportation system connecting key points from the outskirts of the Seoul metropolitan area to its downtown. The GTX project, included in the 3rd National Railway Network Construction Plan (2016-2025), officially began with the opening of the GTX-A line on March 30, 2024. Currently, three lines have been confirmed (GTX-A, B, and C). The GTX-A line (Unjeong, Paju – Dongtan, Hwaseong) has commenced operations, with the B line (Songdo, Incheon – Maseok, Gyeonggi) and C line (Yangju, Gyeonggi – Suwon, Gyeonggi) scheduled to open.
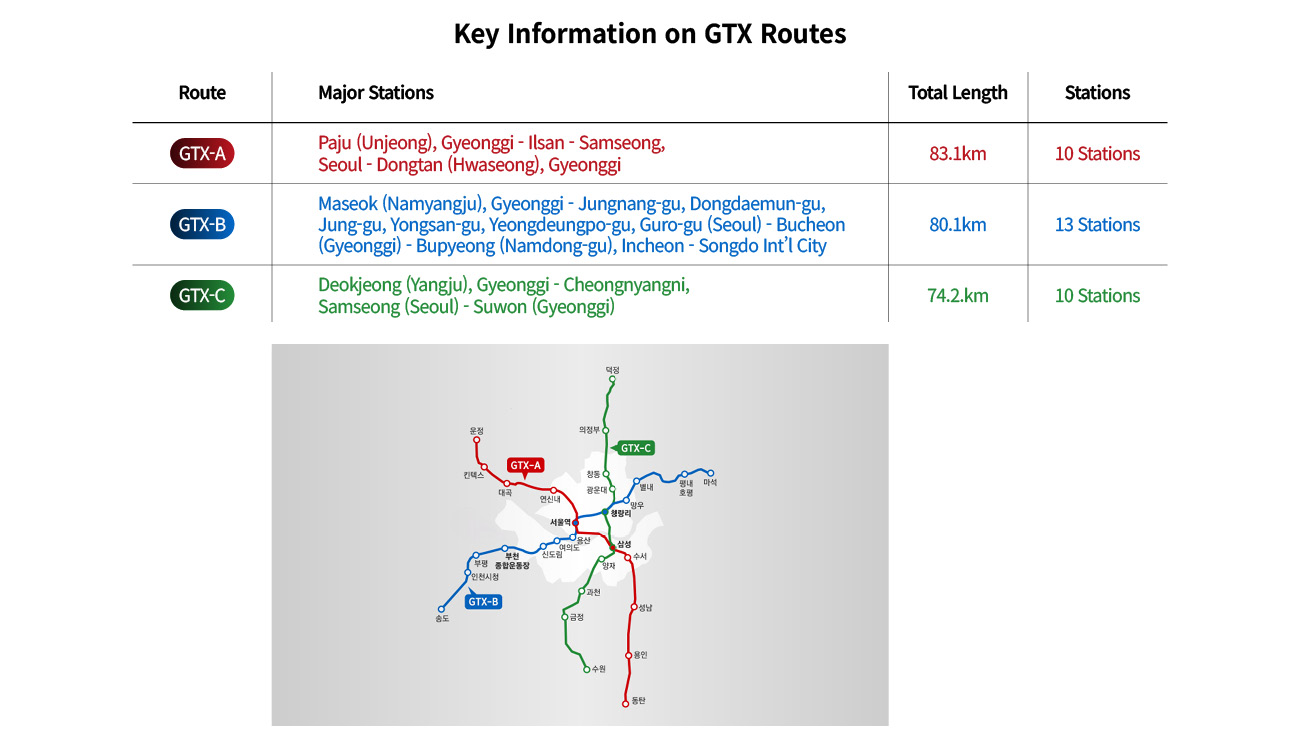
© Ministry of Land, Infrastructure and Transport
As the name “Metropolitan Express Railway” suggests, GTX aims to connect the entire Seoul metropolitan area within 30 minutes. To achieve this, the railway vehicles boast performance comparable to high-speed trains. The vehicles can reach a maximum speed of 198 km/h at a maximum operational speed of 180 km/h, with a scheduled speed (operational distance divided by travel time, including stops) of 100 km/h. Compared to urban subway lines with a maximum operational speed of around 110 km/h, an average speed of 60-80 km/h, and a scheduled speed of 25 km/h, GTX is approximately four times faster in terms of scheduled speed.
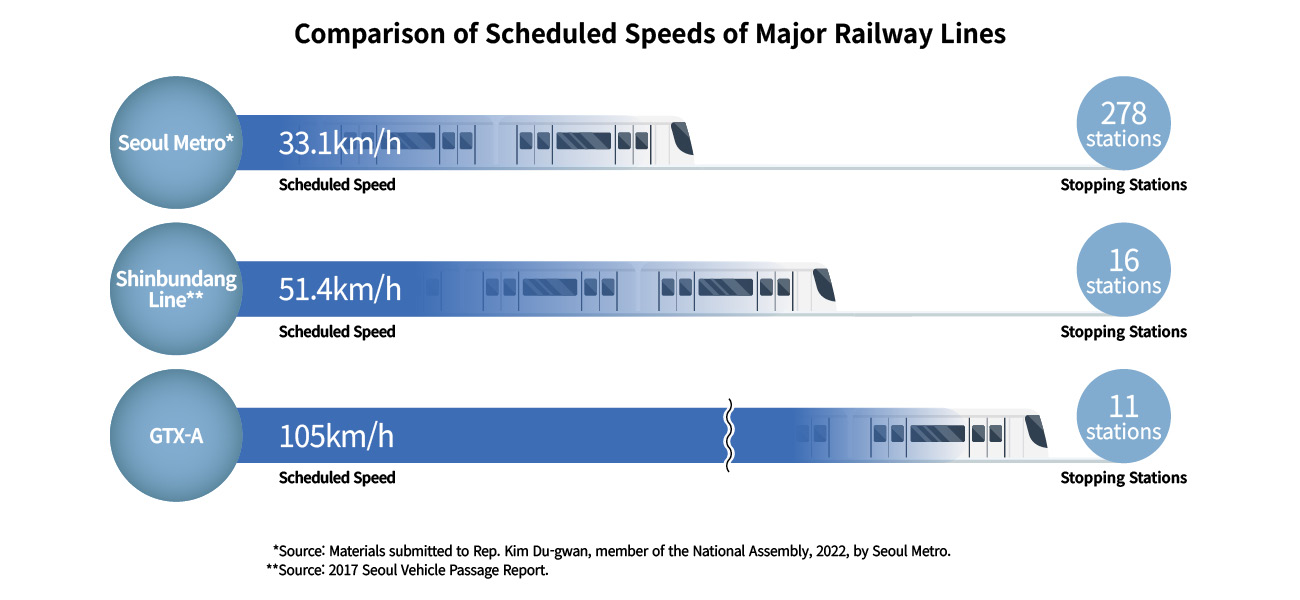
The background behind the capability for railway performance exceeding 100 km/h was due to the “deep-buried high-speed railway” method. This method involves digging deep underground, up to 40 meters, and constructing railways and stations, allowing for simplified line optimization without interference from densely packed urban buildings or underground facilities. The railway’s nearly straight-line form and fewer passing stations make it ideal for trains to achieve optimal performance.
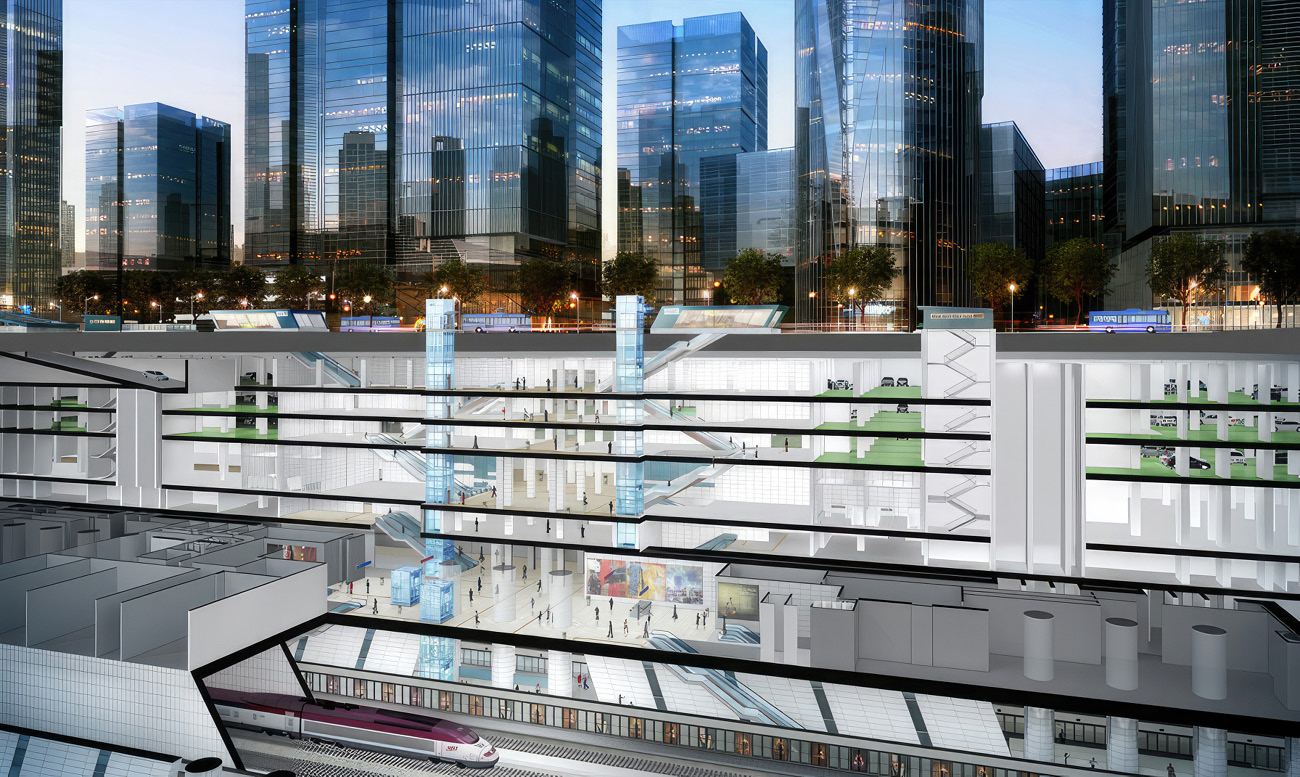
© SG Rail
Hyundai Rotem, which won the contract for supplying railway cars for the GTX-A line, began development in March 2020 and completed the basic design by the end of September of the same year. After hosting a national review in May of the following year, detailed design and initial deployment stages were conducted, culminating in a historic delivery ceremony in December 2022. The cumulative running distance during test runs on the GTX-A main line amounts to approximately 32,000 km.
The GTX-A line commenced full operation on March 30, covering a 33 km section from Seoul’s Suseo to Gyeonggi’s Dongtan with 104 daily runs. Guseong Station (Yongin) opened in June, with plans to begin operations from Paju’s Unjeong Station (Gyeonggi) to Seoul Station starting in December. By 2028, the entire section, including Samseong Station (Seoul), will be fully operational.
Soundproofing Performance, Sealing Performance, and Collision Safety Design Comparable to High-speed Train
Given that GTX operates at a maximum speed of 180 km/h in deep subway tunnels exceeding 40 m in depth, it requires a smart approach distinct from conventional railway vehicles in terms of performance, safety, and passenger convenience.

© Korea National Railway
First, considering the characteristics of operating as a “semi-high-speed train” in the metropolitan area, the vehicle profile was designed to meet the strength and noise criteria exceeding the 260 km/h level of KTX-Eum.
Emphasis was placed on a quiet and comfortable interior design. To reduce indoor noise during stops, a silencer was installed in the HVAC (heat, ventilation, and air conditioning) duct. During operation, traveling at 180 km/h through tunnels inevitably increases noise due to reverberation inside the tunnels. To control this, various combinations of laboratory noise tests were conducted, optimizing the design with integrated panels connecting the vehicle floor, side walls, and ceiling. Since GTX-A is a newly designed vehicle, mockup testing was added during the detailed design phase to reflect the results in the design and undergo thorough pre-verification processes after vehicle production.
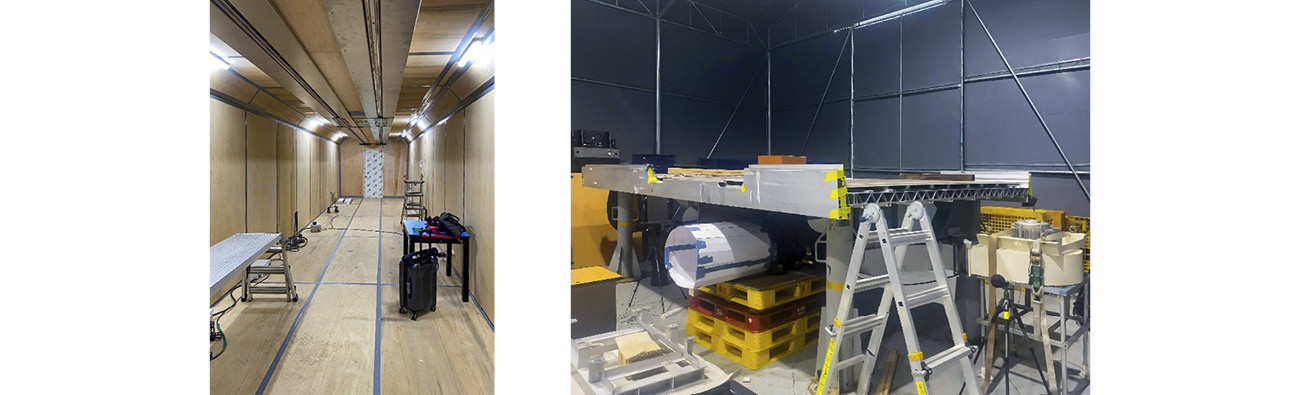
Regarding collision safety, evaluations were made for survival space (driver’s seat and passenger cabin), anti-climbing, and deceleration in two scenarios: frontal collision accidents and collisions with different types of vehicles. It satisfied the collision safety requirements of the general railway vehicle technical standard (Part 44).
Additionally, at the left and right ends of the train’s front, there are anti-climber devices to prevent overriding, along with crash energy absorption components equivalent to those of the KTX-Eum. In the center, a tight automatic coupler* made of rubber material and hydraulic dampers is applied to minimize damage to passengers and crew in the event of a collision.
*An automatic bonding device used to connect vehicles to each other. The adhesive automatic bonding device eliminates gaps between connecting surfaces, minimizing impact during train operation and stop.
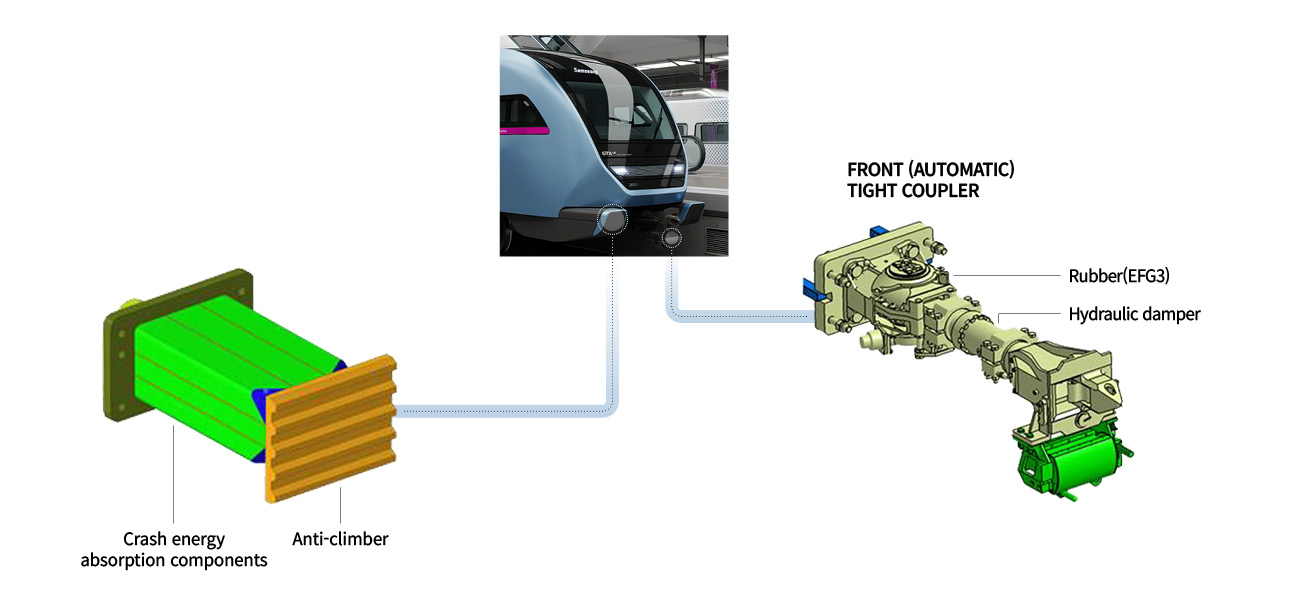
In terms of access doors, the following key manufacturing requirements were followed:
“GTX-A vehicles operate at a maximum speed of 180 km/h and operate under mixed traffic conditions with SRT high-speed trains on some sections, so the performance of access doors must meet the sealing performance requirements specified in the technical standard (Part 31) for high-speed trains.”
As a result, wide-type plug-in doors were installed at six locations on the vehicle sides, marking the first domestic application of a wide-type plug-in door used mainly in conventional EMUs, surpassing a single-figure evaluation criterion for soundproofing performance by approximately 5dB. The inside and outside of the access doors are wrapped in aluminum panels filled with polyurethane foam to withstand the high-speed operating environment’s load. Additionally, the fixed windows use 36mm thick double-glazed glass (tempered glass and laminated glass), which minimizes noise ingress and enhances safety against wind pressure and external impacts at maximum operating speeds.
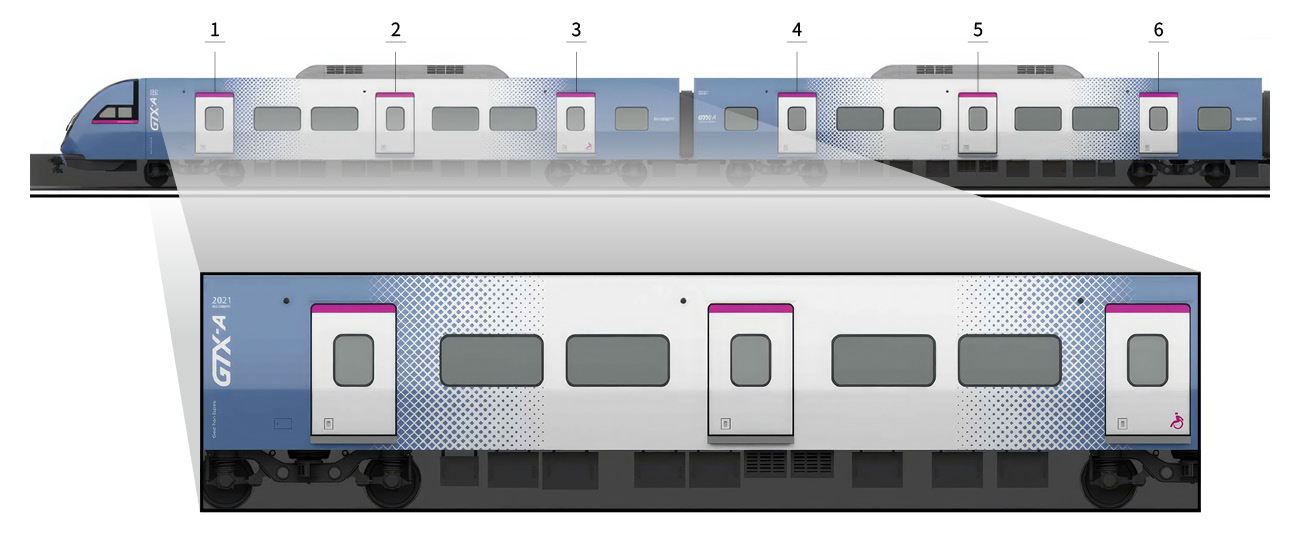
Another critical system maintaining sealing performance in GTX-A vehicles is the room air conditioner, which integrates cooling fans and exhaust fans. Typically, exhaust equipment discharge indoor air to the outside to reduce carbon dioxide levels and improve air quality within the room. The exhaust unit of GTX-A is designed as a sealed type to maintain internal pressure in the event of pressure fluctuations outside the vehicle during tunnel entry or operation. If external pressure exceeds the standard level, the exhaust air damper closes to block internal ingress, while the fresh air damper opens when below the standard to reduce carbon dioxide levels within the room.
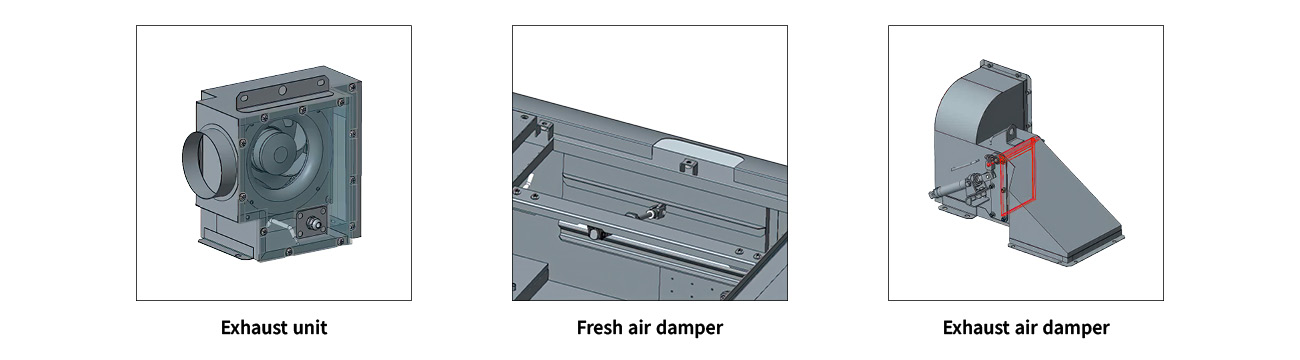
The Fastest Commuter Train in Korea
True to its title as the fastest “commuter train” in Korea, the GTX-A is equipped with Hyundai Rotem’s latest high-speed rail technology. A notable feature is the distributed power system, validated in the KTX-Eum. Distributed power trains have power units distributed under the train cars, ensuring smooth acceleration and deceleration as well as superior high-speed stability. The GTX-A consists of 8 cars in total, including 2 TC cars (control cars with driver’s cabins), 2 T cars (non-powered cars), and 4 M cars (powered cars), achieving high-speed performance and safety close to that of high-speed trains.
In addition to its top speed of 180 km/h, acceleration is another key feature. As shown in the table below, the ITX-Cheongchun train accelerates at 0.55 m/s² up to 80 km/h. In contrast, the GTX-A train, which shares the same top speed as the ITX-Cheongchun, accelerates at 0.7 m/s² up to 60 km/h, allowing it to reach speed more quickly. This advantage is utilized considering the relatively short distances between stations compared to metropolitan trains and the longer distances between stations typical for semi-high-speed trains operating in deep underground tunnels.
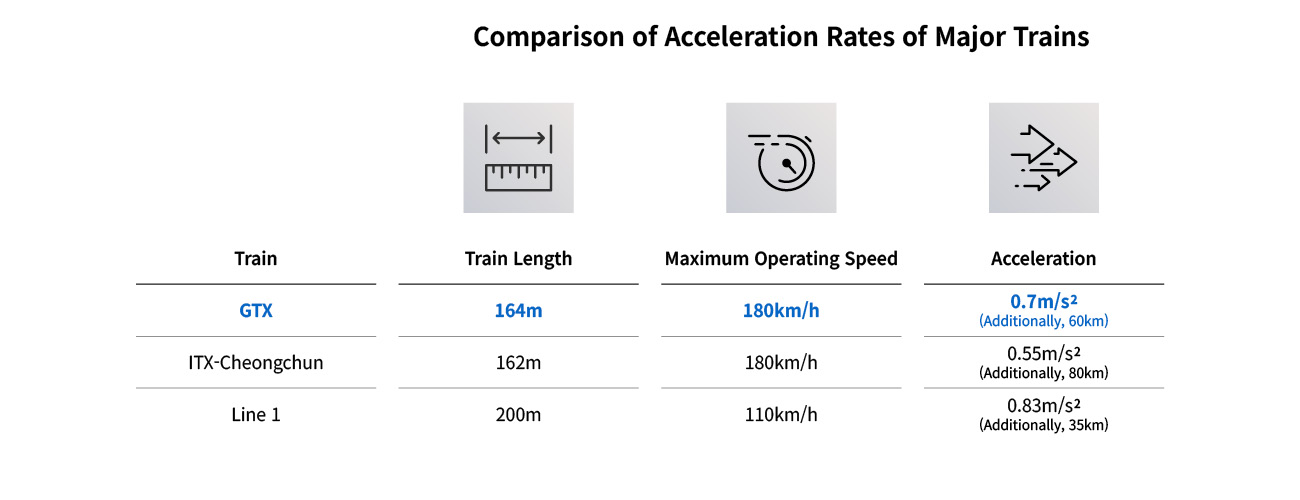
the “zero speed regenerative braking” technology in the propulsion control system is noteworthy. This technology continuously uses regenerative braking until the train comes to a complete stop. The inverter-based zero speed control system in the GTX-A extends the regenerative braking phase, enhancing energy efficiency and improving stopping accuracy and ride comfort with consistent deceleration.
Source : Hyundai Rotem’s Eco-friendly Railway Technology Leading ESG Management
Ergonomic Interior Design Enhancing Comfort
Aimed at achieving “30-minute commutes in the metropolitan area,” the GTX, specifically the A line, covers the Suwon Station (Seoul) to Dongtan Station (Gyeonggi) section in just 20 minutes. The maximum passenger capacity is 1,062 people (296 seated, 766 standing). Compared to the Seoul Metro Line 1, which has a passenger capacity of 1,576 (513 seated, 1,063 standing), the GTX provides a more spacious and comfortable commuting experience per car.
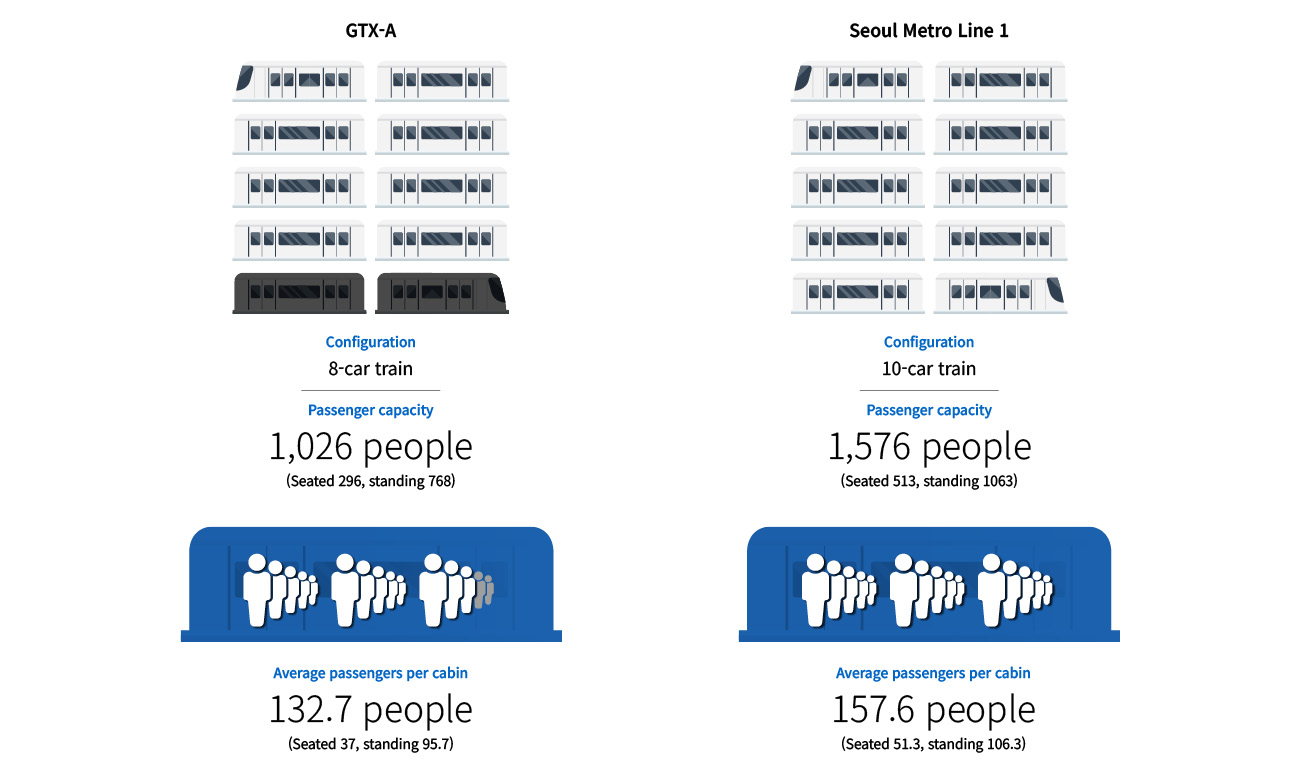
The interior of the cabin has been designed with both comfort and passenger safety in mind. A notable feature is the wider door width of 1,300 mm to facilitate the boarding and alighting of passengers. The side panels of the cabin’s doors are also inclined to ease passenger movement. The design also features varied height handgrips to accommodate passengers of different heights, enhancing comfort and convenience.
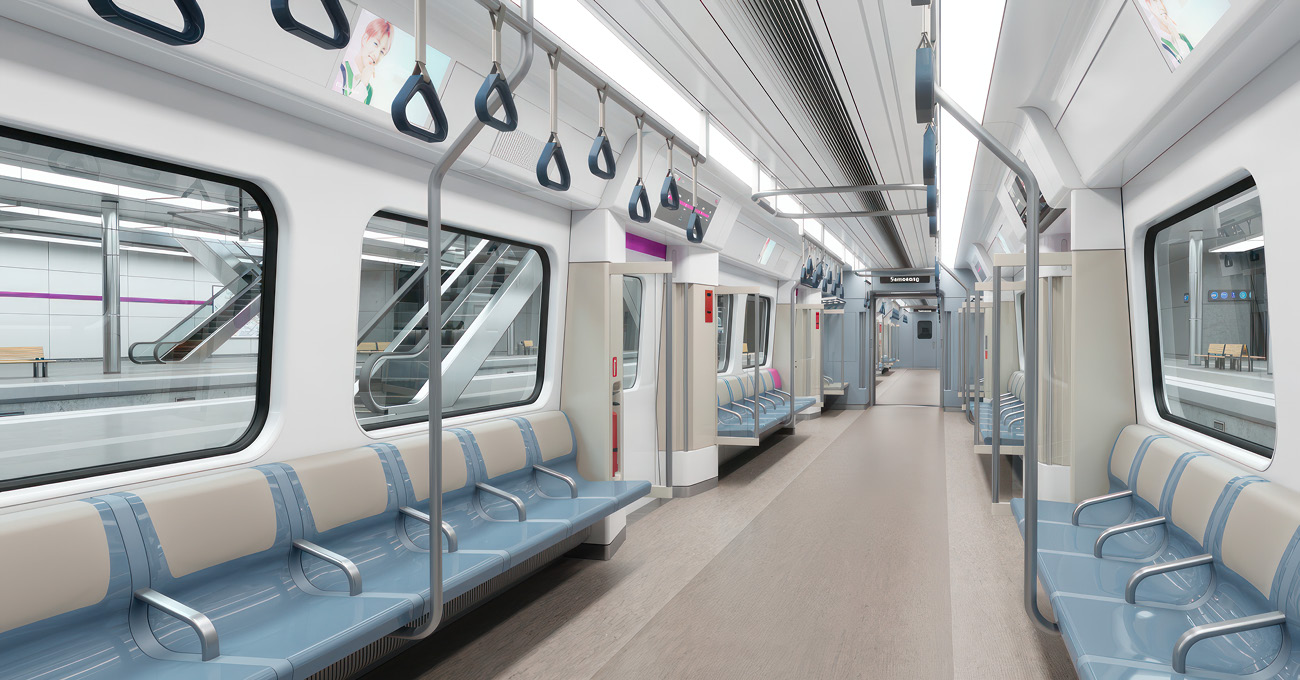
The seven-seater seats have been widened to 480 mm each, with separators for increased comfort, convenience, and stability. General seats, seats for people with disabilities and pregnant women, and priority seats are color-coded for easy identification. Each cabin includes at least five seats for people with disabilities and two seats for pregnant women. At both ends of the cars adjacent to the doors, there are seats reserved for people with disabilities, elderly passengers, and others in need of assistance. Depending on the cabin, there are between 3 and 12 reserved seats, demonstrating ample consideration for passengers with special needs.
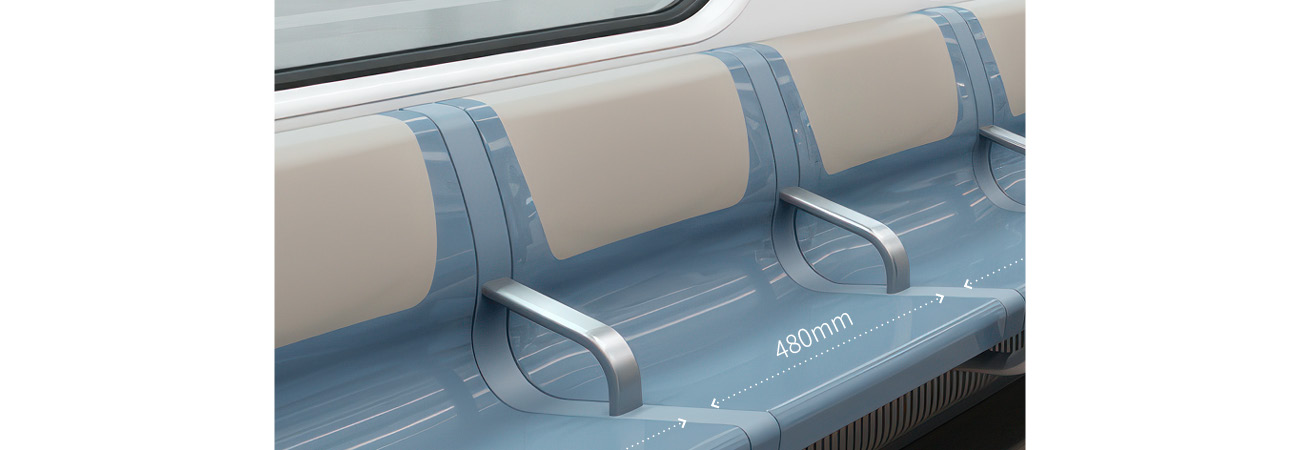
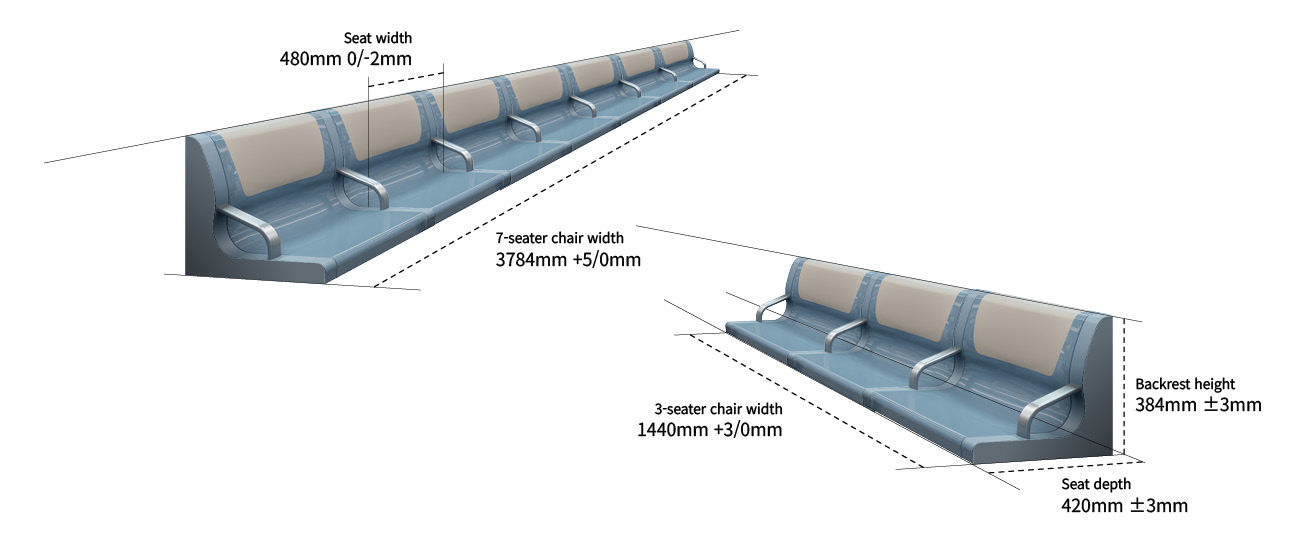
One notable feature is the absence of overhead luggage racks above the seats, eliminating the risk of passengers hitting their heads when standing up and adding to the open feel of the cabin. The space previously occupied by the racks has been replaced with 37-inch large wide-type LCD displays. Each cabin has a total of 10 LCD displays installed above the seats and doors, minimizing blind spots and providing passengers with various information, such as the GTX route map and boarding information.
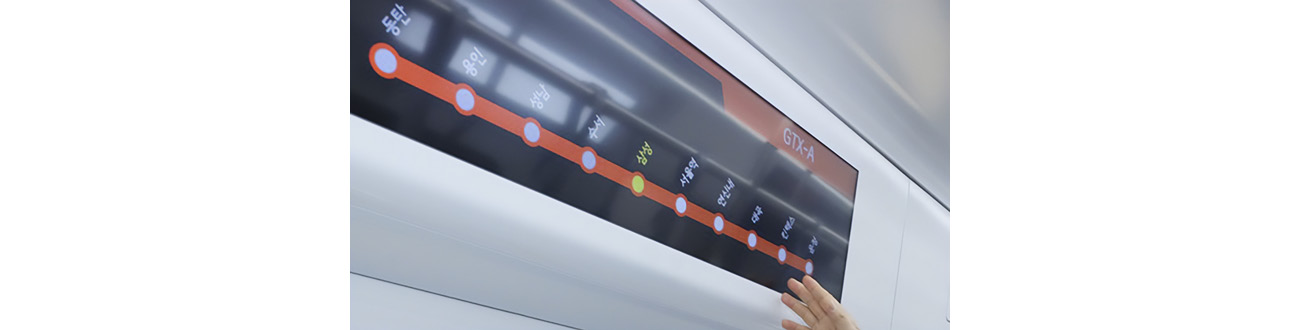
Enhancing Comfort with Air Quality Improvement Systems and Eco-friendly Carpets
Hyundai Rotem has improved the GTX-A travel experience to a premium level with advanced air quality improvement systems and luxurious interior materials. The air quality improvement system filters outdoor air and automatically detects and reduces fine dust and carbon dioxide in the cabin, continuously supplying clean air. Each GTX car has one unit in the driver’s cab and four in each passenger car, featuring an efficient design that includes a fan motor, pre-filter, fine dust filter, LED sterilization lamp, and control module.
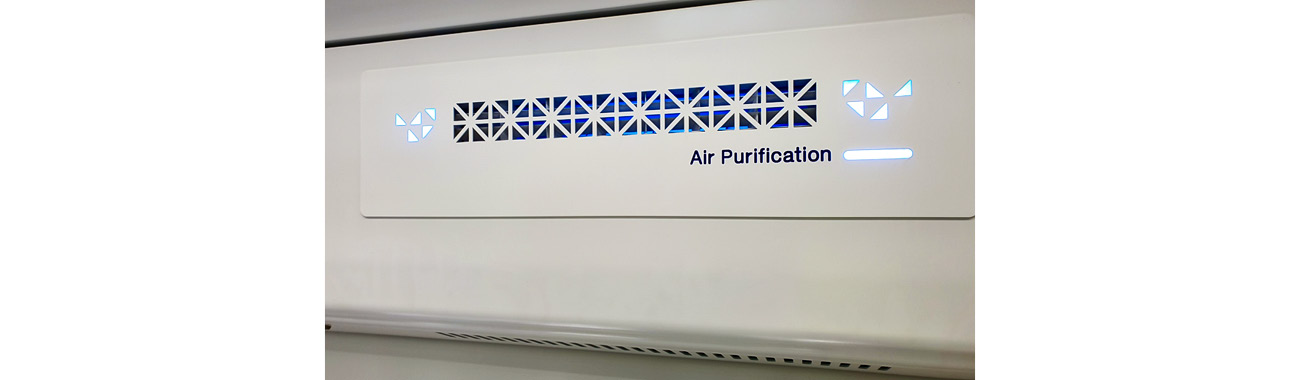
This system uses a fan motor to draw cabin air through the filters and reintroduces purified air back into the cabin, effectively maintaining air quality. The filters include H-13 grade HEPA filters and photocatalyst filters to effectively capture PM 2.5 fine dust.
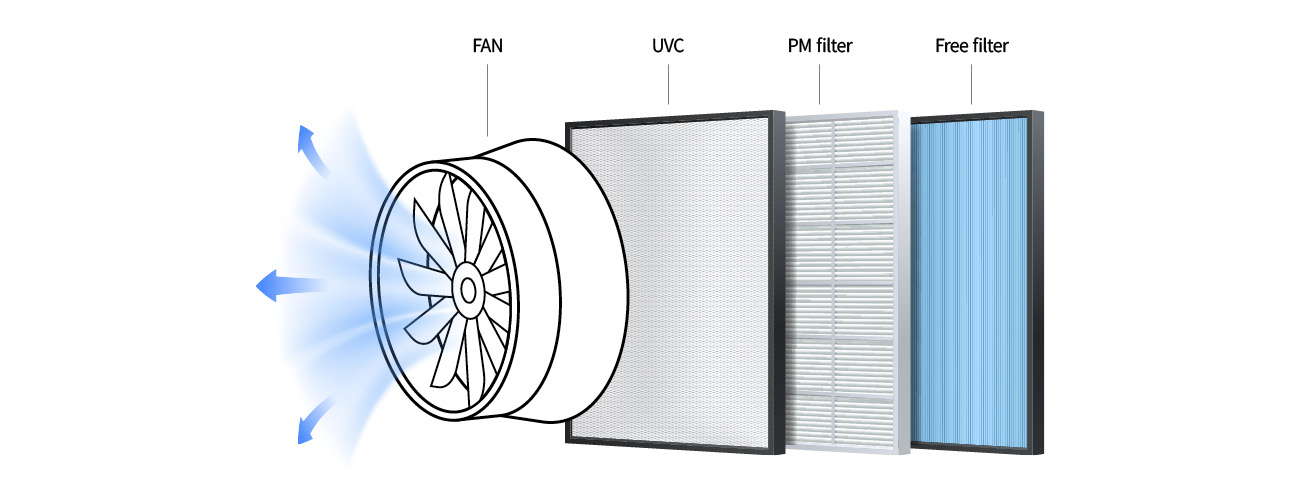
UV-C LEDs are installed between the filter and fan motor. UV-C LEDs emit ultraviolet rays with an output of 100mW or more, destroying the DNA of viruses and bacteria, boasting a 99.99% sterilization efficiency. UV-C LEDs applied in the GTX air quality improvement device irradiate the filter surface with UV light for 10 minutes per hour, removing bacteria and viruses attached to the filter.
Along with the air quality improvement system, eco-friendly antimicrobial carpets with anti-slip capabilities were used instead of conventional rubber flooring. The flooring of railway carriages, considering they are used by many commuters, must ensure waterproofing against water and moisture. It should also incorporate antimicrobial properties to resist pathogens, taking into account passenger hygiene. In addition to strict fire safety standards such as flame resistance, aesthetic considerations that provide comfort to passengers are also essential.
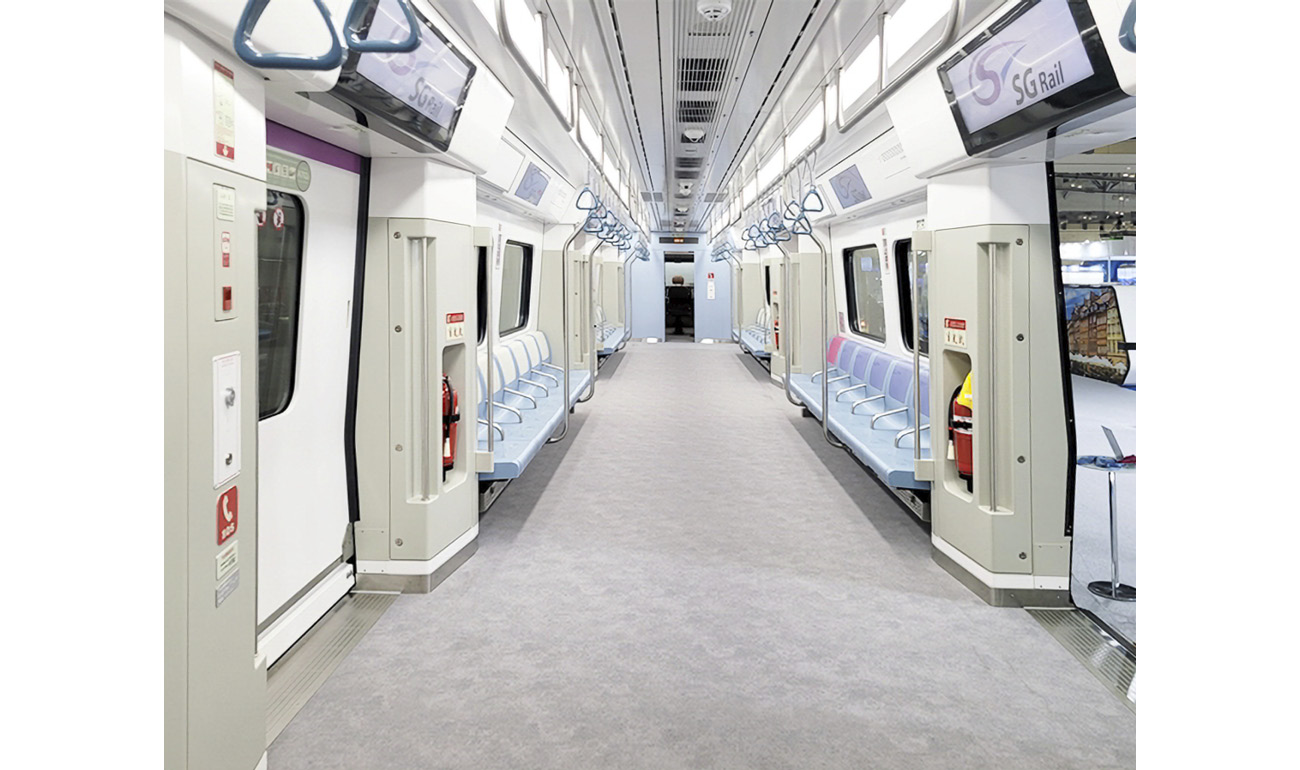
Flotex, a premium carpet used in airport railways and KTX-Sancheon special cabins, meets these requirements. It is over three times more durable than regular carpets and has a 99% recovery rate, ensuring no reduction in walking comfort or cushioning and no permanent indentations. In addition, sanitized antimicrobial treatment inhibits the growth and reproduction of bacteria, microorganisms, and mold. Incorporating the electrical flocking technique ensures permanent anti-static performance. The unique woven structure has a sectional density more than 50 times that of regular carpets,* fundamentally preventing the ingress of contaminants. Even if contaminated, it can be easily cleaned like vinyl flooring, and concerns such as carpet distortion, shrinkage, expansion, odor, and bacterial growth after water cleaning are minimal, making it easy to maintain cleanliness.
* According to the supplier’s own test results
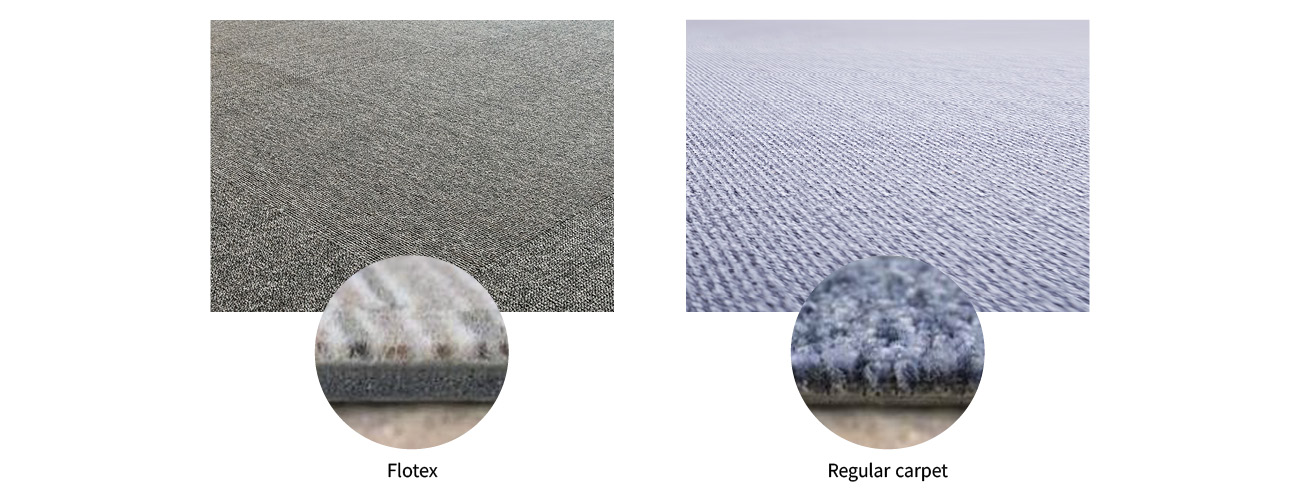
We have introduced the innovative features of the GTX train, performance, safety design, interior and convenient facilities, offering a unique travel experience for metropolitan express train passengers. Hyundai Rotem’s advanced rail technology through the GTX opening provides an unprecedented rail experience worldwide. This accumulated technology will continue to be applied to various trains and high-speed rail in the future.