In industrial terms, maintenance refers to the various processes for keeping equipment or facility in proper working condition. It is practically impossible to maintain diverse equipment and facility used in industrial sites semi-permanent due to wear out, performance deterioration, and unexpected damage to mechanical devices. Therefore, fixing and preserving devices and facilities in good operating condition whenever an unexpected failure occurs such as a breakdown or defect, is crucial daily work for machinery and equipment industries.
Necessity and preparation for maintenance strategies
In the industry 4.0 environment, maintenance exceeds the simple prevention of asset failure. Because a single issue in a small mechanical device may cause the entire system to fail. Since inefficient maintenance system may reduce system availability by approximately 5% up to 20%, it is important to establish an efficient maintenance strategy, and the following six risks must be considered.
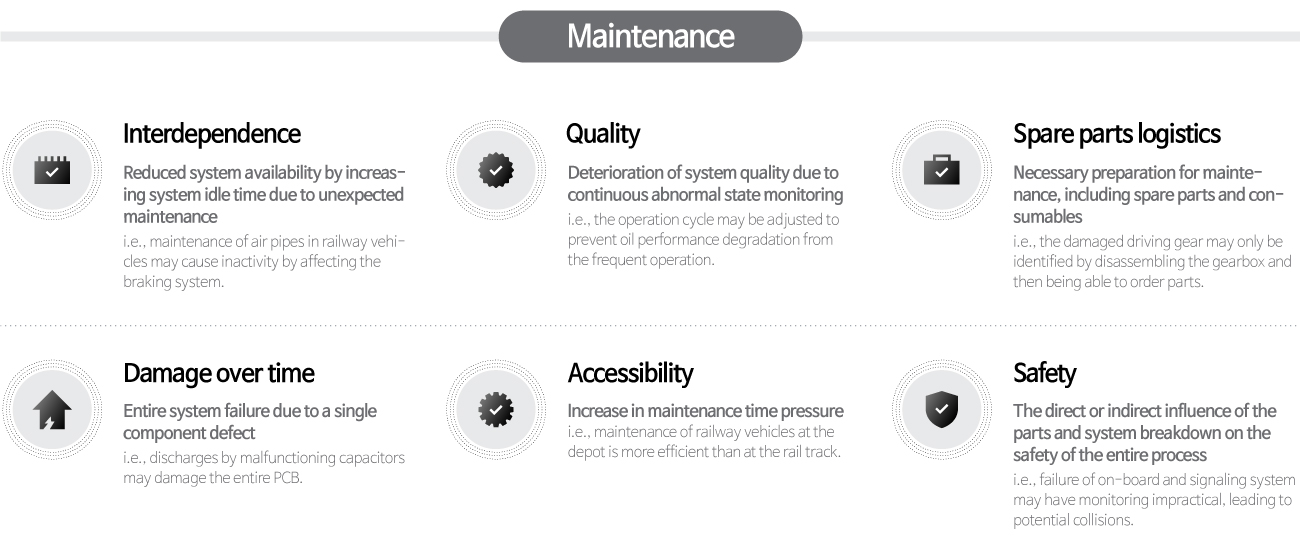
Under the assumption that all system and equipment failures must occur, maintenance is vital for safe and long-lasting usage. The cost is extremely different depending on the maintenance strategy and method. Unpredictable failure from improper and unsuitable maintenance may induce higher idle time and lower asset value due to the decreased system and facility availability. However, performing excessive maintenance may cost a considerable amount.
Components failure rate over time
In general, condition based maintenance of systems and equipment may provide diagnostic insights about operations and functions through monitoring systems and offers asset availability and optimal maintenance intervals. Time/interval-based preventive maintenance proceeds under the premise that the failure of a system or mechanical device is directly related to its life cycle, which has been considered the most efficient maintenance strategy. However, according to research, about 89% of breakdowns are from random issues irrelevant to time and useful life, and 11% represents the failure pattern applicable to time and lifespan.
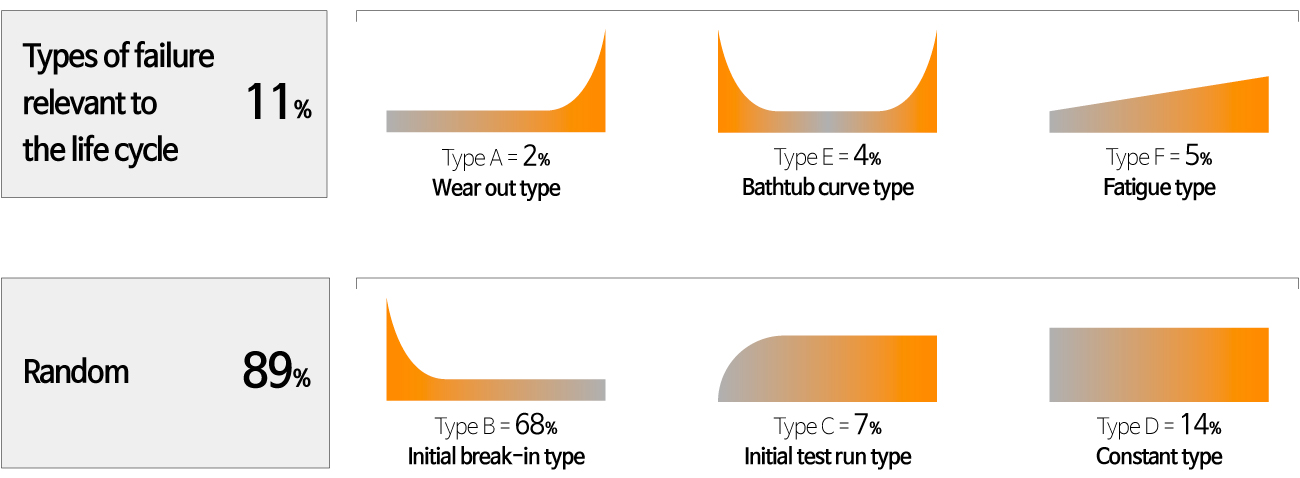
The need for maintenance is based on actual damage or failure of the system and equipment. The meaning of ideal maintenance is performing timely maintenance to operate the device and system efficiently, at least for the designed useful life of components. In particular, the actual operation of the system and facility must sustain time-based functions and performance, which is the closest to the ‘bathtub type’ failure.
Fully utilizing the intended lifespan of parts/elements is essential for an efficient system and mechanical device maintenance. In general, the failure rate of components over time displays a bathtub curve, as shown in the image below, that can be largely separated into three sections: initial break-in stage, effective life stage, and wear out stage. The characteristic of the first stage is a gradual decrease in breakdown rate from higher initial break-in failure. Drawing the curve is associated with component design errors, incorrect parts installation, etc.

The failure rate in the second stage is usually consistent after the first section. Most component failure in the effective life part is from inferior operation and maintenance (O&M). Thus, if there is no problem in usage, efficient maintenance contributes to extending the useful life of components considerably. In the wear out stage, the failure rate rapidly escalates over time. Detecting each part’s wear and tear section and replacing it before failure may minimize idle time.
Railway vehicle maintenance strategy
Maintenance strategies in general industrial sites may be classified into four categories: corrective maintenance, preventive maintenance, condition based maintenance, and predictive maintenance. The last two are emerging relatively recently due to the 4th industry influence. Corrective maintenance in the railway sector is repairing when a breakdown happens, which is the most basic and has been used for the longest time. Preventive maintenance is regularly performed maintenance for system or equipment suppliers to provide consistent system performance, the most common maintenance strategy in the railway industry. As the system operating time dependent on railway vehicle schedule directly affects railway vehicle failure in many cases, interval-based maintenance for the designated usage schedule is commonly suggested.
However, condition based maintenance is a smart method that performs maintenance when detecting system failure or abnormality after monitoring each component, including exceeding the standard value, departing from the standard deviation, and generating a trend. Predictive maintenance is a big data-based strategy that executes maintenance when noticing trends in abnormal conditions regarding pre-analyzed normal versus abnormal conditions generated by the condition based method.
Strengths and weaknesses of maintenance strategy
Maintenance Strategy Types
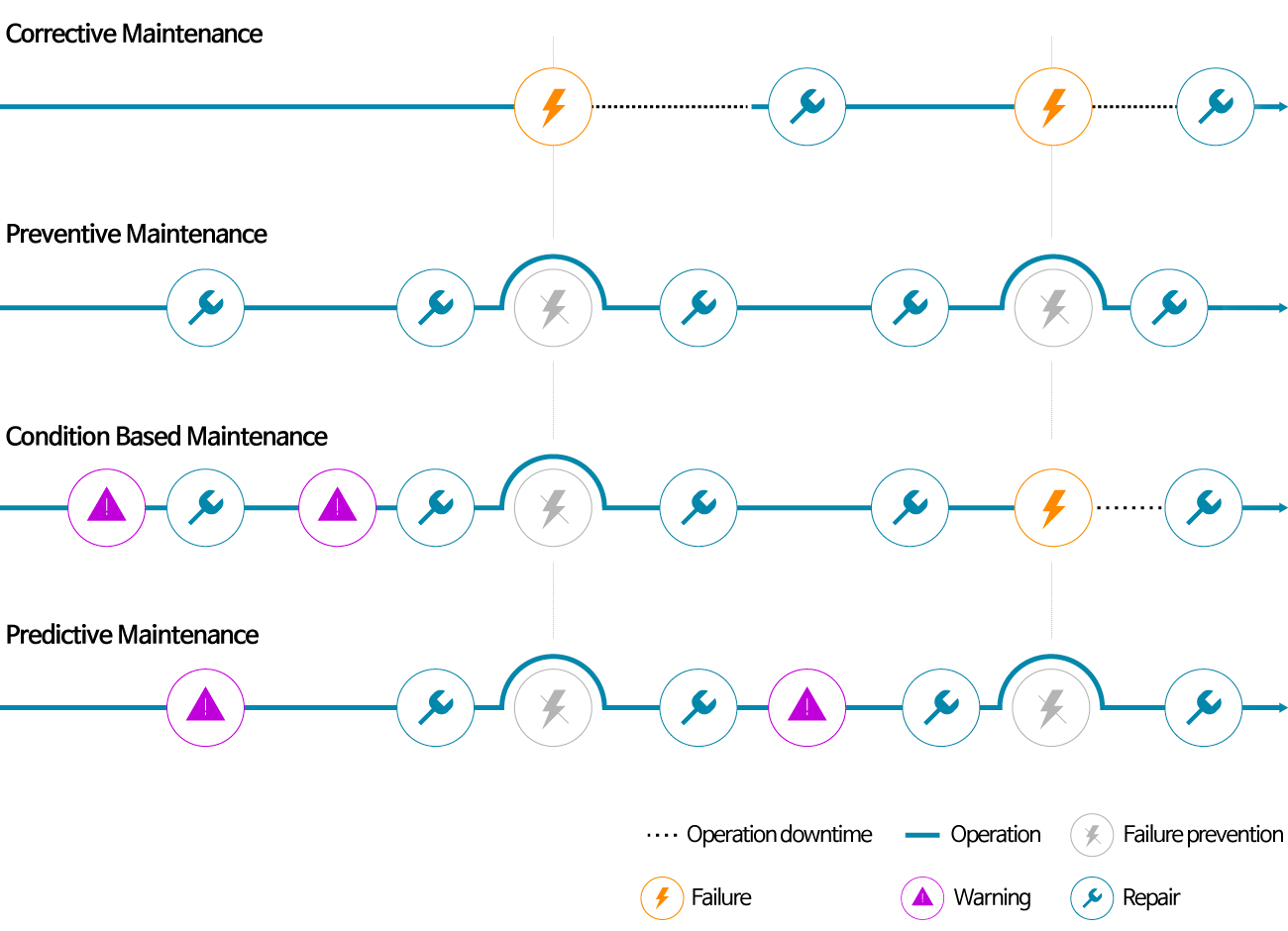
Applying the right strategy is crucial as each maintenance has advantages and disadvantages, and each industry has different environments and conditions. An efficient maintenance strategy must be established considering the following four types. Preparing a maintenance method based on the railway vehicle operator’s workforce, facility, and structure is essential to reduce costs and minimize the entire system’s downtime.
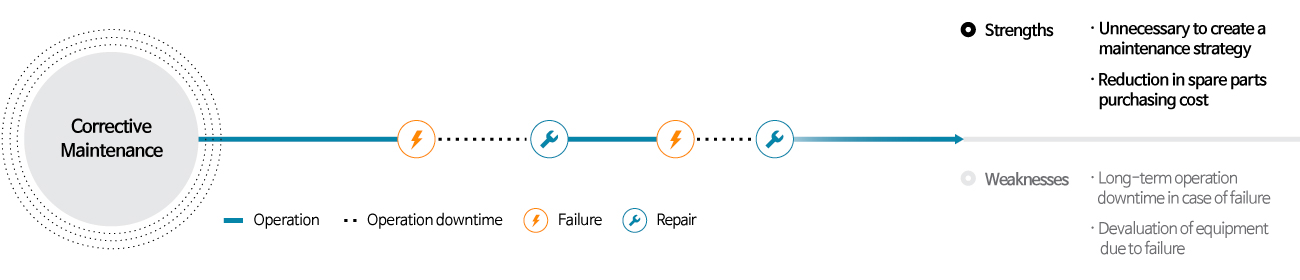
Corrective maintenance proceeds with immediate repair when a defect or breakdown occurs. With the goal of normalizing defective parts, it minimizes unnecessary preparation costs until a failure happens. However, as idle time will follow in case of breakdown, it is not common to apply this strategy in the industrial field, like the railway sector, where inactivity may cause enormous losses.
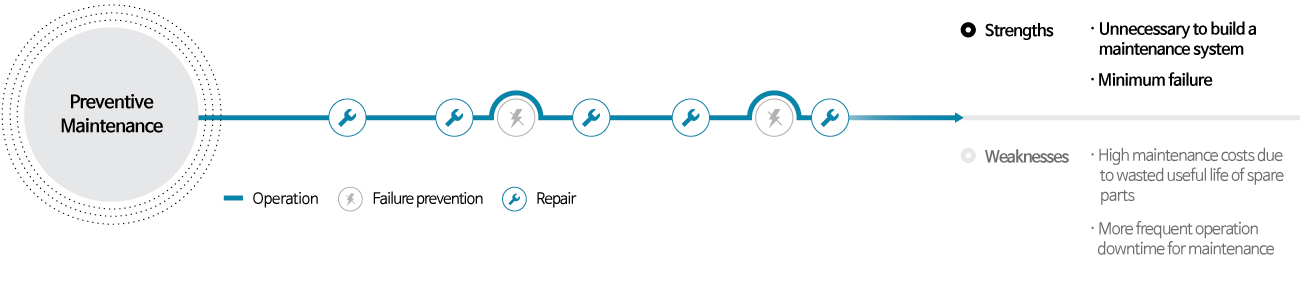
Preventive strategy performs maintenance in advance of actual defects or failures. The goal is to minimize potential damage to mechanical devices and the degradation of equipment, components, and spare parts. This method is pre-planned maintenance, which has enhanced efficiency with the introduction of the Computerized Maintenance Management System (CMMS). It performs data-based preventive maintenance by entering all relevant details of equipment and facility operation and maintenance.
It has the advantage of minimizing failure but has the disadvantage of unnecessarily reincurring costs due to regular replacement of functioning parts. This method is widely used in the railway industry with consideration of passenger safety in case of an unexpected breakdown and operational loss due to idle time. However, it has a clear limitation in efficiency.
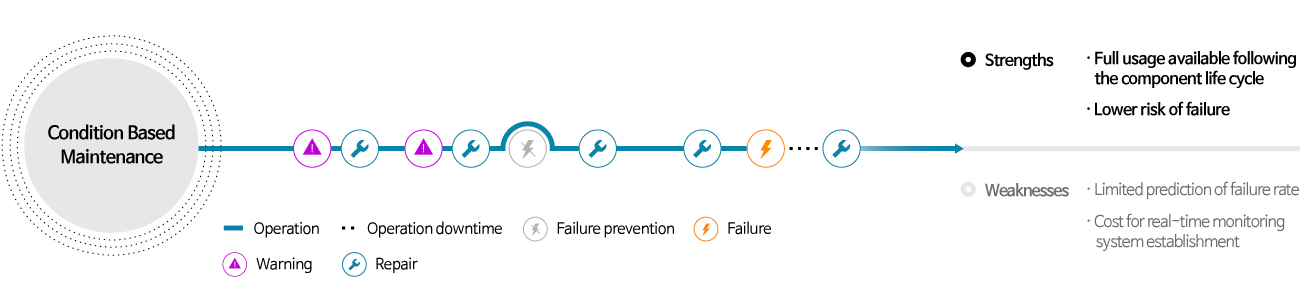
Condition based maintenance requires a preparation process before maintenance compared to previous strategies. This method aims to prevent equipment failure and to monitor and perform maintenance regularly by inspecting various items, such as routine inspections of devices and efficiency, following the unified diagnostic algorithm alarm. On-site data, including the status of equipment or facility, is automatically collected through the connected network, and utilized for maintenance. Maintenance personnel check the wear and tear of each part regularly or irregularly. This strategy has the disadvantage of high cost and technical skills to collect real-time on-site data but has the advantage of cost-effectiveness as it minimizes breakdown upon the system establishment and fully utilizes components up to their lifespan. It is spotlighted in industries with enormous potential operational loss in case of idle time, like the railway field, if the initial investment cost can be covered.
Learn more about Hyundai Rotem’s condition based maintenance system
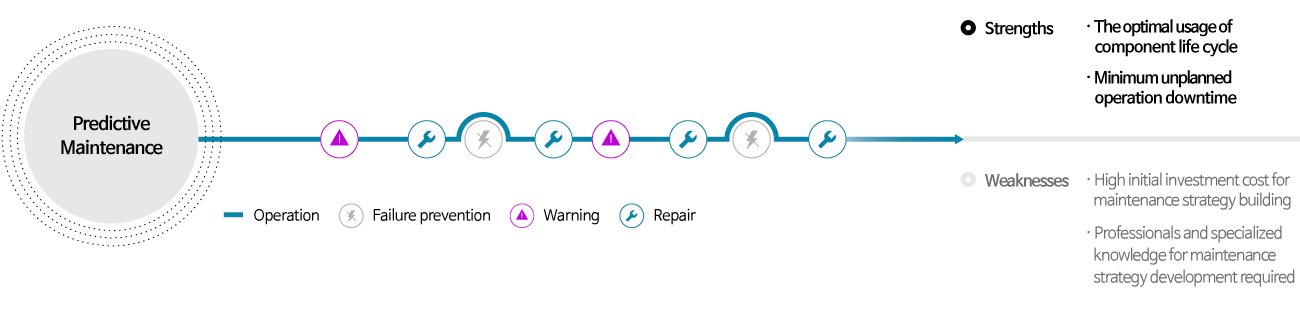
The predictive maintenance performs maintenance depending on the actual condition data of mechanical devices and facilities, similar to condition based maintenance. Through real-time monitoring, the condition-based strategy creates a maintenance schedule for a single part based on the logic and trend algorithm. On the other hand, predictive maintenance designs big data from numerous data of functional and defect-related component details, including basic data, characteristics, and previous maintenance history, on top of the real-time monitoring data and creates a predictive algorithm to anticipate the useful life of each part for generating the schedule and implementation.
The optimal predictive algorithm and predictive maintenance program minimize operation downtime more than any other methods and efficiently manage the cost of maintenance workforce and spare parts. The downside is that it requires initial investment cost for constructing the system and professionals for active development of maintenance structure by continuously analyzing the data, like condition-based maintenance. It is the desirable strategy in the long-term in the railway industry regarding minimum idle time caused by failure and repair.
Railway vehicle maintenance strategy suitability
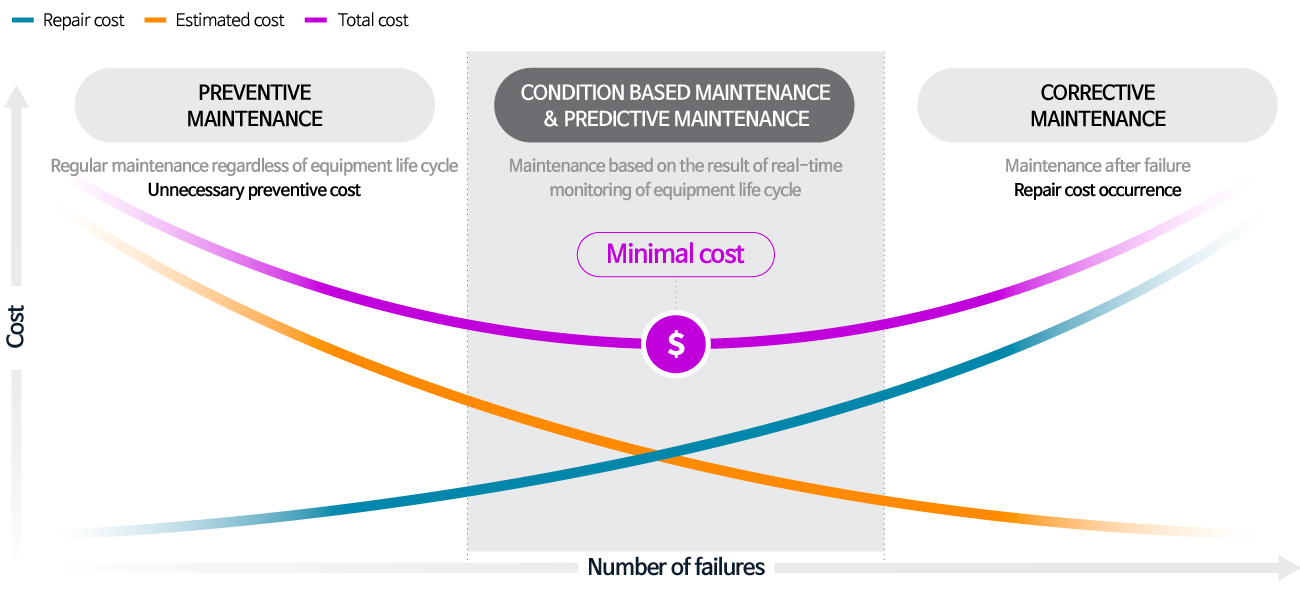
The decision on which maintenance strategy to apply is closely relevant to efficiency. All factors, including maintenance preparation, workforce, and cost of loss in case of breakdown, must be considered. The least costly method should be introduced.
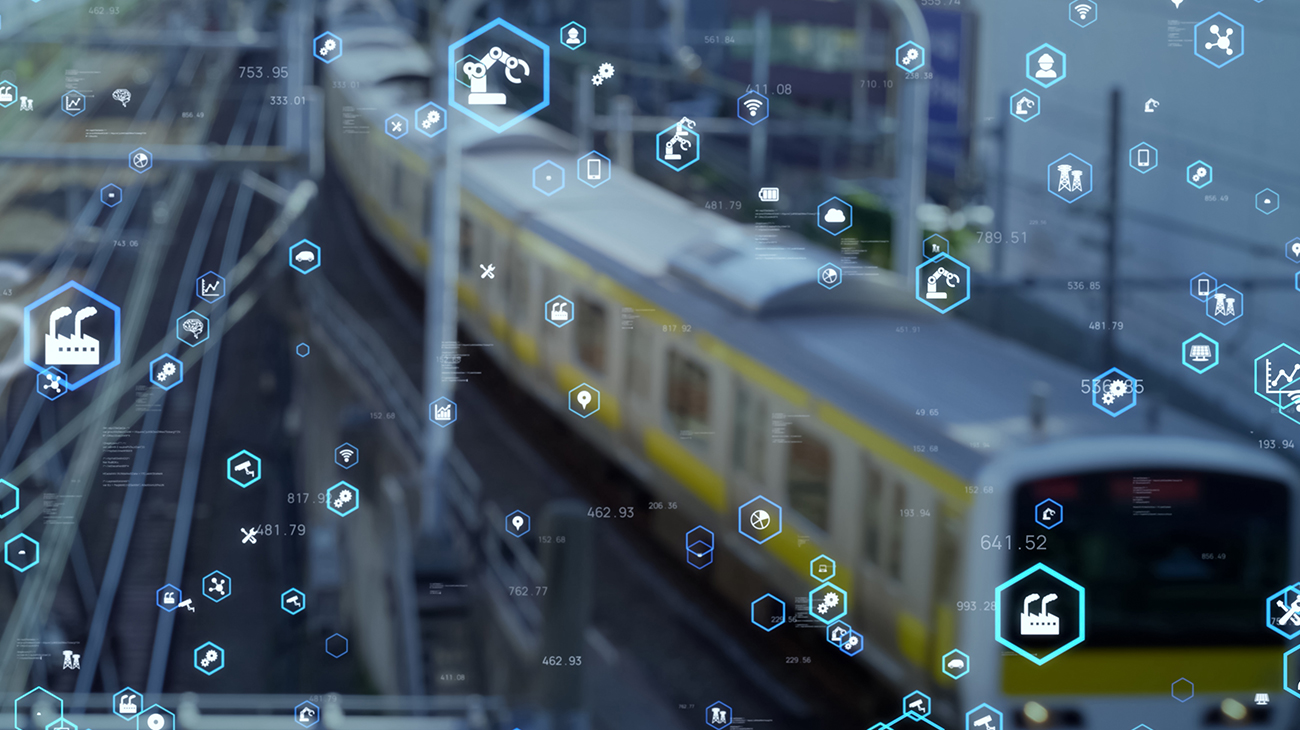
The railway sector must select the optimal maintenance type considering the risk of each system failure. Condition based or predictive maintenance is appropriate for a bogie system that requires utmost safety without easy access to maintenance personnel and frequent defect. Both strategies demand high initial investment costs. However a method minimizing repair and maintenance in the event of a defect should be adopted as railway vehicles are public goods used by numerous people and have enormous potential losses from idle time due to breakdown and frequent failure. Since passenger safety is of the utmost concern for railway vehicles, introducing condition based or predictive maintenance on top of the current maintenance will be effective in terms of availability to prevent safety accidents and provide continuous services.